After working as a semiconductor process engineer, Hank Hogan hung up his cleanroom suit and now writes about process control and other technologies from Austin.
Going modular in its machine design was a matter of survival for Matrix Packaging, says Marc Willden, vice president and general manager. The Saukville, Wisconsin-based company designs and makes vertical form-fill-seal machines, the type of systems that produce potato chip bags with a sealed top and bottom and chips inside.
The machines typically weigh out, dispense, and then package product. Matrix Packaging also may provide printers, metal detectors and other peripheral equipment needed to interface with the rest of a food production line. Shortly after the company started more than 20 years ago, it was clear that the machines had to be customized, a challenge for even a large, established enterprise and a near impossibility for a startup.
“You simply don’t have the time or the money to design a brand-new machine from scratch. We tried it. It doesn’t work very well,” Willden says.
In contrast, a modular approach enabled the company to deliver customized solutions in a timely manner without bankrupting the OEM or its customers. Modular machines can save wiring and installation costs, as compared to a completely custom design. They also add flexibility and allow a greater variety of product to be produced in a smaller footprint compared to a one-of-a-kind approach.
However, pulling off a successful modular machine design does demand more planning upfront, and the result can be more costly for the first machine. After that, the savings can pile up. A look at several cases illustrates these points and indicates what’s needed for success.
When the chips were down
Consider Matrix Packaging’s experience. When it ran into problems at the beginning with a custom design, out of necessity the company totally redesigned the packaging machine it had at the time, putting it on a tubular frame that had the space needed to add different assemblies as required. The functionality changed little, but that was the beginning of a modular machine approach that Matrix Packaging follows to this day.
Over the years, the company has developed a number of options, such as assemblies that tuck the sides of a bag in before it’s sealed or load shelves to support very large bags. However, the options cannot be mixed and matched freely.
Also read: Modular Machine Building Succeeds in Sections
“It’s not possible to do physically,” says Mike P. Krummey, senior controls engineer. “So, as a result of that, the drawing standards that I have require maintenance. Any time that we build something new, I have to roll that into the standard.”
Krummey also maintains the software standards. The company uses PackML, which provides operating mode management and communication structures. This and a modular approach to software reduce engineering and integration costs, increase productivity and improve diagnostics.
Figure 1: Matrix Packaging’s latest example of a modular machine is a continuous motion bagger capable of handling up to 200/bags a minute and is designed on a tubular frame so that optional components can be added as needed.
Source: Matrix Packaging
One of the latest examples of this modular machine approach is the company’s Morpheus model (Figure 1), which was unveiled at the Pack Expo International trade show in Chicago in November 2014. The machine can flexibly fill up to 200 bags a minute and features continuous motion requiring the mechanical jaws that seal the bags to be precisely synchronized. The control system and servo motors are supplied by Beckhoff Automation.
Bob Trask, senior system architect at Beckhoff Automation, notes that the PackML standard started with the packaging industry and is now finding applications elsewhere. Another standard that makes it easier to produce highly connected modular machinery is OPC UA, which enables components to provide secure information to higher-level systems. This can include important metadata, or data about the data. For example, if a temperature reading is being produced, it helps to know if the data is supplied in Fahrenheit or Celsius.
As for the software side of modular machine design, object-oriented programming is a possible solution, but Trask cautions that this does mean making some changes in how software is created. Instead of a single block of code that runs from beginning to end, an object-oriented approach subdivides the task into smaller and reusable chunks.
When properly designed, this makes the software easier to maintain or alter. “It’s much less of an issue to add something or change something. The programmer doesn’t have to worry about negatively affecting other objects,” Trask says.
It does require, though, paying greater attention to source and version control, along with implementing systems to ensure both. Suppose that five people instead of one are working on a piece of software. It is important to make sure that they aren’t stepping on one another’s efforts. The use of software with built-in source code control or other means can eliminate wasted effort.
Savings by going modular
Figure 2: Going modular with distributed motion and I/O control saved packaging machine maker OCME more than 50% in cable installation time.
Source: OCME and B&R Industrial Automation
Another example of a modular design approach comes from machine maker OCME, a Parma, Italy-based manufacturer of packaging systems. These may, for example, label, pack and wrap beverage bottles so that they can be shipped (Figure 2). When it was designing a new system, OCME wanted to go modular, with distributed I/O and motion control.
The starting point was a centralized control cabinet and 33 motors. Cramming everything into a cabinet produced heat, which had to be dissipated by cooling modules that added to the cost and complexity of the system. There were more than 650 m of cabling, requiring 33 hours to wire. Installing the motors and other components took 20 additional hours.
In going to a modular design, the OEM sought to decentralize the architecture while reducing the time to wire and install everything. To do this, OCME wanted a machine in which everything could hang off a single network cable. That would make adding something like a conveyor as simple as plugging in a cable.
That goal of modularity placed certain requirements on the components. For instance, Antonio Mosca, OCME electrical department manager, says the company was “looking for a way to combine the motor and the servo drive into a single compact unit.”
When done with its modular design, OCME realized some substantial benefits. These included a 55% reduction in cable lengths and a similarly sized decrease in installation time. As a result, the overall cost of the machine was 10% less.
The combination motor and servo drive that OCME used was supplied by B&R Industrial Automation. They are IP65-rated and so can be machine mounted, with a single cable providing communication and power. They also support IP67 I/O blocks, so that sensors and other input/output elements can connect to the drive instead of having to run back to a controller. Thus, there can be one cable instead of many. Along with an automatic configuration capability, this helps enable modularization, says Derrick Stacey, solutions engineer with B&R.
A modular approach requires a shift in thinking, he adds. Solutions must be broken down into the smallest pieces possible, with the idea being that these will be common to different applications, and they will then be snapped together to produce the total, final solution. This means that the old approach of finishing a mechanical design and then throwing it over to the electrical team will not work. Instead, the interactions between the mechanical and electrical aspects and how everything will function together have to be established beforehand. Similarly, how to break up software into the appropriate modular chunks has to be settled.
This change in thinking extends to the design targets of the machine. It must be laid out in such a way that it allows for every conceivable module, a process that demands considerable upfront investment of engineering resources. It really epitomizes the approach of measuring twice and cutting once. “In many cases, it’s measure 10 times and cut once,” Stacey says.
Quick connection
Figure 3: Automotive exhaust part dimensional gage docking system reduces capital expense and floor space, while increasing flexibility for future products.
Source: RedViking
When making a production line changeover, designing a modular machine to handle the task can prove beneficial. A case in point comes from RedViking. The Plymouth, Michigan-based integrator designs, builds and implements manufacturing and test solutions for the aerospace, off-highway, military and automotive industries. The company uses modular designs extensively for its gages, leak testers and powertrain test systems (Figure 3).
“When applied correctly, customers love it for its lower acquisition cost and reduced floor space,” says Mark Sobkow, vice president of manufacturing systems.
He points to automotive exhaust gages as an example of modularization. RedViking’s customers have to change tooling every model year. Previously, this meant creating an entirely new set of gages on dedicated machines. This was expensive and presented a logistics challenge, since last year’s machine could not be used for this year’s models.
With a modular approach, there is a docking station with fixtures swapped in and out as needed. The docking station has a PLC, light screens and other safety systems, pressure decay or mass flow instrumentation for testing, welding devices, control systems and other assembly devices such as strap guns or nut runners (Figure 4). So, if a line is running 10 models or parts, there could be one machine and 10 tooling fixtures instead of 10 machines.
This reduces purchase cost and conserves floor space. There also is a consistent user interface, simplifying operator training. What’s more, it’s much easier to integrate new products.
Figure 4: Multiple automotive exhaust parts can be tested and repaired by wheeling custom fixtures into stationary docking stations.
Source: RedViking
Care must be taken, though, in the design and placement of the machines for several reasons. One is that, because fixtures are repeatedly attached and removed, connectors can wear out more quickly if the machine is not designed properly. Another reason why precautions must be taken is operator safety and comfort. Multiple tools may be competing for a limited amount of space, complicating ergonomic decisions, points out Sobkow.
System integrator Five Lakes Automation of Novi, Michigan, also uses a modular approach when designing solutions for its automotive customers. Often, this consists of a robot to which tooling is coupled and uncoupled. Wiring, communications, air, water and pneumatics are some of the items being quickly connected and disconnected. In practice, this means that the tooling may sit on a conveyor, be shuttled to a robot, picked up, connected, used, and then returned to the conveyor when no longer needed (Figure 5).
The primary reason for this modular approach is capital savings, says Dave Jones, project manager, FiveLakes. “You may invest an initial amount on the first job, which may be just a small percentage more, 5–10% more. But then your savings on the second model will be upwards of 40–50%,” he says.
Figure 5: Tooling for a robot travels on a conveyor to be automatically added and removed.
Source: FiveLakes Automation
Jones adds that this modular approach is not suitable for all situations. For one thing, there has to be a common architecture. An example is communication, such as some form of industrial Ethernet. This common architecture, though, also applies to such mechanical aspects as motion. If one tool, for instance, moves via hydraulics while a second depends upon servo motors, making a common modular assembly will be challenging.
Another reason not to go modular is the time it takes for a tooling changeover. If a line or machine is running too near capacity, there may not be enough slack to absorb the delay of a switchover, Jones says.
Chopping up a machine
Yet another illustration of modular machine design comes courtesy of Fori Automation of ShelbyTownship, Michigan. Among other things, the company makes automated assembly lines, and these have to be shipped to customer locations. This means the machines are assembled, tested, taken apart, transported and then reassembled on-site, where customers, quite naturally, expect everything to work.
The company decided in late 2014 to go with a modular approach, breaking lines down into 30-to-40-ft sections. Each section was made self-contained through the use of machine-mount I/O blocks. The company also developed standardized boxes for light curtains, safety gates and servos (Figure 6). The creation of modular components hasn’t stopped there.
“We are now generating a standard electrical enclosure for robot electrical interface. We’re going to generate a junction box, and it’s going to incorporate the safety e-stops, gates and circuits,” says Garry Hagar, controls engineering supervisor, Fori.
Figure 6: Interior of light curtain and safety gate boxes that enable modular machine design.
Source: Fori Automation
The driving reason for this switch to a modular philosophy was a desire to save labor costs. The new approach saves in excess of 25% of engineering, estimating and installation time and associated labor, Hagar says. If problems arise, the modular nature of the system makes troubleshooting easier, he adds.
For its modular machines, Fori has used IO-Link-enabled products from Balluff. Shishir Rege, Balluff marketing manager for networking and safety, says that labor cost savings in the 30–50% range are typical when a modular approach is used. Engineering savings can also be substantial, due to the ability to reuse designs and reduce terminations.
The labor cost savings appear immediately, but the benefits of easier controls engineering may only show up after several jobs are done, Rege says. There also can be savings due to the elimination of time spent debugging cable problems, a consequence of having fewer cables and cable types overall.
The result of going modular shows up in productivity gains. “Today, if you’re producing 12 to 13 machines a year, without investing in additional resources and additional buildings, you’ll probably produce a few more machines a year,” Rege says.
Bill Sutton, market development manager for motion control solution provider Kollmorgen, has worked with a variety of machine builders looking to improve modularity of their products. One he points to as a good example is a rotary converting platform from Preco, a Lenexa, Kansas-based provider of materials processing solutions.
The machine can accommodate up to seven converting stations, each of which can be configured for die cut, laser cut, laser heat treatment, laser marking and multiple web assembly operations. Consequently, end users can quickly change over from one product to another.
Modular machines in general offer production flexibility, as demonstrated by the Preco machine. They also can save space, require less training of production personnel and offer a better return on investment on equipment.
Modularity and flexibility do have their drawbacks, however. “Long-run, purpose-designed machines allow for narrow focus on accuracy, speed and size. When a machine is modular and flexible, some capabilities in those areas may be compromised,” Sutton says.
Keeping it clean
A final modular example is from GEA of Texas, which finds modularity often comes in the form of a networked system. There may be variable frequency drives, I/O, safety and operator interfaces, all connected over a network, says Lane Daniels, engineering manager. This approach allows a system to be developed in sections, which are then reused from project to project. Wiring is both reduced and simplified, and there’s the possibility of adding options.
Daniels says that good examples of modular machines can be found in automated car washes. These systems use sensors to monitor the position and measure the size of vehicles, with the position of brushes and spray nozzles controlled to keep them at the right distance. Such systems have to be modular because they are manufactured, disassembled, and then reassembled at a customer site. Modularity cuts the cost of this process and the time it takes.
However, to make modularity work it’s important to select the right physical and network interconnection, Daniels notes. On the network side, the choice should be both common and widely accepted, such as Ethernet/IP. As for the physical connection, the familiarity of those who will be installing and maintaining the system with a particular method is the deciding factor.
Reducing or even eliminating the possibility for error is important, Daniels says. “Using pre-made cable assemblies can greatly reduce mistakes during install or relocating a system,” he explains. “If pre-made cable assemblies are not practical, utilizing a logical connection system is imperative.”
Another benefit of a modular-machine design is that it allows optional components to be added in the field, notes Joe Landgraf, product engineer for motion and drives, Omron Automation and Safety.
Lessons learned
As these cases show, modular machines provide significant benefits. However, clearly a one-time-only machine is not a good choice for this approach, says Matrix Packaging’s Willden.
What’s more, modularity does impact design methodology. For instance, Matrix Packaging is in the process of launching a new platform. In designing such a platform, it’s important to step back from the immediate problem in order to anticipate what might someday be a part of the machine.
Describing this process, Willden says one of the company’s engineers “had to think through every possible option that would go on this machine, and, even though he didn’t design all those options, he kind of roughed them out in his own mind so that he knew that the fundamental design of the base machine would be able to accommodate that.”
Such anticipation of what might be a future requirement extends to more than the hardware. The software also should contain code that provides for expansion and even platform changes. The latter has become easier due to the development and use of the open PLC programming environment CODESYS, says Matrix Packaging’s Krummey.
Five Lakes’ Jones agrees that a modular approach requires more upfront work and planning. These include considering communication protocols, power and fluids, with standardization making modularization easier. The planning must also consider what may come, even if the particulars are unknown.
For instance, suppose that a robot is being used to move material from one point to another. One set of tooling may allow one type material to be moved, while a different set of tooling is needed for another. But knowing which tooling is needed is not enough, Jones says.
“If your second product is much heavier, then you run the risk of overloading the payload or the robot,” explains Jones. “So you have to have an idea of what’s coming in to that station.”
Fori’s Hagar seconds the observation that any new component cannot simply be thrown together. As part of the process, for example, a junction box that incorporates all possible needed components must be generated.
However, modular systems are easily reconfigured as requirements change. “If I have to add something new to a system that we didn’t have before, modular design allows for easier integration,” Hagar says.
Any drawbacks to modularization are outweighed by the benefits, though. Economics and the development of standards help to ensure that, says RedViking’s Sobkow. “We see more and more of a demand for modular machines due to decreasing budgets and limited floor space,” he explains. “We’re also anticipating a higher level of standardization so that manufacturers can purchase interchangeable fixtures from multiple vendors.”
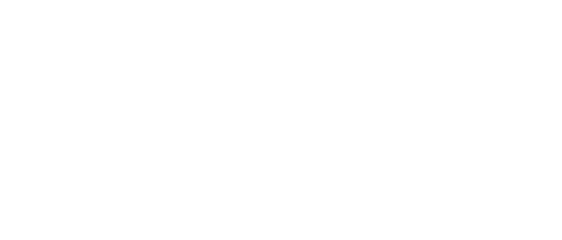
Leaders relevant to this article: