Beckhoff USA hired Paxton Shantz to serve as digital manufacturing industry manager. Shantz will use his extensive automation and fabrication experience to direct Beckhoff sales and support efforts for manufacturers and machine builders in forming, welding, cutting, additive manufacturing and many other applications across the United States.
Before joining Beckhoff, Shantz worked as west regional manager for Lenze Americas, leading technical teams throughout the western United States, Mexico and Canada. Based in Greater Los Angeles, he has also held regional sales management positions at B&R Industrial Automation and Advanced Motion Controls. He started his career at Delta Tau Data Systems, now owned by Omron, as an application engineer and eventually engineering manager.
“Paxton Shantz is a renowned automation industry leader with experience in machine tools and fabrication and a track record of success with large machine builder OEMs and end users,” says Kevin Barker, president of Beckhoff Automation. “The comprehensive Beckhoff portfolio, including powerful PC-based control hardware and TwinCAT software for CNC, robotics and many other industry-specific functions, has helped us continually increase market share with leading companies in the fabrication industries. We are excited to harness Paxton’s skills and understanding of the market’s trajectory with new IoT, motion and machine control solutions as a new industry manager at Beckhoff.”
Shantz earned a bachelor of science in mechanical engineering from California State University, Northridge.
Shantz answered a 7 questions about automation technology’s future.
What are three key things that a machine builder, system integrator or manufacturer should know about your company?
Paxton Shantz, digital manufacturing industry manager, Beckhoff Automation: First, they should all know Beckhoff is a global automation provider that has a proven track record of providing market-leading control platforms. These solutions greatly simplify the machine hardware and software requirements while simultaneously providing unmatched flexibility and performance. This holds true for wide-ranging fabrication applications, as well as machines and systems across many other industries.
Second, we are committed to working closely with our customers and partners to ensure their projects are successful. From the beginning, Beckhoff has made collaboration a top priority as evidenced by representation in more than 75 countries, a deep pool of application engineers, free technical support and our Beckhoff Integrator Group (BIG) in the United States. Also, Beckhoff has accomplished double-digit global revenue growth on average for the past 20 years. In addition to expert technical support and sales consultation from skilled engineers, we also design, develop and manufacture our products in Germany. This means we are 100% in control of our short lead teams, production, excellent quality and lengthy product lifecycle.
Third, the Beckhoff control platform provides the most highly integrated machine control platform available on the market today. Having grown from supplying PC-based automation and I/O terminal systems, Beckhoff now offers a completely integrated, backward-compatible control system that delivers unmatched computing power, open communications, I/O processing capability, programming flexibility, functional machine safety, HMI and much more. The platform readily scales from simple to complex, ensuring the best price-to-performance ratio according to each machine’s requirements, including for CNC, robotics and other complex systems.
What new technologies are driving your product development and why?
Paxton Shantz, digital manufacturing industry manager, Beckhoff Automation: The new technologies provided by Beckhoff center around ease of connectivity, performance and cost savings. In addition to being well-suited for IIoT and Industry 4.0 concepts, we have expanded our view to the entire control system’s connectivity to eliminate unneeded hardware, wiring, software, license fees and communication delays. Also, in terms of performance, our motion control has been a market leader for more than a decade. Our goal is to provide a platform that has no challenges with third-party software, fieldbus communications, robotics integration, testing and diagnostics. The primary technologies pushing us forward are advancements in PC chipsets for greater processing power and memory, remote connectivity (IIoT security and analytics), software and control algorithms (especially involving kinematics and adaptive motion control), among others.
How does the Industrial Internet of Things figure in your business strategy?
Paxton Shantz, digital manufacturing industry manager, Beckhoff Automation: Relative to the fabrication industry, Beckhoff continues to develop easy-to-integrate IIoT solutions, which begin with local data collection, pre-processing, data transmission and data analytics. We remain at the forefront of cloud computing in industrial applications, and we plan to keep leading the market with robust edge controllers, remote diagnostics, integrated machine learning, automatic code generation, digital twins and more. All the while, we will offer an easy-to-configure IIoT package that supports everything from a single-cell machine or fleet of machines up to end user plant management.
How will machine automation and controls alter the way companies staff their operations in the future?
Paxton Shantz, digital manufacturing industry manager, Beckhoff Automation: The most attractive aspect of automation and controls is the high degree of efficiency it provides. When coupled with innovation, companies will require staffing that is very similar to today but weighted more towards development and implementation and less on execution. As Industry 4.0 concepts become the norm, products and services of the future will be much more tailored and personalized than they are today. The companies staffed to continuously meet these demands will do well, while those staffed to for the more traditional static production will fail.
How is the development of software solutions impacting your requirements for hardware?
Paxton Shantz, digital manufacturing industry manager, Beckhoff Automation: Because the Beckhoff automation platform has always consisted of a well-balanced mix of PC and deterministic control technology, we easily integrate new software solutions with no impact on our hardware requirements. For example, it is 100% seamless for us to integrate any OEM-developed or end user software, such as ERP systems, schedulers, CAD/CAM tools or nesting software to custom PID algorithms.
The key to this ability is our TwinCAT automation software. It was originally developed in 1996 and has now grown to TwinCAT 3. In short, this software provides flexible runtimes and a universal engineering environment, which is also integrated into Visual Studio, to meet any programming and configuration requirements. Beyond supporting all NC, NC PTP, CNC and robotics control requirements, TwinCAT 3 enables programming in PLC languages and computer science standards, including IEC 61131-3 and its object-orientated extensions, C/C++, predefined or proprietary function blocks and links to MATLAB/Simulink. Communication to higher-level systems can take place via OPC UA, MQTT, AMQP, SMS/SMTP, FTP, TCP/UDP, XML Server and so on.
As engineering and IT continue their convergence, which one is and/or will be leading the direction of future automation and technology at your organization?
Paxton Shantz, digital manufacturing industry manager, Beckhoff Automation: Without a doubt, integration of IIoT technology is leading the way for our future automation development. However, instead of a traditional approach focused primarily on managing the data, we start at the component level. This means reducing the number of different software components, hardware components and termination points by increasing the intelligence and capability of each part in the system.
A good example of this is our ability to fully automate and control a CNC laser cutter, its material handling system and the necessary safety from a single machine controller.
Unlike other systems, there is no need for additional black boxes, switches, a stand-alone safety PLC, multiple networks with excessive cabling and multiple software packages with the associated license management. This cuts costs as well as complexity. Just as important, each remaining component leverages EtherCAT and TwinCAT to provide all of the information needed to diagnose precisely where a fault or failure has occurred and a log to help determine why. When combined with data analytics, the goal is to guarantee uptime and eliminate inefficiencies with scheduled maintenance and unplanned downtime.
Looking into the future, how will technology change your company over the next five years?
Paxton Shantz, digital manufacturing industry manager, Beckhoff Automation: Technology advances, coupled with the COVID-19 pandemic, are already accelerating the demand for automation systems that are much easier to commission and operate than machines of the past. Over the next five years, we are going to stay the course with component reduction, while focusing heavily on enhanced software capabilities for machines to self-configure and self-diagnose.
IIoT data gathering, analytics and easy-to-commission hardware, software and dashboards are already available today. The focus for tomorrow is providing machine builders with the full power and openness of PC-based control. This will support an integrated automation system that is unmatched in terms of investment security, safety, interconnectivity, information transparency, technical assistance and performance.
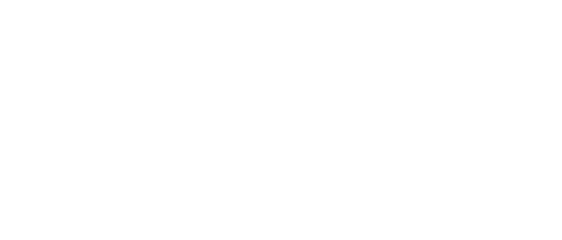
Leaders relevant to this article: