Joe Feeley is editor in chief for Control Design and Industrial Networking. Email him at [email protected] or check out his Google+ profile.
Shifting energy equations. Increasing environmental regulation. Accelerating demand for larger, multi-use ships. When it comes to designing high-performance, cost-effective diesel electric vessels, today's shipbuilders face daunting challenges. For each new challenge they face, they must find a solution that can withstand the rigors of a marine environment.
This week at the Marine Industry Forum at Automation Fair, presented by Rockwell Automation in Houston, marine industry professionals offered insight into industry trends and best practices that help drive efficiency, flexibility and productivity across a ship, address current environmental demands, and discover how to lower total cost of ownership, whether it's a private fleet or Navy transport vessels.
SEE ALSO: Making Permanent Savings Through Active Energy Efficiency
"The pressure to innovate is ever-present and it's growing," noted forum host Mike Tangora, business development manager, Rockwell Automation. "There are demands for constant change from all around the marine industry. The U.S. energy revolution in progress is changing traditional shipping route constraints; ports that until recently were receiving energy supplies are now exporting energy. The entire U.S. shipping distribution network is being redone in the midst of a renaissance of private American shipbuilding."
Tangora noted that oil exploration is heading into ever-deeper waters and will require larger- capacity oil and exploration and production vessels, while at the same time the cost pressure on traditional government programs is growing.
Forum speakers also made it clear that cost and performance pressures don't stop outside the gates of the U.S. military. Similar performance pressures are found there as well. "The Navy's platforms are getting older," began Johnny Walker, Capt. U.S. Navy (Ret.), and president, Thor Solutions. "They need to get to the full service life that taxpayers paid for." Thor Solutions is a technical consulting group with a range of acquisition, program management and engineering services centered on surface ship and combatant craft maintenance, training, logistics, warfare assessment, machinery controls, environmental and safety sectors within the defense and Homeland Security domains.
"It was the risk of a legacy system and the consequences of failure." Johnny Walker, Capt. U.S. Navy (Ret.), and president, Thor Solutions, on the U.S. Navy's motivations for overhauling the control systems on its LSD-41/49 Class ships.
In early 2005, the Navy faced declining control system reliability and obsolescence in its twelve LSD-41/49 class ships, but was unable to fund replacement. "These are the ships that carry armored landing vehicles to the beach, the first ones in," Walker explained. "The heavy stuff is on the horizon waiting. If you don't have that ship that puts in the first set of armor, nothing happens. This can be a single point of failure for an operation."
The Navy embarked on the implementation of a distributed PLC-based advanced engineering control system (AECS) for these ships, based largely on ControlLogix architecture from Rockwell Automation. Now nearing completion of its few remaining installations, LSD AECS includes new subsystem controls for propulsion, electrical power management, steering and an on-board trainer (OBT). The result, Walker reported, is an energy-efficient, low-cost solution providing lowest total cost of ownership, and more dependable performance.
"Somebody asked me, what led to the decision to upgrade and refit the control systems on the ship," Walker continued. "It was the risk of a legacy system and the consequences of failure," he said, citing personal experience with a controls malfunction during an already dangerous refueling at sea operation.
The expected service life of these ships was at 40 years. "It started out at 30, then went to 35, and the next year they wanted us to make it 40, and today it's at 45 years," Walker recalled. "It's designed service life is 30." He pointed to the new installation that included Allen-Bradley Logix PACs, PanelView HMI and PowerFlex drives from Rockwell Automation, and new AC motors as the critical elements in ensuring the performance of functions such as crane operation that were single points of failure elements.
Environmental Pressures Loom
Along with cost pressures, new regulations governing seafaring pollution limits on the marine industry mandate reductions in sulfur-containing fuels and NOx pollutants. The marine industry, in similar fashion to other land-based industries has been developing NOx reduction technologies such as fuel injection and combustion enhancement, exhaust gas recirculation (EGR) and selective catalytic reduction (SCR). But these technologies face unique limitations, given the typical quality of marine diesel fuels and the extreme operating conditions they face.
"Up until 2000, marine exhaust emissions were completely unregulated," reported Philip Wasinger, vice president, new equipment, MAN Diesel & Turbo North America. One of the alternative fuel choices is a dual-fuel engine technology that uses liquefied natural gas (LNG). "Natural gas is the only fuel available today in great quantities and excellent prices, but it can only work for ship applications in a liquefied state, stored at -200 °F," Wasinger explained. "That means it has to be contained in a cryogenic vessel with a vaporization system for delivery to the engines. While ships that transport LNG already have some of this required infrastructure design, it could be a problem on smaller ships."
However, Wasinger noted, the environmental benefit is significant. "Compared to diesels, an LNG-powered engine would produce 20% less CO2, 85% less NOx and eliminate more than 99% of the SOx and particulate matter found in shipping-grade diesel fuels." Hardware requirements are not insignificant with this approach, Wasinger added. "The fuel delivery system could cost more than the propulsion system, so these are areas of cost we're looking to reduce." He pointed to Tote Shipping's first non-transport, LNG-powered merchant ship, of which several are on order, as the first wave of possible things to come.
Regardless of what emissions levels a merchant ship might achieve, the monitoring and reporting requirements will be far more likely to catch offenders than in the past. Ship owners and operators will soon be required to meet the emissions reduction and monitoring requirements of the International Marine Organization (IMO) and new rules of MARPOL 73/78 Annex VI global regulations.
"People don't appreciate how many ships are crossing the oceans," said Joseph Miller, global technical consultant–environmental at Rockwell Automation. "It's estimated that from 20,000 to as many as 90,000 ships are crossing at any one time."
Miller discussed the use of the company's SeaPEMS, a software-based continuous emission monitoring system (CEMS) for cost-effective monitoring and compliance reporting. "A lot of new technologies to control emissions are being installed on ships," he said. "The problem is knowing that it's all working properly and being maintained at sea."
The SeaPEMS system doesn't just measure the smoke. It's monitoring "the processes that make the smoke," Miller said, explaining that the system monitors variables such as injection rates of the urea going into the SCR, how fast the crankshaft is turning, bearing temperatures — many things that wouldn't be looked at by an environment monitor. The system should hold up better as well, Miller continued, since it has no moving parts, no spare parts requirements and no calibration gases.
It's tamper-proof as well. "The model is locked down," Miller said. "If someone tries to tamper, we get an email. Also, for these systems, the requirement is that it must be up and running 95% of the time an engine is running and be accurate to +/- 20%. We tend to be around +/- 7%, and that improves to around 3% after a year or so of operation. It also reports if it's been taken offline and the operator will have to explain why."
Miller says the system has been proven in more than 2,000 installations on land and off-shore platform applications.
Power Source Selection
Using electro-mechanical actuation (EMA) technology coupled with modern, variable-frequency drives can help lower energy demands, increase operational effectiveness and reduce overall logistics costs, reported Clyde Thomas, systems business program manager at Exlar, which supplies electromechanical linear and rotary actuation products to a wide range of industries and applications. "By accommodating industry trends such as energy efficiency, simplified connectivity and higher machine intelligence, EMAs can be an effective technology to address the challenges faced in supplying, using and supporting today's modern marine and naval platforms," he said.
Thomas pointed out that there are still a lot of companies that haven't really started. "Some 40% of industrial actuation applications haven't taken energy-efficiency into account, and more than 50% don't deploy any level of smart motor control," he noted.
Thomas presented the pros and cons of using an electro-mechanical solution as compared to using hydraulics or pneumatics. He pointed to a study produced by UNB-Kassel in 2012, which compared the energy efficiency of the three choices. "It was a pretty basic setup of a mechanical weight-lifting of a 1,000-Newton force through a 150-mm stroke at a 1.7-second cycle rate for a number of hours. Based on the test results, with the electric option as the baseline of 1 kWh, the pneumatic system consumed 10.3 times more energy; the hydraulic system consumed 4.4 times more energy. The conversion of energy to work for the electric option was 90%, compared to 77% for pneumatics and 57% for hydraulics."
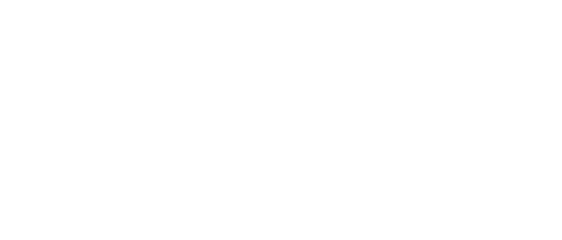
Leaders relevant to this article: