Keep it simple. For all its complexity, an automated machine’s main requirement—after making good product—is to do its job as simply as possible.
However, duplicating and replacing human movements historically required a lot of mechanical equipment, and so automating and controlling those components became equally complicated. Cable bundles and trays grew to the point of bursting, and some builders still joke that cabinet space is the world’s most expensive real estate.
In recent years, the advent of increasingly capable computers and software, and then digital networks, lightened the load on the hardware. As these assets took on more jobs that formerly were hardware-based, basic operations, changeovers between production runs, maintenance, troubleshooting and repairs became a little easier—if you knew how to write the right code and make the right network links.
Also, as these newer machines evolved, many began to draw their I/O points out of traditional cabinets, closer to the production lines and near or onto the machines. This gathering and distribution of control components resulted in increasingly modular and almost Lego-like machines, which can be plugged in and pulled out as needed, thanks largely to those simpler networking connections and software.
Linkable Wafer Handling
Semiconductors usually are made by robots in vacuum-maintaining mini-cleanrooms called cluster tools. But their traditional radial design became unwieldy and expensive as wafers grew bigger and semiconductor processing became more complex.
BlueShift Technologies, Santa Barbara, Calif., recently used a more linear design to build QuickLink, a modular wafer-handling system, which it claims is 30-40% less costly because it has a smaller footprint, easier reconfiguration, better quality and increased throughput than conventional radial handlers.
Wafers pass along a line of BlueShift’s process modules and transfer chambers that are smaller than radial chambers, and this reduces raw material and etching costs. QuickLink’s linkable design lets fab operators add processing modules as needed in a compact configuration with footprint reductions up to 40%, compared with radial footprints, and optimize throughput by balancing the workflow, while eliminating bottleneck processing chambers. BlueShift believes these building blocks make it easy for users to configure wafer-handling systems for high capacity and long process time, high throughput and short process time, or increased vacuum isolation and contamination control.
Robotic Motion Control
Robot design is critical to any wafer-handling system. High repeatability is essential to avoid damaging the wafer, while providing high throughput requires high speed. “Because these robots are designed to operate in a vacuum, they have to provide smooth and accurate motion with as few moving parts as possible,” says Chris Kiley, BlueShift’s engineering vice president. “When initial systems originally were designed there were no off-the-shelf (OTS) motion control components that could meet these needs. However, when we designed QuickLink, we saw that high-reliability, low-cost OTS components had improved enough to handle this application.” The company started with motion control cards and amplifiers based on Firewire A. “However, we found that its motion control card couldn’t run more than one robot axis at a time, and each of our robots has three axes—the alpha and beta rotational axes and a z-axis for vertical motion,” says Kiley. “Our design specifies that one card will control an entire wafer-handling system which might easily have six robots.”
Consequently, BlueShift began to work with Target Electronic Supply, a system integrator in Westwood, Mass., that concentrates on motion control. “BlueShift wanted to add axes as needed to support their modular architecture, and so I thought Danaher Motion’s XMP motion controllers were a good match,” says Les Peabody, Target’s manager. “These controllers provide up to 32 axes and support servo update rates up to 16 kHz.” The XMPs communicate via SynqNet, which Peabody says provides a synchronous real-time connection between the motion controller, servo drives, I/O modules and custom nodes.
Pristine Printing
Figure 1: Kammann Machines’ flat-screen head module uses an open architecture to integrate with any narrow web printer. Its technology is more flexible, uses fewer parts, and requires less labor and time than traditional rotary screen printers.
Source: Kammann Machines
“SynqNet on one Cat 5 Ethernet cable between the controller and drives can carry all their conversations, and this allows designers in the field to simply add drives to the control system as needed,” explains Erik Brewster, Danaher Motion’s principal design engineer. SynqNet also has a hot-swap feature that allows users to remove and replace a machine’s subsystems while it’s still running, which dovetails with a modular machine’s other advantages.
“Previously, builders and users had to yank out whole wiring harnesses and rebuild or replace them,” adds Brewster. “Also, motion controllers usually were wired to servo amplifiers, and so there might be 15-20 discrete wires from a controller to each amplifier. For 10 motion axes, this means about 200 wires. So, the worst isn’t that a machine goes down, but that the user doesn’t know which wire caused the problem or where it is.”
Divide Modules and Conquer
Though cost and size issues often inspire builders to go modular, evolving end-user technologies also can spark demand for modular machines. Kammann Machines in St. Charles, Ill., reports it recently divided its long-established K61-OS web press technology into several functional production modules to give users added capability and flexibility in narrow-web printing operations. These open-architecture modules offer in-line or off-line screen printing and post converting (Figure 1).
“We wanted to extend Kammann’s technology to users in the printing community that were unable to replace existing printing machines but still needed the capabilities of new equipment,” says Steve Gilbertson, Kammann’s president. “These modules also let K61-OS users add to their existing precision technology investments.”
As a result, Kammann’s new servo-driven modules include flat-screen head printer, waterless offset, rotary or flatbed die cutting, rotary or flatbed hot stamping, cold foil stamping, flexo station, and hot-air dryer/IR module. Gerry Nigg, Kammann’s international product development manager, says the modules formerly combined in one package gain several advantages when separated. “The flat-screen head module’s open architecture allows integration with any narrow web printer,” says Nigg. “The cold foil-stamping module is an alternative to traditional hot-stamping methods used in flat-bed printers and allows stamping and drying to be combined into one process for maximum production efficiency.”
However, unlike accessories and modules simply hung on existing machines in the past, Kammann’s press drive units and other modules are equipped with encoders and servo drives and coordinated in their own right, which saves even more time and further increases accuracy. “We might even add a modular vision system to monitor the web as it moves,” adds Nigg.
Taming a Multiplying Variety
Another reason to build modular machines is flexibility so they can be reconfigured quickly to produce, handle or package products in all the wildly varied sizes and shapes that are in demand these days.
Beam Global Spirits & Wine’s plants in Clermont and Frankfort, Ky., and Cincinnati use adaptable case-packing machines to cope with growing and increasingly varied streams of new products, bottle sizes and types, such as Starbucks Coffee Liqueur, which comes in 375 ml, 750 ml and 1 liter bottles of various shapes (Figure 2).
Plug-and-Play Packing
Figure 2: Beam Global Spirits & Wine uses flexible programming and plug-and-play components in Standard-Knapp’s servo-driven 939 Versatron case packers to perform 15-minute changeovers, and handle as many as eight different bottle sizes. bottles of Starbucks Coffee Liqueur and pack about 30 cases/min.
Source: Standard-Knapp
“With our large portfolio of premium products, we need case-packing equipment that can adapt to a variety of bottles and do so quickly and easily during our frequent changeovers,” says Robert Land, Beam’s corporate packaging engineer. “The case packers need to be gentle on our premium packaging and must operate reliably at high speed because we have limited accumulation space upstream on the production line.”
Beam has been using 939 Versatron case packers from Standard-Knapp to pack about 30 cases per minute for about 10 years at its Kentucky facility and recently added three more to pack cordials at its Ohio plant. Versatron includes a two-axis servo system that controls a lift table to create a “soft catch” procedure that matches the downward speed of bottles as they enter their cases and then decelerates slowly, greatly reducing breakage and sticky clean-ups. The servo system and associated variable-frequency drives (VFDs) are controlled by an A-B SLC-500 controller and ControlLogix software, programmed and monitored via its operator interface (OI).
Land reports that Beam’s operators use Versatron’s flexible programming capabilities and touchscreen OI in tandem with the case packer’s hardware to do complete production-run changeovers in 15 minutes without tools. Versatron’s plug-and-play components include a patented, lightweight snap-in grid basket, drop-in lane-guide spacers and slide-in riding strips. As a result, one Versatron at the Cincinnati plant runs eight different packages, including rectangular and round bottles in three different sizes.
Think in Pieces
To select the most appropriate and useful modular machine strategy and solution, Danaher’s Brewster suggests builders and users collaborate with system integrators. They should select a controls architecture and protocol that allows them to do what they want with their machines. This typically involves picking a non-network controller or a network controller.
Non-network controllers are usually older-style devices that work with a PC card to simply control axes in smaller applications. Brewster contends that network controllers are the way everyone is going now because most machines have most of their axes or I/O in the middle and many users want to add some capabilities on the side. “Builders and users have to decide how they want their machines to expand in the future,” says Brewster. “If they need high availability and they don’t expect to add that much to the machine, they can use a non-network controller. However, if they’re probably going to add a lot of devices, axes and I/O points, then they need network controllers and the right architecture to support them. The fundamental techniques are the same, but the real difference with modular building is breaking the machine design into functional parts and then planning ahead, so they can be bolted onto each other.”
As production lines and machines become modular, their components are taking the same path and can be mounted on or near and work better with these building blocks. For example, B&R Automation’s (br-automation.com) X20 System slice I/O has a separate bus module with a plug-in electronic module and a terminal block for cabling. Stephan Strickler, B&R’s product manager, says X20 lets users building modular machines leave out some I/O slices they don’t need and use optional features they want to switch on. X20 also can transmit up to 100 m and handle up to 250 modules.
Divide and Recombine
Perhaps it was inevitable, but during a period of modular machine design, some developers began to think about putting some divided functions back together in larger devices. Ironically, the same software and networking that allow modular machines to flourish also can be used to bring some modules back under a common umbrella when it makes sense.
Fanuc Robotics Americas, Rochester Hills, Mich., says traditional, dedicated welding cells usually only worked on one part type and required lots of manual loading and unloading. Now, Fanuc’s new Intelligent Welding System activates 11 robot groups as needed, coordinates their activities and works on a variety of different parts and models. These robots basically plug-and-play themselves based on the project specified.
“Instead of doing so much loading, we have a large robot that serves as the positioning device, and then the other robots come in,” says Joe Hoffman, Fanuc Robotics’ senior welding engineer. “Our quad-arm system robot talks to another group, and their overall CNC software harmonizes them by conducting I/O handshakes and carrying out code statements via Ethernet TCP/IP. This modularity is further enabled by additional boards in the welding system that allow us to immediately add more robots, I/O points and other devices as needed. For example, because we have room to have a vision board already installed, all we have to do is plug in a camera. This makes expansion and troubleshooting much easier.”
Meanwhile, Icon Technologies division of Hydromat Precision Machining Solutions, St. Louis, Mo., just debuted its 29-axis, palletized Icon 6 250 machining center that combines four more traditional centers into a larger machine enclosure that provides a 10x10x10-in. work-piece area. Icon 6 250 merges the high-production capabilities of a rotary, transfer dial machine with the flexibility of a horizontal or vertical machining center.
“All of Icon’s modules are coordinated by GE Fanuc’s 30i CNC controller and proprietary code, which manages servo controls for the 29 axes and enables us to control multiple machines in one envelope,” says Don Flannery, Icon’s manufacturing director. “When this CNC controller was introduced in Japan, its developers thought it would be used as one control for many separate, distributed machines. However, users like us to pack more machines back into one envelope. Previously, it would have taken 8-10 standalone machines, all networked for communications and control, to do what Icon 6 250 can do in one setting. And, we still get the benefits of a modular machine by just changing pallets, instead of bearing the costs and complexity of a fixed ring.”
How much modularity do you build into your machine designs? Compare notes at ControlDesign.com/modular.
Modular Machine Building To-Do ListThere are several basic steps when designing and building the controls and related data processing functions for a modular machine. In B&R Automation Product Manager Stephan Strickler’s world, that means:
|
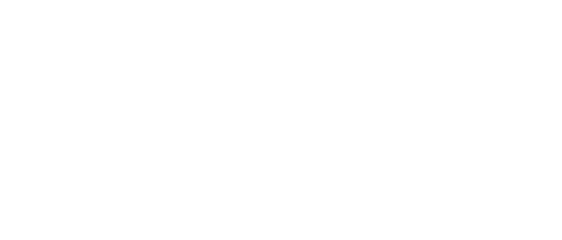
Leaders relevant to this article: