After working as a semiconductor process engineer, Hank Hogan hung up his cleanroom suit and now writes about process control and other technologies from Austin.
Machine mount — the placing of everything from I/O to PCs directly on factory floor equipment instead of in a cabinet — is increasingly being used. The benefits are less cabinet space and wiring, as well as reduced commissioning time and expense. Other advantages are easier maintenance, greater modularity and more flexibility.
However, compared to cabinet-enclosed equivalents, machine-mount components are more expensive because they must be rugged enough to survive and work on the plant floor. Consequently, machine mount may not make sense for simple machines with few I/O points or in cases where cabinet space cannot be eliminated and is not at a premium.
Spend to Save
For an example where machine mount saves even though the components cost more, consider the experience of Durrer Spezialmaschinen. Based in Kussnacht am Rigi, Switzerland, Durrer makes a variety of specialized machines. The company’s REGA 3 counts different paper types and cuts step indexes into books, catalogs and other printed material. This involves complex movement along 21 axes in a system measuring 2.8 by 1.8 by 2.0 m (9.2 by 5.9 by 6.6 ft).
Figure 1: Machine-mount IP67 modules and motion control help make possible precise counting of pages in each section of printed materials, part of a process that adds index tabs.
(Source: Beckhoff Automation)
Patrick Suter, Durrer’s head of development, says the I/O is handled by machine-mount modules that are IP67-rated, a standard protection category for direct installation on a machine (Figure 1). Being dust-tight and water-immersion-resistant, these cost more than functionally similar components in a cabinet but are worth it.
"Because most I/O signals are recorded in the machine by the IP67 modules, we have just a few signals in the electrical cabinet," says Suter. "So, then we could reduce the I/O space inside of the electrical cabinet by approximately 80%. On the wiring, we saved approximately 50% of the installation time."
One of the reasons for the wiring decrease is that now only two wires are used, one for power and another for an EtherCAT connection. In the past, there would have been several multi-wired cables to configure with plugs, Suter says.
The machine-mount I/O modules are supplied by Beckhoff Automation, all with an EPxxxx (industrial housing) part number. They consist of a total of 56 digital inputs, 24 digital outputs and 16 safety inputs, in an array of 16- or 8- channel digital input or output boxes.
Machine-mount use is expanding because the environments in which machine-mount devices can function are growing, according to Kurt Wadowick, I/O and safety specialist at Beckhoff Automation. For example, devices can now withstand pressure washdown, common in food, beverage and pharmaceutical processing. They also can work over an extended operating temperature range of -25 to +60 oC.
"The robust nature of these machine-mount solutions makes them well-suited for many specific application types, and they remove the need for a control enclosure," says Wadowick.
He adds that these I/O modules are accessible without even having to touch a cabinet door. This allows operators to quickly and easily determine the status of the I/O and, if need be, replace faulty sensors. It also streamlines the machine’s cabling, improving safety, appearance and cleanliness, says Wadowick.
Less Cabinet Space and Wiring
Figure 2: A centralized baggage handling system at Halifax Stanfield International Airport in Nova Scotia saved money and cut commissioning time using machine mount I/O. (Source: Cofely Services)
Another example of machine mount savings can be found in baggage handling (Figure 2). In solving this material-handling problem at Halifax Stanfield International Airport in Nova Scotia, Canada, Cofely Services, a worldwide technical services company, went with machine-mount IP67-rated modules and M12 connectors (Figure 3 on next page). The choice paid off in various ways.
"We estimated that for this project we decreased probably 30% of electrical cables and electrician time," says Yan Le Meur, automation technology expert with Cofely Services.
Other cost savings were in panels, with more than two-thirds eliminated. A final savings came in commissioning. Earlier projects were plagued with short circuits, inverted polarities and other electrical problems. In contrast, none of these appeared during commissioning of the Halifax project, Le Meur reports.
Figure 3: Machine-mounted I/O modules are equipped with M12 connectors in Halifax airport baggage handling system.
Cofely Services
The ease of commissioning and troubleshooting and the reduction in wiring is no surprise to Derrick Stacey, a solutions engineer with B&R Automation. The company supplied machine-mount modules to the Halifax baggage handling system.
Machine-mount modules are typically daisy-chained together, which means only one wire may go back to the controller. Besides a wiring savings of two-thirds or more, that one wire carries information that can be exploited for troubleshooting.
"From my HMI — I don’t even have to walk out there — I can see where I’m getting diagnostic data," says Stacey. "A lack of data means there’s no communication and that gives you a start."
B&R has machine-mount counterparts to almost all of its product line, with its drives and other high-powered equipment IP65-rated. This means they are dust-tight and resistant to dripping water.
As for why machine-mount is now possible for a wider array of components, one factor has been a decrease in chip power consumption and the consequent elimination of fans. Networking advances have also helped.
Realizing the full benefits of machine-mount components takes planning, Stacey says. For example, a machine-mount I/O module takes some space and should be placed where it won’t require tearing a machine apart to replace. Also, it must be mounted where it won’t be exposed to damage from a forklift running by.
More Modularity
Figure 4: On an overhead conveyor system, modularity and machine mount of I/O and drives cuts reconfiguration time significantly.
(Source: Rockwell Automation)
An example of another machine-mount benefit can be seen in an overhead conveyor system from OCS IntelliTrak of Fairfield, Ohio. These are used by car and truck makers as a material handling system, and IntelliTrak has found that use of machine-mount I/O and drives means that changes are easier to implement, a distinct advantage (Figure 4).
"Within the automotive industry, changes to process, work content and system requirements occur right up until full production starts," says IntelliTrak President Tom Robertson. "The flexibility to move drive zones, cabling and hardware allows us to provide the customers exactly what they need in a timely manner. The on-machine design allows our main enclosure to be small and easy to manage."
He adds that the flexibility, modularity and scalability make this approach worthwhile. The company has been able to standardize on a small control cabinet, configuring the remote devices easily. The additional hardware cost is more than justified through implementation savings, reduced downtime and ease of troubleshooting, says Robertson.
Rockwell Automation supplied the machine-mount modules used by IntelliTrak. Rockwell’s machine-mount offerings span multiple business groups, says Todd Bissell, commercial programs manager. One advantage of mounting I/O, computers and other components directly on the machine is that the diagnostics, such as LEDs, help those who are running the factory floor equipment.
"It’s easy to see where things might be going wrong and need replacement," Bissell says. "With on-machine, you can actually have an untrained person, someone who doesn’t know about ladder logic, be able to walk around the machine and say ‘Oh, red LED.’"
Figure 4: Machine-mount power supplies provide power where needed.
(Source: Balluff)
Although machine mount has been around for a decade or more, there are some interesting recent trends, says Will Healy III, strategic marketing manager at Balluff. Chief among these are power supplies, he says (Figure 5).
"There can be a dramatic benefit in reducing the size or even eliminating cabinets on equipment," says Healy. "This in turn, creates less panel drawings and faster panel builds; plus, it provides flexibility to add power wherever you need it and quickly connect it to automation equipment."
Also Read: Switch to Machine-Mount I/O?
Flexibility
Machine-mount technology has expanded to include PCs. Out-of-the-cabinet placement is possible because modern PCs are thin, fanless and have touchscreens, making the entire assembly attachable via an industry-standard VESA mount that’s rugged enough for the factory floor. VESA is the Video Electronics Standards Association.
"All of the cabling is extruded out of the bottom of the PC through grommetting, so it even has an IP65 connection," says Eric Reichert, product marketing specialist for Industrial PCs and HMI at Phoenix Contact.
With this configuration, savings arise because the machine-mount PC can be put on the line where needed without requiring an enclosure. That can more than offset the fact that a ruggedized PC is more expensive, according to Reichert.
To see another benefit, look at the use of a Phoenix Contact machine-mount PC in manufacturing. The Apex Tool Group of Sparks, Maryland, makes high-end, intelligent wrenches that can tighten bolts precisely and aren’t constrained by ergonomics. These tools are used in automobile, aerospace and other industries.
A recurring challenge for car and truck makers is the launch of the next model year, which involves pre-production runs. Hence, there may be a need to temporarily run a new recipe and then change back, which can be an expensive undertaking. There also is need to capture vital data as settings are changed.
Figure 6: Machine mounting a PC and intelligent wrenches cut the cost of pre-production runs in car and truck manufacturing.
(Source: Apex Tool Group)
Apex’s solution is a mobile pilot cart, says Dominick DeBello, chief engineer of electronics and software. Equipped with three to five intelligent wrenches, the cart has a machine-mount PC on it that allows pre-production to be run without having to install anything on the line itself (Figure 6). The PC helps capture adjustments in torque and other information.
This flexibility is only possible because the PC is IP65-rated and on the factory floor. In this situation, machine mounting brings flexibility and yields savings. "I reduced the amount of cabling, the amount of mounting, and a few other things," DeBello says.
Taking Care and Making Sense
The environment that a machine-mount solution goes into is critically important, says Mark Schuerman, business development manager for global automotive projects at Molex. The company provides interconnection solutions, including some machine-mount IP67-rated I/O, Ethernet switches and industrial communication interfaces.
In a production environment, there can be chemicals, oils, or exposure to high pressure jets during washdown. There can also be weld slag or extreme temperatures. "Care must be taken to ensure the components selected can withstand the environment in which they will be used," Schuerman says.
The payoff of being careful can worthwhile, though. Molex worked with an automotive paint system supplier, revamping products by adding plug-and-play wiring and machine-mount technology. Equipment construction lead time fell from 12 to four weeks and installation time dropped from seven to two days, Schuerman says.
However, machine mount isn’t always the right solution. For example, it may not make sense when a large, and largely empty, cabinet is a given, says Rockwell’s Bissell. This could be due to some necessary component that cannot be moved out of the cabinet. In that case, machine mount may not offer any savings, particularly with a low I/O count.
Expanding on this theme, Balluff’s Healy adds that special requirements, like the ability to survive washdown or operate in an explosion-proof manner, can mean machine mount is not feasible. These requirements may reduce the types of products available for machine mounting and increase the likelihood that an enclosure or cabinet will be needed anyway. In such circumstances, the total lower overall cost possible with machine mount in other settings may vanish.
Durrer’s Suter agrees that machine mount is not always the best solution. Because the components are more expensive, there must be offsetting savings, either in wiring, cabinet space, commissioning or elsewhere. Suter says that is easier to achieve when cabinets are more than a few feet away or when a sensor-laden or function-rich part of a machine has to move.
In summing up the circumstances under which machine mount does not make sense, Suter says it’s when the "electrical cabinet is near or in the machine or fewer signals are mounted on a moveable part."
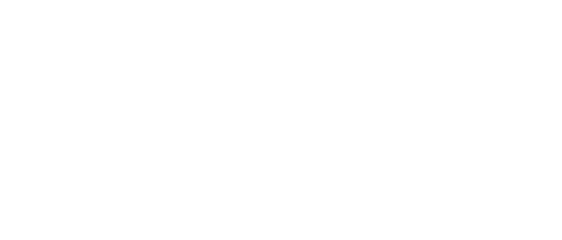
Leaders relevant to this article: