Machine builders and manufacturers across industries need to meet demands for greater throughput while increasing functionality, such as track and trace, customization down to lot size 1 and greater implementation of IIoT and Industry 4.0 concepts. Dynamic motion control solutions, such as the eXtended Transport System (XTS) from Beckhoff Automation, can help to achieve these goals by leveraging mechatronics and software-based changeovers.
The U.S. launch of XTS this year coincides with the 20th anniversary of Beckhoff USA. The XTS is truly a milestone, but it is just the latest success in a long line of PC-based automation technologies backed by an efficient and effective engineering team in the United States.
Jeff Johnson, mechatronics product manager for Beckhoff Automation, answers important questions machine builders have about XTS and key differentiators for selecting linear transport systems.
JEFF JOHNSON
Mechatronics Product Manager, Beckhoff Automation
A: In general, it’s a linear motor that drives in a circle—that’s the combination. The benefits of both motion types are possible without limiting either. The XTS comprises motor modules, guide rails and movers. The track configuration is extremely flexible, enabling straight, open segments, as well as circles, rectangles, S-curves and custom shapes. This minimizes space requirements and can reduce machine footprint 25-50% depending on the application. The wireless movers glide along the track in groups or alone, and they can be automatically monitored and adjusted independent of the others.
Some real-world examples include assembly, bag filling, inline package assembly, product stream sortation and synchronization, and automated inspection using machine vision systems. In this last case, the movers can speed up between stations, pause and undergo manipulation beneath the cameras without halting other processes.
Q: Regarding the control system, where are the drive, electronics and feedback devices?
A: As a true mechatronic system, the power electronics, communication and mechanics necessary for operation are integrated directly into the XTS. The system does not need additional drive electronics or amplifiers in separate electrical cabinets. Electromagnetic coils in the motor modules generate propulsive forces with magnetic plates inside the movers, enabling speeds of 4 m/s and acceleration up to 100 m/s2. The movers contain a mechanically robust encoder flag that continuously communicates its position to the motor modules with high precision. The movers absorb and compensate for attractive forces on both sides to provide highly dynamic motion control with extremely accurate positioning.
Unlike other linear transport systems, the XTS does not require cables to be daisy-chained or run to each individual track segment. Every motor module plugs directly into the next to share power and communication via EtherCAT industrial Ethernet. Options for +/-22.5°, 45° and 180° modules combined with reduced cabling offer greater flexibility and customization to achieve the desired track design with minimal footprint.
The only additional requirements are a PC-based controller that serves as the EtherCAT master and TwinCAT 3 automation software for the programming and runtime of the XTS.
The eXtended Transport System (XTS) features customizable movers, guide rails and motor modules, with flexible, dynamic control via EtherCAT and TwinCAT 3 automation software.
Q: How do EtherCAT and PC-based control technology factor into XTS performance?
A: EtherCAT and PC-based control from Beckhoff are foundational to the success of XTS. EtherCAT provides real-time, deterministic communication that ensures movers transport parts or tooling to the correct position at optimal speeds. This translates into exceptional precision, energy efficiency and heat reductions. Two tracks can even work together simultaneously, when stacked on top of each other to carry the top and bottom of a part or pinch together to open a bag under a filling station. Harnessing the communication flexibility of EtherCAT, the mechatronic XTS can also work in concert with other systems, even those networked over other industrial Ethernet protocols and legacy fieldbuses.
Beckhoff offers numerous industrial PC (IPC) options that are well-suited to the XTS. The IPC performance level can be scaled to suit track length, complexity and the amount of other processes and systems that are in the overall machine control architecture. However, one of the keys to unlocking the significant benefits of XTS is in the software.
TwinCAT 3 offers a standard framework with built-in software libraries and preprogrammed functions, such as station-to-station and load applications. Intuitive programming via IEC 61131-3 and computer-science standards make it easy to get started on a new system. The software treats each mover as a normal servo axis with built-in collision and jerk avoidance, automatic buffering and greater track-and-trace capabilities. While mechanical components are typically obstacles to rapid product changeovers, software addresses this challenge for XTS, enabling greater implementation of Industry 4.0 concepts, including lot size 1 production.
Q: What specific mechanical design and control methods make XTS better than traditional approaches?
A: XTS provides greater flexibility, adaptability and throughput than traditional methods, but, most importantly, it does all this with fewer components. Beyond machine footprint reductions, XTS eliminates expensive components, such as chain drives, actuators, rotary indexing tables or multi-station conveyors. In addition, the XTS reduces maintenance requirements. The motor modules contain no moving parts and are therefore not susceptible to wear, unlike previous options. The rollers on the individual movers are equipped with a particularly wear-resistant synthetic running surface. The lifetime of the rollers depends on the payload.
The convergence of electrical and mechanical technology in the XTS has yielded proven, real-world advantages in the field. However, because this system incorporates expertise from multiple engineering disciplines, machine-builder OEMs should make sure that both mechanical and electrical engineers are involved from the very beginning of the design process to ensure the highest possible success of the application.
For more information about Beckhoff Automation and the eXtended Transport System, visit www.beckhoff.com/xts.
Control Design Newsletters
Latest from Sponsored Content
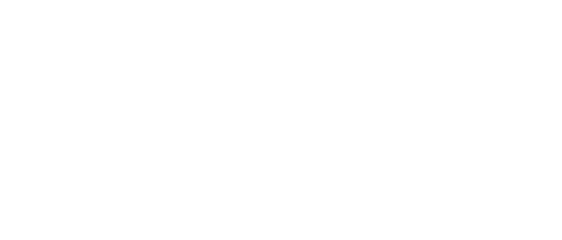
Leaders relevant to this article: