The idea behind EtherNet/IP is to stay with standards and to simplify, says Anatoly Moldovansky, principal engineer at Rockwell Automation, a pioneer of the original IEEE 802.3 specification before it was called Ethernet, and member of the EtherNet/IP Infrastructure Task Group. EtherNet/IP retains the standards specified in 802.3; there are no changes to Layer 1 or Layer 2. There is nothing proprietary, and according to Moldovansky, the move to 1 Gbit technology will use the same standards that commercial systems use. The TCP/IP layers have not been changed, but to control traffic, managed switches often are used. EtherNet/IP apparently is real time enough to handle tasks such as a a 90-ton, 50 ft. long automated coal-shearing machine as it eats through layers of coal underground in Queensland, Australia. “As part of the automation project, we also are introducing some enabling technologies, most notably a high-end military grade inertial navigation systems and ruggedized wireless Ethernet gear,” says David Reid, senior research engineer for CSIRO Exploration and Mining at the Queensland Centre for Advanced Technologies. As bandwidth demands increase, how will EtherNet/IP guarantee any semblance of real-time operation—or hard real time that distributed motion control requires? The answer is CIP Sync, according to Moldovansky, and it has origins in two other standards: IEEE 1588 and IEEE 802.1Q-1998, which helps define timely data delivery. IEEE 802.1Q, though it primarily deals with switches, concerns Quality of Service (QoS). IEEE 802.1D defines these priorities more specifically. For motion control applications, the motion control data is assigned the highest priority. Ethernet Powerlink Slices Time
Ethernet Powerlink technology is what provides high-speed synchronization in real time between the servo axes in the Cookie Capper built by Shelby, N.C.-based Machine Builders and Design Inc. “The machine is capable of making sandwich cookies with placement accuracy of the top piece of ±1 mm and filling weight control within ±1%,” says company president Darryl Mims. “The Cookie Capper is designed to run delicate soft cake, wire-cut and rotary molded cookies that fluctuate in size and shape because of upstream processes that lack adequate control. Servo control synchronizes up to 19 phase-locked axes. Ratios, profiles, and speeds can be changed with the push of a button.”Like EtherNet/IP, Ethernet Powerlink (EPL) is compatible with IEEE 1588 clock synchronization, but it uses time slicing to arrive at hard real-time response that can run multi-axes motion control systems. This, according to Pfeiffer, produces cycle times down to 200 µs with precision of better than 1 µs. Less important time-critical data can be transferred in larger cycles than the basic cycle. This method complies with standard Ethernet 802.3 and can be implemented on any standard Ethernet chip or interface card. All IP-based protocols (e.g., TCP and UDP) can be implemented without modification. Powerlink also provides standard device profiles according to CANopen EN50325-4 for automation.The CANopen interface is new and was needed. “EPL V1 did not have an application layer--it could not communicate with any devices unless the customer or the vendor wrote the interface themselves,” says Bill Seitz, president of Ixxat. “We were the primary developer of the CANopen application layer for CAN bus, so it was natural that we were selected by EPSG to apply the CANopen application layer to EPL. This then became EPL V2, which is the current standard. We are presently working on V3, which will incorporate the IEEE 1588 time stamp feature.”Profinet IRT Builds on Fast HardwareMan Roland Printing Machines is the world’s second largest printing machine manufacturer and global leader in web offset machines. It chose to use Profinet for complete communications within its RotoMan machine (See Figure 1 below).
With Profinet, Man Roland achieved faster throughput in the machine and higher accuracy in motion control than the previous technology. In a company pilot machine, 31 axes are coordinated over Profinet and this can be extended to more than 100 axes without a reduction in performance.
Profinet takes a tiered approach to real time. “We have to differentiate several aspects of performance,” says Ralph Buesgen, networking infrastructure engineer for Siemens E&A. “A CNC machine needs synchronous communication in the range of 250 µs to 1 ms, in comparison to a packaging machine that needs a modularized architecture with the possibility to reconfigure communication between machines. In addition to performance, many other capabilities have to be taken into consideration when choosing an automation network for a particular machine such as support for safety, redundancy, wireless, diagnostics, network management, and connectivity to higher level systems or security.”
According to Jeff Howe, Siemens networking team manager, AMD, Discrete Automation, Profinet IRT extends Profinet functionality to cycle times of 250 µs for 35 nodes of motion control with jitter of less than 1 µs. To achieve this response, it uses ERTEC 200 and 400 chips for two and four-port switches. The switches work by responding to the time-slice technology of the IRT channel, ensuring that systems connections are made precisely at the right moment to pass messages between designated devices.
For real-time communication, Profinet uses standard message formats to IEEE 802.3 with an official Ethertype assigned by the IEEE for Profinet real-time (IEEE 802.1Q). Within the user data, Profinet distinguishes different types of data such as cyclic data or acyclic transmission from one another on the basis of IDs. Four status bytes at the end of the user data determine the device status. Real-time communication builds directly on Layer 2, eliminating the processing times of the higher Layers.
EtherCAT Goes With Hardware
EtherCAT (Ethernet for control and automation technology) is being introduced in the IEC 61784-2 standard, Digital data communications for measurement and control—Part 2: Additional profiles for ISO/IEC 8802-3 based communication networks in real-time applications. The technology also will be integrated in the next version of the international fieldbus standard, IEC 61158.
EtherCAT recently found application in a pilot press project from Schuler Hydrap, located in Plüderhausen, Germany. “With the prior PLC/hydraulic controller-based system for our Profiline hydraulic press line, cycle times better than 5 ms were difficult to achieve,” reports Clement Peters, group representative for control and drive development. “Using an EtherCAT-based system brought cycle times down to 1-2 ms. In addition, the PC no longer required a bus-based card--just an Ethernet card--which brought the price down from the €400-500 range to about €50 [$75].”
Rob Rawlyk, application manager at Beckhoff Automation LLC, says that many of these real-time Ethernet networks have had to strip out the TCP/IP stack because it takes too long to unpack and repack it every time data is sent, for example several milliseconds and several clock cycles. “EtherCAT networks depend on hardware for data exchange,” explains Rawlyk. “Since communication uses a logical (full-duplex Fast Ethernet) ring architecture, the master clock determines the propagation delay offset to the individual slave clocks. The distributed clocks are adjusted based on this value, which provides a network-wide timebase with jitter less than 1 µs.” External synchronization (across the plant) is based on IEEE 1588. “With hardware integration in the slave and direct memory access to the network card in the master, the complete protocol processing takes place in hardware and is independent of the run-time or protocol stacks, CPU performance, or software implementation,” adds Rawlyk. “The update time for 1,000 I/O is 30 µs—including I/O cycle time. Up to 1,486 bytes of process data can be exchanged within a single Ethernet frame.”
SynqNet Simplifies Inspection
Based on the IEEE 802.3 physical layer of Ethernet, SynqNet replaces the venerable old ±10 V analog interface between motion controller and servo drive with a real-time synchronous digital network.
While many people think of motion applications as robotics, webs, and printing presses, another application requiring the same high-speed performance is optical-based inspection. The SJ50 Series II from Aligent Inc. uses and industry-first solid-shape modeling to measure and characterize components and solder joints with lifelike 3D visualization. The machine can be applied at multiple locations in SMT lines, such as in all phases of solder flow and paste inspection. “Unifying the control architecture was a key goal of the project,” says Barry Eppler, Agilent motion control engineer. With the right motion system, one that could be reused for multiple products, we would be able to simplify the product line and reduce manufacturing costs. We qualified several different servo drives and ultimately used CD SynqNet drives from Kollmorgen.” The SJ50 consists of a 600x600 mm gantry mechanism with linear motors and linear scales on both X and Y axes. Inspection speeds up to 21 cm2/s (3.25 in2/s) are typical, and the machine carries its own proprietary lighting system and imaging head.
The network provides the bandwidth required for torque updates to 48 kHz and support up to 32 coordinated axes. Remote diagnostics of motor-drive performance are available, and there is an automatic network configuration and integrity check. SynqNet is built upon openly available industry silicon, and there are no ASICs required to implement a SynqNet design. Configured in a ring topology, SynqNet allows for continuous operation in the event of a cable break, loose connections, or a complete node or multiple node failure.
SERCOS III—Hints of Ethernet
Originally designed as a drive interface in the 1980s, first-generation Serial Real-time Communications Systems, better known as SERCOS, supported transfer rates of 2 and 4 Mbits/s and were used primarily for machine tool applications, supporting more than 400 standardized parameters that describe drives and controls.
According to Peter Lutz, managing director of Interests Group SERCOS (IGS) in Germany, SERCOS III doesn’t use TCP/IP for real-time protocols. “It’s like having two channels: one that is strictly real time with SERCOS, and the only thing compatible with Ethernet is its usage of Ethernet frames, but there’s no TCP/IP because this would reduce its efficiency. The additional channel carries TCP/IP if the user wants it.” Switches aren’t needed, and Lutz says that the nodes behave almost identically to the way they did in the first two iterations of SERCOS. Asked if SERCOS III uses IEEE 1588 for scheduling, Lutz said that it wasn’t necessary because scheduling algorithms had already been built in, and had 1588 been used, SERCOS III would no longer look like the earlier versions.
Modbus TCP—Partner With Real Time
According to a recently released study from ARC Advisory Group, Modbus TCP was the leading industrial Ethernet in 2004—at least in number of units shipped. Modbus TCP is the Ethernet version of the Modbus protocol introduced in 1979.
While certainly a good option for a device level network, Modbus TCP is not geared toward dozens-of-axes motion control, says Rudy Belliardi, motion engineer at Schneider Electric. He adds that when teamed up with a SERCOS-based motion control system, Modbus TCP offers a good supervisory, real-time solution that can be used for configuration, diagnostics, and remote monitoring. Belliardi makes no apologies. “We say use Modbus TCP with motion—not for motion,” he says.
Click the Download Now button below for a .pdf version of the Tables referred to in this article. |
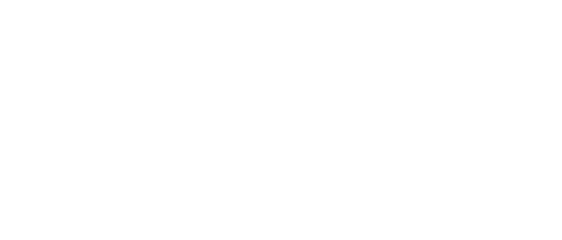
Leaders relevant to this article: