CONSIDER THE CASE OF A MACHINE OR SYSTEM BUILDER THAT has a large installed base: Some of the machines and systems are on controller platforms supplied by one automation vendor, while others are controlled via other vendors' products. Any new projects and/or upgrades envisioned probably will have to accommodate those disparate systems and machines because of end-user insistence and the knowledge already invested in those machines.
Cofely Services' Airport Group can identify with this situation. It operates in more than 25 airports, including Boston-Logan, Louisville, Kentucky, Montreal Pierre-Elliott Trudeau, Paris Charles de Gaulle, Athens, Brussels, London Gatwick and others.
Dual Platform Support
When Yan Le Meur, automation and technology watch expert with Cofely Services, began to evaluate I/O solutions for a baggage-handling system (BHS) project, he indeed defined a specification that required both an EtherNet/IP- and Profibus-compatible device that could communicate with Allen-Bradley and Siemens PLCs.
"We didn't want to move away from the Siemens and Rockwell platforms due to end-user requirements, our own investments in supporting current solutions and employee/user comfort level," Le Meur says.
The bag room improvement project at Halifax Airport, Nova Scotia, was designed to transport baggage from check-in to carousel (Figure 1). About 100 conveyors are used to transport the bags. Each conveyor is equipped with encoders and infrared sensors with deflectors used to track bags or to detect a bag jam; a selector to start/stop the conveyor in automatic or maintenance mode; and motors from ½ to 2 hp, depending of the size of the conveyor. All this equipment is controlled by a safety PLC, and safety logic is handled by the software. Conveyor speed range is 0.7 to 1.5 m/s. During peak periods, each line can carry about 600 bags per hour into a secure area. Lines must be ready to operate from 3 a.m. until 10 p.m., 7 days per week and 52 weeks per year.
Also Read: Infographic: What Type(s) of I/O System Do You Use?
Transport time is critical to guarantee that bags arrive in time to be loaded onto an airplane, so every component must be reliable, and every fault must be identified and fixed as soon as possible to have a very low mean time to repair (MTTR). Each line also is equipped with an automatic tag reader (ATR) that sends bag data to high-level software, Bagstage, which was developed by Cofely Services. This software is used to track bags into the system and to inform the PLC as to which line must be used to send the bag to the final destination. All alarms and status are displayed on seven redundant SCADA viewers in different rooms and areas or on mobiles, and also could be accessible remotely via a VPN connection. For maintenance, alarms are logged to a historian in order to retain operating data.
Improve the I/O Scheme
Figure 1: During peak periods in the bag room at Halifax Airport, Nova Scotia, each line can carry about 600 bags/per hour into a secure area. Lines must be ready to operate from 3 a.m. until 10 p.m., 7 days per week and 52 weeks per year.
Baggage handling systems often have long conveyors with many sensors distributed among them. In a traditional, centralized solution, the sensor cable would be tied back to a main control cabinet, resulting in substantial labor and cable cost.
Another possible solution would be to use remote or distributed IP20-rated I/O. This type of solution can reduce cable lengths, but multiple junction boxes are required on the machine. "The cost of junction boxes can add up quickly, so it's important to evaluate the cost of cable, junction boxes and I/O," Le Meur explains. "Cofely Services was well aware of the additional cost associated with traditional solutions. Our knowledge and experience prompted us to specify machine-mountable I/O with IP67-rated protection."
The length of the conveyors had a lot of influence on the selection criteria for this application, Le Meur adds, saying, "Flexible topology and the ability to carry signals long distances between I/O modules therefore became a key differentiator in supplier selection."
Cofely Services wanted to integrate advanced diagnostics in order to make troubleshooting the system easier for the end user. Implementing advanced diagnostics in the system would let the end user identify faults and errors much sooner and result in less downtime and more overall productivity. "LED indicators on each module indicate general and detailed errors in the SCADA system," Le Meur explains. "And because this information is easily accessible by the web server included in each module to provide a completed detailed diagnostic and status, we don't need to develop it on our side. On each conveyor, we can detect faults such as motor overload, encoder faults and bag jams."
The scan time of the network was an important consideration, too. About 2-millisecond (ms) scan rates are needed in order to connect the square signal encoder on a standard I/O module, and move this signal into the PLC's Fast Task. Cofely Services wanted to use an encoder directly on classic I/O, so there would be no need to have a high-speed card. In addition, the company wanted to have the flexibility to set up I/O on devices to connect a motor or a sensor. Conveyors are standard for I/O, but sometimes we need to locate some extra pushbuttons, lamps or stack lights close to this equipment.
Serial communication was also an important point in order to communicate with scales or automatic tag readers. Cofely Services wanted devices that could be easily integrated in both EtherNet/IP and Profibus-DP.
"A final important criterion," Le Meur adds, "was that every sensor was to be wired for M12 connectors and terminal blocks to decrease device wiring time and wiring error."
Decision Criteria
Figure 2: Instead of hard-wired or centralized design, all conveyor devices including motors, encoders, stack lights, selector switches and disconnect switches are connected to remote IP67-rated I/O nodes.
"Although we found multiple vendors that could provide us with a solution that met the specifications, we decided that B&R Industrial Automation (www.br-automation.com) could provide the best solution for the application," Le Meur says. "We found the B&R solution was cost-effective, reduced the total number of components and would be easy to support. The I/O is easy to support, even when integrated with a third-party master. This is due to the advanced diagnostics on the hardware LEDs, as well as in the software. Cofely Services engineers could program, troubleshoot and commission the application all within the STEP7 or ControlLogix/RSLogix platforms they already are very familiar with. All of the diagnostics information such as short-circuit, overload and reverse-polarity protection is monitored in the controller tags sections of the Allen-Bradley PLC and the Siemens Step7."
Gary Martins, vice president of B&R, reports, "B&R has a 16-channel, digital mix module, which has 16 configurable input or output channels. The added functionality provided by the built-in ‘function models' allowed Cofely Services to configure one of the standard channels as a high-speed counter to be used for an encoder with square signals. This helped reduce the total number of components required for the application because a single module could be used for digital inputs, digital outputs and high-speed counters."
A bus controller for both Profibus-DP and EtherNet/IP was also a key differentiator. "These devices allow fieldbus communication with Siemens and A-B PLCs with the same I/O module and a very fast (1-ms) network scan time," Le Meur explains. "This provided the benefit to keep the same module instead of different I/O devices, and for maintenance, it meant a decreased spare parts list."
It also offers many benefits to be able to communicate with serial devices and easily could be connected with an M12 connector to serial controller. It was linked to Cofely's ATR, and the LEDs were really helpful to diagnose Rx and Tx communication signals, adds Le Meur.
Installation and Commissioning
The use of machine-mount I/O reduces cost compared to a centralized, DIN-rail-mounted I/O system. A majority of the cost savings associated with machine-mount I/O are realized in the installation and commissioning phase. "If you only compare the cost of goods, IP67 I/O might appear more expensive," Le Meur says. "But when you evaluate the cost of cabling, you will see reduced wiring time, less cable and faster start-up times."
Some additional cost savings will come from simply moving the I/O out of the cabinet and onto the machine. "With fewer components in the cabinet, we can reduce the size of the cabinet, resulting in lower cost," Le Meur adds. "Not only can the size of the main control cabinet be reduced, but also the use of junction boxes on the machine can be eliminated completely. Before we made the change, each conveyor had a small decentralized panel (DCP). Now with this IP67-rated and M12 connector solution, we eliminated about 70% of those panels."
He adds, "Industry-standard M8 and M12 connections can account for huge time savings when wiring the machine. Instead of stripping and terminating wires, you simply use a torque wrench to screw on the connections from the sensors to the I/O. These standard cable connections also result in fewer wiring errors and quicker commissioning times."
He continues, "On another similar project, we had a lot of errors due to the number of manual connections that caused short circuits, created a poor understanding of wiring diagrams and so on. Now we only have to train people to understand the M12 connectors approach, and for the first part of this project, we didn't have any damage due to short circuits—and we reduced time and cost by probably 30%. We also observed that we decreased the time to commission I/O on both PLCs because I/O modules are similar configuration."
Mounting the I/O on the machine directly next to the sensor or actuators reduces the total cable length required for the system. All of the benefits given by IP67-rated, machine-mountable I/O lead to reduced total cost of ownership.
Le Meur says that Cofely has received no complaints from the customer and the maintenance team onsite, and another advantage for the customer is that it can have the same module for both PLCs, reducing the cost of spare parts.
After commissioning, Cofely Services also will need to support the installation site round the clock from its call center for about one month.
Training
Minimal training was required in order to implement the solution. The B&R I/O can be programmed within ControlLogix, Step 7 and many other third-party software platforms. This greatly reduces the cost and learning curve associated with making changes.
"B&R Industrial Automation offers a free configuration software called fieldbusDesigner, which generates a .L5K file," Martins explains. "When this configuration file is opened in ControlLogix, a generic Ethernet module is added to the project, the I/O data populates the controller tags, and all input and output sizes are automatically defined. For Profibus you just need to import a GSD file in the hardware configuration of Step 7."
As a result, the programmer is now working in a software platform with which he is comfortable.
The Road Ahead
"Ethernet is now the standard for fieldbus and, combined with IP67 modules and M12 connectors, this is definitely something that we want to propose for our next project," says Le Meur. "The other point is we easily could have the same connectivity and module on any kind of new or existing network. We will continue to promote this kind of solution to our customers because it's an honest win-win solution for everybody.
"For future projects we'll continue to include web server access from our SCADA, so it could provide for easy access inside or outside by a secure VPN connection. Equipment or controllers with an integrated OPC UA server seems to be an interesting option for communication.
"Wireless also is something that we could consider for other projects, not only for airport projects."
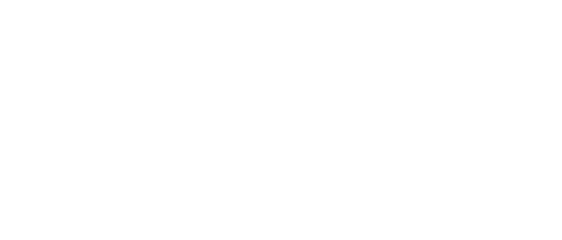
Leaders relevant to this article: