Complexity
Figure 1: As connectivity and automation become more widely adopted, marshalling of electrical signals is becoming increasingly complex.
Marshalling is a critical process in industrial plants. It brings order to thousands of electrical signals on which connectivity and automation rely and can be defined by the grouping of inputs and outputs (I/O). Marshalling enables diverse operating systems to interact, and it encompasses a wide range of requirements, including intrinsic safety (IS) isolation, signal conditioning, relay interfaces, surge protection and cable terminations, often including loop disconnects.
As connectivity and automation become more prolific, the increased use of fieldbuses and smart devices in large and complex industrial processes means that the numbers of electrical signals connecting field instruments and a plant’s distributed control system (DCS) are multiplying, making design increasingly complex (Figure 1). The DCS architecture around plants has resulted in more efficient ways to improve reliability of control, process quality and plant efficiency; however, the design, documentation, installation of I/O and marshalling in distributed control systems can be a labor-intensive and lengthy process.
Indeed, this process has barely changed since distributed control systems were first introduced in the 1970s. As a result, marshaling, with its disparate systems and hardwired connections, is a neglected area of system design. With OEMs often specializing in individual aspects of marshalling, it has lacked an overall vision for future development to enable it to keep pace with the challenges of modern production environments. So, how can traditional marshalling be transformed into something that is fit for purpose?
Marshalling challenges
Traditionally marshalling may involve up to five separate cabinets, one for each of the different marshalling functions, with complex wiring between the marshalling components. Interconnection is a key concern. Historically, marshalling solutions require up to eight interconnections per channel. However, this creates a complex wiring structure and is a major source of faults and downtime. Faults commonly arise from simple wiring errors or connection failures within cabinets, and they are not easy to trace. Eliminating the interconnecting wires would significantly increase uptime.
A typical design process makes specification at the outset difficult. It can be a real challenge for design engineers to know what exact requirements an industrial plant may need in a few years’ time as a facility grows and projects evolve. This is particularly true for surge protection. Therefore, flexibility is paramount to prevent delays from changes and associated cost increases in project specification.
Another major source of concern is multiple components from multiple suppliers. A traditional marshalling solution with IS typically involves 20 different component types. During later design stages, the component type often needs to be amended, which results in changes to the bill of materials that are long and complex. Additionally, late changes make it difficult for end users to maintain the marshalling system and control lifetime costs.
Space requirements are a further challenge and marshalling systems can become increasingly unwieldy as further cabinets are added in response to post-installation changes. To save space, some sites are remote-mounting DCS I/O in field enclosures. While this option may deliver substantial capital cost savings, it still requires I/O and marshalling components that are suitable for lifetime operation in harsh and sometimes hazardous areas.
[javascriptSnippet ]
Another approach
[pullquote]It is clear that there is a need for a new marshalling solution: one that facilitates a standard design for all marshalling requirements. A modular approach could enable all five key marshalling requirements to be achieved using a single cabinet design. This would deliver a system that is compact and space-saving, while at the same time is simple to install and maintain. Furthermore, a modular universal marshalling solution would be easier to reconfigure and so have minimal impact on project and whole life cost. Let us examine the implications in more detail:
Fault elimination —With all the marshalling functions in one unit, there is no longer any requirement for complex, hardwired interconnections. The modular design therefore eliminates the risk and associated costs that arise from wiring faults.
Future-proofing—The configurable design accommodates late changes. This reduces risk during project execution as modules can be reconfigured easily or added as necessary at any point during the build. For example, the surge protection module can be added as and when it is required on completion of the surge risk analysis, which is usually carried out during the detailed engineering stage. This is a major benefit because it enables plant managers to save initial costs where surge requirements are not known. It also ensures that the system is adaptable over time, capable of responding to changes in production requirements without major rewiring or the introduction of bolt-on equipment.
Component reduction—Universal marshalling typically reduces the number of marshalling components, which makes things much simpler from the outset. The benefits really stack up when considering any changes to specification as the project progresses. For example, on a project with about 4,500 I/O, small changes in the number of each I/O type results in the bill of materials for the traditional solution requiring 4,651 changes. The bill of materials for the same project could require only 115 changes using a modular approach.
Ease of maintenance—Often, if components are made smaller, they can be trickier to install and maintain: but the opposite is true with universal marshaling using a plug-and-play approach (Figure 2). Fewer component types mean fewer spare parts are required to be held in stock. Comprehensive diagnostics are an integral feature, notifying the process managers when action is required. LED indicators for power, function and status simplify commissioning and troubleshooting. The configuration information is held in the terminal, so a module can be changed out without the need for reprogramming.
Figure 2: Plug-and-play configurable modules eliminate the need for intricate wiring.
Saving space—The modular design approach eliminates some components altogether, as well as enabling components to become more compact, so there is typically a reduction in the number of marshalling cabinets required. The universal marshalling components can be mounted in two or three columns in each side of a standard cabinet. This delivers the highest packing density of 512 or 768 I/O channels per double-sided cabinet. This high density reduces the number of cabinets required, which delivers savings on cabinet hardware, installation and weight. Each cabinet typically weighs around 270 kg, so any reduction in weight has significant advantages for offshore applications. There is also potential to reduce the overall size of control rooms.
Table 1: End users can realized ongoing operating costs for a typical project with 6,000 I/O channels.
End User operating costs |
Traditional |
MTL SUM5 |
Control room air conditioning |
$ 69,638 |
$ 21,762 |
Training costs |
$ 185,760 |
$ 61,920 |
Lifetime documentation |
$ 165,120 |
$ 32,250 |
Inspection costs |
$ 134,721 |
$ 60,842 |
Component maintenance and stocking |
$ 360,000 |
$ 150,000 |
End user operating costs |
$ 915,239 |
$ 326,774 |
|
|
|
|
End user operating savings |
$ 588,466 |
|
% saving |
64% |
Reducing operating costs
Table 1 demonstrates typical operational savings of 64% can be made using universal marshalling compared with a traditional solution. Calculations include the ongoing operational costs of marshalling systems for the end user, such as personnel training, documentation and maintenance. The simplified nature of universal marshalling means each of these associated activities is less onerous.
It is therefore clear that many industries would benefit from the development of a universal marshalling design solution.
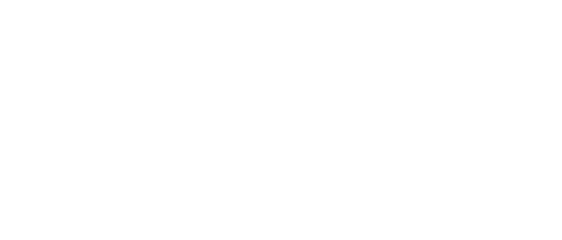
Leaders relevant to this article: