In pharmaceutical and medical applications, there are many cases where a syringe needs to be filled, to have its contents inspected and its label printed and validated. In these types of applications, it's common for pharmacists or pharmacy technicians to perform these operations at a cost of approximately $65 or more per hour. These operators have lots of education, but handling syringes, inspecting vials and applying labels is not the best use of their time.
To be more cost effective in the competitive pharmaceutical market, machine automation with programmable logic controllers, collaborative robots, cameras, laser markers and label printers must be used to do the work, but all of these smart devices must be tied together. To do that, a modern HMI/SCADA system can be used as a gateway to connect all the devices via Ethernet, in addition to providing a graphical operator interface, database functions and Internet-of-Things (IoT) access.
FP Developments in Williamstown New Jersey, makes a variety of machines for the pharmaceutical and medical industries that bring these smart devices together. Its machines also work with a variety of consumables, such as bulk bags of medicine, syringes and product labels.
Needs develop into innovation
FP Developments is a family-owned and -operated business started in 1963. About 20 years ago, Marvin Samson, a customer active in the specialty pharmaceutical industry noticed there was a big problem in the country. The problem was that there were many process steps/operations and a significant amount of time for a nurse or pharmacist to produce a vial of medication that is ready for use on a patient. That's too many, so he came up with a better delivery method to take the medicine from a bulk bag to a deliverable unit—a syringe full of a known dose.
Samson's experience was a big help with development of our automated vial-filling machine two decades ago. He started off working in a pharmacy, and, instead of becoming a pharmacist, he started a pharmaceutical company, which he then sold and started a pharmaceutical distribution company, which he also sold, and started a different type of pharmaceutical company. He asked FP to make its original syringe-filling machine.
Working closely with Samson on the original filler-machine requirements and concept, FP Developments was in a unique position to provide pharmaceutical and healthcare machinery systems. Samson's needs and experience fit well with FP's design, project development, manufacturing methods and technology and installation and validation capabilities.
FP Developments created its first automated filler machine several decades ago. It replaced high-priced operators with a highly accurate and efficient machine. Over the years its solid-modeling CAD/CAM systems and design capabilities moved it into turnkey system development and integration with other OEM equipment.
There has been high customer interest in robotic filling, assembly, labeling and inspection. Many of our new designs and manufacturing capabilities center around fully integrated collaborative robotic work cells for small-scale pharmaceutical and medical device production. FP's new labeling system is a new entry to this price-sensitive market. It's smart devices and collaborative robots connected via Ethernet through an HMI.
Labeling system
Figure 1: The automated filler machine replaces high-priced operators with a highly accurate and efficient machine.
(Source: FP Developments)
FP Developments created an automated, hands-free label-applicator system to reduce manufacturing costs and eliminate the waste, errors and repetitive motion related to manual labeling methods. The system uses a Cognex In-Sight VC200 multi smart camera vision system connected to a Cognex In-Sight 8402 vision system/camera and Cognex DataMan 8600 barcode reader, a Universal Robots UR3 robot and a Herma 400 label applicator; all are talking over Ethernet. There are no discrete signals used; all smart-device handshaking is done through the Ethernet connection.
The UR3 robot picks up a vial from an infeed nest and inspects fill level and presence of the stopper. It then moves the vial to a Videojet printer and applies the label. The label is then scanned and verified by the In-Sight camera. Labels that failed verification are placed in a reject bin. The robot places good parts with labels attached in a bag, or in a bag of 25, depending on configuration.
To operate the collaborative robotic labeling system, the operator uses the HMI to log in and then enters the work order. All of the printed work order data can be entered manually, scanned in using a Cognex DataMan 8600 Series barcode reader, or, with the additional of a Pro-face HMI, data can be pulled from an SQL database with a single scan of a 2D ID.
HMI adds capabilities
The In-Sight VC200 vision controller is a smart device. It's network-ready and connects directly to up to four Cognex cameras. In the label-apply machine it is used to inspect the stopper and verify the printed label.
The VC200 includes a graphical HMI that provides remote access via a Web browser on a local Ethernet network. It also provides the programming platform to configure the smart cameras, acquire and inspect camera images and communicate the results to the printer and UR3 robot to synchronously trigger their cycles, as well to automate the label-apply machine sequence.
The capabilities of the Pro-face HMI and its data entry fields, on-screen keyboard and database access features enable a variety setup options beyond what is possible with a VC200 vision system alone. With a simple scan of a work ticket, the machine can control the location of the barcode label print, populate the print data, define the need for a tip cap and execute a variety of other requirements that can be pulled from a database.
This labeling machine can operate standalone or integrate with adjacent devices. The Pro-face HMI makes the integration to the upstream filler and downstream inspection equipment easy. It also adds significant data collection capability. We know every alarm, every point of data, all collected through the Pro-face HMI using Ethernet.
The HMI is the BOS
To integrate a production line, we use Schneider Electric's Pro-face Blue Open Studio (BOS) development and runtime software as an HMI/SCADA on our machines.
It provides animation, trend analysis, graphical drawing, recipes, reports, OEE dashboards, library of symbols and VB script; it’s also easy to use. It has built-in tag integration with Schneider PLCs, where used, and provides more than 240 drivers to quickly connect with other smart devices such as cameras, robots and printers. It also enables remote access, data logging and retrieval, OPC connectivity and automatic email delivery on our machines.
The Pro-face BOS basically acts as a gateway. It can accept data from outside sources and provides a two-way connection to other sources. For example, there is a script program for the data that needs to be sent to a Videojet 3020 10-Watt CO2 laser marking system on one of our inspection machines. When a laser print is needed, it transmits the data and print command to the laser. The vision system is controlled in a similar fashion. It also tells the robot which program to run and how, such as, “Pick a syringe, and place in Tray Position 3.”
A big part of the Pro-face BOS system is its ability to take advantage of intranet and Internet connectivity. It can connect to any database, and, in our case, we use SQL. It's an easy way to create an SQL bridge with a graphical user interface. It also allows remote viewing of the data using a smartphone, tablet or PC.
On a production line, all of the scanned data, all of the alarms, all of the failures, all of the logins are handled by the BOS. We pull the data from the PLC, camera, robot, RFID unit and other sources.
The Pro-face BOS HMI also controls user access through user name and password. Where needed for tighter security, it can include two-factor authentication that reads an RFID tag or barcode added to a user ID.
Data and support needs
FP Developments’ previous version of the filler machine's control hardware needed improvements and would have been too expensive to upgrade to provide access to the data. Because of this, we started from the ground up and designed a new control system. This system is the realization of Ethernet communication in the industrial world.
We use a Schneider Electric PLC, HMI and hardware to control and collect all of the data. The machine includes Schneider Electric motors, with Ethernet communication, for control and status. Any data point we have can and is being collected.
Adding a Universal Robot and its collaborative capabilities to a filler machine allows us to design a system without guarding, which makes the system much less expensive. FP Developments and our customers find the robot easy to use. Generally, onboarding a customer's on-site maintenance staff takes less than a day. They can keep the robot running, and, if they can't, it's all done over Ethernet, so we can remotely connect and correct most problems.
The customer simply needs to plug in the Ethernet cable to the programming port for us to support it remotely. We strongly recommend that the programming port is disconnected when not in use, and we do keep the data communication and control network physically separate from the programming network.
ALSO READ: Design distributed I/O on your machines instead of running bundles of wires
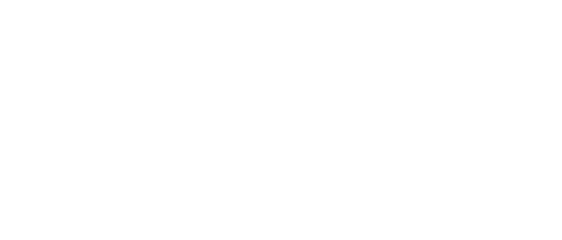
Leaders relevant to this article: