Some futures are better than others. Naturally, the trick with industrial networking, and most endeavors that invest in the future, is to pick the right path now to achieve the best outcome later.
Not easy—especially for users, engineers, system integrators and suppliers trying to cope with the constantly shifting terrain of industrial networking. It's all most folks can do to keep up with the present—or yesterday for many of us. Few, if any, have time to speculate or bet successfully on what's going to happen to industrial networking five or 10 years down the road. Fortunately, to handle present tremors and upcoming upheavals, there is plenty of helpful advice and many useful resources. Ironically, one of the best may be a cold splash of reality, and then a clear-eyed look at industrial networking's recent past as an indicator of its likely future.
Wake-Up Call
"Everyone believes Ethernet in some form will be what all the analog and fieldbus networks will head toward in the future because it's fast, simple, inexpensive and ubiquitous, and because users can just give their devices an address on their network and be done with it," says Hunter Vegas, senior project engineer at Avid Solutions (www.avidsolutionsinc.com), a system integrator in Salem, N.C. "However, despite all the marketing brochures and CEOs at conferences, the process control-related industries still move very slowly. Twenty years ago, 4-20 mA was supposed to be dead because buses were going to change everything in five years. Well, even today, all the fieldbuses together don't add up to more than a fraction of all industrial networks. This is because, if you lose enough instruments and your plant shuts down for a couple of days and you lose $2 million dollars, then the $100,000 you saved on wiring doesn't matter. It's still difficult and costly for fieldbuses to achieve this kind of redundancy, and users still aren't going to walk away from the thousands of hardwired instruments they have in place."
Despite these drawbacks, Vegas adds that some networking protocols, like lower-level Actuator Sensor-interface (AS-i), help reduce costs because they're simple and easy to implement, and they don't require users to do as much engineering as other fieldbuses. He explains that all industrial networks must strive to be almost as easy to use as 4-20 mA if they hope to replace it in the years ahead. "Many instruments and fieldbuses are leaving the average technician behind," says Vegas. "I know a dozen plants where, if a transmitter fails, they have to call in an engineer. In the past, if a 4-20 mA line failed, anyone could go hook up a new one and get the system running."
As a result, Vegas reports that some networking design tools and hardware are becoming easier to use, and this is the direction that users need their suppliers to follow. "For instance, users can adjust AS-i networks on the fly with a lot less pain than before. We also have handheld AS-i readers that are very plug-and-play because they allow us to assign numbers to nodes, punch in those numbers, and immediately get a reading from that particular switch or device. New fittings and blocks also make it a lot more like using 4-20 mA. It's also good that users now can buy fieldbus transmitters and plug in whatever chip they need into that common device. I think we're going to see more common devices like this soon, too."
Likewise, a lot of networking hardware is getting easier to mix, and this will continue, says Vegas. "For instance, you can run Profibus or DeviceNet out to a particular area and use gateway converters to immediately convert to AS-i at your field devices," he says. "Also, the buses are getting easier to deploy because you don't need as many special cards or licenses, and this helps to accelerate their use."
Cooperative, Coalescing Networks
Because of their varied legacy equipment and newly required capabilities, many process applications increasingly need networks and strategies that allow all these controllers and other devices to talk to and interact with each other and—you guessed it—do it faster and easier, too. Maybe comprehensive interoperability isn't too far off either?
For instance, Caeté-Matriz Distillery, part of Grupo Carlos Lyra (www.carloslyra.com.br) in Alagoas, Brazil, recently upgraded its huge sugar and ethanol plant from 4-20 mA/HART to Foundation fieldbus (FF) High-Speed Ethernet (HSE) and Profibus as an alternative in its classified and motor control center (MCC) areas, and used a Smar distributed control system, client-server schema and flexible function block (FFB) software to coordinate and optimize its various installed and legacy equipment and systems. Meanwhile, plant supervision is performed by a GE Fanuc HMI/SCADA system, which uses redundant database servers to communicate with the controllers via OPC in real time.
To integrate its new and existing equipment, Caeté-Matriz's fermentation process uses a Smar controller that functions as a Profibus-DP master and a HSE remote I/O (RIO) at the same time (Figure 1). It controls the fermentation process by automatically injecting defoamers and backwashing the fermentation tank's heat exchangers. In general, these Smar controllers have native and redundant HSE connections that provide twin 100 Mbps connectivity. Because FFBs in HSE controllers provide data between analog and discrete controls, it's possible to use FFBs to create HSE links between controllers and integrate analog and discrete controls.
To exchange data between controllers, Caeté-Maritz Distillery's plant control cabinet integrates Smar's Profibus master HSE RIO, gateway DP/PA and Foundation fieldbus HSE RIO.
SMAR
These fieldbuses enable Caeté-Matriz to locate its PID algorithms in field devices for more reliable and secure control that's closer to their process. Also, once it integrates different technologies, the plant's HSE infrastructure gives users a Web-based HMI that includes the facility's new and existing automation systems and provides trending capabilities for tighter operations control.
PoE or Vice Versa
One of the main forces likely to fuel Ethernet's growth is power over Ethernet (PoE), in which two of the wires in an Ethernet cable are used to furnish power to an application. "I think an eight-port switch can now do 2.5 A, and this level will likely rise in the future," says Avid's Vegas. "This means you can put a block in the field and get power to it without added lines. They're also getting better protected and safer, though they're not at Class I, Div. 2, yet."
Conversely, while some users try PoE, others find they can communicate via their power lines. For example, German brewer and bottler C&A Veltins (www.veltins.com) decided in 2007 to deploy 284 of SEW Eurodrive's mechatronic drive units in a single-line network installation (SNI) on the container and box conveyors serving its 60,000 bottles-per-hour filling line in its new plant in Meschede-Grevenstein. The drive optimizes the interfaces between its motor and gears by directly combining those gears, motor, drive, motion control and communications in one gear housing, which achieves 12-20% better efficiency and delivers similar energy savings, says Rich Mintz, strategic product marketing manager at SEW Eurodrive (www.sew-eurodrive.com).
"To further simplify its network, the brewery's SNI daisy-chained its drive units together by their three-phase power cables, but these wires also use a PowerLAN method to carry the application's high-frequency communication signals," says Mintz. "This meant that Veltins didn't need to install about 4,600 m of 24 V standard bus wiring, and so it saved about 60% on its cable costs. Usually, we're trained to keep encoder and bus signals away from 480 V power due to electrical noise, but applying good modulation with this method ensured that noise was not a problem."
Moving on Time
Because higher-speed motion control needs more speed and data, it's been even slower to emerge in industrial networks than in process and other comparatively slower applications. This too, will change in the next few years.
For instance, carpet sample machine builder Modra Technology (www.modra.com.au) in Warragul, Australia, recently added Ethernet Powerlink protocol for real-time, multi-axis, synchronized motion control on its Mtuft machines, which now can set up and—at 30 stitches per second—produce a new tufted carpet sample in just 20 minutes, which takes at least a day on conventional carpet sample or production machines. The machine holds the web/backing material for the carpet sample in tension on two backing drums driven in ratio gear mode, while two synchronized, reciprocating heads, above and below the web, traverse the material. The needle motor provides the reference signal for all interpolated axes, and the top head uses a large servo for needle actuation, using a driven-spline arrangement to save weight on the head (Figure 2).
Modra Technology's Mtuft carpet sample machine uses Ethernet Powerlink-based motion controllers and servo drives. The machine's top head employs a servo for needle actuation, using a driven-spline arrangement to save weight on the head.
BALDOR
Mtuft machines combine pneumatic and electrical actuation. There are nine axes of electrically operated movement, all controlled by a Baldor Electric real-time motion controller. Seven axes are driven by Baldor ac servo drives and servo motors, using Powerlink for communication between the controller and drives. Five of these axes use interpolation over Powerlink, while the remaining two electrically driven axes use small dc motors. Mtuft's built-in host computer is an industry-standard PC, running the machine control software and NedGraphics' Vision Tuft software for creating new sample designs, which are downloaded line by line via Ethernet to the motion controller.
"Complex, high-speed, multi-axis applications usually involve lots of wiring, mainly on the control side and especially for encoder feedback," says Tim Modra, Modra's managing director. "Over the years we kept an eye on decentralized motion control and strategies to help reduce machine wiring, but we dismissed non-deterministic Ethernet as unsuitable for critical real-time automation control purposes. When Baldor launched its Ethernet-based motion controller and servos for overcoming the real-time data transmission limits of standard Ethernet, but still use standard Ethernet cable between the controller and the drives, we wanted to try them out."
Modra adds that using high-speed interpolation on the two main head drive servos provides a key advantage over conventional mechanical systems. "We effectively have a software calibrator that enables us to put a variable offset into the system. So instead of using precision mechanical gears and cams, we now can calibrate our machines digitally using Baldor's software. This all-electronic approach allows us to create a physically compact machine, helps reduce machine build time and costs and gives us an adaptable platform for future product development."
Securing Synchronization
However, even as digital networks make inroads into more motion-related applications, it appears some of their synchronization methods also will soon move from managing individual machines to coordinating larger production lines and even plant-wide systems.
Though lots of chipping away at legacy hardwiring remains to be done, the most persistent forces likely to influence industrial networking's future are well-known. In the past few years, their presence has echoed continuously through most networking applications and solutions, and they will undoubtedly shape the course of its future. Though they might overlap and fuel each other in some places, these seven main forces include:
- Ever-accelerating power, speed and variety of PCs and computing, which are only rivaled by their ever-shrinking cost and size.
- Simpler and easier-to-use software and hardware tools, which allow more point-and-click configuration and require less traditional programming by users.
- Growing dominance of Ethernet-based protocols, wireless and even Internet-based networking, which continue their migration down from the enterprise levels, and onto the plant floor and out into the field. This will likely push fieldbuses into sub-network arrangements for sensing and operations, while Ethernet runs above with higher-level, asset-management systems, also delivering electricity via power over Ethernet (PoE) methods.
- Increasingly automatic gateways, switches and linking devices that, in turn, enable more automated addressing, polling, updates, alerts and alarms, smart responses, field-level decisions and distributed intelligence.
- Better integrated security and safety functions within their larger data and communications networks.
- Rapid emergence of handheld and other consumer electronic devices such as cell phones, Blackberries and iPods, which are indirectly fueling acceptance among even veteran engineers of both wireless communications and handheld devices on the plant floor.
- Increasing machine-to-machine or "Internet of Things" communications as devices gain a presence on Ethernet-based and Internet-enabled networks. Internet of Things is an informal name for a network of objects or devices that are Web-enabled and often wireless and reportedly can be set up to use these capabilities to form a self-configuring network. The concept was devised by the original seven-university Auto-ID Center research group, which was founded in 1999 and based at MIT.
Openness Needs Security
What would be the perfect accompaniment to all these new and faster interconnections that will be made in future industrial networks? You guessed it again—a big scoop of security.
"Back when most industrial networks were connected only via proprietary protocols, they could rely on ‘security through obscurity.' However, in recent years, Ethernet and TCP/IP have opened them to all of the vulnerabilities faced by office networks, and so they're adding the same security methods used in office networks, and this will only become more important and more prevalent going forward," says Mark Cooksley, product manager for network security at Belden and its Hirschmann Automation and Control division (www.hirschmann.com). "As a result, we're going to see more hardened perimeters around networks, including firewalls and demarcation points that more clearly define IT's jurisdiction and automation's jurisdictions.
These points will have one or more firewalls and DMZs between them and will be part of defense-in-depth strategies that set up protected zones. These zones also will be firewall-based and will either mirror office networks by including written rules for data packet filtering or use PC applications to graphically define rules for setting up zones." He adds that Hirschmann is presently working with Byres Security and its Tofino software and hardware security solution to establish security zones using this graphical method and then download to applicable equipment and participants on the network.
Even wireless is gaining the security it needs to go mainstream in industrial automation. "Robust security standards for wireless networks have been developed and adopted over the last several years, and the early Wired Equivalent Privacy (WEP) security algorithm has been superseded by much stronger and more secure transmission algorithms. Wi-Fi Protected Access (WPA) replaced WEP in 2003 and the more recent WPA2, introduced in 2004, uses the even more secure Advanced Encryption Standard (AES) 802.11i algorithm," says Ben Orchard, Opto 22's (www.opto22.com) application engineer. "Moving forward, these security standards will become more evident to those in the industrial sector, and individuals will begin to let go of their preconceived and erroneous notions that wireless isn't secure enough for industrial applications."
Standards Aid Ease of Use
Besides providing workable security, another crucial step in convincing users to implement modern industrial networks in the future is making them and their equipment as easy to use as traditional tools.
Eddie Cantu, sales product specialist for industrial networks at Cooper Crouse-Hinds' MTL Instruments division (www.mtl-inst.com), reports that his firm also is using Tofino to help users set up and configure VPNs and then make sure their VPN traffic complies with their firewall rules. "A lot of industrial networking tools will become easier as the EDDL-based protocols come together with DTM-based protocols," says Cantu. "This will make a lot of them as simple to use as mainstream software drivers."
In fact, most of the major fieldbuses have coordinated their efforts around electronic device description language (EDDL) for several years. The original partners included the Fieldbus Foundation, Profibus Nutzerorganisation and HART Communication Foundation with assistance from the OPC Foundation, and they formed the EDDL Cooperation Team (ECT). More recently, ECT has been working to welcome in new capabilities provided by the field device tool/device type manager (FDT/DTM) protocol and its FDT Group, again with matchmaking from OPC and its OPC-UA technology method. This latest effort is known as the FieldDevice Integration (FDI) group, and its team members are drafting specifications now.
In addition, easier networking is achieved as different technologies strive to adopt best practices from each other. For example, wireless networks are beginning to take on some of the most useful routing and switching methods of their Ethernet-based counterparts. "We have a new WirelessHART gateway that acts like a router and access point," explains Patrick McCurdy, product marketing manager for Phoenix Contact (www.phoenixcon.com). "It collects WirelessHART data, and then gateways it to wired Ethernet or a wireless LAN, but we don't need a Cisco access point to do it."
Smart, Self-Healing, Biological?
As instruments and field devices gain more onboard data processing and decision-making abilities, and as network routers and gateways learn to circumvent line breaks and even help compensate for failed devices, some observers say these self-healing and dynamically responsive capabilities are beginning to take on an increasingly biological appearance. And at least one area of this new field even has its own acronym to prove that it has arrived—highly adaptive control (HAC).
"Industrial networks are becoming self-healing because users don't want to shut down an entire process if one part of it fails," explains Andre Jordao, Weidmüller's (www.weidmuller.com) network connectivity product manager. "Even on the wired side, this idea is taking off, and so many devices don't need traditional maintenance. So, if you lose one sensor, another can pick up the slack and let you know where the problem is. Many sensors, limit switches, drive banks, valve banks, solenoid valves and manifolds already have built-in intelligence and are on fieldbuses now, and there will be more soon."
The downside to all this terrific smart instrument autonomy is, of course, that users risk losing sight and awareness of what's going on in their processes. "Having control in the field to the point that PIDs run in the valves, so those valves can control themselves, sounds great until you want to shut them down and can't do it and are blind to what's happening in your process," says Avid's Vegas.
"When PLCs came out, all decisions had to go back to a central processor. In the Ethernet world, sensors, variable-frequency drives and other devices are getting smarter and being assigned to make more of their own decisions," says Jordao. "These capabilities make life easier for users, but their potential risks means that better security is needed, including firewalls, locking out unneeded devices and network sections and authenticating all devices on your network to make sure it's reliable and that there are no cracks in it. Luckily, these tools also will get easier in the next few years."
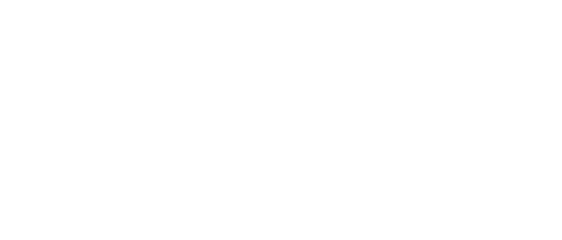
Leaders relevant to this article: