Control platform makes motion and safety easier to build
Inventek Engineering is a Santa Ana, California-based automation services company and systems integrator. Inventek’s experts provide creative and cost-effective turnkey solutions using industrial robotics, vision and sophisticated control systems. Its diverse applications include automated assembly systems, flexible bottling equipment and material packaging and handling.
For the past 30 years, Inventek has utilized the expertise from the engineers at Valin to better understand and master the technology it needs to best serve its customer base.
Inventek prides itself on attention to detail. By monitoring and controlling all the key elements in an automated system, it provides customers with a greatly improved and efficient process.
This in turn leads to higher productivity and lower overall production costs. Additionally, Inventek delivers systems that are streamlined and highly reliable, often the two qualities that customers desire most in an automation system.
In order for Inventek to continue delivering systems that meet its customers’ high standards, it needed to find a more intuitive, easily understood PLC technology and be trained on its use and features. For this, Inventek turned to its long-time partner Valin, which has kept up to date with the latest technology for the past 45 years.
Valin knows how to help design control systems and train customers on both hardware and software to shorten the learning curve. This allowed Inventek to focus on what it does best.
Valin’s engineers are essentially an extension of Inventek’s engineering department. They’ve worked side by side with Inventek on many projects over the past 30 years, both domestically and internationally, to solve a large number of challenges that ensured the projects were implemented successfully.
Inventek has had a number of projects in the automotive, life science and packaging industries.
In a recent automotive application, Inventek needed controls to interface with a six-axis robot, machine vision and pneumatic manifolds (Figure 1).
Figure 1: In a recent automotive application, Inventek needed controls to interface with a six-axis robot, machine vision and pneumatic manifolds.
The robot and machine-vision system performed assembly functions. The initial design assessment showed that controls with both EtherCAT and Ethernet/IP capabilities would be advantageous.
In the life-science application, the machine needed to have motion coordinated with the machine-vision system (Figure 2). After performing the inspection, the vision system would communicate the inspection results to the machine automation controller, which then calculated the required offset automatically after each cycle. The equipment design also required the integration of different safety devices, such as light curtains, safety door interlocks and e-stops throughout the machine. It required two human-machine interfaces (HMIs) so that operators could access them at different working locations on the same machine. This machine was designed using a lot of remote I/O. The end customer used many process recipes and needed to log data for FDA requirements, so a bar code reader with serial communication was introduced to select the correct recipe automatically.
Figure 2: In the life-science application, the machine needed to have motion coordinated with the machine-vision system.
In a packaging application, the customer wanted to control stepper motors for the precise rotation of a part before the robot inserted another part into it. The customer also wanted the ability for Inventek to service the machine remotely without compromising the company network. The secure connection would allow Inventek engineers to connect to the controls over the Internet and modify or troubleshoot programs and configurations without travel time or expenses.
Figure 3: The secure connection would allow Inventek engineers to connect to the controls over the Internet and modify or troubleshoot programs and configurations without travel time or expenses.
Inventek was looking for a way to better integrate all the motion, robotics and machine vision in the systems they design and deliver to their manufacturing customers. The solution needed to have simplified wiring and setup of industrial networks and limit the number of programming/configuration software packages needed. Motion, I/O, machine-vision, machine safety and HMIs should all integrate cohesively. Plus, Inventek did not want to be left to learn it all on its own, and it needed the learning curve to be as short as possible. The bottom line is that Inventek needed a simpler way of integrating everything together.
The team at Valin came up with an effective solution for the integrators at Inventek. First, it suggested utilizing the Omron NX1P, a modernized PLC/machine automation controller that has Ethernet, Ethernet/IP and EtherCAT built into it. This alone would make development easier because, in the past, Inventek would need three different software programs to deploy the motion, industrial networking (Ethernet/IP and EtherCAT) and HMI. It had been a very cumbersome process. However, with the new platform, Inventek could use updated software for everything in a fully integrated development environment, Sysmac Studio. The improved software allowed Inventek to create variables (tags) and use the same tags in the PLC and HMI as opposed to making a new tag for each device, like in the older system. Sysmac Studio program/configuration software made building the EtherCAT network of Omron I/O, motion and machine safety devices much easier than controllers it had used in the past. With this control solution, stepper motors, servo motors, machine-vision systems, robots, I/O and bar code readers could all communicate with the NX machine automation controller (MAC) using the EtherCAT and Ethernet/IP networks, as well as multiple serial communications interfaces.
The final piece of most automation controls puzzles is data logging. The NX MAC allows the option to log process and operation data to an SD card or to act as an FTP server or FTP client so that log and history data can be transferred as needed.
The Inventek team was brought up to speed and trained on the new control platform, as well as on updated HMI and Sysmac Studio software. In addition, an MB Connect Line secure router would be used to provide secure remote access to all the controls in the system.
This led to savings both in terms of initial cost and engineering efforts on Inventek’s part. The new hardware and software, combined with Valin’s ability to provide training and bring them up to speed, saved Inventek significant software development and installation time. In addition, Inventek gained experience using a controller that had the flexibility to meet all current, plus future application requirements.
ALSO READ: A very short history of PLC programming platforms
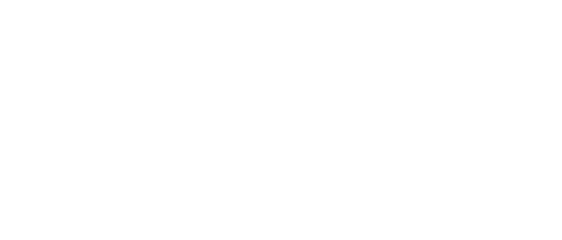
Leaders relevant to this article: