Artificial intelligence (AI) is taking the world by storm. According to a 2018 report published by Marketsandmarkets research, the AI market will grow to $190 billion by 2025. Companies large and small across a range of industries are investing in this technology as a way of improving the customer experience. In the automotive industry, AI is being used to create the world’s first fleet of fully autonomous cars. It’s also changing the way we think about driver assistance, predictive maintenance and accident prevention.
But these innovations extend to the warehouse, as well. Automotive manufacturers are using AI to increase operational efficiency, reduce labor costs and improve customer and business relations. AI is moving beyond self-driving cars to revolutionize the automotive industry.
Predictive maintenance
[pullquote]Automotive manufacturers are looking to simplify the maintenance process as much as possible. Every time a machine needs to be repaired, it means halting the line of production. That’s why more companies are switching to predictive maintenance (PdM). Instead of waiting for a machine to break down, the company will use artificial intelligence to monitor the performance of the equipment. AI will then notify managers and maintenance personnel when the machine needs to be repaired based on its recent performance, warranty information and machine learning.
This allows managers to be more selective in terms of when and how often these machines need to be repaired, thus minimizing any disruptions to means of production. Ideally, these machines will be inspected and repaired before problems occur. Every repair can be scheduled to a T, so the manufacturing process can resume without delay. While the use of predictive maintenance is on the rise, most companies still prefer preventive maintenance, which means fixing the machine proactively without the help of AI.
Automated guided vehicles
Self-driving vehicles aren’t just for the road. Manufacturers are using automated guided vehicles (AGVs) to speed up the production timeline. These sophisticated machines use sensors to navigate their surroundings in the warehouse. They are often used to retrieve items in a facility, so human workers can stay focused on the task at hand. Small crafts will roam the aisles of the warehouse, adjusting their height to grab items from the shelf. If they encounter an object or obstacle, the craft will find an alternative route so it can hand off the item in question as soon as possible.
Facility managers will program these devices with an established route. This creates a network of AGVs, each responsible for retrieving different items. AGVs simplify the product retrieval process. Employees can spend more time and energy looking at the bigger picture instead of sorting through similar parts and accessories on the shelf.
Retrieval times tend to vary by a few seconds or more, disrupting the means of production. AGVs regulate this process so that managers know exactly how long it will take to complete each task.
Employee guidance in the workplace
Robots have long been a part of the manufacturing process, but there’s always a role for humans to play. Human workers are still responsible for last-minute touches and quality assurance. But repetitive tasks can take a toll on the health and safety of these workers.
Automotive manufacturers are turning to AI-powered devices and bodysuits as a way of improving employee safety. The still-in-progress Hyundai Vest Exoskeleton (H-VEX) fits around the arms and legs of the worker to guide them through the manufacturing process. The machine is designed to reduce pressure on the neck and arms, meaning workers can move more easily through the factory floor and reduce the chances of sprains, muscle aches and other common workplace injuries.
The H-VEX can also reduce fatigue, so workers can make the most of their time on the floor. More companies will likely leverage this technology in the months and years to come. One bodysuit could save the company thousands of dollars in labor, related injuries and insurance.
Smart manufacturing
We know self-driving cars will use machine learning to better their performance on the road, but this same idea applies to the inner workings of the warehouse, as well. Facilities can generate hundreds of gigabytes of data every day. Companies just have to know how to use it.
With intelligent systems in the automotive industry, managers can collect data on every aspect of their operations, such as product retrieval, energy usage and time to completion for existing models. AI-powered software will then help them to glean insights from this information, namely tips for improving efficiency, reducing unforeseen errors and improving workplace safety.
Employees scan items and vehicle models as they move through the supply chain, so managers can track their completion in real time. This keeps them abreast of the latest situation. That way, they can keep their business partners, dealerships and vendors in the loop. If a product or shipment is delayed, they can take steps to remedy the situation in real time.
Managers can use this information to improve the existing supply chain, including everything from delivery routes to storage equipment. A small change, such as switching to plastic pallets, could make all the difference when it comes to shipping and transportation. Companies can also use this data to improve their handling of hazardous materials, including implementing new storage and transportation tactics that can improve worker safety. Intermediate-bulk-container (IBC) totes are one choice when it comes to handling industrial solvents and chemicals. They can also be used to store large quantities of automotive parts.
The future of automotive manufacturing will focus on big data, which means having a robust data storage platform. We should see more companies investing in cloud AI-powered services as a way of streamlining the data sharing process.
For many automotive manufacturers, the future is already here. The first step is learning how to increase a warehouse’s order-fulfillment efficiency, so you can capitalize on these trends before they reach the mainstream.
ALSO READ: AI models and the IIoT close the loop and optimize manufacturing
David Madden is a director at Container Exchanger.
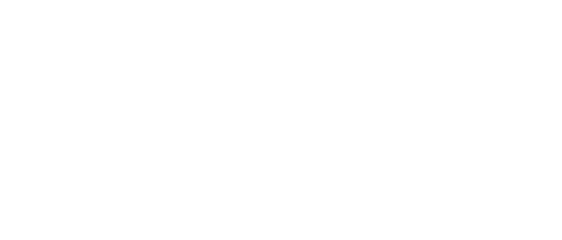
Leaders relevant to this article: