How to design and build a digital manufacturing device
As a mechanical engineering student, I was drawn to mechanical design and manufacturing. I was part of a team that built open-wheeled racecars where we did a lot of work with sheet metal.
Unfortunately, Penn Engineering did not have a waterjet cutter because they’re so big and expensive. Since Penn didn't have one, the students built a small one as a senior design project in 2012 with a team of five. The goal was to build a small, affordable waterjet for the university.
Three years later in 2015, I partnered back up with my co-founder and CTO Matt Nowicki, and we quit our jobs and started a company, Wazer. That started our product development. After a couple months of development at HAX accelerator, Wazer created the first desktop waterjet and launched it on Kickstarter in 2016, where it raised $1.3 million in presales. About 1,300 backers pledged $1.3 million to help bring this project to life. Our future customers pledged money up front to support us and be the first ones to get a machine.
Fast forward to 2019, and we are in production of the first desktop waterjet—a digital manufacturing device—that can cut parts out of any material, primarily metal, but also glass, stone, composites and thermoplastics (Figure 1).
Figure 1: The first desktop waterjet—a digital manufacturing device—can cut parts out of any material including metal, glass, stone, composites and thermoplastics.
(Source: Wazer)
We have a corporate headquarters in Brooklyn, New York, that is also a production facility where we assemble, test and ship every machine. As of early 2019, we have completed shipping machines to all of our initial Kickstarter backers and are now filling orders we have received over the past two years.
It took a long time to get to production with three years of development, including a year of product development and two years of design for manufacturing and production, but we are now building and shipping machines every day to a variety of customers, including industrial, education and professional artisans.
Cost-effective cutting
For $7,500, you can have a compact and contained desktop machine that can make precision parts in any material. Before Wazer, traditional, entry-level waterjets and other methods to cut precision sheet metal cost more than $100,000 and were too large and messy to fit in most workshops.
Our equipment enables professional-grade results at the desktop level in any workshop. The unit is fully enclosed, making it safe, clean and quiet to operate.
The big waterjets work at very high pressures, more than 60,000 psi, and require specialty components. What we have done is leverage hydraulic components from other industries and combined these off-the-shelf components with some customization. This made a more affordable machine that still has sufficient cutting power.
It’s the only desktop machine that cuts virtually everything. It provides a quick way to iterate designs without having to spend time and money to send a part drawing to an external waterjet service to be made. It also enables manufacturers to keep their large machines running while their Wazer desktop machine is used for prototyping and providing low-volume manufacturing.
It's on the desk
Wazer's high-velocity waterjet uses a combination of high-pressure water and sand-like abrasive particles to cut through the workpiece, achieving a high level of digital precision. The waterjet and pump need to be physically separate to isolate the vibration from the pump and motor.
The desktop waterjet has an overall size of 34 x 25 x 21 inches (864 x 635 x 534 mm) with an empty weight 110 lb and loaded weight of 300 lb. Its cut area is 12 x 18 inches, which covers a wide range of use cases, and is capable of cutting up to ½-inch aluminum and ¼-inch mild steel. A separate pump box, 21 x 15 x 11 inches (533 x 355 x 280 mm), is typically located under the desk or table.
This waterjet is easy to set up with no special electrical or water requirements. It runs on U.S. standard 120 Vac/60 Hz, or the new Wazer global 240 Vac/50 Hz version now meets electrical standards used in most countries. All that is needed is a water source, such as a sink or hose connection, a drain and two power outlets.
One of the original constraints for Wazer was to require minimal infrastructure changes, so you could use it anywhere. The requirements were that the system would work off a standard 120 Vac, 15 A circuit and a common tap-water source. The supply power source directly operates the 2-hp high-pressure pump motor without voltage conversion.
The water is open-loop with the tap water drained out at a rate of less than a gallon of water a minute when in use. The electronics on the gantry operates on a dc voltage, as do all the other machine components.
Design and development
Wazer developed the desktop waterjet in-house, including the mechanical design, electrical design, software and programming. We have a big team; there are 23 of us now.
We wanted a desktop system and making the waterjet smaller like that made it more difficult to design. Many different subsystems needed to integrated into one enclosure. We were rethinking water jetting from the ground up.
For example, usability was important. We wanted the workflow to be streamlined, so the user could go from a drawing file into our software in less than two minutes and then onto the machine and cutting in less than 10 minutes. We wanted to press print and be printing instead of going into a several-hour setup process. This required onboard controls to prepare the cutting file when a start button is pressed.
Abrasive management is another important usability feature. This led to integration of the abrasive hopper as a drawer on the side of the machine for easy access and filling. Buckets were also integrated into the machine to collect used abrasive (Figure 2).
Figure 2: Abrasive management is an important usability feature that included integration of the abrasive hopper as a drawer on the side of the machine and buckets to collect used abrasive.
(Source: Wazer)
Normally, the wet, used abrasive collects at the bottom of the tank, and it's necessary to remove the bed, drain the tank and shovel it out by hand. We developed a suction system that sucks the abrasive from the bottom of the tank and dumps it into buckets housed within the enclosure that can then be easily removed. Garnet (crushed rock) is the recommended abrasive. Since it is a naturally occurring substance, it's safe to throw the used material in the trash.
Integrating all of these and other systems into one enclosure, making the machine compact and contained, was a nontrivial design problem.
Profile cut
The Wazer waterjet is controlled by a custom controller designed to run a custom flavor of the open-source Smoothieware firmware. The controller has the drivers built-in to run stepper motors, as well as all the digital inputs and outputs to run the machine.
We developed our own Web-based software called Wam that converts a drawing file into a G-code cut file. A new cut file is created by importing a drawing exchange format created in AutoCAD or similar (DXF) or a scalable vector graphics created in a graphics programs such as Adobe Illustrator, Corel Draw or similar drawing file (SVG) into our software.
Once the drawing is imported, it can be rotated and oriented on a virtual cutting bed. The material, thickness, cut quality, such as course or fine, and cut path, such as outside, centerline or inside, are also specified in the software. The output G-code file contains all the information the Wazer needs to cut the design in the chosen material and is loaded onto the machine through a USB connection.
There are basic controls and an LCD screen on the waterjet, which was done for the value they bring. It doesn’t require a computer or device to be tethered to the machine at all and operates stand-alone, which is different from most other jets and metal-cutting machines. An operator uses these controls and display to select the cut file, start/stop the waterjet operation or run a maintenance protocol.
Make the cut
There are many applications were CNC-like tolerances are not needed and a waterjet works well. In general, avoiding CNC, at all cost, helps the bottom line in manufacturing. And it's usually cheaper to work with sheet metal. In an example application, we converted a standard bike into a belt drive. The waterjet was used to cutout the pulleys and gear teeth that engaged the belt from ¼-inch aluminum.
As with any waterjet part, after a cut, there may be a burr on the bottom edge that needs to be sanded off, and the edges may not be perpendicular. Also, the holes, as a final pass, may need to be drilled and reamed and may not be suitable for press fit. However, the bracket outer geometry will be within approximately .010-inch tolerance, and the holes will be in the proper location. Brackets, for example, can be quickly made.
The cut produced by the water stream is roughly 1/16 inch (1.5 mm) in width, so that coincides with approximately the smallest feature—internal diameter or internal line width—you can cut.
By far the most expensive component in a traditional abrasive waterjet is the high-pressure pump. These subsystems operate at 60,000-90,000psi, generate incredible amounts of cutting power, and cost tens of thousands of dollars. We have figured out how to maintain useful cutting performance while significantly reducing the water pressure. So sure, we can't cut through 2-inch-thick steel, but do you really care?
Assembly required
To protect the IP, we assemble the waterjet here in the United States. We have an intimate knowledge of the assembly process, which is technically involved. We designed the components and worked with many different Chinese manufacturers to produce them.
The supply chain in China is at a much larger scale than it is here. Much of it is in southern China around Shenzhen. There is a tremendous manufacturing ecosystem there.
Our U.S. supply chain has many parts, as well. It starts with the innovation, the design and the understanding needed to assemble a complete system that functions correctly. There is also the firmware integration of the control software to run the machine and the web software to prepare the cut file. The whole package is where our trade secrets are, and all of that is happening at our U.S. facility.
With Wazer, we don't have a contract manufacturer; we don't have a factory in China making Wazers. However, to get the components made properly, we had to go live there and set foot in the factories of our suppliers. Our team still visits China constantly (Figure 3).
Figure 3: Wazer assembles the final product at its U.S. facility, but many team members lived in China for many months to set foot in the factories of its subcomponent suppliers.
(Source: Wazer)
We are our own contract manufacturer, and we have direct relations with sub suppliers in China who we work well with. To produce a $7,500 waterjet takes a lot of design, development and quality, low-cost components.
ALSO READ: Innovative technology cuts sawing costs
Nisan Lerea is co-founder and CEO at Wazer, a desktop waterjet OEM in Brooklyn, New York. He can be reached at [email protected].
Latest from Electromechanical
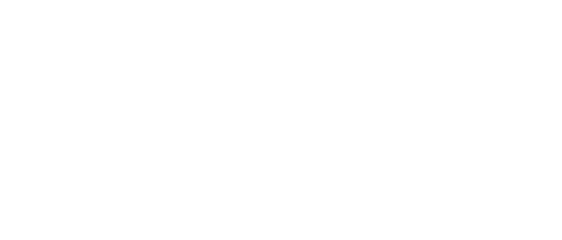
Leaders relevant to this article: