Why rethinking the DCS is important to realize edge and cloud potential
Scalability and flexibility are becoming more important as control platforms make more use of the Industrial Internet of Things (IIoT). Until recently this flexibility has been limited to cloud and edge computing, but challenges mean it has been difficult to unlock the full potential of either.
Since its introduction more than 40 years ago, the distributed control system (DCS) has made enormous contributions to the safe, efficient and reliable operation of hundreds of thousands of industrial facilities, from energy and power, to water, metals, minerals and chemicals.
Although users chiefly need high reliability and high resilience from the DCS, business and market demands are leading to new requirements (Figure 1). This is particularly evident with the rise of the IIoT, making huge demands on the accessibility of data from and around the DCS in a secure manner.
Opening up the DCS
To meet the demands of the future and cater for the changing needs of customers, the DCS must evolve from its closed and proprietary past. To achieve this requires improvements in both scalability and the ease of integrating new technologies while ensuring secure and open access to previously restricted information.
Until recently, the scope for connecting the monolithic core to new emerging IoT technologies has been limited, requiring the addition of separate interfaces that added cost and needed greater computing power and dedicated support.
This is being answered by new approaches to future control systems that are being driven by user groups to bridge the gap between the DCS and the broader IoT landscape. The Open Process Automation Forum—The Open Group—is a global consortium comprising more than 900 organizations, including customers, solution providers, integrators and academics. The group is working on establishing a set of standards to facilitate the development of open, secure and interoperable process control.
Furthermore, the Association for Standardization of Measurement and Control Engineering in the Chemical Industry (NAMUR), another global consortium with origins in Germany's chemical industry and representing process industry end-user organizations, has introduced a new open architecture model called NAMUR Open Architecture (NOA).
Both entities advocate an approach that effectively segregates core control and automation functionality from a broader digital environment, where non-time-critical monitoring and optimization functions can be carried out. This approach seeks to foster a harmonious integration between traditional DCS and the vast potential of IoT technologies.
A digital ecosystem
The challenge of expanding the potential of the DCS will be met by moving to a digital ecosystem for easier access to data and better scalability. This will enable manufacturing and process operations management to be much more agile when responding to future demands.
The digital ecosystem will be built on emerging edge and cloud technologies. These will bring major changes to the automation landscape by providing a flexible and secure computing infrastructure. This will include servers, data storage, development environments, business-intelligence services, artificial intelligence (AI) and data analytics that will help improve risk management, optimize productivity and achieve sustainability targets.
Future process automation systems are expected to be based on a robust evergreen core, where reliable, deterministic responses are prioritized, and an extended, digitally enabled environment that performs tasks that are less time-critical. This digital environment will also allow more rapid innovation and continuous improvements in performance.
Such an extended automation environment will enable secure connectivity with additional IIoT initiatives and allow for greater collaboration among people, systems and equipment.
Decouple software and hardware for maximum flexibility
Most distributed control systems provide a tightly coupled environment that makes it very difficult to be flexible in the technologies used.
By contrast, decoupling software from the hardware environment allows a user to move the intellectual property in the form of applications across multiple types of platforms; they are no longer limited to just one or two potential platform options.
Decoupling allows DCS integrators to make installations more modular, greatly improving scalability.
By separating hardware from software engineering, tasks can be decoupled, allowing independent teams to work in parallel and reducing the impact of changes on the project schedule.
Project execution can be further smoothed by making use of libraries of modular, reusable code—developed for particular types of processes or assets, these can be ported to other processes rapidly.
Future process automation systems will use pre-made, pre-tested automation software modules that come complete with elements for control, visualization and associated services. Using well-defined communication interfaces eliminates the need to develop special routines to coordinate the behavior of different modules. Pre-made modules also allow easy and rapid upgrades to control strategies, as well as ensuring that processes can be reconfigured easily. Quality controls on pre-tested code will also help to ensure that the unit becomes operational quickly and without incident.
By building a process control system out of a series of software modules, the automation system will help shift the control engineer’s tasks away from programming control logic; they will spend more time configuring process-specific automation requirements.
In the future, if an engineer needs to design a process unit for which a pre-tested module cannot be readily used, automated engineering methods will allow the rapid development of new code.
Keep it secure
Whatever technology or architecture is chosen, cybersecurity will remain a major concern. Beyond the issue of safety certification, today’s hot issue is about verification of the devices accessing the data. Now that we have open access to information, how do we ensure information is protected and reliable and comes from a trusted source?
Mechanisms are needed to authenticate devices and ensure that software components are running in the way they are supposed to. Building security into an automation system from the start means it will be a main part of your infrastructure costs and will need to be updated over time.
The more open DCS also offers the chance to improve the way projects are deployed, allowing more automation in design and also more autonomy in operation, with systems making many of the more routine decisions. Greater modularity and flexibility will also allow the DCS to be used by much smaller companies, spreading the benefits of sophisticated control to many other industries.
Luis Duran is global product line manager, safety, at ABB.
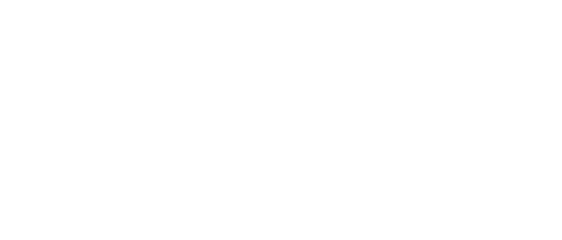
Leaders relevant to this article: