Controller upgrade modernizes American Castings’ molding line with minimal downtime
American Castings supplies large metal components to some of the world’s heavy equipment makers. The Pryor, Oklahoma-based company makes axles, frames, suspensions and other components that weigh up to 3,500 lb and are used in mining, farming and oilfield job sites (Figure 1).
The foundry where American Castings makes its heavy-duty metal components has been in operation for more than 35 years. Recently, the control system on one of the foundry’s main molding lines was showing its age, and the company decided it was time for an upgrade.
This presented a major challenge. Migrating the line’s control system and extensive I/O to new technologies would require weeks of downtime, something the company’s production schedule couldn’t afford.
Then, one day, a routine sales visit led to a solution that would allow American Castings to upgrade the line’s controller while avoiding extensive downtime.
Obsolete and disruptive technology
The control system at issue was on the automated no-bake molding line, one of two production lines in the foundry.
The no-bake line consists of a series of conveyors where sand molds are created, and molten metal is poured into them (Figure 2). Once metal solidifies, castings are shaken to remove the sand (mold). Throughout the line, transfer cars are used to move the molds from one conveyor to another.
Figure 2: The no-bake line consists of a series of conveyors where sand molds are created, and molten metal is poured into them.
The decades-old controller on the line was obsolete and causing production disruptions. In particular, the controller was experiencing slow scan times, which is how long it takes the controller to take in, read and react to information.
If a conveyor was moving and a limit switch told it to stop, it could take an extra half second to one second to stop. When this happened, the metal part could move out into the way of the transfer car, and then we have a crash.
The crashes were not catastrophic, but they occurred multiple times a day and took a toll on productivity.
We’re dealing with parts that are several feet long and weigh hundreds of pounds. You don’t just pick it up and put it back in place.
Not only was the controller obsolete, but so was the 1980s-era computer technology used to support it.
If something happened on the line, we had to use a computer to troubleshoot the PLC’s ladder logic. But the control technology was so old that we had trouble finding a computer that was slow and dumb enough to talk the same language.
It was clear the no-bake line needed to be modernized with the latest control technologies. The question was how to do it. The system had 10 remote I/O racks and about 1,100 I/O points. Replacing the controller and all the I/O would bring down production for four to six weeks. The company couldn’t afford a stoppage that long, given its high production levels.
A home-run solution
We chose to migrate the no-bake line’s legacy control system to an Allen-Bradley ControlLogix controller from Rockwell Automation. The modern controller offered significantly greater performance and capacity than the legacy PLC to resolve the slow scan times on the line. It also offered greater data availability. And it would eliminate the need for ancient computer technology to troubleshoot issues.
As far as how this new controller could be implemented with a minimal impact on downtime, a serendipitous encounter helped American Castings find an ideal approach.
A representative from Rexel, an automation distributor, just happened to be at the foundry when the topic of the control system upgrade came up. The representative mentioned the EtherNet/IP to Square D Remote I/O Gateway from ProSoft, an Encompass Product Partner in the Rockwell Automation PartnerNetwork program. The gateway would allow the new ControlLogix controller to talk to the legacy I/O.
The gateway would only be a fraction of the cost of replacing the line’s I/O racks and rewiring all the I/O points. More importantly, the time savings from avoiding all that work would allow the control-system upgrade to occur with minimal downtime.
Before implementing the gateway on the no-bake line, our department, which also includes Jerrod Estes and Chandler Beck, decided to first try the solution in a similar upgrade for the foundry’s environmental system. The system, which runs all the roof ventilation for the 433,000-sq-ft facility, used the same proprietary control system and I/O as the no-bake line.
In that pilot project, not only did the gateway allow American Castings to retain the environmental system’s legacy I/O, it also improved connectivity to the different environmental units across the facility. Instead of walking across the massive facility just to confirm that fans are running, or to turn air units on and off, workers could now do those activities from a central operator station.
The new system ran about one year without a single iota of a problem. We found we had a home run. We were ready to bring this to the no-bake line.
No growing pains
With the new control system now in use, the no-bake line is achieving scan times that are up to five times faster than the legacy controller (Figure 3). This has improved machine reaction times on the line and tightened conveyor movements, putting an end to crashes resulting from slow scan times.
Figure 3: With the new control system now in use, the no-bake line is achieving scan times that are up to five times faster than the legacy controller.
The new control system and its connectivity to devices on the line has also made operational data more accessible. Now, production managers can follow each component’s journey through production, as well as track overall line performance and downtime.
We expect the new control system will eventually help us increase production from about 30 or 40 molds per day to 60 molds per day.
The ProSoft gateway allowed the upgrade to occur at a much lower cost and with minimal downtime compared to replacing the legacy I/O.
American Castings saved more than $100,000 in wiring and installation costs, alone, by retaining the existing I/O on the no-bake line. And not having to shut down the line for up to six weeks saved the company hundreds of thousands of dollars more.
Certainly, not having to rewire more than 1,000 I/O points helped reduce downtime for the project. But our team was also able to run the new control system in supervisory mode to commission, test and tweak it while production continued running using the legacy system. We worked with ProSoft technical support to workout a few minor bugs related to fault handling of scans that caused a few minor headaches but were quickly taken care of.
All told, instead of being down for four to six weeks, the upgrade only brought down the line for a matter of hours.
Typically, once you start a control system conversion, you’re committed until it’s complete. This approach allowed us to have the two systems running essentially in parallel. We could go in, test the new system and review the results without taking production down for an extended period.
Currently, two of the no-bake line legacy I/O remote racks have been replaced with Rockwell Automation remote I/O with no additional loss of production. The ProSoft gateway continues to allow communication to the remaining legacy I/O racks. There are plans to replace the remaining legacy I/O on the no-bake line as the production schedule allows. With the ProSoft gateway in place, American Castings will be able to migrate one module or rack at a time based on what works best for the company and its production schedule with little or no downtime to the line.
ALSO READ: PLC vs. Arduino for industrial control
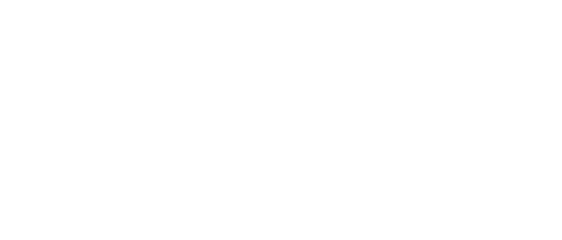
Leaders relevant to this article: