Two companies that have a strong presence in the packaging industry, EIS Automation in Las Vegas, Nevada, and Packaging Made Easy in Chino, California, partnered to engineer a modular horizontal flow wrapping machine that adds value to packaging operations while being well-positioned to provide manufacturing advantages in the future.
Omron became involved in the development process through an existing partnership with EIS Automation. Based on the project goals, Omron engineers worked side-by-side with both companies to incorporate several solutions that would give end users more control over their machines. Along with a customized human-machine-interface (HMI) screen that promotes maximum flexibility and ease of operability, Omron also provided the technology behind an initiative to let end users seamlessly add functionality to the core machine as operations change in response to market demands.
Figure 2: Designed to be modular, the Athena-S3 promotes a multi-step approach for improving the entire packaging process.
Packaging Made Easy, which serves the pharmaceutical, medical-device, food-and-beverage, cosmetics and confectionary and many other industries, has seen success with the launch of the Athena-S3, a fit-for-the-future, modular flow wrapping machine (Figure 1). The company is also promoting a multi-step plan for improving an entire packaging process in which new functionality can be seamlessly added without replacing the core machine (Figure 2). This process includes, among other things:
- incorporating automation on the feeding side
- adding a collaborative robot for casing at the end of the line
- a complete, end-to-end traceability system
- automated quality control subsystems.
Background
EIS Automation, an automated packaging system integrator that covers a wide variety of packaging automation needs, entered into a strategic partnership with Packaging Made Easy, an OEM specializing in horizontal flow wrappers and other packaging process innovations, to address an unfulfilled need in the market (Figure 3). The two companies began working together to develop a scalable, modular flow wrapping machine that would stand the test of time and be fully adaptable to changes based on market demands.
Figure 3: Product is transferred from the conveyor into the plow fold section where the film wraps a bundle of sage.
During their own market research, the companies were able to pinpoint a disconnect between how most processing and packaging companies envisioned a future-ready machine versus what features were actually available on machines ready for purchase. They were often contending with end users who would sometimes procure a machine based on price and find that it would not meet their preconceived needs for functionality.
At the same time, those machines would only work for a short period of time or would require frequent repairs that were difficult to accomplish.
Finally, with a great many of those machines being shipped from out-of-pocket outlets or even from a refurbished source, finding local support from the OEM also proved to be difficult. Tackling these challenges head-on, EIS Automation and Packaging Made Easy developed the Athena-S3 Horizontal Flow Wrapper, a user-friendly machine requiring little to no training and for which support would be readily available across North America.
The advantage of a solid service-and-support network is processors and packagers can be tempted by a low price. Unfortunately, initial savings are often outweighed by the costs of maintaining and repairing machines in the future. When a machine isn’t serviceable by an OEM, it may mean that it was acquired through a third party and not registered to the procuring company. A myriad of problems can follow, ranging from difficulty obtaining spare parts to confusion over who is responsible for general and emergency service and support.
On top of these mounting issues, price-effective machines can be island solutions, or static machines that are neither scalable nor modular in nature. These types of machines make it difficult to integrate additional automation modules, such as robotics and machine vision, after purchase.
EIS Automation and Packaging Made Easy maintain the design and build of the Athena-S3 and have a solid network of authorized service and support professionals located throughout regional markets. And with their flow wrapping machine being automated by Omron, both companies have access to an additional layer of product support and application assistance through Omron support specialists.
Challenge
Prior to working with Omron, Packaging Made Easy sourced machines from various OEMs.
These machines functioned well and performed as the OEM intended, but they usually required a significant amount of engineering hours for modifying mechanical and electrical components to satisfy the goal of offering their end users a scalable and modular machine that could readily adapt to future market changes. This lack of control over the guts of the received machines made it much more difficult to customize solutions that fully covered their desired offering.
Packaging Made Easy also found that the received machines were often equipped with automation technologies from multiple vendors, which made control of the entire machine more challenging.
For example, at times, certain control technologies would have trouble communicating with a different brand of servo motor. And oftentimes other controllers were limited in their capabilities to control other manufacturers’ components.
Most aspects of the original application would need improvements, including the motion, controls and HMI integration. Due to these challenges, Packaging Made Easy started looking for a new hardware solution, as well as a new platform that would provide easy troubleshooting and simple remote connectivity. It challenged EIS Automation to help the company design and build a custom machine with integrated control and components that would work seamlessly together without incurring a high number of engineering hours.
Solution
The partners chose to power their machines with the Omron NX1P2 programmable logic controller (PLC). It runs on EtherCAT and is compliant to IEC 61131-3, a vendor-independent, programming-language standard for industrial automation.
“The NX1P2 model we selected has coordinated motion capability for up to four servo axes over EtherCAT, which was a great fit for the three-axis requirement of the FlowWrapper,” says Josh Watson, managing member EIS Automation.
Coupled with the NX1P2, the partners chose the award-winning 1S series of servos for motion control, the NA Series HMI for quick activation of add-on functionalities, and the NX-TS I/O for bag sealing, according to ASTM standards.
“Our plan is to export the Athena FlowWrap in the near future, and we needed a controls component provider that offers a standardized component platform with a global presence and support,” says Watson. “Serviceability and using components from one manufacturer for easy integration without compatibility issues was a very important decision-making factor, as well.”
The Omron 1S Series is a servo system designed to optimize the full cycle throughout machine design, installation, commissioning and maintenance (Figure 4). Offering a high-resolution multi-turn encoder without battery backup, a built-in safety network and improved loop control, the 1S supports higher levels of machine productivity with exceptional accuracy.
Figure 4: The servo system assures precise positioning, smooth acceleration and deceleration for perfectly sealed packs.
Features include:
- power range from 100 W to 3 kW, 100/200/400 V
- 23-bit high-resolution encoder
- 350% momentary maximum torque (200 V, 750 W max)
- fast, secure screw-less push-in control I/O connector and brake interlock connector
- pluggable connectors in all connectors for easy pre-wiring and system maintenance
- direct wiring of I/O signals to eliminate the need for terminal block units.
“We investigated two other motion control platforms but eventually decided to standardize on the Omron platform due to the wide offering of controls products and expandability with our modular design approach,” explains Watson.
Programming in Sysmac Studio, the advanced automation platform from Omron, proved to be an intuitive and efficient way to then communicate with the PLC, which then sends packets of data
to the individual components on the EtherCAT network. Both EIS Automation and Packaging Made Easy saved time designing the initial architecture of the robust network that makes the Athena-S3 Horizontal Flow Wrapper scalable for the future.
“From the beginning, our goal was to design a scalable platform that has a modular approach at its core,” explains Watson. “This will allow customers to grow the platform with their operation. Starting out with just the FlowWrap, once volume increases, we can easily add an end-of-line pick-and-place solution, machine-vision quality control or ID and traceability (Figure 5).”
Figure 5: This add-on, end-of-line modular solution using the Omron collaborative robot provides automated pick-and-place of primary packaging into cases for distribution.
Other special features include custom HMI screens with intuitive navigation and embedded troubleshooting, an easy-to-activate energy savings mode, automatic bag size calculation functionality and a remote servicing module that allows for quick support via VPN whenever necessary.
“The remote service module is integrated into every machine as a standard,” explains Watson. “The main reasons are the ability to help customers to troubleshoot remotely by logging directly into the control system of the machine. The second important aspect is the ability to download new software revisions/updates to the machine remotely. In order for us to do this the customer doesn’t need a laptop and/or any software; just plug the network cable into any network port with Internet connection in the plant, and we will be able to help via secure VPN tunnel.”
Omron engineers worked with both partners to make this machine a great fit for processing and packaging companies that are looking
toward tomorrow.
Results
The Athena-S3 Horizontal Flow Wrapper has already seen plenty of success with its recent launch into the market. Packaging Made Easy has recorded a 124% increase in sales and expects demand to continue to grow with processing and packaging companies’ increased investment in automation. Omron controls, motion and industrial components can be recognized in every Athena-S3 that comes out of the production facility, thanks to its ability to enable a wide range of features that add value for manufacturers in the packaging sector looking to find machines that can be modified as the market changes.
Figure 6: Integrated at end-of-line, the Omron collaborative robot places packs onto another conveyor for casing, automating the entire packaging process.
Packaging Made Easy is also promoting its multi-step plan for improving an entire packaging process, which involves providing the ability to seamlessly add new functionalities without replacing the core machine. This involves the development of an end-of-line modular solution using the Omron series collaborative robot for automated pick-and-place of secondary packaging (Figure 6). This module will also be scalable, allowing end users to incorporate add-ons as demands shift within the industry, also making it truly fit for the future.
ALSO READ: PLC vs. Arduino for industrial control
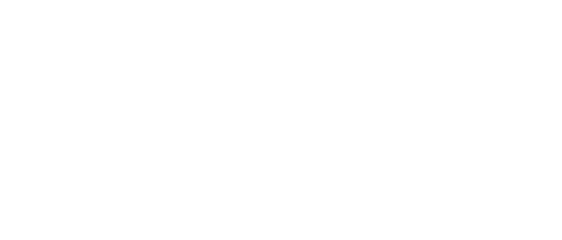
Leaders relevant to this article: