The customer is always right—and these days that can mean going green. Consumers, retailers and pretty much everyone else is waking up to the value of saving energy and reducing waste. As a result, many demand that utilities and manufacturers run greener and provide tools enabling them to be more ecologically responsible themselves. In turn, manufacturers require machines and equipment that consume fewer resources and produce more sustainable products. So, some machine builders are redesigning to run greener and handle greener materials.
However, the reality of a sustainable manufacturing environment—an environment based on renewable sources of energy and raw materials—is a long way off for many industries. Basically, like so much else, the concept of sustainability rolls downhill. So, going green is a first step for manufacturers and machine builders. It is also a way to make some green.
For example, jet fuel is very expensive, and so airlines try to conserve it by flying planes with lighter airframes. This is why airplane manufacturers and their parts suppliers use more carbon-fiber-reinforced plastic parts. However, machining carbon-fiber can produce potentially unhealthy particles, and so machine tool builder Mori Seiki USA's (www.moriseikius.com) Machining Technology Lab (MTL) recently developed and implemented its Zerochip high-pressure vacuum process for many of its machining centers. The system uses hollow machine spindles through which a specialized vacuum sucks the dust-like chips from machining carbon-fiber, graphite and composite materials into a sealed container. This allows users to safely machine the lighter, energy-saving parts they need for green airplanes, as well as racing cars, bicycles and other future products.
Creating more efficient machines, applications, facilities and products requires users to adopt and follow some better practices. Though each machine and application is different, here are some basic practices that can be used across a variety of production settings and industries.
- Measure and evaluate the energy, materials, water, compressed air and other resources you and your organization are using now and begin to develop a plan for conserving those resources. This plan might include powering down or turning off equipment when it's not being used and replacing simple induction motors and drives with variable-speed motors and drives or servo drives that can more closely match production needs with energy used.
- Check if your machine, application or facility could use regeneration technology, which typically uses a shared power source and linked drives to capture power from decelerating components and use their energy to accelerate other components.
- Conduct a mini-audit of one of your machines or production processes, investigate which solutions might help it save energy or reduce materials, implement a test or trial run and evaluate the savings it generated.
- Examine all the materials that your machines consume or process into products and seek ways to reduce waste, perhaps by running closer to tolerances or by recycling materials. Also, check if more sustainable alternative materials could be used, and determine which design changes they might require in your machines.
Combining Tasks
While making machines simpler is one way to go green, other builders are joining together several devices to save energy and materials. For example, Hyatt reports that Mori Seiki MTL's newly released grind-hardening process brings together formerly separate rough machining, heat treating and finish machining processes into one center, such as its NT4250DCG mill/turning machine that makes heavy machine parts. Besides combining machining functions, grind hardening uses heat from rough machining to selectively heat-treat machined parts in the same unit. This allows users to avoid sending parts out to an off-site furnace for heat-treating. Hyatt reports this process is 85-95% less costly than traditional machining and heat-treating methods.
More Than Efficiency
Is this just good old efficiency dressed up in green clothing? No and yes. While traditional efficiency affects a builder and its end users, green manufacturing influences a wider circle of disciplines and requirements—eventually touching everyone. In short, green manufacturing appears to embrace more technical areas and a larger jurisdiction than efficiency.
"We see and hear about green and sustainability all the time, so we offer energy savings and simpler designs in the machines we build," explains Craig Friesen, product manager at packaging machine builder Thiele Technologies (www.thieletech.com) in Minneapolis. "For instance, we can do 440 V or 220 V machines that use less current, save power, cost less to run and help the environment. Or we simplify the design and have a conveyor that used to need two motors now operate with one. However, this doesn't always involve equipment and can instead involve greener consumables." For example, he says, a customer might want to use a more recyclable hot adhesive, and Thiele then needs to design around it.
"It can be hard to get more efficiency and energy savings out of a machine that we've been building for 50 years, but we'd rather update a design than invent a whole new machine, and so we have to be very creative," he adds. "We work with our fabrication shop and engineering group, look at what we usually build, perhaps a laser cutter and brake, and then design easier-to-manufacture parts. It's an ongoing process, and there are lots of baby steps. But sometimes, after building the same model for years, an engineering and assembly guy suddenly says, 'I think if we did this differently, we could save some assembly time.'"
Saving Energy
No doubt the most obvious and significant way to go green is to conserve energy. Mark Elsass, applications and technical services manager for Milacron's (www.milacron.com) U.S. mold-making operations in Batavia, Ohio, reports, "For us, 'green' means being more energy-efficient by using larger and more efficient motors to translate rotational motion to linear and using servo-driven motors to drive the axes on our electric machines instead of the ac induction motors we used on previous machines. Because we supply machines to users to make molds, we work closely with mold manufacturers on what their users will need as they seek to be more efficient and sustainable."
Likewise, to better handle seasonally fluctuating demand and increasing product varieties and save energy at the same time, German brewer and bottler C&A Veltins (www.veltins.com) decided in 2007 to deploy 284 of SEW Eurodrive's (www.sew-eurodrive.com) Movigear mechatronic drive units in a single-line network installation (SNI) on the container and box conveyors serving its new 60,000 bottles/hr filling line in its new plant in its hometown of Meschede-Grevenstein. The line alternates between Veltins' Pilsner, alcohol-free and beer-mixture products, and must quickly change over between different bottle types.
Movigear optimizes the interfaces between its motor and gears by directly combining those gears, motor, drive, motion control and communications in a single gear housing, which reportedly achieves 12-20% better efficiency and delivers similar energy savings, according to Rich Mintz, SEW Eurodrive's strategic product marketing manager.
To further simplify its network infrastructure, the brewery's SNI daisy-chained its Movigear units together by their three-phase power cables, but these wires also use a PowerLAN method to carry the application's high-frequency communication signals, adds Mintz. "This meant that Veltins didn't need to install about 4600 m of 24 V standard bus wiring, and so it saved about 60% on its cable costs," he explains.
Energy in Europe
Not surprisingly, European manufacturers and machine builders have dealt with higher energy costs for a lot longer than their counterparts in North America and elsewhere, so they have many lessons to offer about green manufacturing and the goals of sustainability.
"Every organization can look at the energy, materials, water, compressed air and other resources they consume," says Scott Hibbard, automation vice president at Bosch Rexroth (www.boschrexroth-us.com). "This can involve plugging in a kilowatt meter and turning off some lights, but it also can involve looking at the resources consumed by individual processes and changing machine programs to save energy by using servo drives instead of bleeder resistors. For example, a thermoforming machine that makes yogurt cups might have platens that press down in sequence to form the cup's rough shape and internal ribs. Each step requires the drives to use a large spike of energy, but where the excess energy used to go to a resistor that dissipated it as heat, it can be put back on the grid by being stored in capacitors and then shared on a dc bus between multiple drives."
Conserving Materials
While saving energy is hugely beneficial, it's also just the beginning of going green. Machine builders and end users need to think about how to reduce waste, recycle and seek alternative materials that are easier on their communities and the environment. Some veteran builders say this challenge is similar to learning about and adopting any new capability.
"Green is just one more ripple in the whole process and history of understanding customers and learning what their real problems are because they don't always tell you," says Thomas Kleeman, CEO of Spartanics (www.spartanics.com) in Rolling Meadows, Ill. "For example, about 10 years ago, our European customers wanted to stack the leftover material coming off our PVC plastic printing and die cutting machines that make credit cards, so they could ship it to their recyclers more easily. As a result, we designed and built a machine to neatly stack all this scrap that used to go into a bin. This material still goes into a dumpster in the U.S., but more end users here are looking at this kind of recycling. These types of plastic can either be reused by their initial manufacturer or used down-market in milk jugs, traffic cones and park benches."
Spartanics builds laser and hard-tool die cutting, screen printing and re-registration, machine vision inspection and finishing machines, which are used to produce everything from credit cards to automotive dashboards and displays (Figure 1).
Simplify the Machines
Besides just trying to save energy, green manufacturing also can mean simplifying packaging machine designs, so they can run more flexibly and efficiently and also save on raw materials while making lighter, stronger packages, adds Friesen. "We build packaging machines for consumer goods manufacturers, and they demand green equipment," he says. "This is because their customers are retailers who use supplier standards such as Walmart's Green Scorecard, which require goods manufacturers to address environmental impacts and sustainability issues. So, if a customer needs to design a greener package that uses less material, we have to make sure our machines can handle these new designs. Once we understand what they're trying to accomplish, then we can go back to them with machine design modifications that achieve what they want."
In the end, green manufacturing and sustainability are just a couple more design requirements that end users can tack onto the next request for proposal (RFP) and design specifications. "I don't see green and sustainability backing off anytime soon," adds Friesen. "We're going to have more regulation of energy use and waste generation, and so retailers will push their suppliers to provide products to accomplish these goals."
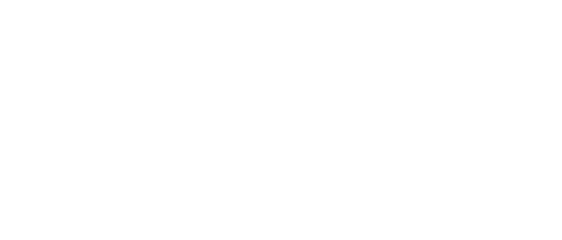
Leaders relevant to this article: