Paper Converting Machine Company (PCMC) in Green Bay, Wis., makes the converting machines used by leading wet-wipe manufacturers. The company is always looking at upcoming trends in the market to find new ways to provide more value for its customers. It has been particularly innovative with its patented rotary saw cutting technology, and it is PCMC's latest saw, the Mako, that earns the 2011 Innovator Award. It's a cutting-edge, two-bladed, high-speed rotary saw application that increases throughput, and provides flexibility for wet-wipe converting processes.
The Web of InnovationNon-woven fabrics, such as wet wipes, are made by a process that creates a single sheet of materials from a tangled web of separate fibers such as cotton or rayon. Fibers are made into liquid slurries with water and other chemicals, and the resultant paste is pressed into flat sheets by rollers and then dried to form long rolls of fabric.
A converting machine folds the individual webs into various shapes that will "pop up" from the wet-wipe container when they're packaged (Figure 1). Once folded, the webs form a ribbon that is essentially a long stack of wipes that haven't been cut. The machine then cuts the ribbon to individual lengths that get wrapped into a conventional package.
Traditionally, adjusting the cut length of the stacks required changing mechanical parts followed by manual re-timing of those parts. PCMC wanted to improve throughput on its wet-wipe machine by designing a faster saw cutting application that would allow operators to adjust cut lengths with the push of a button. The challenge for PCMC was that this capability didn't exist at the time. Making this change represented a step forward for the non-wovens industry, and required PCMC to tap into some of the newest automation technologies.
"PCMC is an established industry leader, and we believe that's because we're constantly looking for ways to provide more value for our customers," says Rodney Pennings, product line engineering leader at PCMC. "With the Mako saw application, we wanted to think about how we could continue to improve the value customers gain from our machines, while designing technological improvements that would move the industry forward."
Because PCMC was seeking a significant step forward in its saw cutting technology, the company decided to take a mechatronic approach early during machine design in order to validate the performance of new concepts and save testing time in the future. Mechatronics — a combination of mechanical, electrical and control engineering—offers a collaborative, interdisciplinary approach to machine design that helps machine builders bring engineering processes closer together to achieve faster time to market, and reduce design and development costs. This was the first time that PCMC had applied some of the latest mechatronic design tools, so again it was faced with the challenge of applying new technology to provide greater customer value.
A Cut AbovePCMC set out to design a saw cutting technology that would significantly increase the speed and throughput of its wipes converting machine. The high-speed rotary Mako saw cuts wipes at speeds of 500 per minute with a two-bladed, servo-driven head and drum. It is 67% faster than its predecessor, and is said to be the highest-speed saw cutting application on the market today.
The Mako saw technology is used primarily for PCMC's Clipper series, which runs a wide range of materials and accommodates almost every flat-pack format. But Albaad, a leading wet-wipe manufacturer that produces 9,000 tons of non-wovens each year, has the Mako saw installed on a PCMC Mermaid machine, which was put in place in September (Figure 2).
Before we got the PCMC machine, we were producing with much smaller machines," says Jürgen Kockmann, technical manager at Albaad Germany. "The new PCMC machine is three times faster than our old machines, and the machine setup, because of product changes, is much easier and faster."
Those product changeovers are more important than ever in today's versatile wet-wipe market. Albaad, for example, says it can customize a full range of wipe characteristics, including embossing, aperture, sheet thickness, colored wipes and printed wipes. The wipes can be loaded with a variety of aqueous solutions, gels or lotions. They can be fragranced or alcohol-free, they can be enriched with vitamins, or they can contain other additives such as chamomile, aloe vera or lavender. All of these materials are cut and folded to varying dimensions as well, to be packaged for at-home or on-the-go use.
That's a considerable change over previous market conditions, and customers are asking for increasingly varying product, Kockmann says, each with its own characteristics. "Therefore, it is very important for us to have very flexible and fast machines. A few years ago, we could run with a machine setup application a week or longer. Now, we have to change the machine setup nearly every day," Kockmann adds.
A Little HelpAs a company-level Machine Builder partner within the Rockwell Automation PartnerNetwork framework, PCMC got help from Rockwell with the advanced design software and automation technology needed to achieve, not only its aggressive throughput goals, but also the kind of flexibility needed by wipe manufacturers.
The Mako application was PCMC's first foray into mechatronics, so Rockwell applied the simulation using its Motion Analyzer software. Because the simulation correlated closely with the actual results on the test floor, PCMC gained the confidence to use the model in the future.
"We feel mechatronics can help us in the future, saving test time in assembly, because it will help eliminate rework of replacing drive and motor combinations," Pennings says. "We'll also save time by more fully testing our applications in a simulation environment before we get to the plant floor."
No Crashing BladesAnother major benefit that PCMC has achieved in its Mako technology is the reduction of spare parts. After being acquired by Barry-Wehmiller in 2005, PCMC worked to incorporate its new parent company's lean manufacturing principles, including reducing the number of components in each machine. This initiative still stands today, and the use of Allen-Bradley direct-drive, rotary servo motors helped PCMC reduce spare parts on its saw cutting application by 25%.
PCMC also took advantage of a brownout protection feature implemented on the machine's electronic drives, which helps ensure that the saw blades and the segmented support stay synchronized in the event the supply of electricity is interrupted.
Loss of coordination between the two would mean destroying the saw, and create a potential safety risk. This feature is particularly important to PCMC because its machines frequently are shipped to countries where brownouts are common.
PCMC needed to be able to maintain power of the drive system long enough to stop the blades (Figure 3), while coordinating the machine to stop as quickly as possible to avoid crashing the blades. An integrated motion solution allows PCMC to stop the blades within milliseconds of detecting a brownout condition. "Between the size of the blades and the physical structure holding them up, there is an incredible amount of inertia when the machine is running," Pennings says. "There's no way a conventional motor would provide the control needed to stop the blades as quickly as we're able to with the Kinetix technology. With conventional motors, we'd be looking at one to two seconds, at best."
Based on the results of the Mako application, PCMC has plans to apply mechatronics in the next generation of the technology. Pennings estimates that future applications using mechatronics have the potential to reduce testing time by 50%.
Albaad is also looking to what its new PCMC machine can do for future development. "The Mako saw and also the complete Mermaid machine are based on a highly computerized machine technology," Kockmann says. "This gives us a lot of options for production and machine optimizing in the future." One flip side of that, however, is that the more complex machine technology means that Albaad has to bring its own technicians to a higher standard to be able to use all the available options, Kockmann adds.
But it's worth it in the long run. "The competition in the wet-wipes market is very hard," Kockmann sums up. "The prices for the products have been decreasing dramatically in the past years. For us as a production company, this means that we have to increase the machine output and decrease the production costs every year. Machine components like the Mako saw help us a lot in this matter."
To deliver the innovations Albaad and other customers need, PCMC gives much credit to the help from Rockwell Automation. "From mechatronics to motor and drive selection to startup support, Rockwell Automation provided an immense amount of value during every step of the design and delivery process," Pennings says.
How to Win a Control Design Innovator Award It's like Steve Martin says about how to be a millionaire: First, get a million dollars. If you want to win Control Design's coveted Innovator Award, first, be an innovator. What we're looking for are industrial machine builders and system integrators who have used automation and controls technology in an innovative way to increase machine performance, reduce costs, improve marketplace standing, overcome competition or secure other outstanding results. If you've done that, then the hardest part is already complete. Next popular truth: You can't win if you don't play. We typically open nominations around the start of each year, with a final deadline in mid-April. But the reality of the matter is that you could send in your nominations any time, and we'll consider them for the next round. Send your nomination — whether you're nominating your own company or perhaps a customer's or supplier's company — to Aaron Hand. The main things we want to know are what machine you're nominating, what it does, which industry it serves, what components/technology it uses, and what makes it so special. Tell us your story, and get our attention. Now here's the part that has been the downfall of many an innovator: Get us some customers to talk to. If we are going to be able to truly judge the impact that your innovative machine design has had, we need to be able to get it straight from the horse's mouth. We need end users who are willing to go on record with their own stories about how your innovative machine has helped them produce faster or smarter or more cost-effectively; how your innovation has helped them get ahead in their markets. This not only will help Control Design's editors judge the merits of your machine, but will also help us tell a story worthy of sharing with your peers. Still have questions? Send them along to [email protected], or call 630/625-1177. |
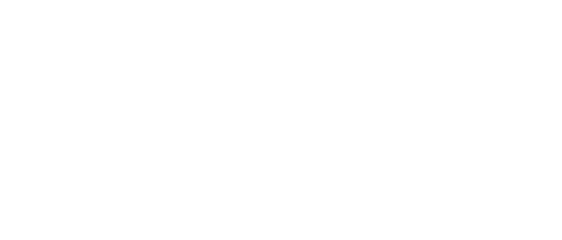
Leaders relevant to this article: