A key requirement for many types of machines and material-handling equipment is the need to detect the presence or absence of a target. The target might be a box, bottle, or other product being moved, or it could be a part of the machinery itself. For several reasons, photoelectric sensors are a preferred technology for many of these applications.
Although photoelectric sensors have been a workhorse technology within industry for many years, there are several possible configurations available, and some operational advancements. Specifiers need to be aware of all the available options to ensure they are obtaining the best-performing versions for their applications.
Photoelectric basics
PE sensors represent one type of technology within a much larger family of discrete object sensors. Other sensor types may use mechanical contact, electromagnetics, sound or other physical properties to provide on/off object and material sensing. But PE sensors are popular due to several advantages:
• non-contact—prevents the sensor from being damaged and the target from being marred
• range—allows objects to be detected at a distance, whether or not the object alignment or position is tightly controlled
• detection flexibility—most kinds of materials can be detected, and a few versions are available to provide optimized sensing for an application.
• red light-emitting diode (LED)—commonly used for many applications, these emitters produce a visible spot or beam, which helps users with alignment
• infrared LED—this type is invisible to the human eye, making it harder to align than other styles, but it efficiently generates a usable light frequency with little heat generation and with less susceptibility to nuisance dust as compared to red LEDs
• red laser—lasers provide much better light coherence due to a tight beam diameter, with a longer range than other types. Lasers are excellent for precise small-part detection, but they are the most expensive version, can be interrupted by dust or other contaminants, and need to be arranged so they do not affect the eyes of plant personnel.
• through-beam—consists of separate emitter and receiver modules, which are commonly arranged on opposite sides of the target travel area. These offer the longest detection distances among PE sensor types, and they reliably detect non-transparent objects of any type. However, they require more installation wiring, and they must be maintained in careful alignment. They are best used for detecting targets such as boxes on a moving conveyor.
• polarized retro-reflective—similar to through-beam, but the emitter and receiver are combined into a single device, and a passive reflector is installed on the opposite side of the target travel area. The emitter polarizes the light in one direction, and the reflector changes the polarization by 90°. The receiver only responds to the changed polarity reflection, which allows these PEs to work reliably, even with reflective/mirrored targets. They are best used in applications where through-beam could be used, but simpler and lower-cost sensing is desired.
• diffuse-reflective—this type also combines emitter and receiver into a single device, and it is even easier to install and aim because no reflector is needed. However, they are affected by target color and surface reflectivity, and they only provide a short detection distance. Diffusive-reflective sensors are best used for consistently detecting known types of objects, such as a standard box on a conveyor, or hands underneath an automatic water faucet.
• background suppression (BGS)—this type combines one emitter and two receivers. One receiver is “tuned” to recognize a consistent background, such as a wall, which is effectively “suppressed” as part of the sensing signal. The other receiver detects any object passing between the background and the sensor. The result is that small differences can be detected, without negative influence due to the target material or color, but the detection distance is short. These are best for detecting smaller targets within a compact geometry, such as detecting parts like printed circuit boards moving through handling equipment.
For best flexibility, designers should look for PE sensors with a mode function switchable between dark-on and light-on. Dark-on sensors provide an output signal when light is blocked, and light-on sensors provide an output signal when light is detected. Designers may need one or both types, depending on the automation logic and other application characteristics.
Other features and details
PE sensors can be hardwired to perform various functions, but they are most commonly connected to inputs of programmable logic controllers (PLCs) or other microcontrollers associated with machinery, equipment and automation systems. Specifiers need to review the following considerations as they select the best product for the application.
Form factor: Some PE sensors are offered in a barrel configuration, but the most common form factor is a rectangular device. Compact sizes, with various mounting bracket options, are a benefit for most applications. Most users prefer to standardize on models with at least an IP67 rating for resistance to dust and water, making them suitable in factory and machine environments where those contaminants are likely to be present. For best durability in harsh conditions ranging from refrigerated equipment to high-temperature machinery, designers should ensure devices can operate in a temperature range as wide as -30 to +55 °C.
24 Vdc PNP and NPN: Most industrial applications use low voltages ranging from 12 Vdc for vehicles up to 24 Vdc for equipment, so a PE should work over these ranges. PEs are typically three-wire devices, supplying +Vdc, 0Vdc and returning an output signal. Positive-negative-positive (PNP) devices, where the +V is switched on and off to the output, are most common in North America. Negative-positive-negative (NPN) devices, where the 0V is switched on and off to the output, are more likely to be used in other parts of the world. Designers should ensure the selected product lines have both styles.
Wiring: Depending on the installation, designers may choose PE sensors with built-in pigtail cables ready to run to a nearby junction box, or standard M8 four-pin connector models ready for use with associated connectorized cabling. The latter is a little more costly, but it is easier to install and maintain.
Marking: Traditionally, industrial devices have used labels or other printed markings. For the best paperless and environmental-friendliness of a modern device, users can choose PE sensors that are marked with a durable laser method and include a QR code, which can be used to access browser-based instructions using a mobile device, such as a phone or tablet.
Detection distance: Each PE sensor vendor will supply a table of device detection distances, which vary based on the model and technology. Generally, users benefit from device families offering the widest possible range of detection distances.
Response time: The response time of a PE sensor is an often-overlooked specification, but it directly affects the rate at which targets can be detected and how quickly the automation system can act. Standard devices have often provided a 1.0 ms response time, but more modern versions using updated application-specific integrated circuits (ASICs) have reduced this to 0.5 ms, allowing reliable detection of small and fast-moving objects.
Specialty features: PE sensors are often called upon to work in environments with high levels of dust, chips and even mist, all of which can lead to false signaling. To combat this situation, some suppliers offer an air-blower accessory unit that keeps the sensor detection surface clean, maintaining performance even in challenging environments.
More application support
For robust and reliable discrete object detection, PE sensors are a proven technology for many applications and industries, such as:
• machining equipment
• material-handling and conveyor systems
• packaging machines
• food-and-beverage manufacturing
• robotics.
Bruce Fink is a product marketing manager at IDEC and responsible for control components including sensors, relays, power supplies and LED Lighting. His career spans 34 years in industrial controls and 7 years’ experience with IDEC.
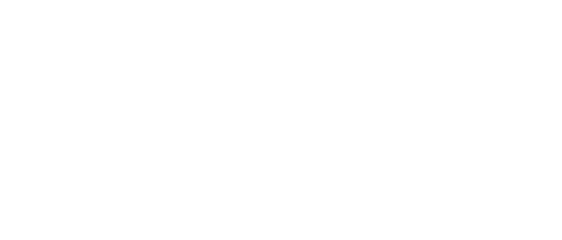
Leaders relevant to this article: