"We provide a lot of after-sales support for our machines. One of our headaches is control circuit (24 V) protection, particularly identifying and troubleshooting blown circuits. The other part of this that's becoming a pain is stocking and supplying lots of types of fuses and circuit breakers. We know we can justify the extra costs for both our customers and ourselves if we migrate to electronic circuit protection. How do we make that case to our customers?"
—From June '13 Control Design
SEE ALSO: Electronic Circuit Protection Technology Minimizes Factory Downtime
Answers
Here's the Case to Make
It sounds like you're experiencing all the common pitfalls of traditional 24 Vdc circuit protection from breakers or fuses that have been adapted to a control-level-sensitive world. Justification to make the leap to electronic circuit protection is easier than you might think. Consider the downtime costs associated with a tripped circuit. First, there's recognition of a problem. Is it in a cabinet? Which circuit? Where on the circuit? Will the breaker reset, or do I replace the fuse only to have the same problem again when the resistance in the wires reaches a temperature or current draw with enough impact to fault again? How many people need to be involved to diagnose and repair the problem? All this, and you're still where you were in the beginning.
We need better accuracy now, so we're changing to digital panel meters from our trusted analog panel meters. As we view options, it looks like we could really reduce the number of different meters we buy by using higher-end, digital panel meters that offer optional expansion cards with a lot of extra functions, maybe to the point of needing fewer controllers. But it puts us in expertise and cost areas where we haven't been before. Anyone care to share experiences about this possibility?
Send us your comments, suggestions or solutions to this problem.
Sell this to your customer: Mr. Customer, our newly designed control cabinet uses state-of-the-art protection for 24 Vdc circuits. This means better protection for the devices on the circuit, less heat on the cables before a fault is detected, a notification of a fault or warning of potential overcurrent before a fault happens, and fault detection in milliseconds. Visual indication of the affected channel is possible through an HMI or other device, and you can test and reset without opening the cabinet and disturbing the wiring inside.
Sell this to management: Fewer service calls for "ghost" short circuits, better monitoring of circuit load, reduced inventory, reduced wiring, fewer opportunities for the user to open the cabinet and disturb the wiring.
As for the hard costs to the initial build, you should quickly realize savings in assembly, procurement, and inventory costs, which make the switch to electronic protection the easy and right choice. Offer protection and detection not reaction and inspection.
Aaron Henry,
marketing manager,
Murrelektronik
Complexity Brings Vulnerability
The use of analog and digital I/O signals have multiplied greatly, as discrete systems and processes become more integrated and compact. Integrating separate functions and controls, and reducing overall size of the control system is a very desirable goal. However, by doing this, the control device and process becomes very vulnerable to damage from voltage transients (surges). Because the modernized devices perform more functions, the impact is greater overall system interruption. To ensure system reliability, proper implementation of surge-protection devices (SPD) will improve signal integrity greatly, protecting both devices in the field and in the control panel.
Best practice for mission-critical applications is to protect all wiring that leaves a controlled environment greater than three meters. A controlled environment should be considered a safe place for controls. A controlled environment would be an RTU control panel enclosure or perhaps a room such as a SCADA room. The only way to assure that an RTU or SCADA structure remains a controlled environment is to install appropriate SPDs on all galvanic wiring that enters or leaves that space. If not implemented, these wires are potential points of entry for damaging surge events. If this happens, then technically the space can't be considered as a whole, controlled environment.
Fusing and circuit breakers don't protect against voltage surges, only over-currents that originate on the load end of a circuit. SPDs protect against over-voltage transients. SPDs have extremely fast response times, normally around 25 ns. This is critical as surges are extremely fast. A fuse or circuit breaker does not come close to the performance or speed of an SPD.
The job of an SPD is to be invisible to the circuit, and at the same time, be a voltage-activated switch that diverts the damaging voltage surge to ground, away from the circuit that is to be protected.
David Torres,
product marketing lead specialist,
Phoenix Contact
Seeing Is Believing
Start by assigning a value to the time savings electronic protection devices yield, especially if any after-sales support might incur additional fees (e.g., holidays, evening hours, travel expenses). Obviously, the customer's bottom line is tied to how quickly they resume operation. Also, the more variables you can streamline in your own day-to-day operations, the more competitive you become. For instance, four- and eight-channel electronic circuit breakers (ECBs) can be configured easily up to 10 A per load. This customization enables you to serve multiple customers with one unit, eliminating the need to stock multiple devices and sizes.
Advanced devices like our ECBs have an active output/channel serving as a watchdog. Direct digital signal processing is used for the outputs, so output 1 is linked to an isolated signal contact on select ECBs. Via the ECB's free configuration/visualization software, the signal contact can be programmed to cover multiple fault conditions and diagnose faults. This dramatically simplifies in-the-field troubleshooting. Once a tripped channel is identified, it can be reset via on-unit keys or remotely reset via PLC. This can save the customer (and your service technician) an inordinate amount of time and travel-related resources.
SEE ALSO: Make Circuit Protection Easier
Beyond expedited troubleshooting via visualization and fault diagnostics, the ECBs' free software provides control of Active Current Limitation (short-circuit current limitation at 1.5 times rated current). A convenience traditional fuses and circuit breakers can't match, it prevents a voltage drop in one channel from impacting others during a short-circuit. End-users no longer need to worry about one fault tripping an entire system, the potential loss of production data, and any time-consuming reprogramming. Further, customers can specify current or tripping characteristics of individual channels for precise protection — rated currents are set in 1 A increments for each channel. As part of the feature, power-good threshold and fuse-trip times are also adjustable, providing faster response than typical fuses and circuit breakers.
Often, the lower initial purchase price of mini-CBs and fuses is offset by troubleshooting. Productivity also can be compromised because just one tripped load can trigger a system-wide shutdown that impacts the bottom line. The case is clear: these older technologies simply can't match the efficiencies provided by an ECB.
Michelle Goeman,
product manager,
Wago
CAP the Problem
One short-circuit load fault could be a disaster for a multi-load dc system supplied from a switch-mode power supply. Even with individual circuit breakers fitted and rated to protect each load, the fault can occur so fast that, without additional protection, the entire dc voltage supply could collapse. Industry-standard switch-mode power supplies often don't react quickly enough, and might not have sufficient internal capacity to support a sudden fault-current demand.
An innovative method for protecting dc-powered systems from short-circuit or other sudden overload faults is by using a capacity (CAP) module. CAP modules are separate DIN-rail-mounted devices connected into new or existing installations. They're typically used with any nominal 24 Vdc power supply, and fitted between the power supply output and the circuit breakers for the loads. When the CAP module is charged, it waits in a ready state to respond to a sudden high demand for current from any of the connected loads. If this occurs, its capacity will immediately supply the high overload current as a pulse for the few milliseconds necessary to trigger the individual circuit breaker into trip condition. This isolates the faulty load, relieves stress on the power supply, and preserves the security and operation of the remaining loads in the system.
Effective pulse-triggering relies on using the CAP module and circuit breakers with "no-delay" trip characteristics or faster trip curves such as "B"or "C." It's important to know the breaker's resistance, and to minimize the total resistance of the load circuit, especially minimizing the length of cabling and/or maximizing the conductor size. This provides the best conditions to enable the full overload current to flow in order to achieve sufficiently fast circuit breaker trip action.
CAP modules inevitably increase the cost to an installation, but their worth should appeal to producers of high-value products and users who depend on revenue from fault-free operations.
Alan Balcombe,
portfolio marketing manager, electronics,
Weidmüller North America
Have to Be Faster Than the Power Supply
Control power provided by a modern, switch-mode power supply can benefit from a different type of protection. Most of these power supplies operate at 24 Vdc and are self-protecting to prevent overcurrents and subsequent overheating. However, maintenance engineers could face difficulties as they try to provide protection on the load side of the power supply to locate troubled loads and sensors.
Traditional circuit protection devices, including fuses and circuit breakers, are designed with the expectation of essentially infinite current available. But, when a power supply is applied, only a specific amount of current is available based on the design of the power supply. In some applications, there might not be sufficient current available with sufficient time to operate the protection device. Depending on the condition of the circuit problem, more or less current is needed to trip the fuse or circuit breaker. In some cases, the power supply self-protects and shuts down while the protection device fails to operate.
Electronic circuit protection will operate within the confines of a limited supply of voltage and current, yet it will operate faster than the power supply would self-protect. OEMs and end users can use products that monitor both supply voltage and current to connected loads, so protection is based on load conditions, current and voltage. Not only would the electronic circuit protection operate faster than the self-protection scheme of the 24 Vdc power supply, it indicates which circuit has an operational problem when one arises. Also, monitoring both the voltage and current helps engineers shut down circuits if the supply voltage drops below specified limits, providing easier and more efficient troubleshooting. OEMs benefit at start-up/commissioning when it's important to rapidly locate mis-wiring or application issues.
Jon Phillips,
product manager,
Rockwell Automation
Latest from Power Supplies
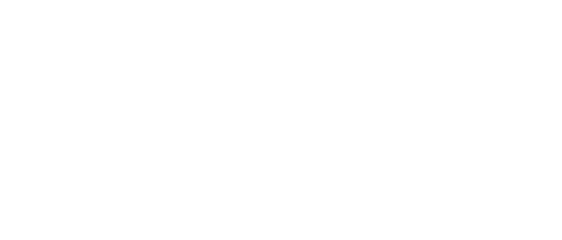
Leaders relevant to this article: