Programmable Safety Cuts Costs and Adds Capabilities
After working as a semiconductor process engineer, Hank Hogan hung up his cleanroom suit and now writes about process control and other technologies from Austin.
For machine builders, there's safety in numbers—specifically, the numbers represented by falling costs, increasing port count and greater connectivity options of programmable safety solutions. Uncomplicated setups may still best by served by traditional, nonprogrammable and relatively simple safety relays, but ongoing improvements and greater flexibility have made programmable safety cost-effective for a wider array of situations.
For an example of the impact of programmable safety advances, consider a system from Intelligrated, a Mason, Ohio-based provider of intelligent automated material handling solutions. Intelligrated built a mixed-load palletizing cell with specialized end-of-arm tooling that could handle multiple case sizes in a single pick, integrating advanced software, controls and vision technology to do so (Figure 1).
A mixed-load palletizer with specialized end-of-arm tooling can handle multiple case sizes in a single pick by integrating advanced software, controls and a programmable safety controller.
(Source: Intelligrated and Rockwell Automation)
"Prior to programmable safety, achieving the functional and operational requirements of this kind of solution was costly and problematic," says Matt Wicks, vice president of product development for manufacturing systems at Intelligrated.
Flexible and Safe Movement
"Using programmable safety allows for more complex safety functionality to be implemented cost effectively," says Intelligrated's Wicks. "An additional benefit is that this allows for quicker, less-costly changes to the safety system when there are changes in project scope like layout reconfiguration."
For this particular system, Intelligrated used Rockwell Automation's Allen-Bradley Compact GuardLogix programmable automation controllers. To understand why the flexibility added by programmable safety is important, it helps to realize that an automated palletizing system may consist of multiple robot cells, each with its own point of entry, as well as a discharge transfer system of the finished pallet of material. The final product may go through a stack-and-wrap solution that readies the pallet for shipment.
Each piece of equipment has a potential safety-level interaction with others in the system. Programmable safety can define this interaction, eliminating the time spent on complex safety circuit wiring. Consequently, equipment providers and integrators can make functional changes as needed while minimizing any implementation risk.
That flexibility can be important to end users, Wicks says. "It also reduces risk for our end customers as they may not recognize operational impacts until the system has been implemented," he says.
Intelligrated has used Rockwell Automation programmable safety solutions for years. But for simple setups such technology may be more costly than an approach based upon more traditional controllers and safety relays. Generally, programmable safety makes sense in situations where there are more interactions with other types of equipment and if there are more specialized or unique cases that must be handled, Wicks says. All applications with a PLC or similarly capable controller will need some sort of safety solution, says Tim Roback, marketing manager for safety systems at Rockwell Automation. He adds that an integrated solution that combines control and safety into one programmable product enables optimization because there is information associated with a safety event. Data such as how often a fault occurs or an e-stop activates can be important in devising ways to avoid such halts to production. This data also can help to minimize downtime by pinpointing what caused a fault and why.
Also Read: Making Sense of Safety Components
hen combined with the right choices early in the design cycle, such programmability can help to improve both safety and productivity. For example, a machine can be zoned into different sections, with staging areas between the zones. As a result, a problem in one area and the opening up of an interlocked door may not mean that the entire manufacturing process has to stop.
"You can continue to produce product in one zone while you clear a jam in another," Roback says. A somewhat similar benefit is that with programmable safety a machine can come to a controlled stop, he adds. For instance, a bottle-filling machine may halt after the current batch of bottles are completely filled, which makes starting up after fixing a fault faster and smoother. Such cases illustrate that programmable safety can make restarting a machine easier and quicker than is possible with simpler and less flexible technology.
Safety and Savings
Another example of the use of and benefits from programmable safety comes from system integrator and tooling manufacturer Five Lakes Automation of Novi, Michigan. Five Lakes Automation works with Tier 1 automotive suppliers, with a focus on welding, riveting or other joining applications, says Project Manager David Jones.
In one case, there was an operator station to which a robot was being added in an assembly line for a major automotive manufacturer. The robot had seven-axis movement, with the entire robot base traveling toward and away from the operator. The use of a safety PLC improved the flexibility of the solution and dropped its cost. The alternative was a large complete panel with an array of safety relays that would have taken up a considerable amount of space and consumed quite a bit of design and installation time.
In contrast, the programmable solution that was implemented involved a single small junction box and much less design time. What's more, adding a safety function at some point later would be as simple as wiring a device to available inputs on the safety controller. Accomplishing the same upgrade with a safety relay-based approach would not be as straightforward.
"We'd have to find panel space and bring wiring in," explains Jones. "It takes something that we could probably accomplish in a couple days using programmable safety to a couple weeks."
Simple setups and machines do not generally benefit enough to offset the extra cost of a safety PLC, Jones notes. Examples might be a single rivet tool or another machine dedicated to a single task. Typically, these tools have very little in the way of safety requirements. Also, they often are single enclosure tools located within 10 ft of any safety systems.
However, even for some relatively simple machines, savings in design time and reductions in startup debugging may make programmable safety cost-effective, says Jones. That's one reason why Five Lakes Automation steers customers to safety PLCs from Rockwell Automation and Pilz. "We recommend these options to our customers over hardwired applications due to their flexibility in design changes and the reduced time in startup," Jones says.
One advantage of a programmable safety solution is the more-extensive diagnostics it offers, says Dino Mariuz, engineering manager at Pilz. The additional information thus produced will add value and may overcome any price added, even for simple setups.
A growing trend is to make programmable safety systems compatible with Ethernet-based or other network communication protocols. One result will be an expansion into wireless platforms, explains Mariuz.
Wilson Transformer uses a programmable safety controller to manage control components and safety systems, an approach that allows for flexibility with multiple network communication platforms.
(Source: Pilz Automation)
With regard to advice about programmable safety, Mariuz offers two items. One is that being able to program a PLC doesn't necessarily translate into being knowledgeable about safety. Thus, accepted techniques and safety standards must be followed. The second is that the safety of a solution, programmable or not, must be verified by control engineers or end users with the appropriate qualifications (Figure 2).
"Once the system is installed, they need to validate the safety system to ensure that the system meets the safety specification," Mariuz says.
Density, Connectivity and Lifecycle
Programmable safety offers benefits that aren't possible otherwise, says Matt Dodds, safety product marketing manager at Omron Automation & Safety. For instance, programmable safety can enable a scalable solution, which means that customers can potentially master one style of programming and hardware that moves up with them from stand-alone machines to entire production lines.
There also can be a productivity payoff. With programmable safety, there can be an emergency stop and a separate protective, or Cat. 2, stop. The latter brings things to a halt in a controlled fashion and holds everything in place under power. Doing so leaves actuators energized, preserving position and other information needed for a restart.
Today a compact safety controller can replace three 6-ft panels full of safety relays and associated wiring, reducing space requirements twenty-fold, says Dodds. An added advantage is that reliability can be increased because hardwired relays that wear out are eliminated. While there will always be a need for safety relays and associated equipment, ongoing cost reductions have dropped the point in application complexity at which programmable safety makes sense.
"Once you move into systems requiring more than three sets of inputs, then compact safety controllers start to become cost-effective, and they give you the added convenience of being able to be monitored over networks by a PLC, HMI or other similar device," Dodds says.
The trend is toward more connectivity and more compact programmable safety devices, says Martin Lalonde, applications engineer at Wieland Electric. The second of these shows up in increased density, such as a greater number of ports and with more of these configurable. For instance, some recent programmable safety products have 24 I/O ports in their base configuration while their predecessors had none. As for connectivity, that typically involves the addition of Ethernet, a capability that brings various benefits.
"That Ethernet port can be used for remote programming, so if somebody is doing remote support maintenance through a VPN router, for example, that's something that would be fantastic to have," Lalonde says. "Nobody wants to have to fly over to fix a non-issue or do a simple change to a program that could be done remotely. So you can save a lot of time and effort and money."
Perhaps the biggest reason why safety systems of any type are defeated is that those designing the safeguards don't take into account how machines will be used. Maintenance personnel, for instance, may need to bypass some safety interlocks while working on a machine. Programmable safety can help to minimize any hazard by allowing for the use of a maintenance mode. Another specialized mode might involve starting a machine, particularly if during such times greater access is needed than is the case during full-blown production.
"You have to look at safety as a lifecycle approach," says Rockwell Automation's Roback. That lifecycle includes the design of the machine, its various modes of use on the factory floor, any upgrades or changes that it may undergo and finally its disposal. Because of its flexibility, programmable safety offers a way potentially to better meet these diverse requirements.
Finally, whether or not newer technology or the more traditional approach should be used will depend upon the particulars of a situation. Machine builders need to evaluate their equipment and applications and then do the math to determine the ROI that comes from leveraging the greater capabilities offered by programmable safety. In those return-on-investment calculations, it's vital that everything be considered, including any hidden costs, as well as unrecognized benefits. Doing a complete evaluation helps when comparing programmable to traditional safety solutions.
"Do your homework and understand the pros and cons to implementing programmable safety," advises Intelligrated's Wicks.
Latest from Integrated Control & Safety
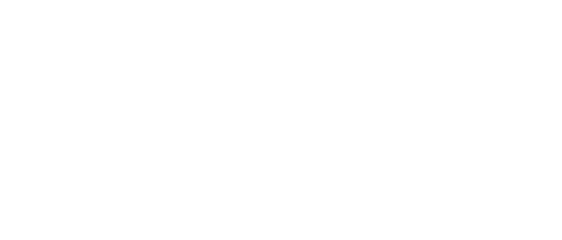
Leaders relevant to this article: