In 2013, Aaron Hand was the managing editor for Control Design and Industrial Networking.
Introducing the company to the public on its website, Aagard, a small packaging equipment manufacturer in Alexandria, Minn., makes a pretty bold statement about motion, noting that it creates, controls and analyzes motion "in ways not seen before." When it comes to innovating motion, there's no standing still.
"It's fairly easy to build a mechanical mechanism, but how the motion is controlled with other mechanisms is the key to our unique approach," says Brad VanderTuin, engineering manager at Aagard, adding that the company is able to build equipment that's smaller and faster than its competitors' equipment.
SEE ALSO: Innovation Keeps Motors Humming
To achieve this, Aagard's engineers plan out a machine's motion carefully early in the design stages, using tools developed internally for timing charts and motion analysis, VanderTuin says. "We get both our mechanical and controls engineers involved in that discussion so that it works for both disciplines."
Brenton Smith founded Aagard 16 years ago. His plan was to create a company that could focus on more innovative systems; that would create completely custom designs for the packaging industry.
Aagard's key market is food packaging, and machinery includes cartoners, sleevers, case packers, palletizers and horizontal form/fill/seal machines. With more demand for new and different package designs that continue to evolve, the food industry comes to Aagard for custom solutions.
"That's been a strength of ours — being able to look at each application a little bit uniquely, and not trying to take a standard piece of equipment and make it fit into a situation," VanderTuin says. "We have some standard approaches; concepts that we try to implement and reuse. But we take a little bit more of a clean-slate approach to a project when it's needed."
To help achieve customization at a reasonable timeframe and price point, Aagard has largely modularized its design. "Going to a more modular approach to programming lets us reuse code from previous projects more," says Daren Myren, controls engineer. "Because we reuse our own machine assemblies, we're able to reuse the majority of the programming for that portion of the machine as well."
Aagard began working on modular concepts in the early 2000s when it developed its original controls platform, and it's been evolving ever since. A couple years ago, the machine builder switched its machine control from a PC-based platform to Rockwell Automation's PLCs, including its Integrated Architecture system with Power Programming. "We had ideas on what we wanted to change to make programming easier," Myren says. "We evaluated Rockwell's architecture, and it fit very well with what we were looking for. It allowed us to be more modular and reuse more code."
Until recently, PLCs couldn't achieve the necessary scan time with the axis count needed in Aagard's equipment, which is why the machine builder relied on a PC platform. "It was not a good fit for PLCs because they didn't have the capacity we needed," VanderTuin says, explaining that the situation has since changed. "The advancements in PLCs are significant. They're now at the level that would support our equipment."
Newer, faster processors, along with more available tools, have a lot to do with the PLC's increased capabilities, according to Myren. "We can now have coordinated motion across multiple PLCs," he says. "The PLC is really becoming more flexible. I don't want to call it a PC, but it's going in that direction. Yet you have the security of a PLC. The PC has some security risks, and the PLC is a more stable controller."
As Myren notes, Rockwell has changed to calling its controllers PACs, which incorporate more than just logic control, integrating PC functions into the controller. "From my standpoint, it does not matter to me whether it is called a PLC or a PAC," Myren says. "It's the functionality that I care about."
As an example, Myren points to a machine that Aagard's engineers are working on now — it has 52 axes controlled by three PLCs. "Because of the speed of part of the machine, we're limited on the number of axes and the amount of programming we can have," he explains. So the machine coordinates motion across all three of the PLCs.
It's easier these days to coordinate the PLCs, he says, because of the tools that Rockwell has integrated into its controllers. CIP Sync, for example, is a time-stamping synchronization technology that enables motion to happen at specific time points. "There are new tools and new products that allow us to control that timing relationship easier," Myren says.
Last fall, one of Aagard's machines was used to demonstrate machine-mount ArmorBlock I/O at Rockwell's Automation Fair. "That in particular had CIP Sync," Myren notes. "That's what allowed us to precisely locate product so the robot could accurately pick up that product and place it on the other products."
CIP Sync is accurate down to the microsecond level, Myren adds. "We don't receive product location data every microsecond because the controller is not able to handle the scan time. So we receive it at a later time, but we know exactly when the product passed the photoeye. This tells us the time when the product was at a certain location. With our knowledge, knowing how fast a conveyor is moving, we know exactly where the product is when we receive the data."
Taking motion to the next level, Aagard has recently implemented an automated motion generation technology that fits in with its modular design methods. It's the motion that typically changes a lot, depending on speeds and distances required, Myren notes. "Calculating the motion through formulas allows us to reuse the formulas without rewriting the code," he says, explaining how each module could have specific types of motion. "You generate the speeds and profiles of that motion with formulas or calculations. The input to that formula is what changes. So with product size or mechanical changes, it generates the profile that's necessary to run the product. With that, we don't have to change the code, just the input parameters into the code."
Aagard continues to look for new ways to improve its machinery. On the company's wish list from suppliers would be the ability to integrate more of its own design tools into the automation platform, Myren says. "From our standpoint, we want to further our automatic motion generation and continue to develop that so that our customers receive machines where they enter in product characteristics and the machine automatically generates motion for that product."
VanderTuin adds, "This gives them more flexibility in the long term, as they develop new products that they didn't yet know about when the machine was ordered."
Aagard recently made a foray into a new area, developing a stretch wrapper to be integrated into palletizing functions. "The customer came to us with a case packing and palletizing project," VanderTuin relates. "The cases were very unstable on the pallet because of the weight and size of them. So we developed a stretch wrapper within our palletizer, containing each layer and stretch wrapping as we go."
The full system, including four case packers, was implemented using Rockwell's Rapid integration solution. "The case packers are all running different recipes, so control is very important," Myren explains. "It was very easy to implement the Rapid integration solution into our system because the systems were all designed using the base architecture of Power Programming."
Because of the wide variety of products this particular customer runs, it was here that Aagard recently created and developed the automatic motion generation. "It's the first project where motion is completely automated," Myren says. "They had been here for just a couple days, and they created their own recipe and set up a brand new product by themselves because all they had to do was enter product dimensions."
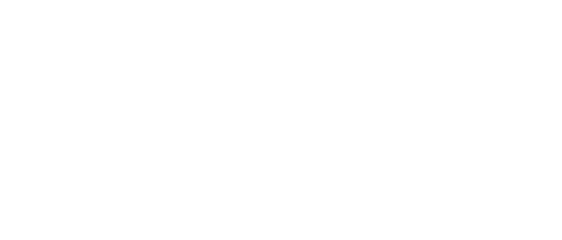
Leaders relevant to this article: