In times of globalization, manufacturing companies are rarely producing in the same country where they have their headquarters. High wages and low shipping costs made a just-in-time production in countries with lower labor costs highly desirable. However, the tables have turned; supply chains seem to be quite unstable. All of a sudden, companies are happy to source locally, be it machine parts or workers.
The costs are still lower than the exploding shipping costs. Having a local supplier means having a trustworthy relationship, which is very valuable in an unstable economy.
Also read: Autonomous mobile robots’ value is more than just speed
However, years of outsourcing jobs have created a labor shortage in the manufacturing market. Companies are turning to automation to ensure profitable and technically efficient production.
A good starting point for automation is familiarizing oneself with robot applications. According to ISO 8373:2012 from the International Organization for Standardization (ISO), a robot is an actuated mechanism, programmable in two or more axes with a degree of autonomy and moving within its environment to perform intended tasks.
Software is a crucial part of a robot; it allows the robot to function properly. In general, there are two types of robots: industrial robots and service robots.
Industrial robots are automatically controlled, programmable devices with three or more axes and serve multiple purposes in industrial automation applications such as handling or welding.
Figure 1: The operational stock of industrial robots worldwide is steadily increasing. (Source: IFR/World Robotics 2021)
Service robots perform all other tasks outside industrial automation. Their design is usually application-specific, and they often come with just two axes.
Promising times for industrial robots
After a challenging year, sales of industrial robots are finally rising again. In its market analysis, “World Robotics 2021—Industrial Robots,” the International Federation of Robotics (IFR) presented an annual growth rate of 9% for newly sold robot units and a 13% increase in worldwide robot units stocked from 2015-2020 (Figure 1).
More than 3 million industrial robots operate globally. In 2020, 384,000 new industrial robots were installed, including 22,000 collaborative robots. Nevertheless, the growth is not distributed equally.
While the markets in Europe and the Americas are declining, Asia is constantly on the rise. Overall, almost half of the industrial robots are used in handling applications (43%). Other fields of use are welding (17%), assembly (12%), clean room (8%), dispensing (2%) and machining (1%).
Although COVID-19 restrictions are still hampering business, the global economy is recovering. As a downside, the scarcity for raw materials and intermediate products increases, which will affect the market for industrial robots.
COVID pandemic fostered service robots
Figure 2: The demand for autonomous mobile robots (AMR) and delivery robots is growing very strongly. (Source: Fraunhofer IPA/Universität Stuttgart IFF/Rainer Bez)
Equivalent to the market figures for industrial robots, the IFR also published “World Robotics 2021—Service Robots.” This market is still growing strongly, despite or maybe because of the COVID-19 pandemic. The division of professional service robots showed strong growth in 2020 of 41% to 131,800 units. This equals a 12% increase in turnover to $6.7 billion. Consumer service robots are widely acknowledged all around the world. Who doesn’t know somebody with vacuum-cleaning or lawn-mowing robots?
According to the IFR, 19 million units were sold in 2020, which equals an increase of 6%. The equivalent turnover increased by 16% to $4.4 billion. During the pandemic, the higher demand for service automation led to new opportunities for service robots.
- The demand for autonomous mobile robots (AMR) and delivery robots is growing very strongly (Figure 2).
- The same goes for cleaning and disinfection—during the COVID-19 crisis alone, 50 companies expanded their portfolios by disinfection robots.
- The trend for individual support increases demand for medical and rehabilitation robots.
- People turned to telepresence more during recent months, which leads to a higher demand for social robots.
- Finally, yet importantly, the need to support restaurant staff and reduce personal contact may lead to more automation in restaurants.
To conclude, sales are rising in almost all service-robot applications. More than 1,000 robot suppliers are in business worldwide. In the future, we will most certainly see more platforms as a marketplace and a focus on safety, security and privacy. Robots will finally enter the open world and interact with non-experts.
Structured planning is key for successful automation
Over the years, the unit prices for industrial robots steadily have been decreasing, while labor cost are solidly on the rise. In a highly automated country such as Germany, the development was very strong: In 2019, the IFR recorded an average unit price for an industrial robot of $36,200, which means a 66% decrease in comparison to 1991.
At the same time, according to the statistics portal Statista, the average salary of a worker in Germany rose to approximately $4,400/per month in 2019, which is an 80% increase from 1991. In the United States, the development of wages was less drastic but the industrial robots are on the rise, as well: The value of demand for industrial robots increased from $1.4 million in 2006 to $9 million in 2021, according to market research from Freedonia Group. This is an increase of 542%.
With this radical change in prices and demand, more companies are using industrial robots in their manufacturing processes. Price is not the only reason: robots have developed over time; now they are more accurate with high-resolution sensors, have a better cycle time, a higher load capacity, make programming more comfortable and deliver safer diagnostics.
However, like the tip of an iceberg, only 20-25% of the costs for a robot system is the robot itself. The majority of the costs for system integration is often overlooked. Once companies have bought the robot system, they often lack the skilled people to integrate and program the robots, which is a real bottleneck problem.
The Fraunhofer Institute for Manufacturing Engineering and Automation IPA addresses this costly part of using robots and is constantly working on solutions. Experts do practical research on industrial topics such as handling and intralogistics, planning and development of robot systems but also work on professional service robotics or household and assistive robots. Collaborating with various companies, Fraunhofer IPA provides concepts, simulations, feasibility studies, developments, specifications, implementation support and even concrete realizations.
Companies often want to know how they can automate their processes. For this purpose, Fraunhofer IPA assists with the Automation Potential Analysis (APA). In the beginning, experts assess the situation. They identify key processes needed for feasible and cost-efficient automation. Following, they develop a comprehensive automation concept together with the manufacturing firm. To secure safety issues, feasibility studies are conducted before the automation scenarios are realized in the production process.
Figure 3: End users realize quick wins and HMLV becomes controllable through automation of automation. (Source: Fraunhofer IPA)
All research done at Fraunhofer IPA aligns with the four biggest emerging trends in the robotics world:
- use of artificial intelligence (AI) and digitalization
- democratization of robotics
- automation of automation
- use of human-robot collaboration and assistive systems (Figure 3).
AI and digitalization
Industry 4.0 and the development of impressive deep-learning applications, especially in the fields of social media and marketing, have brought attention to AI and digitalization. Robotics is benefiting from these trends through better availability of data and better models.
Complex processes, such as sorting flexible or tangled working parts, are very difficult to automate. Robots would need cognitive abilities to solve these problems and sensors to detect shining or transparent pieces.
AI and machine learning (ML) help to automate these processes. At Fraunhofer IPA, scientists have developed the AI-Picking demonstrator: A robot system can detect whether components are caught in the box and, if so, how the robot must move to unhook them. Previous solutions relied on additional sensor technology to detect entangled components, so-called stowaways, or shaking-off movements, which can extend cycle times and damage components.
For automated unhooking, scientists trained deep neural networks in a simulation. Training in simulation is very important for machine learning because the more complex a model becomes the more training data the neural network needs.
To avoid expensive interruptions of the actual production, the neural network is trained in simulations first and then transferred to the real application. As production companies increasingly rely on digitalization and AI technologies, processes that previously could not be automated are becoming economically feasible with robots.
Democratization of robotics
The democratization of robotics describes a disruptive development in which end customers operate robots on their own without needing the system integrator. This is possible thanks to the do-it-yourself (DIY) principle, where platforms act as catalysts. The focus is on processes that are easy for robots to automate and for which standard solution components already exist, but which at the same time have a high savings potential—low tech, high profit.
Typical examples are palletizing and inserting work pieces into processing machines or simple assembly tasks with only one component variant.
The end-customer platforms tend to be successful when robots and peripherals are compatible with each other and have an instant price quote for the configured applications. Modularity and no necessary coding skills—also known as low-code/no-code—enable a minimum viable product, even for nonprofessionals.
The platforms support end customers by building up their robotics expertise through learning by doing. Knowledge and best practices are often shared in communities on the platforms.
Automation of automation
Robots began their triumphant advance in mass production, low-mix, high-volume (LMHV), in the 1970s. Once programmed and set up, robots can often perform their services repetitively for decades. However, the trend is going toward personalized production with decreasing batch sizes—high-mix, low-volume (HMLV).
This individualization needs efficient programming and reconfiguration. Automated processes become infeasible due to tremendous manual efforts for each variant. Automation of automation makes robotics economically feasible for HMLV.
For this purpose, IPA scientists develop different technologies starting from optimized matrix production to automated layout generation, automated risk assessment, automated material flow with autonomous mobile robots (AMRs) and self-configurative bin picking and self-optimization of process parameters.
As a result, this trend enables companies to continue to produce individualized products automatically and thus remain affordable. Unit production costs are on a level with high volumes despite small batch sizes.
Figure 4: The promise of the cobot hype is that processes involving human and robot collaboration will now become much more efficient than would be possible by hand or even by robots alone. (Source: Fraunhofer IPA/Rainer Bez)
Human-robot collaboration as assistive systems
Automation will become increasingly widespread, but some processes, especially in assembly, will not be fully automatable due to technical or economic hurdles. For years, scientists have been researching human-robot collaboration (HRC). The promise of the cobot hype is that processes involving human and robot collaboration will now become much more efficient than would be possible by hand or even by robots alone (Figure 4).
The sales figures for cobots recorded by the International Federation of Robotics since 2017 show that they still have a niche existence with a share of only 22,000 out of 362,000 industrial robots sold worldwide in 2020.
However, the market research company Interact Analysis predicts strong growth figures of 15-20% per year in the cobot segment until 2028.
Besides this, assistance systems are already supporting people on a large scale and with much success and market acceptance. They use robot technologies in perfect symbiosis with humans.
Fraunhofer IPA worked together with the manufacturer Trumpf to develop the Sorting Guide. An image processing technology assists in sorting laser-cut sheet metal components. The AI solution then recognizes the removal process and automatically provides employees with the necessary information for intralogistics.
For example, it clearly displays sheet metal parts belonging together in different colors. Like this, the solution replaces enclosed documents, saves time and helps to avoid errors. Even if full automation is often the long-term goal, technologies that support humans have a greater impact in the short to medium term for many tasks.
The potential applications for robots in production are diverse and expanding practically every day. Addressing the right applications requires either expert knowledge or a structured approach to assess quickly whether a process is suitable for robots. The Automation Potential Analysis (APA, www.ipa.fraunhofer.de/en/apa) is suited for this purpose. Interested companies can also try out the APA themselves as an app in a first step.
New production architectures to be expected
An enormous amount has happened in automation technology in recent years. Innovations around digitalization and AI technologies have become indispensable in production, and their potential will be further enhanced along the four trends. Fluid or metamorphic production architectures are promising concepts for the next big push, in which production resources autonomously reconfigure themselves according to the production order.
About the author
Dr. Werner Kraus is head of the Department Robot and Assistive Systems at Fraunhofer Institute for Manufacturing Engineering and Automation IPA. Contact him at [email protected].
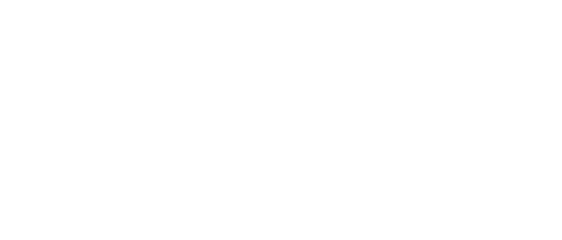
Leaders relevant to this article: