A Control Design reader asks: I’m trying to reduce field wiring on the packaging lines that we build. Typically, I might have a dozen servo drives on the equipment. Instead of running servo power and feedback cables, along with wiring to solenoids and sensors, we’re looking at using distributed methods.
Any recommendations on I/O methods for the major motion and sensing devices on the machines?
ANSWERS
Everything on one network
Today there exist more options for distributed vs. centralized motion than ever, and the good news is that they can often be mixed and matched on the same network, even motors, actuators and drives from third-party suppliers that support a given network architecture.
Integrated servo motor/drives have been around several years now, with the drive electronics mounted on the motors. This frees up cabinet space and quite possibly will allow you to run one hybrid motor cable from the cabinet out to the motor/drives, typically in a daisy chain. These motor/drives can also provide onboard I/O options, which can be used in combination with both cabinet-mounted and machine-mounted IP67 I/O modules, all on the same industrial Ethernet network.
A newer distributed option is the machine-mounted drive. This allows you to distribute higher-powered motion out onto the machine because the separate drive doesn't face the same heat dissipation issues as a motor-mounted drive. It also allows you to use different motor types, such as linear or torque motors, third-party motors or stainless-steel motors.
For automated changeovers, there are now stepper drives in the IP67 remotely mounted I/O form factor. This also is great for retrofits on existing lines.
Likewise, distributed motor/drives are great for headless add-ons, such as leaflet inserters or smart belts, controlled by adding or activating a software module in the main automation controller.
Safe motion is also a huge opportunity for packaging machinery builders and line integrators to go into a safe mode instead of stopping the line. This isn't safe torque off, it's safe torque, speed, position, direction, robotics and more.
Integrated motor/drives are great for rotary machines, too, where power and communications go through a slip ring to turret-mounted motor/drives. Other options include micro drives mounted in the turret, both stepper and servo. A common power supply on the stationary portion of the machine saves space in the turret and allows simpler dc power distribution through the slip ring.
Among the latest developments are servo drives the size of a single-axis drive that can run two and now up to three servo motors, thanks to increasingly integrated electronics. Better yet, drives of this type may be designed to power single-cable motors, presenting another way to reduce both cabinet size and cable runs.
You should also be able to mix any and all of these form factors with conventional single and multi-axis drive systems. Some servo drives can also be used as frequency drives if you have some axes that can benefit from the lower cost of induction motors, with or without encoders.
Today's controllers and networks allow you to run everything on one processor and one network. So it's no longer necessary to buy multiple CPUs to run 12, 15, 20 or more drives and no longer necessary to have separate motion and device buses, even for high-axis-count systems.
— John Kowal, director, business development, B&R Industrial Automation, www.br-automation.com
Distributed by distributor
For the case of distributed I/O and servo systems, you would best look into manufacturers that have an integrated motor drive system. Since you have not specified the type of machine, there are many options—integrated motor and drive VFD for conveyors, integrated motor servo systems even stretching up to 10 hp. Now, if your machine design requires washdown, then I suggest redesigning the machine for a balcony or bathtub design so you don't have to use washdown on stainless steel motors.
There are a number of manufacturers offering machine-mounted servo drives and inverters now. Often these will have extensions/connection points for local I/O at the machine-mounted device for local sensors. I have even used noncontact wireless I/O sensor systems and just run 24 V along the machine. As long as the I/O is not time- or safety-critical, then does it have to have wires? There are many ways to approach the system design and accomplish your goal. I would recommend that you contact a distributor and make sure the communications system has one of these five fieldbuses—Profibus, Profinet, EtherCAT, EtherNet/IP, SERCOS III.
— David Arens, senior automation instructor, Bosch Rexroth Drives and Controls, www.boschrexroth.com
Isn’t it obvious?
You mentioned one of the most obvious ways to reduce wiring: distribute the I/O devices and servo drives throughout the system to reduce the number of discrete conductors and reduce the length and number of power and feedback cables. A secondary benefit of distributing devices is control-cabinet size-and-cost reduction.
Two additional ways to reduce wiring include using a modern network like EtherCAT to replace discrete conductors with inexpensive CAT5/6 cable and choosing a servo solution that supports a single cable between servo drive and motor containing both motor power and feedback.
Used together, these can reduce system wiring by 80% or more. The more axes and sensors you have, the greater the savings will be. Many solutions support IP54 or higher-rated devices so it is easier than ever to distribute devices, regardless of the operating environment. Some distributed drives also have onboard I/O that can help reduce I/O devices. Distributed technologies that combine both servo power and EtherCAT into a single hybrid cable maximize savings and may result in only one cable going back to the control cabinet. EtherCAT makes it easy to add remote I/O devices and supports network updates of 0.25 milliseconds (4 KHz) or lower to meet requirements of time-demanding applications. Servo drive and I/O device configuration can be changed on the fly and real-time device operating and status information are continuously available to the machine controller.
— Carroll Wontrop, senior system engineer, Kollmorgen, www.kollmorgen.com
Think IP67
You have a few options when transitioning to a distributed control network. The first option is to move the equipment from a single large cabinet to multiple smaller cabinets distributed along the conveyor system. Each of these cabinets can contain power distribution, servo and I/O for that section of conveyor. These cabinets can then be networked back to the PLC, reducing a large percentage of the parallel wiring.
The second option is to make the leap to a fully IP67 installation using servos and I/O with direct network connections back to the PLC. With this option, you need to look past the initial sticker shock on product cost and evaluate the time savings of not having to build the individual control boxes. In the end, a combination of both options may work out best. A good starting point would be to evaluate the cable savings by distributing IP67 I/O modules on the conveyor to pick up your solenoids and sensors.
— Jason Haldeman, lead product marketing specialist—I/O & light, Phoenix Contact USA, www.phoenixcontact.com
Link to it
Distributed I/O for sensing and valve connections makes a lot more sense than bringing all the individual wires to the control cabinet. As you already know, the wiring that you currently have requires tremendous amounts of labor efforts, and it is more prone to human errors.
Figure 1.
Distributed I/O naturally reduces complexity and wiring. Machine-mountable distributed I/O can further reduce complexity, as you can use standard M12 or M8 connections for all the I/O instead of terminating it. IO-Link-enabled machine-mount distributed I/O certainly adds even more value, as it simplifies connections and adds diagnostic capabilities for sensors and smart sensors, as well as I/O.
Furthermore, IO-Link adds flexibility as you build the I/O architectures. We generally refer to an IO-Link-based architecture as “distributed modular I/O.” IO-Link is the first sensor actuator communication standard as described in IEC 61131-9. The communication with IO-Link is over three wires and utilizes a standard M12 prox cable; no special cables are required. An open IO-Link port on the field device can host as many as 30 I/O points or any smart sensor from over 115 IO-Link vendors from across the world. On the three-wire communication that IO-Link offers, you can have your process data, parameter data and even events data on the same line.
There are many more features and functions with IO-Link that a standard approach for a centralized wiring concept cannot offer—automatic parameterization, savings on labor, added diagnostics that can reduce downtime and most importantly reduction in human errors, so that as a machine builder you can get to market faster.
The picture in Figure 1 shows a quick view of the architectural design possibility with a machine-mount IO-Link modular design.
— Shishir Rege, marketing manager, industrial networking, Balluff, www.balluff.com
All in one
The good news is that there is a wide range of servo and distributed I/O innovations available today that are designed precisely to tackle these kinds of field wiring and installation challenges. When simplifying difficult applications in the field, we increasingly point our customers to time- and space-saving one-cable solutions. The availability and reach of one-cable technology continues to expand, giving manufacturers the ability to instantly reduce cabling cost and effort by 50%. For example, options include:
• one-cable motors combining power and feedback into a standard motor cable (One Cable Technology servo motors)
• one-cable automation solutions combining industrial Ethernet communication and power in a single four-wire standard Ethernet cable (EtherCAT P)
• single-cable display solutions—DVI signal, USB 2.0 signal and 24 V power supply transferred through one cable (CP-Link 4).
Other options available to machine builders and system integrators include I/O terminals with special integrated functionality. For instance, DIN-rail-mounted servo drive terminals have been available for years that pack motion control functionality into an I/O housing as compact as 12 mm wide. This permits the drive to be simply added to the existing I/O rack, right alongside all the other I/O that connects to the rest of the field devices such as sensors and actuators. This dramatically simplifies installation in difficult, space-constrained application areas. Even better, there are One Cable Technology-compatible versions of these I/O terminals, too, providing even more efficiencies and savings via one-cable control solutions.
— Matt Prellwitz, drive technology application specialist, Beckhoff Automation, www.beckhoff.com
For safety’s sake
Traditional servo technology used separate cables for feedback, power and brake control, so each servo needed two or three cables for motor control. With the latest servo and motor feedback technology, users can combine the power, feedback and brake signals into a single cable, thereby reducing wiring cable requirements by up to 60%. This not only helps save on installation time and costs, but also reduces the chances of wiring mistakes and the resulting troubleshooting time.
In addition, modern servo drives leverage network-based safety implementation. Compared to a traditional, hardwired, servo safety system, the network approach helps to reduce overall system wiring, save time during installation and remove potential points of failure, which can result in less downtime and troubleshooting. Modern integrated safety systems allow users to change safety zoning and configurations without needing to physically rewire devices.
— Jim Grosskreuz, global product manager, Rockwell Automation, www.rockwellautomation.com
In enclosure or on machine
A distributed I/O system can be either an IP20 or IP67 system. IP20 I/O requires mounting inside an enclosure, while IP67 is mounted directly on the machine. Typically, servo controllers are located in the PLC rack and cabled to the servo motors located along the packaging lines. There are numerous servo manufacturers today that have developed Ethernet-based servo systems with embedded servo control, such as CIP Motion, where an Ethernet connection is all that is required for both IP20- and IP67-based resolvers and servo signals.
Power to the servo motors are also available in distributed IP65/67 power cabling or the traditional power feed from an enclosure. Today, many packaging line manufacturers are utilizing IP67 Ethernet-based digital and analog on-machine I/O modules to take advantage of the Ethernet network and reduce field wiring.
In an IP67-based on-machine distributed I/O system, reducing field wiring decreases the typical startup time of a new system installation by removing the field terminations and replacing them with IP67 connections. These on-machine control systems enable you to move into production quickly, which in turn negates the initial higher cost of distributed I/O within the on-machine IP67 system. This is accomplished by simply removing the field wiring terminations, which are typically where most problems occur due to incorrect wiring, improper cable jacket stripping and loose screw terminations from incorrect torque.
— Ray DiVirgilio, machine builder industry manager (North America), Belden, www.belden.com
Next-generation solution
Today’s packaging machines require flexible and decentralized solutions to compete and meet the needs of their customers for the future. Many of the major OEM packaging machine builders come to us with the same question: With the cost of engineering, labor and materials ever increasing, how can you help us to improve and simplify our machine design, layout and fabrication?
With the need for machines to be reconfigured on the fly in order to accommodate additional axes, multiple package sizes or products, the need for motion and discrete sensing devices distributed throughout the machine is on the rise.
We have examined the needs for these next-generation machines and designed a flexible motion control solution with distributed I/O to reduce the cabinet size by up to 90% and reduce wiring needs, thus saving costly floor space by reducing and, in some cases, even eliminating the electrical enclosure. Such solutions encompass the entire machine, utilizing a single cable that is daisy-chained from drive to drive or I/O block. This eliminates the need to run every device back to the control cabinet, substantially reducing the wiring, complexity and cost.
The solution utilizes a single cable that transmits the main power for operating servo or induction motors, as well as EtherNet-based fieldbus communications for controlling the motion and I/O devices. This solution is extremely versatile as it utilizes a number of today’s most popular protocols including SERCOS, EthernetIP, EtherCAT and ProfiNet with others on the way.
Instead of the machine design described by your reader with the servo controller, VFD and PLC I/O installed in the control cabinet and running costly cables out to each device, the solution mounts the servo controller directly onto the motor. Now, only a single cable is needed to be daisy-chained from drive to drive.
Each motor is equipped with four configurable input/output points that can be used at the OEM’s discretion but also allow special functionality like high-speed capture of product or motor position that can be very costly to implement in many traditional PLC designs. Additionally, EtherNet breakout ports are available that allow fieldbus I/O or devices to be connected to the network.
Cabinetless power supply modules eliminate the need for putting high power contactors, inductors, filters and power supply in the control cabinet. Instead, IP65 modules are mounted directly on the machine base.
On bigger machines, this can eliminate the need for air conditioning of the main control panel, as well as reduce its size. These units are fully line-regenerative, which means that the energy used to stop the load/motion is put back into the power line instead of being turned into heat, thereby eliminating the need for resistor banks and providing a greener, more energy-efficient solution that fits well with many of today’s corporate mandates.
This cabinetless design also lends itself to some of today’s modular designs where the machine designer has divided the machine into function sections that perform a specific task. These modules can then be mixed and matched to meet the specific needs of the end user on the production floor. This also allows a section to be pulled out and replaced if the process changes in the future without the need to rebuild the entire machine.
Another point to consider when evaluating fieldbuses are the emerging requirements to support machine safety. U.S. machine builders are no longer able to sell a machine into the European market without this implemented. Many of the large corporate end users here in the United States are upgrading the internal standards to include machine safety on new machine installations.
Only a few of today’s fieldbuses allow support for safety functions to be intermingled on the same bus network as the standard I/O, thereby requiring two networks on the same machine. A good example of this is SERCOS III that has support for safety functions up to SIL3, according to IEC 61508 via CIP Safety for SERCOS. This allows for safe motion, guard doors and light curtains to be on a signal network that operates the indicator lights, pushbuttons and sensors throughout the machine.
— Jeff Bock, senior application engineer, Bosch Rexroth, www.boschrexroth.com
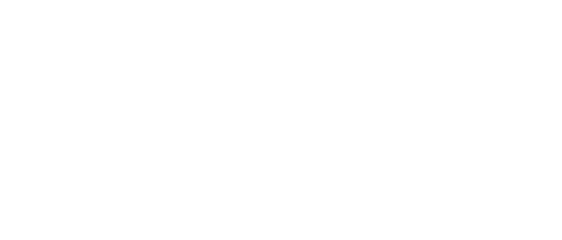
Leaders relevant to this article: