Process Description
Components and System Functionality
The IDEC components and the Ethernet capability of the FC5A-D12S1E was requested by the customer for size and function. They needed to conserve cabinet space, and most important, remotely monitor the sorting system. Down-time is not acceptable and prevents them from meeting critical on-time commitments. With the ability to remotely monitor and restore service, they can expedite troubleshooting and improve system restoration response time. In critical situations, a vendor utilizing the Ethernet function has the capability to remotely access the PLC and/or HMI to assist with troubleshooting, minimizing down-time.
The IDEC system is controlling and monitoring over 500 feet of sectioned conveyor, including accumulation. It is controlling variable speed conveyors from 0 to 360 fpm merging and diverting cartons to four different lines. Twenty-three IDEC sensors monitor and control the digital input functions of the system. This includes triggering for divert position, monitoring line full conditions, and signaling to stop traffic when needed.
PLC Process Design
- 1 IDEC PLC……………………………… Model # FC5A-D12S1E
- 1 IDEC HMI……………………………... Model # HG3G-AJT22TF-B
- 3 IDEC Output Module…………………... Model # FC4A-T08S1
- 4 IDEC Input Module……………………. Model # FC4AN08B1
- *1 IDEC Analog Input Module …………… Model # FC4A-J8C1
- 2 IDEC Analog Output Module………….. Model # FC4A-K2C1
- 2 IDEC Analog Output Module……..…… Model # FC4A-K4A1
- 1 IDEC Power Supply……………………. Model # PS5R-SF24
- 1 IDEC Power Expansion Module……….. Model # FC5A-EXM2
- 12 IDEC Contactors……………………….. Model # YC1A-9D24
- 1 IDEC Switch, LED…………………….. Model # ASLW200-Green
- 1 IDEC E-Stop…………………………… Model # AVW401-R
- 23 IDEC Sensors…………………………... Model # S6-1-A6
- 6 ABB VFD Drive……………………….. Model # ACS355-03U-02A4-4
- 6 ABB VFD Drive……………………….. Model # ACS355-03U-04A1-4
- 1 ABB Circuit Breaker
- 6 SMC Solenoid and Valve
* One Additional module is on order to be installed week of 10/30/11
Twelve IDEC 480 VAC/3 PH Contactors are positioned between twelve ABB VFD's and the A/C motors. They are controlled by the PLC digital outputs to start and stop all sections of the conveyor.
Six IDEC Analog Modules control the analog input and output functions. The output modules control the variable speed functions of all the A/C motors to speed-up or to slow-down as production volume changes. The input modules perform monitoring functions which include Current draw, KWh readings, Voltage readings, Temperature, etc. of all motors. The values are displayed on the HMI and/or a remote located PC via the Ethernet function. One IDEC HMI monitors the health of the overall system and provides means to make value changes when necessary.
System Functionality (Refer to workflow diagram for graphic details below)
The High Speed Packing Sorter is designed to move boxes from piece part packing stations to four separate taping stations all in parallel orientation to one another. Each station is set up for box content inspection, bar code scanning, manual dunnage insertion, automatic top & bottom taping, and automatic top label application. From there, cartons proceed to a shipping sorter where they are routed to an appropriate bay for shipping. As filled cartons first enter the sorting system, they will merge with oncoming accumulated traffic, if present, keeping the appropriate spacing between cartons for downstream sorting. Each carton will pass the first sensor in the cycle which will assign a sequence number 1 thru 4 for each corresponding line. As a carton reaches its designated line, another sensor detects the presence of that carton and diverts it off the main line via pneumatic controlled rollers. The PLC FIFO function is utilized to keep multiple cartons designated for the same line in sequence order. This also keeps other cartons from diverting off to the wrong line. Each line has two sensors for partial and full indications. When a line backs up to the partial sensor, the system automatically re-routes destined cartons to the next available line keeping the work flow even. When all lines are backed up to the partial sensors, each line opens up again as normal to accept cartons until conditions change. This cycle continues to keep all lines equal.
When a line completely backs up to the full sensor, the system automatically re-routes destined cartons to other available lines. When the full condition clears, it will once again start accepting cartons. This cycle continues for each line.
Via a remote switch, the operator has the ability to enable or disable their line when necessary. When a line is disabled, boxes are automatically routed to the remaining available lines. If all lines are backed up to the full sensors, in-line cartons on the main conveyor waiting to divert will simply by-pass the assigned destination continuing on to the overhead accumulation conveyor. The cartons will travel approximately 160 feet, decline down, and return to the main conveyor to start the sorting process once more. The system counts all cartons that enter the accumulation area and removes them from the count when they return to the main conveyor for sorting. At any time, a supervisor can access this information from the HMI.
The accumulation conveyor has three zones that the system monitors. As each zone fills to the next, they will slow down or shut off while maintaining carton position. If all lines are backed up and all zones are full, the system will shut down all overhead conveyors and slow down the main and divert lines. If product does not move at the taping stations for 5 seconds, the system will shut off all motors and wait for product movement before starting up again.
The system monitors operator throughput for each line in 5 minute intervals. Based on the throughput, the conveyor will match the pace of the operator. This function conserves power and keeps the conveyor from unnecessary start and stop operations.
The HMI has four major screens to control and monitor the system. The Main screen is a graphical representation of the complete sorting system with Icons depicting the control components. While components are in a rest or off state, they show up red. When their state changes to on, or momentarily energized, the color changes to show that action. As product travels around the conveyor, each input and output will change color to indicate whether a carton has stopped, passed by, or has been diverted. The graphics screen also provides information on the control components by simply touching the Icon you want to review. The Icon will blink, while maintaining its condition, to indicate that it is the one you are viewing. The information will pop up on the screen and includes: Label name, PLC I/O number, Wiring locations, Manufacturer, Model number, etc.. For the motors, it includes all plate information. When done, simply press the Icon again to return to normal status. One screen controls the speed of the conveyors. The logic is written to show and set speeds in fpm. It includes set points and compensation parameters to govern the maximum speeds of each conveyor section to control automatic speed variables between them.
Features and Benefits of using the embedded Ethernet MicroSmart Pentra
Utilizing information provided by the VFD's, and the PLC analog inputs, the HMI displays the health of each motor and components they control. The information includes Current draw, KWh of operation, Temperature, and Voltage readings. This can be used by maintenance to determine if a motor needs service, bearings need changing, etc.. The KWh history can be used in cost analysis to apply or improve schedules for preventative maintenance.
All this can help in reducing power consumption, prolonging the life of the equipment, and as a result, save money. Another screen is used for pre-sets, compensation settings, and display of critical operating registers. In addition, two other screens are used to troubleshoot I/O on the system. One for digital I/O and one for Analog I/O. Pilot lights show status changes of all the I/O to verify functionality.
All of the control systems and functions on the Taping Stations are IDEC PLC controlled. All four of the printer applicators that apply the labels to the top of each carton have the IDEC Web Module integrated in the control modules. Phase two of the High Speed Packing Sorter project will incorporate these systems via the Ethernet for enhanced monitoring and troubleshooting.
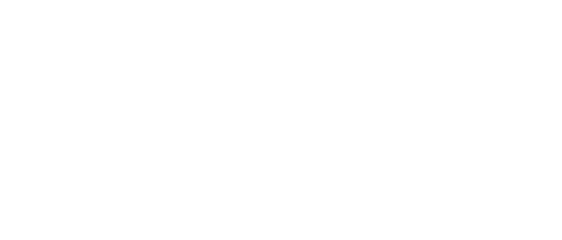
Leaders relevant to this article: