Man overboard! There are times when rescue boats must be placed over the deck and into the water to assist those in distress. However, launching a boat from a larger vessel is not easy, and the captain may need to make these launches and recoveries day or night—with little or no light. And it will need to be done in the open ocean, and that's not often flat and calm.
To further complicate things, the rescue boat may be launched while underway—the boat doesn’t stop. Allied Systems, a fabricator of material handling equipment, was contacted for these and other reasons. The marine industry desired a safer launch and retrieval system for rescue boats—particularly in adverse weather conditions. Safer operation was paramount (Figure 1).
Figure 1: A dual-point davit system uses two cables—one attaches to the stern of the boat, the other the bow which provides a safe and stable boat launch or recovery process.
(Source: Systems Interface)
Get the boat in or out of the water safely
Many vessels use a single davit to launch a boat. A davit system is basically a crane that’s used to lower and lift boats—relatively small boats—from the deck to the water and back. Examples include davits along a line of life boats that would be on an ocean liner and other large vessels.
The problem is if a 30-ft-long boat is lowered with one davit during a storm, the stability of that boat being lifted or lowered by one cable is very limited. Picture a severe, windy storm with significant wave action and then trying to lift a life or rescue boat off a large ship—with people on it—and then into the water. Invariably, the rescue boat will pitch about due to the motion of the parent ship from which it was launched, due to wind velocity and sea state. Wind velocity could easily propel the boat back and forth in an uncontrolled manner. This is dangerous for the crew and passengers that may be onboard, and impacting the side of the parent ship could damage either vessel.
A dual-point davit system uses two cables—one attaches to the stern of the boat, the other the bow. This system reduces the unwanted rescue boat motion. The dual davit lowers the boat very uniformly, which is much more stable and safe for the people in it, even when launched in a rough sea.
The solution
In the marine industry, many of the davit systems for shipboard use are manually operated using a single hand-driven or electric winch and a single cable. The Allied Systems' dual-point davit is automated, and it partnered with Systems Interface to design, manufacturer and test it. The operator console also provides more feedback on loading, positions, maintenance and troubleshooting.
Allied Systems, located in Sherwood, Oregon, has sold more than a half dozen of these specially designed dual-point davit systems. These systems have a nominal working load limit of 11,000 lb and can handle boats up to 30 ft in length. They are also designed to operate any time, day or night, from the North Pole to the equator, from flat water to Sea State 5, which is a rough sea with about 8-ft to more than 13-ft waves.
The Rockwell Automation control system solution was used to control the automatic operation of the system. The controller synchronized the two winch systems, and the operator station increased safety of both personnel and equipment.
Becoming shipmates
The new dual-point davit system was the first time Allied Systems worked with Systems Interface (www.systems-interface.com), a control system integrator and Rockwell Automation solution partner. The scope of work was basically divided with Allied taking on the mechanical and hydraulic design and related manufacturing aspects while Systems Interface took on the electrical design, control panel build and programming aspects.
Allied Systems began designing and manufacturing equipment for the wood product industry more than 40 years ago. Its success allowed the company to diversify into the marine, coal and agriculture industries. In the marine market, it serves a wide host of customers from family-owned companies to worldwide corporations and different government agencies.
Systems Interface has worked with Rockwell Automation for more than three decades. One of its fortes is the marine environment and, specifically, winch control systems and marine cranes.
Due to its customer's needs and control system requirements, Allied Systems contacted Systems Interface a few years ago to use our expertise in the maritime market to help to develop a new dual-point davit system.
Calming the hydraulics
Our controls engineers worked with the Allied Systems’ mechanical engineers helping to develop the dual-point davit system. Allied knows a lot about cranes but discovered there were some mechanical elements related to the system hydraulics that really didn’t accomplish what needed to be done.
One problem dealt with the limitations of the hydraulic fluid flow that did not allow the davit arms that positioned the rescue boat to move smoothly. And when you have two pieces of equipment, in this case with dual davits, it becomes even more complicated.
Allied came to us with the problem and asked if we could solve it with the control system. The hydraulics problem was described as a pulsation. Similar to water hammering, when a valve was closed, a pressure wave is sent backward up a pipe. This can make controlling the equipment very difficult. Instead of having a smooth flowing hydraulic power source, it fluctuates.
One option was to redesign the hydraulics. This would involve changing the size of the pipes and valves, as well as the pump. However, this was expensive and would also create a real-estate problem. There was no room anywhere to make its system skid larger.
The second options was to solve the problem by taking advantage of the diverse instruction set in the CompactLogix 5370 L1 programmable automation controller that Systems Interface specified for this system. This solution was essentially free to use, and its program could be modified quickly.
Of course we chose to solve the problem using the controller. Once Allied Systems advised us of the hydraulic flow issue, the Systems Interface engineers developed code in the CompactLogix to emulate what resized valves and pump motors would have achieved, and they did it while commissioning the system underway at sea. This mitigated the pressure wave and smoothed operation of the dual davits, and the time and cost savings using this approach was significant.
Keeping tension on the tail
When operating a davit system, the operator performs a number of discrete steps. The first step lifts the boat straight up off the supports. Once it reaches proper elevation, it is then moved toward and over the gunnel, the upper edge of a ship's side. When the boat is away from the ship and at the proper angle, it is then lowered. During these steps there is no speed or pressure control needed. And then things become more complicated.
Because the vessel may be underway when the boat is lowered, the water is moving, causing tension on the line, and there may be waves, as well. Even with all these variables, the winch must maintain a constant tension. If you don’t maintain constant tension on the winch lines that are holding this boat in place, the boat can very easily get out of control, turn sideways and capsize.
The Allied Systems CT (Constant Tension) system is critical for the safe launching and retrieval of the rescue boat, especially during storm conditions. The system maintains a constant tension in each of the two davit cables.
In constant tension mode, the davit winch pays cable out as the tension increases and reels cable in when the tension decreases. This improves safety by eliminating snap loads on the hook resulting from the boat rising and falling on the waves. By keeping the rope taught, the system also keeps the crew safe by not allowing a slack cable to wrap around equipment or personnel.
Key controls and operation
Systems Interface designed and manufactured the control system. The bulk of the components are from Rockwell Automation and are housed in two control enclosures, a davit operator console and a remote electrical enclosure.
The davit operator console includes a CompactLogix 5370 L1 programmable automation controller combined with bulletin 1734 Point I/O to save space. Other control hardware includes Allen-Bradley 1492 terminal blocks, model 1489 circuit breakers. Operator controls included series 800F operator devices, such as selector switches, pushbuttons, pilot lights, potentiometer, contact blocks and LED power modules. A series 800H emergency-stop button and model 855P panel mount alarm is also included (Figure 2).
Figure 2: The davit operator console provided both automatic and manual functions and was usable any time and any place.
(Source: Systems Interface)
The remote electrical enclosure was located on the crane. It included many of the same components as the console (Figure 3). Much of the Point I/O in the remote enclosure controlled the hydraulic system. Model 700-HK slim line relays and model 700-HN sockets are used as dry contacts to a variety of equipment outside the enclosure.
Figure 3: The use of the I/O and other space-efficient relays and circuit breakers allowed this remote I/O panel to fit in a small area.
(Source: Systems Interface)
The operator controls included automatic mode, manual mode and related functions. At an operator's request and with automatic mode enabled, automated functions are available at the touch of a button. These functions are controlled by the CompactLogix PAC and include move to park, move to embark and move to water.
In the unlikely event of a controller failure, manual hardwired functions are also available. Manually operated buttons and switches on the console control the hydraulic pumps and the valves that move the davits into position and operate the winches to raise or lower the boat.
Surviving the sea
The davit operator console is typically located on the main deck where the deck, rescue/life boat and sea surface can all be viewed. On the open sea, protection from the elements—the wind, waves, rain and snow—is a must, and all materials and components were specified with this in mind.
The operator must to be able to clearly see the dials, switches, toggle switches and joysticks. The environment can be very harsh. At the North Pole, you can have temperatures to -40 °F, in addition to the elements, and it can be dark. At the equator, temperatures can approach 120 °F in bright sun.
Testing at dry dock and at sea
Several different factory acceptance tests (FATs) were performed. Preliminary testing was done at Systems Interface to confirm the control system, HMI and PAC met requirements. The equipment was then shipped to Allied Systems, along with two of its engineers. Then our engineers spent about two weeks working with Allied in the shop where the dual davit system was set up. Instead of a 30-ft-long boat, metal weights were used to simulate a boat during testing.
After some optimization of the control and hydraulic systems, the customer signed off on a land-based FAT.
Ocean testing was done off the coast of California and was a lengthy process. The testing was extensive, as the customer would only sign off on the equipment if it was convinced no modifications would be necessary. The equipment needed to be problem-free, and, to prove it, they really ran us through the wringer (Figure 4).
Figure 4: Extensive testing was performed on the vessel and on the sea as the system needed to be problem-free and easily supportable once operational, when it left port.
(Source: Systems Interface)
The testing showed everything worked properly. It also confirmed that components could be changed out quickly by seaman, if necessary. Additional testing ensured it worked at night, in the middle of the day and during rough seas. The system passed.
This complex equipment was simple to use and support. Due to its successful maiden voyage, the customer has ordered five more systems. More than 60 identical systems are possible, as there are many ships on the sea.
ALSO READ: Control for massive foundations
[sidebar id=6]
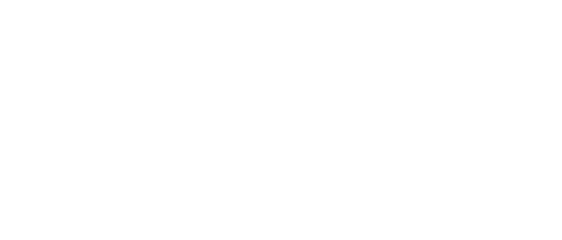
Leaders relevant to this article: