Make the most of cabinet automation
Diversifying consumer needs, labor shortage and other challenges to manufacturing are intensifying. Omron tackles these challenges through three innovations: “Integrated" (control evolution), "Intelligent" (developing intelligence through ICT) and "Interactive" (human-machine collaboration). This is its value-generation concept, Innovative-Automation!
These solutions enable anyone to replicate master craftsmanship and create production lines where machines can continue to learn on their own to understand and assist humans. With more than 200,000 products and on-site support capabilities, this is manufacturing innovation that Omron can deliver.
Omron Automation is an industrial-automation partner that creates, sells and services fully integrated automation solutions that include sensing, control, safety, vision, motion and robotics. Established in 1933 and currently headed by President Yoshihito Yamada, Omron's 30,000 employees help businesses solve problems with creativity in more than 110 countries.
A: Moving components outside of the control panel isn’t a new concept, but advances in component design increased the desirability of doing this. Many new components have LED/LCD screens or visual status indicators that provide a wealth of information for operators and line workers. Having this information readily available in front of you as opposed to being locked away in a panel can be highly beneficial for production. The type of visual information provided by a modern counter or timer will keep operators informed on what’s going on in the production process.
For example, components like timers and counters, if outside of a control cabinet, offer an easy, low-cost interface compared to HMIs and allow operators to change timing, counting and measurement recipes on the fly without having to write new code for a PLC or machine controller, or halt production to open a cabinet to make adjustments. Modern counters and timers are well-designed with an easy programming process that caters to being mounted outside of a control panel.
Panel meters have active functions that are similar to counters/timers, as well as visual indicators that provide important information, so it would make sense to mount a panel meter outside the panel if you need to monitor or interface with it on a regular basis.
From a safety perspective, mounting components outside of a traditional control panel will require extra steps to keep operators and equipment safe. First of all, you need a remote panel-mount box to keep wiring properly isolated away from the environment. Another concern is that most products designed to be mounted inside a control panel do not have IP ratings that would allow for mounting in an open-air environment. Mounting in a remote box will be required for most applications in order to meet safety regulations and protect the equipment.
Ultimately, any product with a display or visual indicator could potentially be mounted outside a panel so operators can keep an eye on the status of equipment. This can include but is not limited to power supplies, power monitoring products and predictive-maintenance equipment. Potentially even relays with visual indicators that may need to be actively monitored by operators.
Q: What steps can be taken to keep cabinet design uniform?
A: Unified dimensions are the cornerstone of Omron’s Value Design for Control Panels concept. When components in your control panel have a unified height, width and depth there’s a multitude of benefits. First, the panel space used is optimized, reducing dead space and helping to condense components horizontally so you can fit more components onto each rail. Data shows that up to 50% of panel space can be saved when compared to traditional components that utilize space less efficiently.
Q: Can you talk about exterior-mounted HMI on the cabinet? How has software changed it, and where is the operator interface headed as it evolves?
A: The improvements made to HMIs have been user-friendly software that allows for improved information on the components you’re interfacing with. Modern HMIs have become highly integrated do-it-all products with some control capability. You can also interface with a PLC, which allows operators to call up different recipes and change the production process quickly to run different customer orders back-to-back with minimal setup and downtime. These newer features allow for greater flexibility and less downtime, which is always welcome in any manufacturing environment. The operator interface is evolving over time to be a more powerful and highly integrated tool in the manufacturing environment. Future HMIs are likely to continue adding new features, logic and control elements, as well as more intuitive user interfaces that provide a wealth of visual information.
Q: As cabinets get smaller, how do you design them to adjust for changing thermal considerations?
A: Improving airflow inside the panel is the key to controlling the temperature of the components in your panel. Fortunately, unified component dimensions offer the benefit of improved airflow. This leads to better thermal dissipation, keeping your components running at optimal temperatures for long-term reliability. Traditionally designed components have varying dimensions that cause turbulence in the airflow through your panel. Turbulence impedes thermal dissipation, leading to inefficient air circulation and hotspots inside the control panel. Heat is the number-one enemy of electronic components. If you allow your components to run at high temperatures for an extended period of time, they will be prone to premature failures, which can cause unexpected downtime in production. Unified component dimensions help to combat this by maintaining adequate airflow throughout the control panel.
Additionally, you can add several axial fans to the panel for an active cooling solution. We’d recommend at least one intake and one exhaust fan per panel; however, panels that have many components generating heat, such as power supplies or solid state relays, may require additional cooling fans. This would be determined on a panel-by-panel basis.
Q: Terminating wires is one of the more time-consuming tasks in panel building. Any recommendations for reducing the wiring and termination time?
A: Push-In Plus technology offers a quick and easy way to terminate wires without the use of tools. You simply insert the bare wire or ferrule into the Push-In Plus terminal, and it clicks into place. Push-In Plus technology uses a spring clamp to hold wires firmly with 125 NM of force (92 ft-lb). This force is greater than a standard screw terminal and can withstand greater levels of heat and vibration without the need for periodic maintenance. Studies show that Push-In Plus wire termination can reduce the total time to wire a control panel by up to 60%, which is a significant labor savings when building a panel.
Q: During shipping, any number of accidents can occur--from dropping a cabinet to excessive vibration. What sort of safeguards to you recommend to minimize the effects of accidents like that?
A: This ties back into our Push-In Plus technology, which is specifically designed to be resistant to the effects of vibration on wire terminals. Vibration can occur during shipment of a panel, as well as during normal operation. Standard screw terminals are susceptible to coming loose over time with any sort of vibration, and, as I mentioned earlier, a loose wire terminal connection will cause an increase in contact resistance. Higher contact resistance leads to lower current, higher temperatures on the wire connection and possibly fire or component failure. Our Push-In Plus wire terminals are specifically designed to combat this while offering a faster method of terminating wires.
Besides using a newer wire termination method like Push-In Plus, there isn’t much else you can do to safeguard wire connections when shipping a control panel. If the panel isn’t using Push-In Plus connections then you’re forced to manually check each wire terminal upon receiving the panel, which is a labor intensive practice.
For more information, visit automation.omron.com.
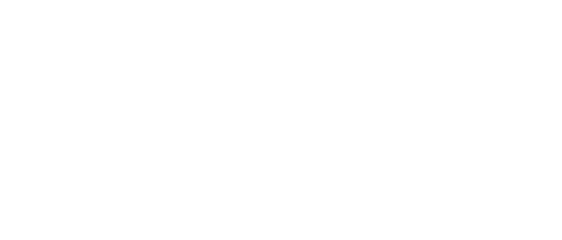
Leaders relevant to this article: