Whether your go-to beverage is soda, water, tea or juice, it's almost certain that the plastic bottle that protects your drink started out as a "preform." Looking much like plastic test tubes with a threaded neck for bottle caps, preforms are manufactured by the millions using injection molding machines. Preforms are then loaded into stretch blow molding machines that shape them into the familiar finished bottle shape.
Responsible for manufacturing preforms for an enormous share of the world's PET plastic bottles, Husky Injection Molding Systems is a global manufacturer of injection molding machines, hot runners, molds and integrated systems. Based in Bolton, Ontario, Husky has manufacturing facilities in Canada, the United States, Luxembourg, Austria, Switzerland, China, India and the Czech Republic. It also has more than 40 service and sales offices worldwide, supporting customers in more than 100 countries. Husky equipment is used to manufacture a wide range of plastic products such as bottles and caps for beverages, as well as plastic parts for the medical industry. Husky provides clients in numerous industries with complete injection molding solutions, including the machines, tooling and auxiliaries.
The PC-Based Past
Husky has been a user of PC-based control since the late 1990s, with several thousand systems in the field.
Husky has been a user of PC-based control since the late 1990s, with several thousand systems in the field (Figure 1). From the start, these PC-based machines have been based on hardware and software solutions from Beckhoff Automation. We stress a value-add approach to system design that leverages leading edge automation technologies. Husky, offering integrated system solutions, has also built a strong aftermarket retrofit program to serve customers with older Husky machines. Called Encore, this program helps customers to upgrade to modern PC-based control without having to purchase a new machine.
"We have built generation after generation of PC-based control systems, and reliable performance is firmly established with over 15 years of continuity using PC-based control architectures," says Husky Electrical Design Team Leader Endel Mell. "Over our long-term business partnership, Husky has enjoyed excellent technical support from management and product developers at Beckhoff as well as the technical services and support staff worldwide, especially in Germany, North America and China."
A major trend in the injection molding industry is the reduction of raw materials used while ensuring top product quality, which unsurprisingly requires continuous advancement in automation technology. "Through best-in-class system design, Husky maintains top part quality in the industry," says Husky Director of Development Engineering Roman Pirog. "We design the system and the automation around the part and create specialized solutions as a result. This ensures the best possible throughput, efficiency in materials use and part quality."
Increased system accuracy, responsive machinery dynamics, and repeatability — each of these is an inherent benefit of the processing on the fly and real-time data throughput associated with EtherCAT technology. Inaccuracy and slower response times are associated with higher levels of raw material waste. By implementing highly accurate and responsive devices, Husky systems are equipped to more efficiently utilize raw materials, producing high-quality injection molded PET plastic products while decreasing the levels of required raw materials.
The Husky HyPET HPP5 builds on the proven technology of the long-running HyPET platform by adding more functionality that enables end users to lower their total cost to produce while ensuring optimum preform quality.
Using automation technology to strike this balance between quality and efficient use of plastic resources is a contributing factor driving many end users to continue going to Husky for leading-edge injection molding solutions. Husky strives to increase this efficiency along with ease of use for all systems and equipment; this holds true for the new Husky HyPET HPP5, which builds on the proven technology of the long-running HyPET platform by adding more functionality that enables end users to lower their total cost to produce while ensuring best-in-class preform quality (Figure 2).
Multi-core Industrial PCs
Husky machines are introduced to the market with continually upgraded features that are strategically designed to anticipate and respond to market demands. As such, the HyPET HPP5 is the latest evolution of Husky's 15-year-long run of machines powered by PC-based control. "Recently, we began using multi-core industrial PCs (IPCs) to bundle the new software functionality we added to the HyPET HPP5 while maintaining ever-faster scan times in our control platform," explains Husky Control Software Team Leader Teodor Tarita-Nistor.
As a multi-tasking centralized controller, the industrial PC runs the entire HyPET HPP5 system, including all PLC, motion control, measurement, communication to auxiliary devices and all HMI functions.
This high-end computing power is implemented in the form of Beckhoff C6930 IPCs equipped with Intel Core i7 processors (four cores) and running TwinCAT NC PTP automation software (Figure 3). As a multi-tasking centralized controller, the powerhouse C6930 IPC runs the entire HyPET HPP5 system, including all PLC, motion control, measurement, communication to auxiliary devices and all HMI functions. In order to cement the company's position as a high-end technology provider, Husky takes great care to grow and protect the intellectual property (IP) of its machinery, especially in all areas of software. Using TwinCAT software, Husky has created a wide range of its own software libraries for motion control and hydraulic control.
Also read: Industrial PC: The Power of the PC Processor
"For the HyPET HPP5, we run the PLC tasks on one IPC processor core while the HMI software runs on another core," explains Tarita-Nistor. "This helps Husky decrease scan times while improving overall control quality in our processes. It also has a direct positive impact by establishing real-time control and the repeatability of every axis of motion. This translates into higher end product quality."
By using multi-core processors and Beckhoff's TwinCAT software platform, separate tasks and processing operations can be assigned to each core, spreading out the processing workload and allowing the IPC to run more smoothly and efficiently, as well as reducing latency because the processor no longer has to prioritize tasks. Separate operations can be processed concurrently, improving the overall efficiency of the high-performance system.
While Husky has specified PLC tasks and HMI software to specific cores, the implementation of an IPC with a quad-core processor also takes future developments into account. The additional cores and the associated processing power enable Husky to add additional functionality or features on further cores if needed, a good measure of future-proofing.
Built using a customized 19-in control panel, the Polaris HMI has a look that is unique to the HPP5, ensuring clear differentiation in the marketplace and within Husky's extensive portfolio of machines.
A major change to the HyPET HPP5 system over previous generations can be seen with the Husky Polaris HMI. Built using a customized Beckhoff CP3919 19-in control panel, the HMI has a look that is unique to the HPP5, ensuring clear differentiation in the marketplace and within Husky's extensive portfolio of machines (Figure 4). "During HyPET HPP5 development, Husky determined it was time to move to a larger format HMI screen and the CP3919 fit the bill with the 19-in TFT screen and brilliant 1280 x 1024 resolution," Pirog says. "In addition to the color scheme and logo on the Polaris panel, we worked closely with Beckhoff to customize an injection molding-focused button layout with excellent ergonomics."
The software engineering team at Husky develops the Polaris HMI program from scratch to further strengthen the IP value of the machines. Husky creates this HMI software using C# as the programming language and loads it with customized injection molding features that commercially available HMI software platforms don't have. The Polaris HMI menu screens have been enhanced to simplify startup, and logic has been provided to act on the auxiliary feedback and alarms during operation. The HMI also provides specific instructions to machine operators on how to correct misalignment of molds without requiring the use of a crane, which improves uptime.
More I/O Points
In addition to use of advanced PC-based control, Husky has also been a long-time user of industrial Ethernet technology. Since 2006, the presence of EtherCAT technology has grown steadily on Husky machinery. "With EtherCAT and TwinCAT software working together, there is a wide range of diagnostic tools at Husky's disposal to pinpoint any problems with equipment or the end product. Naturally, this is a major benefit that maximizes uptime," explains Mell.
For the I/O system, Husky has integrated a wide range of EtherCAT solutions from Beckhoff. "Through EtherCAT, Husky has achieved a better unification of all our systems while reducing I/O wiring and troubleshooting efforts," says Tarita-Nistor. Husky has implemented EtherCAT HD terminals, which have a maximum of 16 digital inputs, outputs or a mix of inputs and outputs in a 12-mm-wide terminal housing. "We continuously add new functions to the machine, and this always requires more I/O modules," explains Mell. "However, our machine footprint can't get any bigger. We benefit from HD terminals, so we can fit many more I/O points in the same or smaller space."
In addition to a wide range of IP 20-rated I/O solutions, Husky has also implemented EtherCAT Box modules in IP67 protection for machine-mountable I/O that can withstand harsh plant environments outside of electrical cabinets. Also, Beckhoff FM3312-B110 thermocouple fieldbus modules with EtherCAT interface technology on Husky machines can connect to 12 or 32 thermocouples each. The connecting circuitry for these thermocouples is housed in a splash-proof metal housing surrounding the FM3312-B110 module.
EtherCAT has also enabled Husky to increase implementation of more advanced I/O functionality. The EL3413 three-phase power measurement terminal, for example, is used extensively on HyPET HPP5 systems and can measure voltages up to 690 Vac. There are three power feeds into the HyPET HPP5 system, each of which are measured to read supply voltage and energy consumption of the system.
The EL3413 EtherCAT terminal tracks the energy consumption of the HyPET HPP5 and gives feedback on energy use while providing detailed data for statistical analysis. "Instead of using a separate, stand-alone measurement device, the EL3414 is fully integrated into the standard EtherCAT I/O system," Tarita-Nistor says. "A dedicated energy measurement solution is more limited in terms of connectivity, complicates system architectures and often requires a different, highly specialized software platform."
Husky has been pushing to the highest performance capabilities of the EtherCAT I/O system with a variety of advanced terminals.
Husky has been pushing to the highest performance capabilities of the EtherCAT I/O system in other ways with eXtreme Fast Control (XFC) from Beckhoff (Figure 5). "The EL3702 and EL4732 XFC terminals with oversampling technology help us minimize the delay in control loops, maximize cycle time speeds, and increase the accuracy of our controls," Tarita-Nistor explains. Using these XFC terminals, the signals are oversampled with an adjustable, integer multiple of the bus cycle time. The time base of the terminal can be synchronized precisely with other EtherCAT devices via distributed clocks. The XFC terminals can output a maximum of 100,000 values per channel and per second.
Need for Speed
The HyPET HPP5 project was completed at the end of 2013, and the results are already quite apparent. "Considering all aspects of the system design, the Husky HyPET HPP5 provides productivity and cycle time gains between 3% and 12%, based on the application," Pirog reports.
The cycle time gains can be attributed in part to EtherCAT industrial Ethernet technology, specifically the EL series XFC I/O terminals. The speed of the EtherCAT network eliminates any delay or system latency, increasing overall system speeds. In addition, the HyPET HPP5 system leverages distributed-clock functionality, which enables the system to function with very precise synchronicity, further removing any latency that may have negatively affected cycle times in the past.
One of the top results Husky has generated using EtherCAT is a dramatic new level of processing speed. "We now run our processes at 500 μs, which was not possible with other fieldbuses in our application," adds Tarita-Nistor. "We are even getting performance at 100 μs in a project that's in development at Husky now."
Increased processing speed allows Husky to do more without increasing cycle times.
To put it simply, increased processing speed allows Husky to do more without increasing cycle times (Figure 6). Production can be increased with the same or fewer machines, optimizing the machine footprint and overall plant floor space. The ability to push significantly higher-quality products and more accurate processes through the machine without adding additional burden to the system is a distinct advantage for Husky and the company's customers. An overtaxed system can result in latencies and/or errors, unacceptable when dealing with the throughput volumes and level of product quality that Husky systems must deliver. The PC- and EtherCAT-based control system provides a robust, flexible and scalable platform that can grow and adapt with the company as needs change in the future.
Latest from Embedded Control
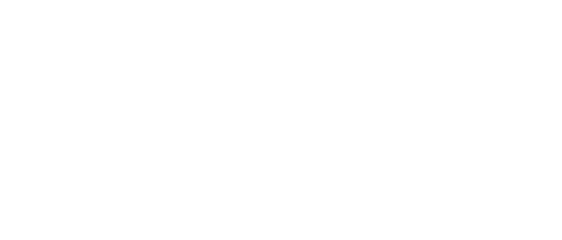
Leaders relevant to this article: