How Better Control Can Pay Off With Improved Machine Efficiency
After working as a semiconductor process engineer, Hank Hogan hung up his cleanroom suit and now writes about process control and other technologies from Austin.
Figure 1: Mechatronics controls, mass flow controllers and careful design enable a liquid filler to offer 75% better-accuracy product weight than is typical. (Source: Apacks)
Ounces count, especially when the cost of a product runs almost $2,000/gal. In that case, filling a container as accurately and precisely as possible is important. Thanks to mechatronics and associated controls, the ability to hit a weight target in a bottle-filling machine has been improved by 75% (Figure 1). A similar combination of electrical and mechanical components along with controls can improve product quality, particularly when new-to-an-application capabilities like machine vision are integrated into a system.
Fill ’er up
Take exactitude in bottle filling. It can pay off for more than just expensive products. Even common, high-value, high-volume liquids like honey can benefit, says Todd Cannon, president of Apacks. The LaPorte, Indiana-based manufacturer makes a complete line of liquid filling equipment.
Filling bottles and the like in the 1-oz to 2.5-gal size creates a challenge. They cannot underfill a bottle, since customers purchase product by weight, and accidental or deliberate shortchanging invites trouble. So, the tendency is to overfill, typically at about 1%, says Cannon.
However, that wastes product and money. In a twist to the story of Goldilocks, the goal is to get things just right without being short.
That’s what Apacks set out to do in its latest machine design, and Cannon says the company succeeded. “If you’re targeting your weight in grams or fractions of pounds, we are less than 0.25% over, instead of being 1% over,” he says.
Achieving this performance required careful attention to design and proper implementation of technology, including mechatronics and the associated controls. The fill process starts when bottles are indexed into the machine. Servo motors then drive nozzles individually down to the bottom of the container. After that, a pneumatic actuator integrated into the nozzle opens valves. The liquid begins to be dispensed, driven by clean, compressed air or nitrogen and gravity.
Individual Micro Motion Coriolis flow meters track how much weight has been dispensed by each nozzle. As the bottles fill, the nozzles retract, moving up at a rate calibrated to keep the nozzle in a fixed relationship to the liquid. Thus, when half the fluid has been dispensed, the nozzle will have pulled halfway out. This approach provides several advantages.
“The benefit of a bottom-up fill with this type of precision control is it reduces indexing time, increases fill speed in most applications and greatly reduces the foam and air encapsulation,” Cannon says.
After the target weight has been reached, the valve shuts off and a servo motor pulls the nozzle completely out. When the entire batch is done, the bottles move on, and the cycle begins again.
The machine can switch between different bottles and liquids, with an adjustment to rails and gates to account for the various sizes of containers. Changing a value in the HMI takes care of setting a different weight. The controller can also store recipes and log data, as well as offer other useful capabilities.
For instance, the software on the machine has some proprietary algorithms and techniques that enable it to reliably come in at almost exactly the perfect weight. “It’s adaptive. It compensates for any changes in temperature or viscosity,” Cannon says.
As for the future, one possibility being pursued by Apacks is the elimination of dead time in the fill cycle. The current process has several steps where bottles or machine components are moving and liquid is not. Eliminating the nonproductive time could substantially increase throughput.
“It could nearly double the speed,” Cannon says.
Controls in hand
The current machine is built upon a control platform from B&R Industrial Automation. Cannon says this offers the needed processing power and expandability to handle the present situation, as well as being able to supply what will be needed for the faster future version of the machine.
Derrick Stacey is a solutions engineer at B&R Industrial Automation. He notes that the trends in mechatronics controls, such as the drive toward modularity, flexibility and scalability, can be seen in the Apacks machine. The idea is that a control system will span everything from a single machine to larger systems and vice versa, as well as supporting the switching in and out of subsystems.
“We’re really trying to focus on a single software development package for all of the components of the machine, including safety, motion, vision, control and the I/O, all built into one software package,” Stacey says.
That all-in-one yet flexible approach can also be seen in the fact that the controls are not tied to a specific fieldbus or network architecture. This means that a machine maker can use whatever fieldbus the builder or user prefers and not be forced to convert to Ethernet or PowerLink. B&R Industrial Automation tailors its products to this fieldbus because it offers the best performance, says Stacey.
The ability to network in a flexible fashion and remotely connect to a machine could prove beneficial, he adds. Being able to access diagnostics from a mechatronics control system could help determine that a problem is not with a machine, but is instead due to issues with incoming electrical power, for instance. That, in turn, can save money.
“The last thing you want to do is have to send a tech a few times a year to understand what’s going on,” Stacey says.
Figure 2: The advent of capable tablets makes it possible for multiple HMIs and system diagnostics to be handheld, giving users the flexibility to access machine information from almost anywhere. (Source: B&R Automation)
As for the future, one upcoming change that Stacey sees happening is the incorporation of consumer devices into industrial machines and systems. This is already happening in the case of B&R Industrial Automation products.Tablets, in particular, could prove handy, particularly as they grow more powerful. With a tablet, an operator could have multiple HMIs in a single handheld device, Stacey says. This will help operator efficiency because the user interface will be a familiar one (Figure 2). Having a handheld HMI could also mean that a technician or operator could move around a machine and yet have access to all of the mechatronics information and controls.
Seeing is controlling
Daniel Nadolny, machine vision group coordinator at Epic Systems, an integrator in St. Louis, also notes the rapid evolution of consumer devices when talking about mechatronics controls. And he sees a similar distribution of computing power across devices happening in the industrial space.
“Some traditionally mechanical devices will have built-in controllers and electronics to perform tasks without the need of add-on equipment,” says Nadolny. “Machine vision cameras are adding more processing power to perform their own logic, and they do not require additional PLCs for some tasks.”
Epic Systems is experiencing increasing demand to incorporate machine vision into mechatronics systems, Nadolny reports. Often there is a desire to add image-based inspection, with gauging and measurement being one important goal. In other cases, this may involve product sorting, counting or defect detection.'
While vision cameras have been getting faster, smaller and more powerful, adding them to a system can mean that there must also be a mechatronics and control change. For instance, to achieve accurate results, parts may need to be presented to a camera, an image taken and then those parts sorted or rejected as called for by the control system. Thus, there is a mechanical, electrical, vision, and control aspect to the solution.
“A simple vision station with an integrated rejecter is a simple mechatronic system. A typical machine vision station might include a photo eye, machine vision camera performing an automated inspection, a conveyor with an encoder, a pneumatic cylinder and electronic controller to track reject parts,” Nadolny says.
He predicts that machine vision will be increasingly part of a complete mechatronic solution because it offers the prospect of greater control of a process. Instead of inspecting only a sample of the parts, it is possible to inspect 100%, thereby improving product quality and producing mounds of data.
This increasing system complexity is both an opportunity and a challenge. Michael Lennard, product manager for motion solutions at Rockwell Automation, notes that these more complex and more heavily software-dependent mechatronics systems can be flexible and faster, and can have a lower operating cost than a purely mechanical solution. They also can cost less to maintain, a consequence of the more detailed diagnostics they offer.
But, the greater use of software can be a challenge if each component and control has to be instructed what to do in its own programming language. To help minimize that burden Rockwell Automation has partnered with a wide range of suppliers so that everything can be programmed and configured using the same tools.
“This simplifies start-up, saves time and allows users to implement a wide variety of new products without having to learn additional software,” Lennard says.
Saving time and money
Having a common programming language and environment is an advantage for both machine makers and the eventual end users, says Doug Burns, director of business development at Lenze Americas. For end users, troubleshooting and maintenance are streamlined. As for machine builders, they benefit from only needing to learn one programming language and not having to worry about handshaking between different mechatronics controls.
A key trend in mechatronics is closer integration between components, says Burns. This starts, for example, with the shaft out of the gearbox or motor, through the servo drive, and all the way to the automation controller, which includes the motion programming.
The approach of one-language-to-rule-all-components streamlines programming and configuration and makes support easier. It also can save significant engineering time in going from developing an idea to producing a running machine.
“Studies that we’ve done show that you can have close to an 80% savings of time, which is significant,” Burns says.
Another important trend is the distribution of mechatronics control and components. This can cut power consumption because it can provide additional avenues for heat dissipation, says Burns. Instead of being cooped up in a cabinet that must be cooled, controllers, drives and the like can be mounted on a machine and thereby be better able to get rid of heat.
On the control front, field programmable gate arrays (FPGAs) can improve the ability of a control system to reject disturbances and maintain a machine’s desired state. Some of these programmable chips can be tailored for a given task so they perform better than general-purpose processors.
“We have FPGAs capable of doing math at a significantly higher speed than processors,” says Lee Stephens, senior motion control engineer at Kollmorgen. “This enables us to limit effects of calculation delays, propagation times and associated phase shift.”
Now, the attention to software and automation does not mean that the laws of physics have been repealed. For instance, force still equals mass times acceleration. No amount of fancy control algorithms changes that. However, better algorithms and faster controllers can help when motor load ratios are not optimum, a problem with early low-bandwidth controllers, Stephens says.
While they have to work within the constraints of the possible, better controls and better mechatronics can definitely pay off. In the case of the precision liquid-filling machine from Apacks, for instance, the return on investment for everyday liquids can be as little as six months, says Apacks’ Cannon. For more expensive products, the payback can be less than a week. “By filling with precision and speed, that delivers to the customer a very fast return on investment,” he says.
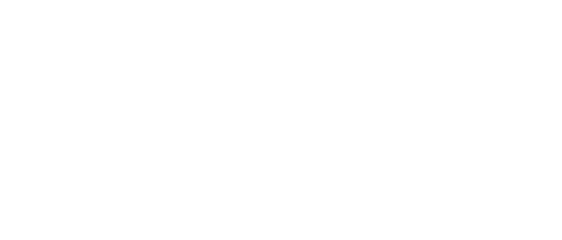
Leaders relevant to this article: