The benefits of using an industrial computer (IPC) instead of a commercial-grade PC when the application required rugged and reliable equipment are numerous. IPCs can cost three to five times as much as their commercial-grade counterparts. However, the benefits gained with the IPC are very often well worth the additional cost.
The largest advantage of using an IPC vs. a commercial-grade PC is environmental protection. IP ratings of 65 and above are not uncommon for an IPC, while environmental ratings for a typical desktop computer are rarely listed. IPCs are often built using fastening screws instead of plastic clips; cable connections utilizing locking mechanisms as opposed to friction fit connectors; and quality construction that is absent from mass-produced, low-cost equipment found in an office environment. Dust and various vapors are present in most factory environments. Installing the computer in a sealed enclosure helps, but enclosures only work when they remain closed. Routine maintenance or resetting a circuit breaker exposes an unprotected computer to the contamination in the surrounding atmosphere. Standard industrial control equipment is designed to operate with these contaminants present; office grade equipment is not.
Overheating is one of the biggest causes of failure with electronic equipment. Integrated circuits temperature-rated at 0 °C to 70 °C work perfectly fine in an office environment, but devices rated at -40 °C to 105 °C are better suited for a plant floor. In extreme situations, military-specification (-55 °C to 125 °C) components are available. Industrial-grade electronics are typically two to five times the cost of commercial; mil-spec devices are even more expensive. A commercial computer usually has an external cooling fan to combat overheating. An industrial computer typically employs a large external heat sink to maintain environmental protection or, if using a fan, extensive filtering. If required, completely sealed, liquid-cooled units are also available.
Quality industrial computers always have shock and vibration ratings. Shock mounting internal components and using damping material to mount the entire computer help to lessen the effect of machine vibrations and resonance. Gauging the quality of the mounting methods and mechanical joints employed in the construction of the computer provides insight into the quality of overall engineering for the product.
A modern, commercial-grade, hard-disk drive (HDD) rotates at speeds up to 7,200 rpm. The tight tolerances between the magnetic pickup heads and the very high data density on the storage platters make HDDs very susceptible to damage from mechanical shock and vibration. Most drive manufacturers have built-in antishock technology in all of their products or make it available for some additional cost. Check the model number of the drive on the manufacturer’s website to confirm the hard drive you are buying has this technology.
Another choice worth investigating is a solid-state drive (SSD). An SSD can cost four to five times more per gigabyte of storage space compared to an HDD, but a greater tolerance to shock and vibration, and possibly a larger temperature operating range, may make the solid-state drive a superior solution.
Resistance to electrostatic discharge (ESD) as defined by IEC 61000-4-X, MIL-STD-331 and MIL-STD-750 and electromagnetic interference (EMI) as defined by IEC 61000-3-X and MIL-STD-461 are critical to an industrial computer. The high voltages and currents commonplace within a factory environment can cause serious damage to improperly protected computing equipment.
IPCs are available in many different form factors. They include single-board computers, box PCs, panel PCs, chassis-mounted motherboards with expansion slots to allow installation of specialized cards, 19-in rack-mount systems with hot-swappable power supplies and drives and blade-style clusters. Single-board computers include the processor, memory and I/O ports. They are typically fanless and operate on dc voltage with limited expansion capabilities; a single-board system is often used in embedded installations or as a single-purpose device to run a specific application.
Box PCs are multi-component products that provide a greater selection of components. They can offer expandable memory, choice of HDD or SSD, mini peripheral component interconnect express (PCIe) slots, USB ports and other selections. More flexible in design than a single-board PC, they are still built to withstand harsh environments. A box PC can be used as a prototyping platform when designing an embedded system or can be used as a multi-purpose general computer able to run off-the-shelf application software. DIN-mounting adapters simplify inclusion inside a control enclosure.
Panel PCs combine a computer with a display, usually a touchscreen. Operating a runtime version of standard HMI software, a panel PC can provide database connectivity and a communication path to multiple networks all within one device. Custom software applications can be written that exceed the functionality of a standard HMI, providing greater design flexibility. The cost of a panel PC can often exceed the cost of a standard HMI-and-computer combination. Consider the cost of replacement if the display becomes damaged. Some manufacturers offer repair methods that do not require replacement of the unit as a whole if the screen is damaged.
Chassis-mounted motherboard computers resemble a common desktop personal computer. Layout and configuration are similar. Industrial versions use higher quality components and better construction than what commercial-grade products employ. The motherboard includes the microprocessor, memory, bios and associated I/O ports. The power supply is a separate component, and expansion slots may be included to add needed communication interfaces (including most industrial fieldbuses), video display ports and digital or analog I/O.
Rack-mount, 19-in and blade-style computers are also available but are more likely to be used in a testing or networking system. Ruggedized laptops have been around for a number of years, and shock-resistant tablets are appearing, though they are typically considered peripheral devices and not part of an actual control system.
ALSO READ: PLCs, PACs and IPCs ─ controller terminology explained
The range of hardware choices varies from manufacturer to manufacturer. Different CPUs, memory types and amounts, HDD or SSD sizes and interfaces are often customizable. Options to directly connect to most major fieldbuses, including the ability to act as an actual node on the network, can simplify communications with other control equipment. Additionally, multiple choices in operating systems provide a stable platform for existing software.
IPC manufacturers often provide multi-year support for the products they sell. Commerical-grade PCs become obsolete after a relatively short period of time. Before investing in a product to be installed on a machine that is expected to last for many years, be sure the manufacturer of the computer will offer support over the expected lifetime.
All this is not to say there is no place in controls for commercial-grade PCs. If the purpose of the computer is to act as a terminal to communicate with a control device and the plant's network, a commercial PC can offer cost savings and configuration uniformity. If the computer is performing a required service the machine or control system depends on, weigh the advantages of using a product that is designed and built for the task.
Thomas Stevic is a controls engineer at Star Manufacturing, an engineering and production company in Cincinnati. Contact him at [email protected].
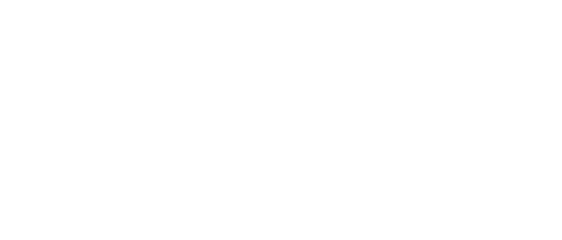
Leaders relevant to this article: