PC-based control yields 33% higher controller functionality while reducing cabinet and machine footprints
Good things come in small packages. There is perhaps no better way to describe Edge Automation, a custom machine builder and automation solutions provider based in London, Ontario. Though our company is small—employing around 47 skilled designers, builders and engineers—it is also nimble, creating and commissioning some of the most technically complex automation projects for a wide variety of industries, taking on many projects where other, larger integrators have said no.
For more than 15 years, Edge Automation has offered complete, vertically integrated automation solutions, designing and building everything from small CNC operations up to the most complex robotic systems. The company serves an incredibly diverse set of markets, with customers hailing from nearly all areas of industry, including automotive, consumer goods, agricultural equipment and food and beverage. Operating as a custom automation provider means that all the products built by Edge are determined by customer requests. Capable design, machining and assembly services on-site bring customer goals of technological advancement and innovation to life.
“Edge Automation offers a wide range of integration options, taking ideas from initial concept design through to final integration and commissioning,” explains Joel Squire, general manager at Edge Automation. “We are a streamlined team of multitaskers from a business standpoint. We don’t delegate work to many different groups, or only offer to build one section of a machine or concept. Our products are complete turnkey systems, designed and built with in-house expertise (Figure 1).”
Figure 1: The Edge Automation streamlined engineering team of multitaskers includes (from left) Jason Hooper, electrician; Travis Thomson, machine assembler; Simon Raimbault, machine assembler; Luke McKeen, mechanical design manager; Gerard Regier, president; and Chris Timmermans, senior controls, 309A electrician.
You name it, we can build it
This variety in projects at Edge necessitates an engineering toolbox with a wide range of hardware and software solutions. This led us to seek out an automation partner with a comprehensive lineup of tools, ultimately leading us to Beckhoff Automation. The business relationship has grown steadily, but has risen substantially in the past few years, as Chris Timmermans, senior PLC programmer at Edge Automation explains. “We typically conducted between one and three projects per year with Beckhoff at varying levels of complexity, constituting approximately 10-15% of our business,” he says. “In the past three years, however, there has been a dramatic change. Now, around 60-70% of our business involves Beckhoff hardware and software—a testament to the strength of this partnership and the power and flexibility of Beckhoff technology.”
Therefore, when a healthcare-product manufacturer approached Edge with a difficult manufacturing puzzle, we jumped right in to develop a solution automated by Beckhoff.
Approximately six years ago, the healthcare-product manufacturer commissioned a machine from Edge to assemble plastic parts for a health-product-dispensing system. As sales grew, the current system quickly reached its limit. “At the time, the customer was working around the clock to keep up with demand for the product but was having a hard time keeping enough staff on-site to achieve the desired throughput,” explains Timmermans. Even with these difficulties, demand continued to grow and the company needed to scale even higher. “Two years ago, the customer approached us to build a second-generation machine to help streamline the process and meet growing demand,” he adds.
The new machine consists of two assembly cells dubbed “PUC” and “PAC.” The PUC, or main assembly cell, assembles a series of plastic and rubber parts to create the dispensing system. The PAC, or subassembly cell, supplies the PUC with parts and pre-installs several rubber components before moving components downstream. A third additional subcell was added to allow on-site production of yet another product flavor for the healthcare line, and this integrates directly into the original two-piece system seamlessly.
We also developed a custom feeding solution for the application. The handling of the rubber components is a point of pride for Edge, as two other integrators turned down the project because they could not find a workable solution to feed the parts into the system. “We knew it would be a challenge, but our group sat down and dissected the issues the previous two competitors encountered, and we were able to build a custom solution that works fantastically,” says Timmermans, who jokes that other vendors still ask us how in the world we made the solution work.
“Essentially the reason our competitors fell short of a reliable solution was vision, where they imposed limitations as to how the task was to be accomplished, basically working inside the box,” explains Timmermans. “Our group threw the box away altogether and reinvented the way these types of parts are fed.”
System-integrated solutions
The demanding control requirements of the three assembly cells are handled by a Beckhoff CX2040 Embedded PC, which offers a quad-core 2.1 GHz Intel Core i7 processor and 4 GB DDR3 RAM (Figure 2). This powerful device controls the entire machine, including HMI and motion control functions.
Figure 2: Inside the cabinet, the embedded PC provides full system control in a compact, DIN-rail mountable format. The robust embedded PC helped Edge to cut PLC scan times in half.
“Assembly process cycle times of 1.8 seconds formed the baseline we wanted to achieve with the assembly machinery,” says Timmermans. “By integrating the CX2040 as our controls centerpiece, we meet and even exceed these goals; plus, we reduce costs with a centralized control solution.”
Providing HMI operator interfaces around the machine are three 12-inch CP2912 multi-touch control panels running third-party HMI software, which seamlessly integrates with TwinCAT via ADS communication (Figure 3). In addition, a CP2712 multi-touch panel PC is connected to the main cell and provides the display for the CX2040, running a third-party HMI software solution.
Figure 3: The multi-touch control panel displays the custom HMI developed by Edge, giving machine operators a feature-filled, modern machine interface.
“The four multi-touch panels all display the exact same HMI software,” explains Timmermans. “In this manner, all operators have access to the rich HMI information via an intuitive multi-touch screen anywhere around the machine. From a design standpoint, this was our goal, to develop an HMI interface one time but deploy it across the entire machine. When the additional cell was added, we were able to bring up an additional HMI interface in minutes with the Beckhoff system.”
TwinCAT 3 automation software platform from Beckhoff serves as the CX2040 runtime and programming environment for all automation tasks. TwinCAT has been a huge boon for numerous company projects, notes Timmermans. “On the original machine, we had two separate systems just for the PLC and HMI,” he explains. “This was further extended with standalone motion controllers and valve banks requiring setup and configuration. TwinCAT, paired with EtherCAT as its communication backbone, enabled us to bring everything into a single development environment (Figure 4). We eliminated almost all of the device-specific setup and configuration, consolidating our required commissioning toolset down substantially. This drastically improved the serviceability of this equipment over the original design.”
Figure 4: Machine-mounted modules move data acquisition closer to the machine processes, saving cabling costs. The EtherCAT machine communication backbone streamlines cabling and installation processes.
Features such as core-isolation to intelligently assign separate control tasks to specific cores in multicore processors bring down overall CPU utilization and increase machine performance, says Timmermans.
System communication outside of electrical cabinets is handled by a collection of EP Series EtherCAT Box modules (Figure 5). This I/O hardware provides a significant upgrade over previous systems, removing topology limitations in terms of communication system architecture and wiring.
Figure 5: Edge engineers created a custom communication topology to meet customer needs.
“From a machine layout standpoint, the EP3174 analog input modules provide unique advantages as each input can be parameterized,” says Timmermans. In this way, we were able to accommodate multiple voltages (-10…+10 V, 0/4…20 mA and 0…10 V) by configuring each input separately.
Previous systems were limited in terms of fault localization and troubleshooting, explains Timmermans. “The way the EtherCAT Box modules integrate into TwinCAT software offers a clear advantage for us, particularly with regard to service,” he notes. “It is much easier now to determine the exact location of any line or signal interruptions to quickly remedy the situation.”
We utilize a series of TwinSafe I/O modules for control of standard safety devices, including guard doors and e-stops. “The whole safety system is driven by the EL6900 TwinSafe logic terminal installed directly into the standard I/O rack,” explains Timmermans. “Up to 128 connections to other TwinSafe devices can be established with the EL6900, and it comes at a very competitive price point.”
Safety functions are easily integrated via the combination of TwinSafe I/O terminals, EtherCAT and TwinCAT automation software. “We were pleased with the simplicity of safety integrated into the existing EtherCAT system,” says Timmermans. “The reduction in safety-related wiring was a great benefit.”
In addition to safety, the assembly machinery requires a robust motion control solution, and the Beckhoff AX5000 series servo drives fit the bill. We maintained consistency in safety technology by equipping the AX5000 drives with AX5805 TwinSafe drive option cards. The AX5805 permits the easy addition of motion-specific functions for safe stop, speed, position, acceleration and rotation.
The AX5000 series hardware brought some particularly beneficial features with regard to the modular positioning system. “This project required a forever-forward motion configuration for the dial indexing system,” explains Timmermans (Figure 6). “We achieved the desired results in a matter of minutes, where on previous systems it took us weeks to get it working correctly.”
Figure 6: The forever-forward motion profile enabled by the drives and servo motors helped Edge to overcome a significant obstacle in the assembly process.
A collection of AM8000 series servo motors are connected to the AX5000 drives, offering simple integration through TwinCAT software. The AM8000 series represents a sleek, cost-effective motion solution, reducing the necessary cabling and connectors by as much as 50% through the standard One Cable Technology (OCT) found in the motors, notes Timmermans.
Programming effort and PLC scan times slashed
The Beckhoff system helped Edge to increase performance for the healthcare-product manufacturer without adding costs, all while reducing the overall size of the control cabinet and machine footprint. “From a panel standpoint, I approximate that we have at least 33% higher controller functionality in this system,” notes Timmermans. “However, the control cabinet is actually smaller—largely due to the compact I/O solutions, including the TwinSafe system. The cabling reductions from the OCT-enabled servo system and the implementation of the 12-mm-wide EL7211-0010 servo terminals naturally made significant contributions, as well (Figure 7).”
Figure 7: Utilizing 12 mm-wide servo terminals for many of the smaller motion requirements coupled with synchronous servo motors for compact drive technology significantly improved machine capability while reducing panel space requirements.
TwinCAT 3, and specifically the system manager, has added value to the Edge toolbox. The ability to quickly and easily add new devices to the control system was game-changing. TwinCAT also allows us to reuse code on future projects, saving a significant programming time and effort. We found the greatest benefit from the Beckhoff system when it came to programming the motion system, reducing the necessary time to achieve the motion goals from a few weeks to five minutes or less.
The software licensing structure offered by TwinCAT was also extremely appealing to us. “The free engineering and development licenses have been great tools to help us service and support our equipment,” says Timmermans. “Simply not having to pay thousands of dollars in licensing fees to connect to end-user equipment is a major consideration. Some of our customers also appreciate the flexibility to equip their service techs with the free engineering software and avoid expensive seat licenses.”
Perhaps most importantly, we were able to cut our PLC scan times significantly, dropping to 1 millisecond static, down from 30 to 50 milliseconds. “There are actually three key tasks that are scheduled to execute every millisecond, one for each of the three cells,” explains Timmermans. “This ensures that a fresh EtherCAT frame is pulled in with updated data of the current machine state prior to executing the machine logic. This is in addition to the motion-control task scheduled every 500 microseconds, which is managing the 10 servos on the system.”
In addition, through the core isolation functions offered in TwinCAT 3, we were able to isolate PLC tasks of the project away from Windows to a dedicated core, utilizing only around 18% of the core processing capacity.
“There are still two completely unutilized cores available to us for future expansion on the CX2040,” comments Timmermans. “This is a far cry from previous systems, where we nearly maxed out the controller. By moving to the more robust Beckhoff control platform, we have much more latitude with machine design and a sizable amount of room to add new functions.”
Figure 8: Chris Timmermans, senior PLC programmer at Edge Automation, runs the new assembly machine through its paces.
As Edge continues to push the boundaries of engineering for projects of all sizes, we now have the tools in place to meet the growing demands of our customers. “PC-based control and EtherCAT provide a flexible toolbox that can be used in all foreseeable future projects,” notes Timmermans (Figure 8). “The abilities to quickly and easily integrate new devices in minutes and to reuse machine code help us to continue proving that no custom project is impossible.”
ALSO READ: Romeo Engineering leverages PC-based control to improve manufacturing speed and accuracy
Latest from Embedded Control
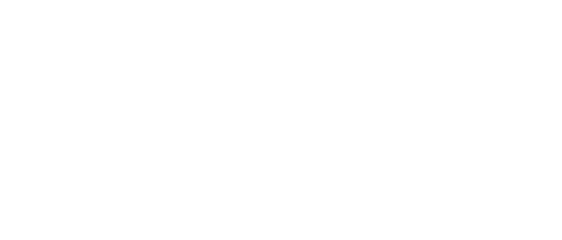
Leaders relevant to this article: