Case Study: Field logic controller solves a clean-in-place application
Figure 1: A common feature of all dairies is the milk parlor; cleaning the equipment is a critical process.
When a dairy has an issue with an intermittent controller, it can cause imbalanced chemical application during the backflush period of its process. When one of our customers found itself in this situation, we decided to replace the failed controller with Turck’s TBEN field logic controller (FLC) to get the dairy’s backflush-cleaning process back on-line (Figure 1). The controller includes ARGEE software and pushes reliable control to the edge devices by adding logic to compatible I/O blocks without a PLC.
The FLC concept is every bit as revolutionary as IO-Link. Turck took what was once just a discrete I/O distribution block and gave it a brain—the ability to solve logic and make decisions. Giving a dumb edge device the ability to solve logic and communicate with other devices is an up-and-coming trend. This is an important step on the path to the Industrial Internet of Things (IIoT).
Our goal was to open our doors as an industrial distributor and get back on the road, knocking on doors with a boots-on-the-ground mentality. Doing that, we always asked a question to our customers: What do you need fixed? The customer wasn't used to that.
They started telling us their problems, and we used our knowledge to come up with solutions to help them to fix their problems. It turned into the customer asking us to help them specify the hardware and then asking us to design it and so on. We slowly turned into a value-added distributor. From there, we developed some of our own products and became an integrator.
Our specialties are in dairies and breweries. It's how we got started in our integration business. A lot of the automation in dairies is also found in breweries. There are many similarities in keeping the milk cool or the beer cool.
Don't irritate the cows
In this application, we worked with DeLaval Direct, a dairy service provider in Jerome, Idaho, and Glanbia Foods, which supplies raw milk product to Glanbia’s three processing operations located near Twin Falls, Idaho. It was a team effort to correct the backflush problem.
Also read: Remote I/O becomes smaller, faster, customizable and intelligent
The backflush process is a critical element in every dairy operation. The pipes that transport the milk from the vats to the siloes go through a clean-in-place (CIP) process to clean the pipes of any old milk for sanitary reasons. During CIP, several flushes of water, air and chemical cleaner run through the pipes and udder assemblies.
To avoid contamination of the milk, irritation to the cow and potential bacterial infection, the control sequence must be correct, allowing the proper amount of cleaning agent to flow through the assembly for the required amount of time. Run time is critical to a successful cleaning process. The control sequence must also ensure the proper amount of water and air is used to remove the cleaning chemicals.
Depending on the size of the dairy, you can typically milk from 16 to 170 cows. Each dairy has a similar process—when the cows are done being milked, the operators in the dairy switch the controls from "cows-to-vat milk collection" to the cleaning process. With the backflush controller working intermittently, the cows were irritated, so the dairy needed it fixed right away.
A smarter edge
One of the things that brought the Turck TBEN field logic controller into play is the dairy needed something that had the brains of a PLC, was small and compact and was very robust. The dairy environment is very harsh. Turck's FLC design includes an IP69K rating, which is very high, and it is washdown capable with an extended temperature range (Figure 2).
Figure 2: The field logic controller is at home in a control enclosure or out in a harsh environment.
Something that makes the TBEN field logic controller unique is that it isn’t just a digital block-I/O module; it has a brain—hence the field logic controller name. It has the appearance of a standard field-mountable I/O distribution block. Turck added a controller and added the ARGEE program to it, turning it into a small, rugged PLC.
With ARGEE software, a small program was written in a structured text type of program by Turck. A single FLC I/O block was added with eight configurable inputs and outputs. This single block solved the dairy's problem.
Although the Turck FLC uses multiprotocol technology, which is basically Ethernet gateways for Profinet, Modbus TCP or EtherNet/IP, simple digital I/O was used to interface to the dairy's main controller. A button press on the main PLC's HMI digitally triggered the cleaning process in the FLC. The field logic controller controlled the pumps and valves using digital outputs and a digital output notified the main PLC when the cleaning process was complete.
In a few hours, the dairy told us what it needed over the phone. We understood the process, which included a number of timed cycles and counters. Chemicals, water and air all needed to flow in the proper sequence, for a period of time and the correct number of cycles.
The customer defined the sequence and Landmark wrote the program, assigned the I/O and worked with and trained the installation team. With quick-disconnect cable connection to the FLC, the installation was completed quickly. In a couple hours it was done and the backflush cleaning of the milking parlor was operational.
A little program and training
The ARGEE program is a big benefit in the FLC. You start programming ARGEE by using a flowchart, which resembles ladder logic. It's simple to understand and learn. Once the flowchart/ladder logic-like program is accepted, it is converted to a structured text format such as AND, OR, IF, THEN.
It was made even simpler by providing dropdown menus in the appropriate locations of the logic, which are helpful hints to flow the program together. This simplifies the ladder logic further. If a program can be accomplished via this flowchart, it keeps things straightforward for any user.
ARGEE keeps the visual feel of ladder logic and adds dropdown boxes across the ladder rung. More complex functions are typically added once the structured text program is automatically created keeping all levels of programmers happy.
The ARGEE programming environment is accessed using an HTML5-compatible Web browser, which eliminates the need for complex third-party software or licensing.
The software is already in the field logic controller, and it's free. To access the ARGEE software, a Google Chrome browser is used to log on. No need for Internet, just the Chrome browser, which it is designed for, but other HTML5-compatible Web browsers will work.
The TBEN field logic controller has really been refined over the past few years. The ARGEE program is getting easier and flashing the program to the FLC is simple and reliable. It's easy to activate and update the firmware in the device, so future improvements will be available. No special software is needed, as it is just a simple link sent via Dropbox.
A smarter edge
The FLC provides a great way to add logic at the edge without investing in a PLC or installing a fragile smart relay in an enclosure. The FLC can operate stand-alone and out in the open, without a need to communicate with a PLC. It can also monitor a machine or edge sensors and interface with a PLC where needed.
We have also used this FLC to add I/O to existing PLCs in other applications. We did this in a mobile cart application where the PLC had only one spare input available. However, to operate properly, there were six sensors that had to be monitored and decisions made based on the sensor’s state and functions being performed. More I/O was needed and program logic was required to monitor the sensors before turning on the output to the existing PLC. With the field logic controller, it was easy to add extra I/O and a little logic to applications that didn't have the spare space.
These TBEN field logic controller blocks also work well in agriculture applications, especially on farming equipment. People who may currently be using smart relays for control applications often have problems if just a little vibration, water, mud, dirt or dust is added to the control panel. With the TBEN FLC and its IP69K rating, environmental conditions are not an issue. It's nearly immune to shock, vibration and the elements, which makes it a great replacement to the fragile smart relay, and it doesn't need to be placed in a enclosure to do it.
For this dairy application, the following morning after installation, veterinary samples showed that the critical metrics were accurate and working well, and the dairy received perfect marks for cow health.
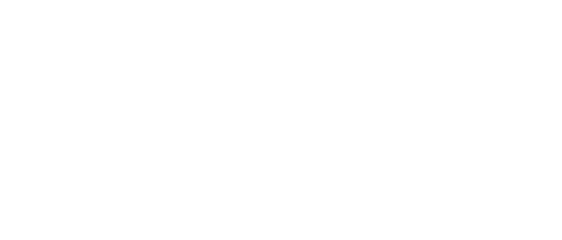
Leaders relevant to this article: