It's not the Holy Grail, but it's close. Ever since control and automation engineers began to move away from point-to-point, 4–20 mA hardwiring and toward twisted-pair fieldbuses, Ethernet and wireless, they've been approaching the means to create the one network that can do it all. This is logical because if you had to implement multiple separate networks for controls and automation, power, safety, physical security, administration and enterprise and other special functions, you'd no doubt prefer—if you had the chance—to install one network infrastructure that could handle all these jobs.
Unified Network from Scratch
Besides saving power and costs, the real benefit of a truly combined industrial network is that it can improve plant-floor control and help users run their applications more productively.
CS Vacuum sought assistance from system integrator Apollo Solutions (www.apollosolutions.it) in Pessano con Bornago, Italy, and its controls division, Saguaro Sistemi (www.saguarosistemi.it). To provide the controls and cooperative network that CS Vacuum needed, Apollo Solutions decided to implement a PC-based control system built around an embedded PC, panel PCs and other equipment from Beckhoff Automation.
"One superior, centralized control system is the best way to make all components play as an orchestra with excellent performance and reduced power consumption. Using standard communication lines such as LAN, CAN, Modbus and others permits the interconnection of several subsystems and lets us better manage subcomponents on the same machine," says Marco Brunazzi, Saguaro Sistemi's development engineer. "We also use advanced algorithms as the ideal way to make machines work in the best way possible, such that only the components that are needed are used at specified times and always at the top of the curve."
In essence, the embedded PC controls the scales, cooking pot and the fryer via Modbus, as well as controlling the oven via Profibus. Another unit archives the resulting data, not only for a possible subsequent inspection by local health authorities, but also to verify production performance and efficiency. Also, production is controlled via the local server. Once a particular day's program/recipe—such as spicy chicken—is entered, the specified program is adopted automatically by all plant modules, including the cooking pot, scales, oven, vacuum device, packaging and labeling machine and discharge conveyor (Figure 1).
Figure 1: Cooking + Environment = Efficiency
Pre-packaged food manufacturer CS Vacuum uses a PC-based solution and integrated LAN, CAN and Modbus networking to coordinate controls between its automated production line's cooking pots, fryer, oven, dosing system, vacuum-sealer, pasteurizer and storage system, as well as the line's dedicated air-conditioning system's fans, coolers, water heaters and pumps and cold-room de-icers.
The panel PCs, which are used for production preparation, are equipped with touchscreens and communicate wirelessly with a local access point. These touchscreen panels are mounted along the entire production line and allow CS Vacuum's operators to monitor each production phase and make corrective interventions as needed.
Meanwhile, the second part of its integrated network controls the production process and the facility's specialized air-conditioning system, which includes four air-treatment units, six fans, two cooling units, water heaters, pumps, overheat switches for the automatic or manual pumps and de-icers for the cold rooms. All consumers in the air-conditioning system are connected to an additional embedded computer.
"Because less consumption means a lower impact, our integrated system manages the various machines in the plant, making all of them work at the highest performance, wasting the least energy possible, all while delivering positive economic returns," explains Brunazzi. "A first-class control system and network allows users to check machine status in real time, including the energy consumption, and view warnings when this consumption rises too much or too fast. This permits the reduction of overall power consumption and cuts energy use, especially in areas that are noncritical in that moment of the production cycle."
Following the renovation and relaunch, CS Vacuum's entire production cycle now is subjected to continuous checking. As requested and designed, the cooking and vacuum-sealing production line's higher-level automation optimizes product quality and reduces demands on staff. Finally, Apollo Solutions also added power generation, building control, order management and traceability of production to CS Vacuum's integrated system. "We were able to implement the solution we developed without changing the basic principles stipulated by the plant designers," adds Brunazzi. "We see this as a big advantage alongside the impressive price-to-performance ratio. Also, the ease of operation of the system control, which only requires basic knowledge of the Microsoft Windows environment, also met with a positive response from our customer."
Combining Networks 101
This emerging desire to unify networks begins with the basic need to get a job done fast and hopefully with less labor, materials and after-care than last time. "We recently worked on a power-monitoring project at a large Midwest airport, and we started with about 80 old Square D, Cutler-Hammer and GE power meters," says Brian Beaufeaux, PE, senior electrical controls engineer and co-owner of Industrial Automation Engineering (IAE, www.iae-online.com), a CSIA-certified system integrator in Ham Lake, Minnesota. "Some used Modbus, so we added protocol converters for Modbus or whatever proprietary protocols they used. These converters get meter data onto Ethernet, and we then put in an Ethernet backbone that allows meter data to be unwrapped at the end. This let all the meters send back data, log it into an historian and then help administrators analyze demand peaks and billing information and also schedule maintenance. On the other end, the plan is to tie in the HVAC system and lights and relate them to an SQL database."
Beaufeaux explains that the Cutler-Hammer power meters at the airport use Eaton's Eponi converters to translate its proprietary protocol to EtherNet/IP. The data is then secured by a Kepware data collection server and put into an historian like Wonderware's SCADA software or an SQL database. In addition, this data can go to a secure website where users can employ Secured Reports System (SRS) and Microsoft's SharePoint software to mine it and analyze it. "There are a lot of real savings here, but first we need the right pieces of information, and then they can go into a report to the finance department. For example, power-meter data could be used to run what-if scenarios and then negotiate off-peak, rate-structure savings for airfield lighting," says Beaufeaux.
History and Ethernet
Of course, most previous efforts to bring different industrial networks into this type of mix have been derailed by different cabling, connectors and other hardware, as well as incompatible communication protocols, data rates, signal frequencies and power conditioning levels. This is logical, too, because they all have different technical histories, and many efforts to bring them together are only a few years old, even though the earliest efforts began 10-20 years ago. Plus, there remain many proprietary interests that might love to keep them apart and continue to make fearful users pay for their lack of interoperability.
On the other hand, the greatest enabler of network unification is Ethernet itself and its many cabling forms and communication protocol flavors. As it has emerged and gained momentum in recent years, Ethernet has come closest to delivering the one network that many of its supporters seek—or at least gathering data from several networks—while continuing to let specialized systems run separately and collect some data from them when available.
Likewise, many protocol conversion tools have grown up to handle translation tasks between different communication languages. These devices often accompany the increasingly intelligent switches and gateways that route data traffic between networks. Also, one of the biggest aids to Ethernet's dominance is its use of Internet protocol (IP) addressing, which now seems to be used by every device from the largest facility or machine to the tiniest module or chip. Also, Ethernet's ability to add new capabilities and pathways, such as wireless Ethernet or Wi-Fi and device power via power over Ethernet (PoE) have fueled its adoption even more.
Herding and Merging Networks
Though building new industrial networks always has been different than renovating old ones, there are more parallels between the two jobs when network unification is the goal. Perhaps it's because industrial networks and their signals running separately can be accessed and linked together by an overarching network in much the same way as this uber-network reaches out and links the software running on hardware systems and individual components.
For instance, embedded systems designer and system integrator Saara Embedded Systems (www.saarasys.com) in Bangalore, India, used National Instruments' (NI) LabView software and single-board RIO platform to build a unified system user interface for its remote facility management system (RFMS) that can monitor and control an application or a facility's or infrastructure's total energy consumption (Figure 2).
Figure 2: Views You Can Use
Saara Embedded Systems built a unified Facility Monitoring Systems user interface that can combine data from different networking sources, such as Modbus, Profibus, DeviceNet and HART and then display power usage, facility temperatures, lighting levels and even the types and number of cups of coffee and tea dispensed by its vending machines.
NI's RIO platform integrates an onboard, real-time processor, a field-programmable gate array (FPGA) and digital I/O with Ethernet and RS-232 ports and onboard storage for data logging. The RS-232 port communicates to energy meters, and remote systems data can be pushed to the central server over various communication protocols such as TCP/IP or over secure wireless modes including ZigBee, GPRS and CDMA.
"RFMS precisely monitors and controls a facility's or an infrastructure's total energy consumption," says Siddarth Verma of Saara Embedded Systems. "It provides unconstrained real-time access to parameters from diesel generators, HVAC, signage boards, security systems, refrigeration equipment, lighting systems, uninterruptible power supplies, printers, beverage vending machines and even single-switch or valve-based devices. With the flexibility of the embedded remote terminal unit (RTU), our customers can monitor and control different points on their infrastructures, making RFMS an ideal system for effective energy consumption and optimization. For example, RFMS reduced energy consumption by one of our customers by 15%. With RFMS, the frequency of fuel replenishments dropped because replenishments now are based on a proactive, on-demand system, fuel consumption accounting is accurate, and fuel-theft issues have been addressed. As the number of RTU-installed branches increases, so do power consumption savings. With the vast improvement in customer service quality due to uniform policies in its offices, our customer has gained a competitive edge as a pioneer in energy savings. Additionally, because of the performance of our RFMS, our customers are recovering the cost of our solution in six months through the energy savings."
In addition, pharmaceutical manufacturer Mantecorp Indústria Química e Farmacêutica (www.mantecorp.com.br) has spent $70 million in the past 15 years to modernize its 100-million-unit production facility in Rio de Janeiro, Brazil.
This ongoing effort recently included updating its controls with a CC-Link network, which allows simultaneous communication and control of the Rio facility's major systems, including air conditioning and refrigeration for both process and environmental control; energy management, filtration and water handling, steam and air handling, and sterilization of air for process areas. CC-Link is also the pathway for system data to operator control panels and PC displays (Figure 3).
Mantecorp uses CC-Link, a master PC and distributed CPUs to communicate with and control major systems such as air conditioning and refrigeration for process and environmental control, energy management, water filtration and handling, steam and air handling and process air sterilization.
The combined CC-Link network consists of one Mitsubishi master and 10 of its slave stations. Each of the CPU slave stations has four CC-Link remote I/O racks containing analog and digital I/O modules connected to various field sensors and output devices. As a result, the reverse-osmosis process in Mantecorp's facility that purifies water is controlled via CC-7890Link and its CPU stations, while more CPUs on the same network control air sterilization. With CC-Link, Mantecorp reports it can produce prescription pharmaceuticals that require a Class 10 environmental facility certification.Securing Backbone Buy-In
Though having a combined and coordinated network might be admirable for its own sake, plant-floor personnel won't use it until they can see how it improves production and their jobs. "We recently put in a holistic CMMS solution for a big grain-handling company that has 25 sites in the U.S. and trained the plant managers on it," says IAE's Beaufeaux. "However, only 5% of them were using it after six months. So, we redid it, but only 7% were using it a year later. Management wanted the CMMS to be used to avoid possible safety issues, but the plant managers wanted to get their barges loaded in four hours, and weren't as worried about dust buildup and overheating." Beaufeaux also notes each group wasn't aware enough of the other's priorities.
"So, we grabbed more local data, added it to the corporate database and set up a 24/7 support service, Hazard Monitoring Reliability Program, to help resolve problems before they could escalate," continues Beaufeaux. "This helped operations understand more about the reasons for not silencing alarms, and enabled them to show that when a barge didn't get loaded quickly, it was being done to prevent a possible accident. This kind of communications isn't available with stand-alone alarms and networks. In addition, it's only possible to do this on a network that integrates many software packages, shows an overview of all plants and then allows reporting and interfacing on all levels."
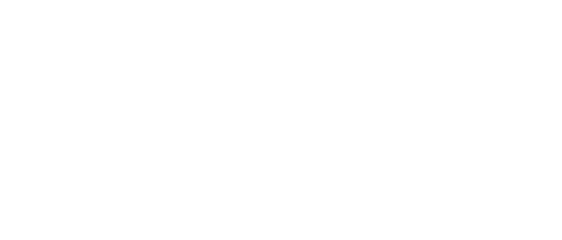
Leaders relevant to this article: