A tool that picks, orients and places a part is common in machine automation. However, when it's part of a wind-farm installation located offshore, it's a rather complex and impressive piece of equipment (Figure 1).
Our company, Houlder, was tasked to develop a reliable, fast and safe system to lift massive wind-turbine steel-foundation monopiles. Each monopile, a cylindrical steel tube support structure, weighs 855 tons and must be lifted from a horizontal position on the deck of the installation vessel to a vertical orientation at the target installation position in preparation for pile-driving it into the seabed.
Our solution required designing a wirelessly controlled crane attachment using National Instruments’ CompactRIO and LabView. The crane attachment automatically engages a monopile, upends it, securely suspends it and helps precisely position it. Once the pile is in position and restrained, the attachment is remotely disconnected from the monopile and parks to recharge the power units. Using CompactRIO and LabView for the pile-upending tool allowed us to rapidly and cost effectively develop a control system that we can easily update and improve for use on future wind-farm projects.
Figure 1: The system includes a tool to clamp to and rotate the pile (right), connected to the end of a large industrial crane with the gripper arm attached to the side of the vessel.
(Source: Houlder/National Instruments)
Houlder’s marine equipment business is located in Tyne and Wear, England. The company is an independent, employee-owned provider of design and engineering services, as well as equipment used in a wide range of marine markets including offshore renewables, oil and gas, defense and liquefied natural gas. The company delivers turnkey solutions to engineering challenges in all these sectors. Our engineers, naval architects, designers and project managers do more than offer their expertise to the market. They combine forces to bring clarity to industry challenges and present well-considered solutions. They balance their intellect, experience and practical knowledge.
Background breakdown
The offshore wind farm project required two pile upending tools for operation onboard the heavy-lift jack-up installation vessels MPI Discovery and Swire Blue Ocean Pacific Orca. The tool lifts monopiles that will be driven into the seabed to act as the foundation for wind turbine generators.
We won the project due to a combination of our experience, innovation in the sector, project success rate and reliability.
Our objective was to improve pile upending operations using a heavy lift crane. We identified a number of engineering challenges to overcome, including:
- controlling the upending tool pivoting and locking cylinders
- powering wireless remote communication between operator and upending tool
- monitoring of upending tool parameters
- overcoming major safety implications in the event of upending tool failure
- delivering an upending tool control system in compliance with both DNV GL rule 2.2, “Lifting appliances,” and EN ISO 13849-2, “Safety of machinery—Safety-related parts of control systems.”
Addressing these issues would result in a faster, more cost-effective, safer and more reliable monopile installation process.
Project packdown
The upending tools comprise many parts, including a crane attachment, flange hook, control cabinet, batteries, hydraulic accumulators, hydraulic reservoir, hydraulic pump, rotating cylinder and locking cylinder (Figure 2).
Figure 2: The self-powered upending tool, clamped to the top-side flange of a monopile, is ready to lift and rotate the pile to a vertical position.
(Source: Houlder/National Instruments)
We developed an upending tool that is self-powered during operations by using absorbent-glass-mat (AGM) batteries for the control system and hydraulic accumulators and a charging pump to provide hydraulic power for the upending tool actuators.
The tool includes two hydraulic actuators: a pivot cylinder and a locking cylinder. The pivot cylinder provides rotation of the tool and locking mechanism. This allows it to engage the horizontally positioned monopile located on the vessel deck. The locking cylinder links mechanically to two locking latches used to lock the upending tool in place on the monopile upper flange.
Once the upending tool engages and is locked to the monopile upper flange, the upending procedure continues. During pile upending, the pivot cylinder goes into float mode so the tool can pivot freely as the pile is lifted from horizontal to vertical. Once the pile is vertical, it is moved to the installation position using a crane where it is restrained using
Houlder’s Pile Gripper Arm integrated into the stern of the vessel. The monopile is then lowered to the seabed, where it is hammered to a final depth.
As the pile upending tool is connected to the end of a large crane, it is linked wirelessly to a controller. Using a handheld device, the operator can remotely retract the latching cylinder to disengage the tool from the pile (Figure 3).
Figure 3: A handheld controller connects to the upending tool's control system via radio.
(Source: Houlder/National Instruments)
Safety first
There are many standards and requirements for certification of a shipboard and offshore crane. This lifting appliance must handle cargo, the monopile, within the vessel while at sea and move it outside the vessel for placement in the seabed.
One certification needed is compliance to DNV GL rule 2.2, “Lifting appliances," and there are many parts, components and systems covered by this standard. Beyond load-carrying structural members and other mechanical components of the lifting appliance, there were many electrical and control parts to comply with. This included power systems for hoisting, brakes and braking systems, safety equipment, protection against fire, control and monitoring systems and electrical installation.
Design examination was a big part of the certification activities. This included strength and suitability of purpose; surveys to confirm compliance with the approved drawings, compliance with regulation and standards; good workmanship and functional testing and load testing.
Compliance with EN ISO 13849-2, “Safety of machinery—Safety-related parts of control systems,” is also a requirement. This standard covers general design principles and validation of safety-related parts of control systems. This includes mechanical, pneumatic, hydraulic and electrical technology. It also describes typical safety functions, required performance levels and validation by analysis and testing of such.
Hardware control
We used the CompactRIO platform to overcome many of the engineering challenges we faced. The CompactRIO system controls the hydraulic valves and the hydraulic power supply. It also monitors the position of the cylinders, accumulator pressure, angle of the tool, reservoir level and battery level. Additionally, the system controls the warning signals and relays the information to the operator through a radio transmitter/receiver module.
The CompactRIO system also helps to implement safety standards. For instance, when there is a communication error in the radio signal, it ensures all the outputs fail safely. Similarly, the system sends a watchdog signal to a safety relay. The tool fails safely in the case of a power outage. The CompactRIO interfaces with the other elements of the upending-tool design, as well.
Early in the design process, we considered several alternative solutions to the CompactRIO. The first solution we considered used relay logic. However, this limited functionality and scope for future development. Alternatively, we reviewed using a programmable logic controller (PLC) or embedded hardware, but they lacked significant advantages compared to developing a solution with LabView and CompactRIO.
We used several configurable and interchangeable modules with the CompactRIO chassis—cRIO-9075—which worked well and can be expanded in the future. These modules included a NI-9425 digital input module, NI-9476 digital output module, NI-9203 analog input module and NI-9263 analog output module.
Modular software design
The LabView development environment significantly improved the design process in many ways. Its modular software design provided seamless integration between software written by multiple developers. Intuitive debugging made it is easier and faster to pinpoint errors when writing the software.
The code is easy to reuse across multiple projects by leveraging subVIs (virtual instruments) and libraries. This will also reduce the engineering time for future projects, and the numerous libraries allow fast and efficient programming by using pre-existing functions.
The drag-and-drop interface and easy-to-make graphical user interface also reduced programming time. Compatibility with other programming languages enabled the developers to program in specialized languages and use LabView to interface them all together.
We used the standard service program from National Instrument to help us to complete online training and reduce training costs. National Instruments also has specialized support engineers to help to resolve any technical issues with hardware or software. We could also simulate the hardware.
In addition to improving the design process, using CompactRIO alongside LabView helped us to add important features to the project that we could otherwise not implement. An important safety feature was to use the CompactRIO field-programmable gate array (FPGA) as a watchdog to monitor the safety relay. We also used the FPGA to generate pulse-width-modulation signals for the locking latch and pivot-cylinder hydraulic control valves to provide smoother system operation.
Through the use of shared variables, we could remotely monitor certain parameters. We also created personalized interfaces for different clearance levels such as operator, service engineer, software engineer and diagnostics checks.
A new iteration
The main advantages of the upending tool, compared to previous solutions, are independence from external power sources and the fact it removes the need for human intervention during connection and disconnection. With no slings or service lines to manage, the connection point can overhang the vessel deck and the overall lifting and upending time can be dramatically reduced. The key benefit of this to installation operations is more efficient and safer use of the vessel’s heavy lift crane.
Once the pile is in place, the tool is returned to the deck, parked and plugged into the its power supply to charge the hydraulic accumulators and battery while the crane is freed to carry out other operations, such as hammering. This solution is simpler to operate and more independent, thanks to the radio control unit replacing signal lines. Using wireless data transfer, however, is less robust than physically connected cables. The CompactRIO ensures that, in the event of a communication error, there are no unexpected failures.
The tools have now installed all 116 monopiles on the wind farm site with no reported downtime, proving the reliability and robustness of the design. The upending tools are now available for use in future wind-farm projects.
ALSO READ: Use distributed control to offload PLCs and PACs
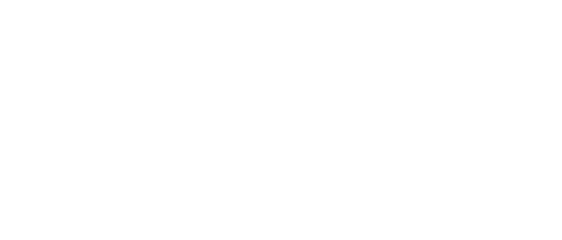
Leaders relevant to this article: