Accurate Fishing Products, in Corona, California, started as a summer work project during my college days in the early 1990s. Design and development of fishing reels in those early years led to the purchase of several Okuma CNC machines and related P-Series Okuma Sampling Path (OSP-P) intelligent numerical control. This provided a solid, robust path to automation, innovation and lights-out manufacturing that continues to expand and improve every year. With the right product designs, machines, control and innovation, we have figured out how to reel in successful lights-out manufacturing.
Let's go fishing
Accurate Fishing Products is a family-owned company started in 1950 by my grandfather. Much of its early business was centered around the aerospace industry and the early days of turbine engine development. At that time it was mainly a grind shop with the ability to hold tight tolerances on turbine shafts and turbine parts. In the 1970s my dad got involved and moved Accurate Fishing Products into the CNC era. The company got involved with all of the processes needed to machine complete turbine products, such as shafts using CNC lathes.
My brother Douglas and I got involved in the early ’90s during our college years at Northern Arizona University. Over the summers, we started manufacturing a variety of things, such as products for mountain bikes, jet skis and golf landscape equipment, and we began selling them on our own. We started dabbling in the fishing industry and that took hold. People were buying our new products. We became a two-part company, working in aerospace and fishing, which was small but developing a following.
Design and development based on a need
In the mid-1990s, my brother and I started making conversion kits for Penn reels. With our kit, you could take your plastic reel and put precise aluminum parts in it and then you’d have a pretty good reel. However, we kept fighting all the tolerances and related issues with someone else's product, so we thought we could make a whole reel. We performed significant design, development and testing to figure out a better way to do it.
We started by taking reels apart and figuring out how they worked and realized the reel designs had some serious flaws. We understood effects of forces and loads on shafts and related tooling, so we could never understand how the manufacturers developed drag pressure with just one pressure plate on the side of a reel. That's like putting the brakes on only one side of a car. Evening out the drag by applying it on both sides of the reel is a much more mechanically efficient and balanced system. This simple idea ending up being pretty revolutionary.
It took several years to develop our first fishing-reel product, and it required a lot of trial and error to get it to work. There was much more to it than we thought to transfer the force from one side of the reel to the other through a shaft. We figured out how to do it and brought it to market in 1998 and called it the TwinDrag. It was a $1,000 reel that no one thought we could sell, but we couldn't keep them in stock.
We started out making them one at a time and ended up manufacturing hundreds and hundreds, selling everything we could make. It revolutionized how people thought about taking a small reel and catching big fish on it. This little reel could apply so much drag pressure, it allowed people to do that. If you look now, guys are catching 200 lb fish on reels a third of the size of what was needed in the 1990s and before. And the reels don't break under the force. They can handle it easily, lasting for years.
The TwinDrag reel was a big thing, and we patented it in 1998. Along with the idea of the TwinDrag and related caliper, you must have strong supporting hardware, such as stainless steel shafts along with strong gears and solid billet frame, side plate and spool. All of that had to come together in the TwinDrag system, since, if you didn't have a strong, robust inner working in the reel, it wouldn't work well. Strong parts made a sweet design, and it's made in America by American workers.
Hooked on an open platform CNC control
Figure 1: The OSP-P series has developed over the years and has gotten better with its open platform concept.
As the fishing-reel business developed, we started buying Okuma CNC lathes, moving away from other manufacturers because we liked the fact that Okuma made the whole machine, including control hardware, drives, axis motors and software. We had dealt with so many problems in the early days when we were calling several different manufacturers to support a single machine. We felt Okuma could be a one-stop shop for machine and support and bought many over the years (Figure 1).
We started falling in love with the Okuma OSP control. The OSP-P series has developed even more over the years and has gotten better with its open platform concept. It has been easy to use and highly reliable. The OSP-P runs on a Microsoft Windows operating system and an Intel-based hardware platform, making it simple to connect just like most computers. We especially like doing background editing of the CNC program using a PC. We can take the program from the OSP-P control side and edit on the PC side, basically just editing text (Figure 2).
Figure 2: The controllers can be connected to the factory Ethernet, and programs can be downloaded from a networked PC.
The ability to connect the controllers to our factory Ethernet and download the program from a networked PC is appreciated, as well. We use a ReadyNAS dedicated server on our network to store, protect and back up our data. All the programs are stored on that server, and we pull them off and load them to the CNC machines as needed. On a weekly basis, all programs on the CNCs are backed up to this server.
When we build programs on Mastercam, creating new G code, we can access these programs that are on the server from any machine on the factory floor. In the past we had problems with storing programs on a machine because sometimes, when you load one, it would say you are out of memory, forcing us to keep only the running program on the machine. Now with the new OSP-P control and ReadyNAS server, it doesn't matter; we can store all we want in the CNC controller (Figure 3).
Figure 3: With the OSP-P control and ReadyNAS server, the CNC controller can store more programs than just the running program.
Since we have more than a thousand CNC programs on the server, we built our own file-management system using FileMaker Pro, an open-source database. All of the programs are stored there under a program name, part number and record number. We use the record number to create program numbers, which works well for revision control, storage and reuse of CNC code, as well as keeping track of the related cutting tools needed.
The control on the Okuma allows the CNC interface to be minimized, opening a Windows PC interface and making it easy to access the network and any files stored on the server. It is even possible to access the Internet or email, but we don't use this functionality. We do access program files and edit them as needed, using notepad or Microsoft Word, and other functions to compare programs, copy and paste.
Fishing lights out
Figure 4: In the late 1990s, Accurate Fishing Products added CNC milling products.
During the initial development of the reel, Accurate Fishing Products was mostly a CNC lathe shop. In the late 1990s, as our fishing product line grew, we added CNC milling products, such as the Okuma Cadet Mate 4020 CNC vertical mill machining center. These machines worked out well and helped to continue the growth of the fishing products through the early 2000s. In 2007, we started adding Okuma horizontal machining centers, as well, and we currently have more than 20 CNC machines of various types. Most are Okuma (Figure 4).
We ended up purchasing an Okuma MA-400HB 10-pallet system—a pallet pool—which enabled automated manufacturing. It reduced setup and programming times and made machine loading and part flow more efficient, which really helped us to increase production. Once set up for automatic operation, the pallet pool enabled unmanned operation of the CNC and the beginning of lights-out manufacturing at Accurate Fishing Products.
The Okuma OSP-P control worked great and provided easy integration to the machine, loading device, programs and tombstones—removable tool holding grid plates. Okuma provided all the hardware and software making the pallet pool a quick success. We could load up to 10 pallets and go home at 6:00 pm, and the machine would run all night long. When we returned in the morning, we'd have 10 completed pallets. It was a great labor saver.
Innovation in machining and control
Figure 5: Lights-out manufacturing allows Accurate to make spools all day and night.
Due to the lights-out success of the Okuma pallet pools, we also moved to install a solution from Gosiger, a machine-tool distributor and manufacturing-solutions provider headquartered in Dayton, Ohio, where it integrated a Fanuc robot and palletizing system to one of our lathes that was making reels (Figure 5). This added more lights-out manufacturing. We were able to make spools all day and night with the robot loading and unloading the lathe.
We added live tools on the lathe turret, which enabled milling, drilling, tapping and reaming on the machine, and it has a sub-spindle, so we can machine 100% of the fishing spool on one machine. In the past, this took three machines and four different setups. This provides huge time and cost savings in manufacturing.
Accurate Fishing Products now has six machines that run lights out, but it needs to know what's happening on the manufacturing floor when no one is there. Okuma uses what it calls The Intelligent Numerical Control (THINC) CNC Apps technology, where it collaborates with users and programmers. Okuma has many programs that can be downloaded to the Okuma OSP-P control providing efficiency-enhancing tools and advanced functions, similar to apps on a smartphone.
CNC apps and programming
One THINC CNC App I really like is the alarm app because it's a great help with our lights-out manufacturing. When a CNC machine has an alarm, it sends a text or email to the technician, detailing the problem. It can also send a snapshot of the CNC controller graphical screen. The personnel on call to support lights-out issues benefit from this app because, depending on the alarm, it can be reset remotely, without a trip to the facility in the middle of the night. Hundreds of apps and functions are available for download. Okuma has had apps available for the last four or five years, but, in the past year, the number of apps available has grown significantly. It is very easy to use these apps in the OSP-P300 control.
The Okuma OSP-P300 just came out and it has a lot of useful features and much more usable information, and it easily connects to automation such as pallet systems and robots. M-codes and discrete I/O provide handshaking signals to quickly interface the automation together.
One of the features of the OSP-P control I like is to create reusable subroutines in G-codes and M-codes for repetitive routines or tasks. An example is a routine to perform a tool touch-off to check if a tool is broken. I also use these routines to move to certain positions in the machine. Once the code is created, it can be called from a CNC program whenever needed. Another example of reusable code is the washdown of the tombs, similar to a four-sided vice, typically needed at the completion of each part. There is no need to write the code on every machine to turn on the wash spray and move the pallet around; I just call the wash program that is native in the control.
We are moving into high-tech manufacturing to enable more lights-out manufacturing by adding more robots, automated equipment and apps using the same workforce. The Okuma OSP-P control was a big enabler. The number of employees is growing more slowly, but we have more highly qualified people running these machines. The robots are doing the repetitive functions while the employees are doing the high precision work. That leaves more time to do other important things. Let's go fishing.
ALSO READ: Safe and fully integrated industrial chainsaws
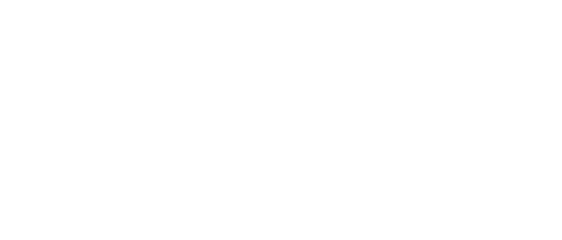
Leaders relevant to this article: