Wireless Unbound: Gather Data and Signals From Difficult-to-Reach Devices
Over the years, industry has implemented wireless technology with relative degrees of caution, depending on the application. Complaints about wireless' steep learning curve have hindered certain users, applications and plants from using it, as have valid worries about security and concerns about the reliability of devices, such as transmitters that quit for no apparent reason. That said, many users are adopting wireless technology in increasing numbers because it lets them gather signals and data from places where they couldn't get them before. This helps cut costs, improve safety, boost productivity and manage assets better.
Consider the case of Reliance Industries in India. The company was having problems obtaining reliable tank-level and temperature readings at its Baroda GOP olefins plant in Gujarat due to difficulties stemming from retrieving transmitter signals of tank levels and temperatures from the farthest sites in its petrochemical complex. The existing wired setup was remotely located and needed continuous troubleshooting and maintenance.
Figure 1: In situations where monitoring a remote location with a wired network would be tricky, such as the Eyjafjallajökull volcano in Iceland, cellular networks provide an alternative network connection for sensors such as seismographs and GPS receivers.
"Reliance already had a suitable Honeywell distributed control system (DCS), so it installed the company's OneWireless network with solutions such as XYR 6000 wireless transmitters to gain control of data, streamline tasks and improve overall efficiency," says Mahendra Upadhyay, instrumentation manager at the Baroda GOP plant. OneWireless is a standards-based, industrial, wireless mesh network that complies with the ISA100 standard and is intended to extend process control networks to the field, allowing transmission of more information to central locations.
Obtaining temperature and level signals wirelessly from Baroda GOP's remote sites lets Reliance eliminate cable, labor and maintenance costs. In addition, wirelessly monitoring and controlling the tank liquid volume helps ensure data accuracy for planning and scheduling. The implementation also improves employee safety because personnel no longer need to travel to remote locations to monitor tank levels.
Also read: Implementation of Wireless Networks Takes Time and Patience
"A real trend has process companies requiring such standards-based approaches to wireless as OneWireless," says Vibhor Tandon of Honeywell Process Solutions in India. "Its compliance with ISA100 Wireless allows it to use a tunneling technology that enables communication of other protocol data over the ISA100 network. For example, users can extract HART data from their wired HART devices using the OneWireless Adapter (OWA) that securely sends the HART data over the ISA100 Wireless network to the HART clients like Honeywell's Field Device Manager (FDM) or Emerson's AMS."
In the future, Tandon says wireless is headed toward developing a protocol for the Internet of Things (IoT), as well as one for a way to handle big data. "However, IoT and other technologies will have to be tailored for the process industry for appropriate adoption," he adds.
Tipping Point
Once a wireless technology hits a tipping point in the consumer world, industry adopts the technology and advances it, explains Mike Fahrion, product management director and IoT strategist at B&B Electronics. "A lighter, smaller version of Bluetooth called Bluetooth Low Energy (LE) was recently developed for sensors," he says. "In consumer applications, Bluetooth targeted applications in retail grocery stores placing tiny battery-powered beacons that send out their IDs. Holders of frequent shopper cards can download an app for their smartphones that works with the technology to help users navigate the store and get special offers."
The idea in industry is to place similar sensor tags on the factory floor. "So, instead of companies putting expensive custom-built HMIs on a machine, an operator with an iPad can walk up to the machine and use the tablet as a virtual HMI, using short-range communications to the device over Bluetooth LE," says Fahrion. "Or a technician can walk up to a cabinet and doesn't have to open the door to see what the oxygen level or temperature is inside."
Flexibility Is Key
Many companies want to use wireless to give them more flexibility and control in extreme conditions. One example comes from Aggreko in Glasgow, Scotland, which provides large and temporary power installations in remote locations. In one installation, Aggreko replaced Ethernet cables laid in cable trenches between its generators with wireless Ethernet using B&B’s Ghostbridge wireless Ethernet bridge to make Aggreko's entire SCADA system wireless. The wireless devices installed on the generators are connected to Modbus TCP serial servers, and they relay data wirelessly between the transformer units and the SCADA master. Since going wireless, Aggreko has reduced installation and de-installation time and costs and improved reliability since it's no longer susceptible to vehicle traffic over the cable trenches.
How is the system installed? A simple Power over Ethernet (PoE) device is installed inside the generator and the transformer. This allows the antenna to take its power straight from the Ethernet cable without the need for additional power supplies. An Ethernet cable is then taken from the original Ethernet connection and plugged into the wireless device, which is mounted on top of the container with supplied mounting brackets. An omni-directional antenna is installed and plugged back into the SCADA marshalling panel, allowing a secure, site-wide wireless connection.
Benefits of the approach include the capability to monitor electrical data and engine information remotely, as well start and stop generators and reset active alarms remotely.
Figure 2: Cabinets for remote stations in an energy distribution application in Belgium include systems provide a secure remote link from the central control room to the remote sites.
In other applications, where monitoring a remote location with a wired network would be difficult, a cellular network can provide an alternative network connection for a solar-powered sensor. For example, to monitor the Eyjafjallajökull volcano in Iceland, the Icelandic Meteorological Office didn’t try to run cables out to the site because of its harsh conditions, which included seismic activity, lava flows and ash fall. Instead, they used a cellular network in which solar panels powered the sensors and the GPRS/EDGE cellular routers (Figure 1). Routers from B&B’s Czech Republic-based subsidiary, Conel, connected the devices to the network.
Really Remote Monitoring
"Years ago, wireless was used mostly in applications that were just too far away and costly to wire with traditional 4-20 mA wiring," says Ira Sharp, product marketing manager at Phoenix Contact USA. "Fast forward, and wireless today also allows doing things that would never be possible with wire, such as taking a tablet onto the plant floor to wirelessly connect to an asset, upload and download new code, and perform troubleshooting on a PLC or control system."
For example, in an energy distribution application for a nationwide energy supplier in Belgium, Phoenix Contact built the cabinets for the remote stations. The system includes Phoenix ILC controllers as the control equipment and mGuard 3Gs industrial routers for a secure remote link from the central control room to the remote sites (Figure 2). In most cases, the 3G mobile network links the sites to the control room.
In another application, a machine builder might ship a machine to seven different states and four different countries, continues Sharp. "Wireless technology lets us log in to any one of the control systems," he says. "So when I'm dealing with the builders on the phone, I can look at what's actually going on in the system real time. This helps to prevent sending a technician on an airplane to various facilities. In most cases, the capability involves using cellular technology, and the nice thing about cellular is it can be used almost anywhere in the world, so it really does allow you to have a long reach to all assets."
Figure 3: The combination of a wireless module with an electro-mechanical energy converter is a basis for a variety of maintenance-free wireless switches in an industrial environment.
Similarly, system integrator Patti Engineering in Auburn Hills, Michigan, reports that it often uses Phoenix Contact's wireless technology in water and wastewater projects. "We're currently working on a water application involving 29 wells across a city," says Steven Palmgren, PE, vice president of Texas operations at Patti Engineering. "A well is basically just a pump. The city wanted to monitor current draw, or how much power a well is drawing, because that information indicates how well the pump is working. We put a Phoenix Contact Radioline 900 Mhz radio in each location, which lets us remotely monitor various process parameters and tell the pump when to turn on and off. We set up implementations, so our customers can operate the system themselves."
The Missing Link
As wireless devices push into more remote locations, some are benefiting from using extended-life batteries, while others are getting power from solar and other methods. "The problem with 2.4 GHz (Wi-Fi, Bluetooth, and ZigBee) is that they’re being loved to death, and so many devices are being added to them that interference is inevitable," says Jim O’Callaghan, president of EnOcean. "Wireless sensor networks need more reliability, and the beauty of using sub-gigabit networks like ours is that they avoid the high-density networks and their interference."
EnOcean manufactures energy-harvesting and storage devices that allow users to implement self-powered wireless networks (Figure 3). These products include energy harvesters, ultra-low-power timers and measurement assessment devices. These communicate via the firm's internationally standardized EnOcean radio protocol, which runs at 902 MHz in North America and at 868 MHz in Europe.
Figure 4: Wi-Fi is being used in a manufacturing application to collect monitoring or control information from the different stations for productivity monitoring.
This technology has its place in areas such as Cascades' cardboard factory in Montreal, Canada, which had 25 gas-fired unit heaters originally controlled by mechanical thermostats. The company wanted to reduce heating costs and improve employee comfort by centrally managing temperature setpoints according to schedules. The challenge was to integrate the heaters into the existing BACnet IP building management system. Because installing miles of conduits and wires throughout the large facility would be costly and cause downtime, the company went with wireless.
The project's contractor installed the "missing link" between the heaters and the building management system using EnOcean relays, which were controlled wirelessly by SmartStruxure Lite (formerly CAN2GO) wired and wireless controllers from Schneider Electric, and equipped with embedded BACnet IP gateways without extensive wiring costs or significant downtime. In the factory, 16 heaters are now controlled by EnOcean-based relays communicating with SmartStruxure Lite controllers. All in all, the contractor estimated a total savings of labor and materials reached $45,000 for a 25-controller project.
"The system let us centralize temperature control and generate energy savings," says Fabien Demougeot, engineering technical supervisor at Cascades. "The installation was done without disrupting our operations, which would have been impossible with traditional wired control solutions."
Different Paths
Figure 5: At the Tüpraş refinery, a device sends oil tank temperature and level data wirelessly via various components to the control system, ensuring the transmission of correct readings.
Another approach to getting wireless data from different areas comes from Red Lion, which gives users the capability to connect, monitor and control devices, explains Diane Davis, director of networking product management at Red Lion. "We don't take wireless down to the sensor level and there's no Zigbee, Bluetooth or HART communications," she says. "Our technology is 802.11n wireless, and we're seeing it used in multiple ways. A good example is automatic-guided vehicles for parts delivery in an automobile factory, which move around a track. You have the Wi-Fi being used on the vehicles themselves as stations, like your laptop moving through an office environment, attaching itself to a wireless access point. Wireless frees the vehicles from being tethered. In addition, more and more wireless devices are being used for monitoring, from phones to iPads and other devices, as well as connecting remotely to the back office for data acquisition and control." In addition, Wi-Fi can be used in a manufacturing application to collect monitoring or control information from the different stations for productivity monitoring (Figure 4).
In contrast, Pepperl+Fuchs' main focus is WirelessHART-enabled devices that monitor field instruments in the process industry. WirelessHART lets users put equipment anywhere they want and not worry about whether they have enough wires or enough room in the conduit, reports Robert Schosker, Pepperl+Fuchs' product manager. "Users also don't have to worry about running wires or burying them in a ditch only to have the application move," he explains. "Wireless equals freedom from wires."
An application example comes from a device used to measure a tank level. "When a food production facility's process was running, it pulled water from a tank to help keep equipment cool," says Schosker. "A freestanding radar gauge sat in the tank. As the processes started to ramp up, the tank required more and more water but it couldn't keep up because it was being filled by off-site wells. The company had to send in technicians to turn on a variable-speed drive (VSD) to pump more water in the tank and keep the reservoir up. At this point, all operations were manual. The idea was to make the level gauge wireless via one of our adaptors and feed data back to the controller, which would then feed the facility's PLC. The adaptor gave the level height to the Modbus card which, in turn, drove VSDs that automatically turned on the pumps at the off-site wells."
In another application involving level gages, Tüpraş' refinery in Izmir,Turkey, used an Emerson Process Management tank gauging system that includes 85 wireless radar level gauges. The gauging system is intended to provide accurate, reliable level measurements on the refinery’s most critical oil-movement tanks (Figure 5).
The Izmir facility has a refining capacity of 11 million tons per year and storage capacity of 1.9 million m3 in 164 tanks, including 44 lube-oil storage tanks that were already being monitored using wired level gauges. On other tanks, however, the existing gauging system sometimes gave incorrect readings because the cables were damaged during excavations in the field. In addition, support personnel were not always available.
A variety of wireless technologies are used in industrial applications, and the type applied depends on their different applications. WirelessHART and ISA100.11a standards are based on the IEEE 802.15 standards and use unlicensed 2.4 GHz band frequencies. These technologies have low power requirements and are relatively short range. They're suitable for sensor-type devices for process control and instrumentation. Certain wireless technologies have been traditionally used for long-haul SCADA applications and remote site connectivity:
- VHF/UHF radios use proprietary standards and licensed frequencies (150-470 MHz) and have very low data rates (65 Kbps).
- Frequency hopping spread spectrum (FHSS) radios use proprietary standards, unlicensed frequencies of 900/2,400 MHz and up to 1.1 Mbps data rates.
- Cellular radios, such as GSM/CDMA (3G), LTE (4G) and IEEE 802.16 (WiMAX) use licensed and fee-based frequencies (700-3,600 MHz) with data rates up to 100 Mbps.
- 802.11a/g (Wi-Fi) uses unlicensed frequencies of 2.4/5 GHz and line-of-sight communication, and its data rate depends on the distance (up to 54 Mbps).
- IEEE 802.11a/g/n technology is used for the most demanding applications with real-time I/O, peer-to-peer, safety control and mobile HMI. Data rates can reach 300 Mbps.
Tüpraş first considered replacing the older system with additional wired level gauges. However, because the tanks are spread over a large area and existing cabling and junction boxes were below par, the high cabling and installation costs of this approach made wireless technology a more suitable approach.
"Ground conditions make excavation for new cable runs difficult," says Ali Erener, project chief engineer at Tüpraş Izmir. "Emerson’s Smart Wireless solutions lets us minimize costs for cabling, cable trenches, conduits and cable trays. Going wireless also gives us the flexibility to add more devices in the future, both for level and temperature measurements, as well as for tank water control and nitrogen pressure control at our blanketing tanks, which are remotely located from the control room. The WirelessHART field network at the Izmir refinery will have a node for each tank, including a radar level gauge installed with an antenna unit, a Smart Wireless THUM Adapter, and a multiple spot temperature sensor to enable accurate volume calculations. Temperature and level data will be sent wirelessly to a Smart Wireless gateway, which acts as the network manager and provides an interface to the refinery’s inventory software or control system."
Latest from Data Acquisition & Monitoring
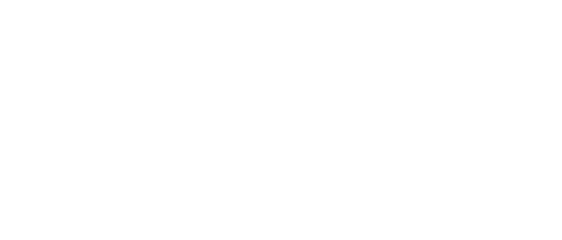
Leaders relevant to this article: