James Ingraham, software development team leader at systems integrator Sage Automation in Beaumont, Texas, says, "I'm not 100% convinced that PACs are actually a thing because any supplier that sells a PAC sells it to end users that call it a PLC.
Historically, PLCs were, in fact, logic controllers, so they were really good at Boolean on/off, 'check-a-photo-eye, turn-on-a-motor' kind of stuff. The addition of servos, PID loops, analog control, communications and database access have complicated the issue. Yet, out here in the real world, we still call it a PLC."
The IEC 61131-3 standard implemented some years ago defines five languages for controlling devices with a PLC or PAC, explains Ingraham. "The languages are ladder logic, which we all know and love, structured text, sequential function charts, function block diagrams and instruction lists. In addition, a lot of PACs also provide more traditional programming languages like C. That said, an advantage of IPCs is their processing power is vastly more than that of a PLC or PAC. A 12- or 16-core Intel processor with essentially unlimited RAM runs circles around a PLC or PAC. So if you have to scale up, that's probably your best bet."
Sage Automation used a PAC to combine motion control and database integration with traditional logic control for the just-in-time order fulfillment of tires.
In an example of one project, Sage used a PAC to combine motion control and database integration with traditional logic control for the just-in-time order fulfillment of tires (Figure 1). "When it comes to end users that are running a bunch of conveyors, for instance, whether they have an Allen-Bradley shop or a Siemens shop down the street matters a whole lot more than a particular processor's technical specs," adds Ingraham. "Most of today's technology is of relatively equal high quality. More important questions to ask are: where is the support coming from, and which supplier do we have the best relationship with?"PACs Handle Tilt-Tray Sorters
Another system integrator has a slightly different take. Pyramid Controls in Cincinnati, Ohio, specializes in developing automation solutions to optimize flow, increase accuracy, increase machine uptime and improve the productivity of product distribution centers (DCs)."Over the years, we started calling controllers PACs because they have more capability than traditional PLCs. A PAC or ControlLogix processor, for instance, can handle servos, all kinds of motion controls and so forth," says Pyramid's engineering director, Mark Hegge. "But in our minds, the biggest difference between PC-based controls, PLCs and PACs comes down to the reliability of the equipment."
Also Read: The father of the PLC explains the difference between the PLC and the PAC
In 2012, the firm replaced an outdated PC-based industrial control at a major retailer's distribution center (DC) with a system driven by Allen-Bradley ControlLogix PACs from Rockwell Automation. Many goods sold in major department stores such as dresses, suits, appliances and accessories arrive at the DC in bulk shipments from manufacturers. There, they're sorted using four tilt-tray sorters and then shipped to hundreds or thousands of retail locations. Packing-sorter machines carry items from the area where workers unload wholesale merchandise from palletized cartons and place individual items on tilt-tray machines, which feed the items into different chutes, depending on where they'll be shipped.
The retailer's legacy PC-based control system was aging and outdated. It couldn't properly control the tilt-tray sorters, which are highly sensitive to the timing at which internal switches needed to fire, within 50 ms or under 12 ms. Missing this window could shut the entire sorter down. The retailer also needed a technology that could synchronize more than 70 motors on each of the four loop sorter lines, as well as track products to eliminate the problem of lost inventory.
[pullquote]
Pyramid replaced the outdated system with several ControlLogix PACs—two to control each of four packing loop sorters and one shipping sorter. The controllers are networked to the devices on the sorting line via ControlNet, a protocol that provides ongoing feedback to the controller from the system I/O. The controller communicates via EtherNet/IP with the Pyramid Director warehouse control system (WCS) developed by Pyramid. ControlNet and EtherNet/IP share the common industrial protocol (CIP), which supports the integration of I/O control, device configuration and data collection across multiple networks. The new control system provides advanced diagnostics and analysis of the loop sorter directly to the WCS, so operators are notified of errors. Operators can then call Pyramid for assistance, and it makes adjustments to the system remotely via VPN access.
"The Rockwell equipment is designed for industrial application and is more robust than PC-based control systems. PC-based controllers are typically upgraded more often because the hardware doesn't last as long and the software operating system isn't supported as long," says Mukesh Ram, Pyramid's general manager. "And, from an end user's perspective, the PC requires an IT programmer, as well as an individual with an electrical skill set, to maintain and troubleshoot the devices associated with the material handling equipment, whereas PLCs or PACs can be managed by one type of engineering individual—an electrical controls engineer. Another advantage of PACs over PCs is they let you do online programming and make changes while the system is running. In contrast, PC programs must be compiled and then executed thus causing interruptions to operations."
According to Keith Staninger, business manager for controller and I/O platforms at Rockwell Automation, a PAC can handle significantly more information than a discrete machine controller or PLC. "For example, users can implement loop control, predictive control and condition monitoring, all of which are different sets of information that make up what we call integrated control," he says.
PC-Based Capabilities
One company that firmly believes in the PC-based control concept is Beckhoff Automation. "Vital to our approach is our TwinCAT software, which runs on PC-based hardware such as embedded PCs to support a wide range of machine automation functions including logic control, motion control and safety," says Aurelio Banda, vice president sales and marketing at Beckhoff North America. "It, along with our scalable hardware, allows the creation of more centralized architectures, depending on the particular machine and the processes taking place on it, while adding, for example, more motion or safety as needed, without having to rebuild the entire application. The technology uses protocols such as EtherCAT, the open Ethernet-based fieldbus system developed by Beckhoff, and provides data communication with user interfaces and other programs by means of open standards such as OPC UA and various software tools from Microsoft. The embedded PC is therefore attractive from a cost point of view because it eliminates the rigid approach of a PLC in controlling machine processes, which necessitates adding more processors, black-box hardware and completely different software packages to provide, for example, additional motion or safety functions."
Dedicated Devices
An important distinction between IPCs and PACs is that PACs are normally dedicated to industrial control, where IPCs typically run a Windows OS and may take on other functions, such as running typical Windows applications. "Unlike a Windows system, the PAC OS is real time and often deterministic," says Jerry Sorrells, product manager for controls and HMIs in the electromechanical division of Parker Hannifin's Automation Group. "PLC and PAC technology are converging such that traditional PLC manufacturers are adding functionality to keep up with PACs. This often includes adding modules for network communication or servo control. This approach, however, increases OEM and end users' costs by piling on additional hardware. PACs on the other hand are typically designed to communicate on multiple networks and execute multi-axis motion without the need for additional hardware. For instance, Parker's PAC doesn't require add-on hardware for common communication protocols or servo control, and it doesn't set an arbitrary limit on the number of axes that can be controlled, since the practical limit is a function of the performance required for the application."
A PAC controls this newly developed additive manufacturing machine that uses a unique metal deposition process.
Parker's PACs have been put to work in applications including driving 200 axes for a fiberglass machine, as well as controlling a newly developed additive manufacturing machine that uses a unique metal deposition process (Figure 2). Consider the example of Plus Manufacturing, +Mfg, in Erlanger, Kentucky. The designers there are in the final stages of developing a six-axis robotic gantry for 3D metal deposition that uses the new Parker Automation Controller to control the building of individual or multiple parts or multiple different parts—each from different metals. "The PAC interfaces with our master computer that delivers the part geometry and takes control of the six axes, so the gantry and build table follow the motion paths it gives them," says Paul Saleba, spokesperson for +Mfg. "The PAC provides the six Compax3 controllers inputs and reads outputs interdependently, all while communicating with the master computer to ensure that all the axes work together. The machine, which will be introduced at the Automate Show in March 2015 in Chicago, will be capable of building complex metal structures quickly and inexpensively to near-net shape, eliminating the need for casting, welding or forging."PACs Analogous to VFDs
The difference between PACs and PLCs can be a grey area, but one of the best ways to understand the distinction is to look at the history, explains Ben Orchard, application engineer at Opto 22. "PLCs were a step up from older pseudo-control systems comprising relays and timers, and they were programmed with ladder logic because that's how electrical diagrams were drawn," he says. "The whole focus and design of PLCs was digital control of relays. PACs were an expansion of this and much better at handling analog signals and PIDs. Then came the age of networking, originally serial and then Ethernet. With Ethernet communication, PACs kicked into high gear and became the de facto standard for control systems because all it takes is one unit to control, monitor and communicate with multiple racks of analog and digital signals and multiple PID loops." In short, a PAC can work with devices using analog, digital and serial I/O signals.
"Currently, just about every manufacturing process is becoming more and more analog," continues Orchard. "A good analogy is that of the variable frequency drive (VFD). In the past, we simply turned a motor or pump on or off, and it ran at full speed. In contrast, VFDs lets device such as pumps be more efficient at different stages of the process by running at different speeds as opposed to flat out."
In more detail, end user Zuno Engineering of Fort Wayne, Indiana, explains how Opto 22 technology takes a different, yet robust and cost-effective approach. "Our company uses Opto 22 in several ways," says Adam Brososky, principal at Zuno. "For example we might replace an existing PLC system or a new system where a new machine is being designed, and implement the Snap-PAC controls. Then, depending on the application, we'll either a install a touchscreen PC for the HMI or Opto 22's Groov technology, which is a Web-based HMI that lets users employ an iPad or smartphone to control their machines."
Zuno replaced all the controls in asphalt plants sold by a local manufacturer.
For example, one project entailed Zuno replacing all the controls in asphalt plants sold by a local manufacturer (Figure 3). "The manufacturer sells the plants worldwide and wanted its own system and the intellectual property," says Brososky. "We use Snap-PAC I/O control and monitor all of the points in the plant. This includes the VFDs controlling the bins and pumps that proportion the material, controlling the mixing drums, monitoring temperatures of material and keeping inventory control of the output silos. The company's systems now have a PC that runs as an HMI and communicates with four racks of Opto 22 equipment. Each rack has 16 modules on it, and each module has between four and 16 I/O points. We sell complete systems from building the back panel up to installing the software."A big difference between the ladder logic of standard PLCs and the programming structure for Opto 22 is that it’s flowchart-based with blocks of code. "Many individuals with a classroom-only engineering degree have never seen ladder logic before, but they're familiar with LabView and C. Opto 22 marries LabView-type programs with C programming in one package. So, for someone who's never been in the industry, it's a lot easier to use than trying to learn how to program controllers from traditional major suppliers," says Brososky.
Latest from Embedded Control
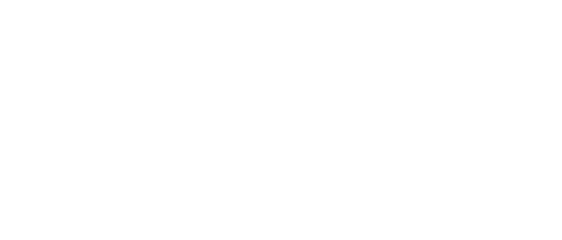
Leaders relevant to this article: