Technically, an operator interface (OI) and a human-machine interface (HMI) could be considered the same thing, and the differences between them are becoming increasingly blurred. The generally accepted definition of an OI is a usually a text-based display that may have a limited number of buttons to allow operator input to the control device. Some alpha-numeric displays have a number of programmable function keys and a full keyboard, but these are becoming rare because of the continuously falling prices of graphical touchscreen interfaces. An HMI is a usually a graphic-based display that provides a greater number of operator input options. One often-cited way to differentiate between a ship and a boat is that a ship can carry a boat, but a boat cannot carry a ship. The difference between an HMI and an OI could be defined similarly: “An HMI can function as an OI, but an OI can not function as an HMI.” The analogy is imperfect, and the terminology is often used for both types of devices within a plant, within an industry and within a manufacture’s product line. For our purposes, let’s consider an OI to be a simple message display and operator input device that doesn’t have a microprocessor for data manipulation.
An OI may be a small device mounted at a specific place on a complex machine. For example, it may serve as a local display for a flowmeter or temperature controller. It may be the only interface on a specific purpose machine such as an air compressor or hydraulic power unit. An OI may be used as an andon board or as a display to show current production status. A programmable traffic sign, variable-message sign (VMS) or matrix sign may also be considered as a type of OI. We are considering operator interfaces as used in the manufacturing environment.
The sophistication of any interface device is limited only by the creativity of the designer. If using an OI with a few lines of text and a few input buttons, a number of operator selections should be limited. While it may be possible to display dozens or even hundreds of individual messages on an alpha-numeric OI, an operator scrolling through multiple selections to find the correct one for the task at hand may spend more time pressing an up/down button than if presented numerous options on a larger graphical interface. A designer must always include the amount of time the operator spends interacting with a piece of machinery as part of the cost of ownership. When used as the primary interface to a control system, an OI is usually associated with a rather simple machine, such as a pumping station, air compressor, motor switching station or other systems with a minimal number of operator adjustable functions and informational prompts.
On larger machines and systems, a small text-based OI can be used as a local display or input-output device at different locations around the machine, even if larger, full-featured HMIs are also incorporated into the design. Most intelligent sensing devices have a built-in informational display of some sort. A process controller may have a six- or eight-digit alpha-numeric display used to set up the device and to display current operational measurements. A disadvantage to this type of display is the limited amount of information it can effectively convey. If an error message such as ER_039 is shown on the process controller’s display, a maintenance person may need to access a manual to determine the meaning of the message. A little text-based OI allows the control device (PLC, PAC or PC) to decode the error message and display an exact description without requiring access to the main HMI. Of course, this only works if the main control system has the information about the ER_039 fault code and the control system has communication to the process controller.
If a certain section of the machine has several intelligent sensing devices, each one may have different methods to scroll through the available information. Using a local OI, an operator, manufacturing engineer or maintenance person can have access to all of the information the different sensors supply to the control device using a consistent method of access.
When selecting an OI, normal considerations include the number of characters that are displayable at any one time. A short message that is shown without scrolling across the display takes less time to read and understand. The physical size and color of the characters should be selected to provide fast and easy viewing from the normal distance the operator views them. An excellent resource for determining the optimal size of a display character is here. The environmental packaging of the electronics should follow the NEMA or IEC ratings that are required for the location. Older technology used for LCDs limited the operational temperature of the displays due to the type of liquid crystal fluid used and the voltage thresholds applied to the display element. LED displays did not exhibit this restriction and were used when the device operated in extreme temperatures. Modern technology has removed this disadvantage by using different LCD fluids. Pure LED devices, not to be confused with LED-backlit LCD displays, are still somewhat brighter, have a wider viewing angle and are easier to see in bright ambient light or sunlight. Because of advances in the technologies, this difference is now minimal. Newer technology, such as organic light emitting diode (OLED), may replace both LED and LCD devices.
ALSO READ: You might have HMI design backward
Communication options can range from a simple parallel interface to EtherNet/IP or even wireless Bluetooth. Parallel interfaces are the most restrictive as far as message display type. Typically, static messages stored on the OI are presented based upon the bit pattern applied to the interface. If displaying static status or fault messages is all that is required, a parallel interface may be all that is needed. Using a lower-end serial connection, such as RS-232/422/485, will allow dynamically changing the messages to be displayed. The complexity of creating or sending messages to the display depends on how easily the control device handles string data. Some PLCs do not handle this task very well, while a PAC or PC may be a better device to create serial message strings. When a serial or Ethernet-enabled OI includes software drivers for the specific control device, messages can be created that contain variable data stored in memory registers. The designer can create static messages such as “Current Pressure = xxx,” with xxx representing a dynamically changing value stored in a memory location of the control device.
Manufacturers who offer lower-end, relatively inexpensive operator interfaces will likely also offer higher-end, more-expensive models that the manufacturer would rather sell. The profit margin on these low-end products is often not sufficient to support many development resources for producing polished software and comprehensive technical manuals.
Properly utilized, a text-based OI can be a very useful tool for machine operation and troubleshooting.
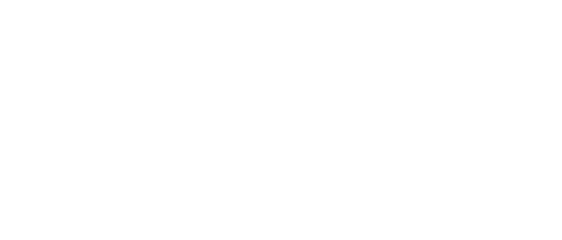
Leaders relevant to this article: