By Scott Smith, Hartness International
Perhaps no industry is experiencing change as fast as packaging. Lighter-weight containers are being introduced to reduce costs and energy use. Packaging is redesigned more frequently to attract consumer attention in a competitive global marketplace. And manufacturers want to use fewer packaging materials to address environmental concerns.
In such a fluid environment, where new demands are being made every day, it pays to stay close to the customer. How to build packaging equipment from a customer’s point of view comes naturally for Hartness International.
Founder Tom Hartness started out as a Pepsi bottler in Greenville, S.C., in 1940, and soon was working on projects to improve the efficiency of the plant’s operations. A breakthrough came in 1945, when he invented a grid system for placing bottles in cartons. He began selling case packing equipment to other bottlers, and Hartness International was born. Today, Hartness has equipment at work in 160 countries and all 50 states, and a customer list of food and beverage and household chemical companies that reads like a Who’s Who of the world’s major consumer products manufacturers.
Constant innovation has led Hartness to a product line that extends far beyond case packers to encompass complete packaging lines. We’ve formed new Hartness divisions to focus on integration, robotics, automation, conveyors and production performance solutions.
Be Preferred. Innovate
“Customers want to go to one source for an integrated packaging line solution, and that means we have to continually evolve to stay competitive,” says Robert Beesley, engineering manager. “And since packaging is always changing, the systems we build are highly customized.”
Waste not
Figure 1: The latest Hartness machine, GlobalShrink, targets the packaging industry’s need for systems that help to reduce the amount of packaging material used.
Source: Hartness International
Our latest introduction, a shrink wrapping system, reflects the continuing evolution of the industry, which wants to reduce the amount of packaging material being used (Figure 1). GlobalShrink film-only multipackers and tray-former shrink wrappers are especially useful for manufacturers selling to club stores such as Wal-Mart, Sam’s and Costco.
“Manufacturers also want packaging equipment to perform reliability, be easy to monitor and diagnose line performance, and quickly change to accommodate different products and packaging requirements,” adds Beesley. “They also want to use fewer operators on their packaging lines.”
Keep It Simple
We use a design approach called “simple innovation” because it eliminates complex control schemes in favor of systems that are easy to operate and maintain. Lean engineering principles and cellular manufacturing techniques enable us to build a new machine in as little as 12 weeks from purchase order to shipment. We even make many of our own parts with steel that is laser-cut at our Greenville plant, and that gives us great flexibility.
The GlobalShrink platform demonstrates how we design packaging machines to achieve the extreme flexibility that customers demand. “Able to pack bottles on four-wall trays, on wall-less pads or with two-wall U-boards, or just with printed or plain film, these machines can be built to perform at 60, 80 or 100 cycles a minute,” states Beesley. “An 80-cycle machine running two lanes of bottles, for example, can pack 160 six-bottle packages every minute.”
Bottles are fed in a continuous process from the filler into the packer using a large conveyor. This mass flow of bottles feeds into a combiner that organizes the bottles in up to eight lanes, where a collator separates them into groups of the appropriate number of bottles. If a tray is required, the machine feeds a tray under each group of bottles, folds up the sides and hot glues the corners. Film is unrolled automatically and fed up and around each package. If printed film is used, sensors ensure that the film is correctly positioned on the package before a knife cuts the film. Each film-wrapped pack is then fed through a heat tunnel for shrinking.
“Controlling this complex set of movements at high speed is compounded by the trend toward lighter-weight bottles with thin walls that are softer and petaloid bottoms that make them unstable,” states Beesley.
“In a typical machine, our engineers use a combination of eight servomotors (3-7 hp) with attached gear boxes, five three-phase AC gearmotors (½-2 hp), encoders and dozens of photoelectric and proximity sensors to ensure precise motion control at all stages of the process.” The master controller is a PLC, and the brand we use varies depending on whether the machine is for use in the U.S., Europe or Japan.
Gear Reducer Is a Key Component
A gear reducer unit is used with each motor, whether it is integrated in a gearmotor or attached to a servo motor, to ensure delivery of the necessary torque. “Servos connected to gear reducers, for example, are used when timing is critical and rapid acceleration is required, such as when film is moving at 200 ft/min and must be cut precisely,” says Beesley. “In constant speed applications, such as filler machines requiring rotational movement, a gearmotor with encoder feedback has proven to be an economical alternative to servos.”
Before Hartness started to use SEW-Eurodrive gearmotors, we had to buy the motor and reducer and integrate it ourselves. It took 20 minutes more in machine assembly time and occupied 3 in. more space. This change also eliminated a coupler, so there’s one less potential point of failure. SEW provides us a more convenient, economical solution that has helped us to make our machines both smaller and more reliable.
Match the Component to the Need
Figure 2: Servos with gear reducers are used when timing is critical and rapid acceleration required, such as when film is moving at 200 ft/min and must be cut precisely.
Source: Hartness International
“Gearmotors from SEW-Eurodrive are standard on Hartness equipment,” adds Beesley. “Not only is the quality and reliability of its products very high, but the company offers a wide range of sizes and torques and builds to order very fast. Since all SEW products are modular, we’re able to use different components to engineer solutions for different motion applications.”
Efficiency Saves Energy
Hartness was the first U.S. OEM to use new energy-efficient motors from SEW in equipment being sold to Australia, where strict energy-efficiency standards are now in force. The new Australian standard, called MEPS2, is similar to that for NEMA Premium motors and requires small motors to be 10% more energy-efficient and large motors, which are inherently more energy-efficient, to be about 2% more efficient. MEPS2 standards require 80.5% efficiency for a 1 hp, four-pole motor, for example, and 95.2% for motors 200 hp and above.
“But efficiency and energy savings aren’t the same thing,” says Beesley. “In applications like packaging that require frequent starts and stops, using a MEPS2 or NEMA Premium motor can be counterproductive because of the higher amount of energy and longer time it takes to get these motors to full operating speed.”
The real key to saving energy in packaging applications is the gearing. “Standard worm gears are only 50–80% efficient, while helical-bevel gears have an efficiency rating of 95%,” adds Beesley. “Combining a standard motor designed to handle frequent starts and stops with a helical-bevel gear unit, saves customers more energy than using a premium efficiency motor.”
Another innovation helped us improve operating reliability in washdown or corrosive environments. SEW developed an encapsulated motor with an epoxy resin that completely surrounds the stator. This non-porous material replaces the air that normally surrounds the stator windings. “By keeping moisture and cleaning agents from reaching the windings, the resin prevents this very common form of motor failure,” states Beesley. “It’s been especially important for keeping machines running reliably in breweries, dairies and other washdown environments or in applications where the liquids being packaged are corrosive, such as bleach and orange juice.”
Service Supreme
SEW is the type of company that will jump through hoops for us when we need them to. Our engineers like to tell the story of when new gearmotor sizes were required for machines built at the Hartness facility in Anzio, Italy. SEW’s U.S. headquarters had the gearmotors quickly assembled in Germany and then flown to Rome. When a truck couldn’t be secured, SEW hired several taxis to deliver them to Anzio in time to meet our customer’s delivery date.
Distributed, Modular Control
Hartness continues to innovate to keep pace with changing customer demands, like adding robotic palletizers to packaging lines so thin-walled bottles can be stacked more gently. We’re also moving to distributed control systems with Ethernet-based I/O to further reduce wiring and assembly time.
“In a centralized control system, every sensor and actuator has to be wired back to the control panel,” says Beesley. “By distributing control, machine functions can be governed by the drives, I/O blocks are located on the machine, and wiring is reduced to a 24 V power cable and an Ethernet cable, which eliminates hours of work and a lot of wires. Since a typical packaging line is 80 ft long, a finished machine must be divided into separate sections for shipping. A distributed control system simplifies reassembly and reduces wiring errors in the field.”
Hartness engineers also are making machines more robust and reliable by moving from analog to digital technologies in both electrical and mechanical systems. “Our drop packer is a good example of that,” says Beesley. “It now uses servos to replace air cylinders, which are prone to inconsistent pressures, water in the lines and wearing on seals and bushings.”
The speed and repeatability of changeovers is another area of focus for Hartness’ engineers. Manual changeovers require the presence of an operator and potentially cost hours of downtime to switch mechanical components and test a new setup. By automating changeovers and controlling them through a machine’s HMI system or by adding color-coded letters, blocks and precise scales to reduce operator errors, we make it easier for customers to handle different products and package sizes on the same production line.
Scott Smith is director of sales and marketing at Hartness International, headquartered in Greenville, S.C. Learn more about the company at hartness.com.
Sometimes meeting a customer’s machine performance requirement revolves around finding the right component. Hartness International found the gear reduction they needed. What’s your “key” component? Tell us at ControlDesign.com/component.
Latest from Vertical Industries
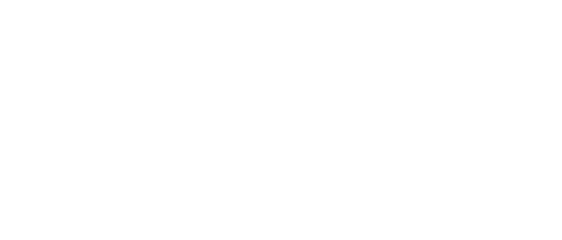
Leaders relevant to this article: