Production systems can no longer exist as silos in the smart factory. They must be connected and able to close the gaps that have long existed between information technology (IT) and operational technology (OT), so their data can be collected, combined and contextualized.
Perhaps nowhere is the need for connected and converged systems more apparent than in your human-machine interface (HMI) system because that’s where production insights created from different data sources ultimately surface for staff.
Today, the hardware and software components that make up your HMI system must be able to combine into a single, seamless, easy-to-use system. And they must be able to converge IT and OT, so you can leverage multiple data sources and support a holistic cybersecurity approach to help protect both your data and your connected operations (Figure 1).
Certainly, specifying HMI hardware and software that’s designed to integrate with each other and with your control system is a good place to start. It can ease access to the data you need to help optimize equipment performance and quality. But there are several other aspects of your HMI system that you should consider if you want it to thrive in the smart factory.
Centralized vs. decentralized architecture
It’s a simple truth: The more devices you have on the factory floor with operating systems and applications, the more challenges you need to manage.
There’s the obvious risk of production going down because a device fails. But there’s also the hassle of maintaining all these devices—making sure each is up to date with the latest software and security patches.
Challenges like these can drive more companies to adopt a centralized HMI architecture. With this approach, a single server hosts your HMI and other application content. The server uses content-management software to then deliver that content to a mix of thin client terminals, mobile devices and industrial PCs across your factory.
This helps ease maintenance and reduce downtime risks by minimizing the number of operating systems on your plant floor that need to be updated and maintained. It can also strengthen your cybersecurity by storing content in a central location instead of on several plant-floor devices.
A centralized architecture can also better suit the needs of your smart factory, where it’s critical that the right people have access to the right information when they need it.
For example, thin-client management software allows you to customize what content is delivered to each HMI device based on the name and role of the person who’s logged into the device. The software also allows you to deliver content from other sources, such as IP cameras or work order systems, that can give operators better visibility into a process.
Flexible content delivery
Your HMI architecture should give you flexibility in not only what information you present but also how you present it.
A good example of this is the use of mobile devices. At the very least, your HMI software should allow you to use smartphones and tablets as operator interfaces. This can help you meet the needs of a modern, mobile workforce.
But if you’re using a centralized approach, you should also consider using capabilities such as location-based mobility, which can deliver content to staff based on their physical locations in the factory.
Here’s how it works. When a worker enters a defined location or scans a location ID such as a quick-response or QR code, your HMI system automatically presents content on the worker’s mobile device that’s specific to that physical area—such as performance or diagnostic data at different points along a production line. The content isn’t stored locally, and, when the worker leaves the location, the information is automatically removed from the device.
Capabilities like terminal-to-terminal shadowing can also help make staff more efficient and responsive. If an operator encounters a production issue, for instance, a technician can use a mobile device to shadow the operator’s terminal and quickly start investigating the issue, even if the technician is on the other side of the factory.
Informative and proactive alarming
Critical issues shouldn’t go unnoticed in a smart factory. That’s because your HMI software can optimize how staff see and respond to alarms.
One way you can do this is with device-based alarms, which detect and manage alarms in a controller instead of a server. These alarms can help staff to detect alarms faster and give them more accurate alarm timestamps than tag-based alarms do. Also, using your HMI software to overlay alarm information on trend data can help your staff more quickly troubleshoot issues.
Multiple notification methods and alarm escalation can also help make sure alarms are seen and addressed as quickly as possible.
This involves using a mix of email, text message and smartphone notifications to help make sure staff is informed of alarms even if they’re not standing in front of an HMI screen. You can also escalate notifications to other staff in instances where a worker doesn’t respond to an alarm or when a condition worsens.
Comprehensive cybersecurity
HMIs in plants are the gateways to production systems and sensitive information. They must be protected as part of a comprehensive cybersecurity approach.
Certainly, you should scrutinize the security capabilities of HMI offerings on the market. For example, HMI software should have strong application security and built-in checks
and balances to help make sure any changes are authorized. And, if you’re building a centralized architecture, your content management software should use access groups and permissions to restrict access and require multi-factor authentication for location-based mobile connections.
You should also consider the inherent security benefits of a centralized architecture.
Consolidating applications and operating systems from several devices to a central server simplifies security updates. And the server can be kept in a secure area, like an IT facility, to help prevent unauthorized access. Thin client hardware used as part of a centralized approach also doesn’t have hard drives or a point of entry for viruses.
Simplified lifecycle support
Key decisions made up front during the design of your HMI system can help ease maintenance of the system across its lifecycle.
For instance, thin clients offer long-term cost savings and simplified maintenance compared to PCs. The devices have no moving parts and a long mean time to failure. And if they do fail, they can typically be replaced by anyone in less than two minutes with no loss of data.
If you’re not ready to deploy a centralized architecture, compact box PCs can be a smart option. They can run a Windows OS or thin client management software, so you can use them as a PC and switch to using them as a thin client when you’re ready.
Meanwhile, graphic terminals are available in stainless steel options that are National Sanitation Foundation (NSF)-certified. These options can help to simplify cleaning and minimize contamination over the life of the hardware.
Connect the human and digital
In the smart factory, your HMI system has a big job to do—connecting people with information that is time- and job-relevant, so they can understand problems quickly and make better decisions faster. With the right design approach, you can achieve this, while creating a simple architecture that is easier to maintain, secure and sustain.
Sue Burtch is visualization software marketing manager at Rockwell Automation. Contact her at [email protected].
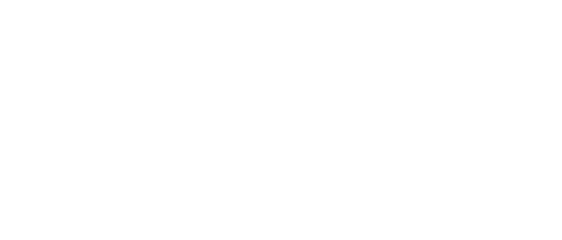
Leaders relevant to this article: