Figure 1: The technology makes it possible to program machinery via LabView software, without having to write a single line of PLC code.
Quality is why companies put their faith in automated testing processes, including regular lifecycle verification, fatigue testing and materials inspections. The machine builder has to match the testing units and instrumentation to the needs of each individual customer.
Many employ National Instruments’ LabView software for this function. This graphic programming system is always used whenever it’s necessary to acquire and process measurement data and to integrate the instrumentation needed for inspection purposes (Figure 1).
“How long is the lifecycle of a component, given what it can withstand and how it’s manufactured?” asks Dr. Ralf Koeppe, vice president of engineering and manufacturing for electric drives and controls at Bosch Rexroth. “This can only be answered by special measuring and testing machines. Not only do they test prototypes, but in large-scale series production, they test series components over and over again in order to guarantee 100% quality.”
One task, one user interface
At Kraus Automatisierungs-Technik (KAT) in Hassfurt, Germany, in Lower Franconia, we manufacture test benches for the automotive industry and other sectors. They’re used to test mechanical elements’ service lives under the most realistic conditions possible.
Also read: 3 types of inspection and measurement
Until recently, the employees at KAT, in addition to programming using LabView, also had to write a PLC program for the actual operation of the machine. This was both complex and time-consuming. In addition, the programmers had to have in-depth knowledge of both systems and had to use two separate user interfaces. That is why KAT sought an integrative solution to write programs for test bench automation without having to leave LabView (Figure 2).
At KAT we have this option now with Rexroth’s Open Core Engineering (OCE). Its new Open Core Interface (OCI) technology makes it possible to program machinery via the LabView software, without having to write a single line of PLC code. With the adoption of Open Core Engineering, we are now working with fewer user interfaces. That is both efficient and minimizes the risk of error. A single programmer has the entire project under his own control. This means that we are far more flexible in manpower planning. Seamless and complete inclusion of the control and drive function in the LabView development environment makes it possible for programming using LabView only. This simplifies and accelerates the commissioning of customized testing equipment and instrumentation.
Developer Uwe Schweinfest at KAT can program machines from beginning to end.
KAT’s customers also profit from OCE. They can use LabView to make modifications to a testing machine themselves, without being familiar with PLC.
OCE translates programming languages for machine control. “When people of different nations work in a team, they must first agree on a common language,” explains Koeppe. “Only then can they coordinate tasks and come to mutual agreements. The same applies for machines and IT systems. For the first time, high-level language-based applications on external devices have access to all the functions of the control units and drives.”
Thus, applications based on C/C++, for example, can run in the real-time environment of the control unit. That is why the OCE software portfolio includes interface technology through which Bosch Rexroth now brings together the worlds of automation and IT. The OCI automatically makes a variety of programming languages available to the control unit. The result is machinery manufacturers can program with modern higher-level languages without having to write a single line of PLC. This reduces the programming efforts by up to 50% as one of the first OCI applications shows.
“In the software of these machines, the program LabView has been established worldwide,” says Koeppe. “It’s designed exactly for the requirements around the industrial measuring and testing. The only disadvantage until now is that, in addition to LabView, the machine manufacturers must program machine controls and coordinate the two programs with one another. There are no standard interfaces for this, which lead to extra time and effort. The specialists for LabView and for PLC had to agree at first and then write their respective programs and then test them to see if they would actually work hand in hand.”
OCI has facilitated the work of the programmers considerably, explains Koeppe. “A programmer now uses LabView to produce the software for the tests and the movement processes of the machine without needing to write a single line of PLC code,” he says. “This eliminates double work and error-prone interface programming. Rexroth is providing libraries with more than 550 virtual instruments. These translate the LabView commands for the PLC controls.”
OEM machine builders such as KAT are already using OCI to their benefit, to reduce engineering efforts and to reduce their delivery times. With the same team, the company can now program twice as many machines.
Reduced complexity
This degree of efficiency when programming instrumentation and test systems using the Open Core Interface is achieved by Rexroth with the aid of a software development kit (SDK). With its help, and in conjunction with the Rexroth IndraMotion MLC and IndraLogic XLC control systems, users can access control functions right from the application program. The programmer uses a supplementary package to import these libraries into LabView and thus has more than 550 virtual instruments (VIs) at hand. KAT uses this new freedom, for instance, to execute the jog mode, but also for travel at velocity, position regulation or switching on and off the corresponding drive regulator in LabView. The signals generated by the sensors and actuators, wired to the PLC input and output modules, are available immediately.
“Everything is programmed from beginning to end,” explains Uwe Schweinfest, a developer at KAT. “We only have to integrate the VIs into a class. That lets us form chains of steps for the actual machine processes. And we can re-utilize our work in later projects without major effort.”
OCE was distinguished in 2013 with the Deutsche Messe Hermes Award technology prize. OCE connects the previously separate PLC and IT worlds by offering an integrated solution consisting of open standards, software tools, function toolkits and the OCI. To achieve this, Rexroth has opened the control core to provide expanded access.
“Now, with a variety of high-level languages and operating systems, machinery manufacturers can create independent individual functions, which run parallel to the firmware directly on the control unit or on external devices,” says Koeppe. “With this capability, machinery manufacturers can now, for example, also fully integrate smart devices into automation and take advantage of their operational interface capabilities.”
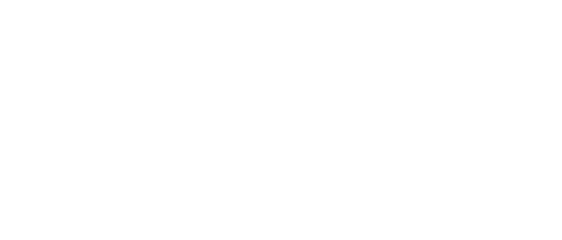
Leaders relevant to this article: