Getting ready for a trip usually takes longer the farther away you go, and the same rule is true for machine builders. When they sell, ship, install and maintain machines in other nations, regions and continents, machine builders face a variety of different technological specifications, safety and other regulations and endless unique local and application-specific needs.
Technical specifications usually arise from differing electrical voltages and frequencies in different countries and regions. The most basic example is that standard industrial voltages in the U.S. are 230 V or 460 V at 60 Hz, while Europe, Asia and parts of South America use 380 V or 415 V at 50 Hz. "These electrical issues can cause mechanical differences because a 60 Hz motor will typically run at 1,800 rpm, while a 50 Hz motor will usually run at 1,500 rpm, and so ac synchronous motors could be needed," says Mike Litten, controls engineering manager at Cincinnati Milacron (www.milacron.com), Batavia, Ohio, which makes plastic molding machines, extruders and other machines.
To make certain its machines' electrical systems will work properly in other countries, Schneider Packaging Equipment (www.schneiderequip.com) in Brewerton, N.Y., installed a generator at its plant to better check equipment operating voltages and frequencies before shipping. "We previously had a 50 Hz problem with a machine going to Europe, so we decided to do more testing and verification," says Pete Squires, Schneider's vice president.
Sorting Out Safety
Though some national and international regulatory authorities are beginning to harmonize their rules, the most difficult hurdle for machine builders trying to deploy their equipment in other countries remains dealing with safety standards. The largest differences in these standards persist between the U.S. and Europe. Most other international regions seem to be falling in line with Europe's more stringent regulations, and even U.S. builders are pulled in that direction by end-user demands and their own legal departments.
Litten adds that UL and CE are philosophically different organizations because CE is part of the EU goverment, while UL isn't a government entity. As a result, he says, EN 201 spells out which rules builders need to follow and documents other standards that apply, but B151.1 doesn't go that far.
"We just shipped several servo-based case packers to the Middle East, and the client asked for CE compliance," says Robert Hattin, president of Edson Packaging Machinery (www.edson.com) in Hamilton, Ontario. "So, we followed CE's self-certification process, which included reviewing drawings, implementing wiring standards, following hardware requirements, adding guarding and doing it all with CE-mark equipment. The self-certification begins with a risk assessment (RA), in which we identify safety issues, and rate ourselves in each area.”
Likewise, Erema North America (www.erema.net) brings its 906T plastic repelletizers to the U.S. from home base in Austria, where it complies with CE rules. The 906T is controlled by a Siemens PLC and touchscreen PC and also uses Pilz safety switches.
"We already comply with CE, so we mainly had to redo 906T's electrical system to use the 480 V, 60 Hz power in the U.S. and then add the right motors and drives and update some of the Siemens Simatic controls," says Tim Hanrahan, Erema's CEO. "The old version had discrete indicators and gauges, but now our repelletizer has one touchscreen that's like turning the pages of a book. This makes it easy for users to access recipes and archives and dial in temperature and other changes. This means a lot fewer headaches for end users, regardless of where they're located, and the PC's modem allows us to dial in to clients' operations and help solve problems."
Languages and Local Lingo
While English dominates most areas of engineering, machine builders must offer human-machine interfaces (HMIs) that display text in many languages.
However, some builders find that even more linguistic flexibility is needed because local dialects, technical and professional groups, and even individual applications and operators constantly generate new words.
Gloucester Engineering (www.gloucesterengineering.com) in Gloucester, Mass., reports its new Symphonix DCS extrusion control offers several language options, but it also has in-line text editing for customized translations, so users can input words and phrases that best meet local preferences. "For instance, the word 'head' often is used for the end of a barrel," says Paul Brancaleone, Gloucester's software and controls manager. "We call it 'end of barrel,' but now a company that wants to use ‘head' can do so, which could be the best word for its application and the most clearly understood by its operators. Likewise, where we use 'pressure,' another user's local word might be the translation for 'push.' We also tried to make Symphonix more graphically intuitive, so it wouldn't need as much text and translating."
Intelligence Aids International Access
Besides harmonizing standards and languages, ever-more-powerful computing is driving ever-easier programming, configuration, networking and communication functions that help machine builders operate and serve end users in international markets.
Makino (www.makino.com) in Mason, Ohio, reports that its year-old, five-axis V33i-5XB mold machining center is faster and more accurate because of how much intelligence its developers shifted away from human operators and back to the machine and its Fanuc-based Makino Pro 5 control system and Win CE front-end interface. This machining center carefully carves out the $200,000 metal molds that its users supply to injection-mold users.
Because its machines are made in Japan, Makino's engineering group there works with counterparts in its offices worldwide to make sure it's following each nation's regulations. "I've got standards in place with Makino R&D to enforce North American standards and keep them up to date," says James Brown, Makino's U.S. engineering manager. "These include ANSI B151, NFPA 79, CSA and others. Our U.S. engineering group in Cincinnati works with the group in Japan. Makino Europe also has an engineering manager like me. The company's engineering managers in Asia, Europe, North America and South America meet in-person at least twice a year, and we use Go To Meeting videoconferencing as needed."
External Partnerships, Internal Cooperation
One especially useful way machine builders resolve international differences is to form partnerships or joint ventures between firms or among disparate divisions within multinational companies.
Cincinnati Milacron's new Maxima 310 injection-molding machine is the result of a six-year joint venture between the U.S.-based company and its Ferromatik Milacron Europe division.
"In the past, the North American division would design its own update for a machine, and the European division would design its own version, and we'd end up with two models, which created a lot of waste," says Larry Keller, Milacron's engineering manager. "So, our joint project team for Maxima 310 communicated a lot over the past six years. We met twice a year in person and four times per year on WebEx and basically saved a whole set of resources for one division.”
These constant communications also helped the team overcome several tough problems. For instance, when sourcing materials for Maxima 310, they found that U.S. and European sheet-metal suppliers offer their products in different physical dimensions, and so they had to include dual dimensional specifications on their blueprints for each region. Also, because relays, switches, wires and terminal blocks are comparatively less expensive, the team decided to let each division source them independently to save on shipping.
Unique Environment and Requirements
While complying with national specifications and standards can help builders get into a country, there are many unique requirements for installing and operating a device on-site.
For instance, bottling drinking water from a 15,000-ft glacier in Tibet might seem easy, once you get up the mountain, but it's not. Husky Injection Molding Systems (www.husky.ca), Bolton, Ontario, recently helped China-based Tibet Glacier Mineral Water produce plastic preforms—plastic tubes that are later blown into the shape of bottles—for its own brand of water. However, Husky's engineers had to adjust their two HyPET 225 injection-molding machines for high altitude because the user's production facility was 4,800 m above sea level (Figure 2).
"Air density at high altitudes is much lower, which affects head pressure at the hydraulic pumps' suction port," says Michael Stirpe, Husky's inside sales manager for the Americas. "So, we put in a smaller pump ahead of the larger one to ensure the larger one receives a constant source of oil. We upsized the machine's cooling capacity and added larger lines for better heat dissipation because at that altitude the lower air density affects the machine's ability to cool. We also switched to a solid-state hard drive because standard hard drive components often fail above 3,000 m. These newly designed systems are in production and working very well."
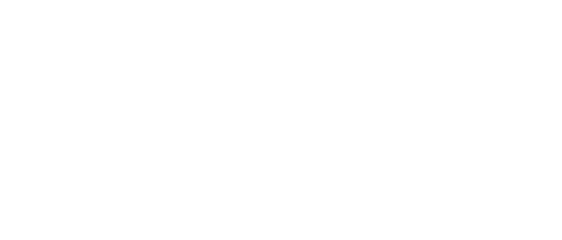
Leaders relevant to this article: