Waterjet Cutting Systems for the Toughest Manufacturing Tasks
Waterjets are among the most flexible cutting systems available. They can cut virtually any material and have become a principal method of fabrication and metalworking for a variety of compelling reasons.
Jet Edge in St. Michael, Minnesota, is a leading developer of this technology, designing and manufacturing ultra-high pressure waterjet systems for precision and mobile cutting, water blasting and surface preparation. Jet Edge offers an extensive range of systems that gives customers flexibility in choosing a solution that best meets their needs.
As a high-profile example, during the Gulf of Mexico oil spill in 2010, British Petroleum needed a waterjet system that was operable 5,000 feet under water. To deal with a major, time-critical problem that had never been solved before, Jet Edge created a system that blasted away hydrate ice crystals clogging a containment system and preventing BP from stopping the flow of crude oil into the Gulf.
Of course, most Jet Edge machines are on the shop floor, not the sea floor. Ultra-high pressure (UHP) pumps and waterjet cutting machines enable fabricators cut intricate parts in all types of materials ranging from soft foams and rubber gasket stock to thick tool steels and space-age composites. The cuts can be simple straight lines or can be extremely intricate, with large or small pierced holes. By using waterjet cutting systems (a cold-cutting process), fabricators avoid heat-affected zones (HAZ) and don't burn the material during cutting. They can enjoy reduced raw material waste and less damage from cutting that would otherwise require rework or secondary processing. Waterjet cutting systems also can be used in applications that process flammable materials. More traditional ways of cutting parts include stamping with metal dies, shearing and sawing (dies, knives and blades dull over time), laser cutters (limited to cutting thinner metals and can't be used to cut highly reflective materials) and plasma cutters (limited to cutting metals and can't cut materials as thick as a waterjet can cut).
Waterjet systems have a higher initial acquisition cost than saws, plasma cutters and flame/torch cutting systems, and they cut slower than saws, plasma, lasers or torch systems and stamping systems. Waterjets, however, are an excellent choice for shops that require the versatility to cut a wide range of materials, including thick materials and those that need to eliminate HAZ.
Complex Cutting With PC-Based Control
Also Read: Water Jet Builder Connects With Unified Control Platform
"To maintain extraordinary levels of precision, high-end motion control is critical, especially for maintaining cut edge quality and for meeting tight dimensional tolerances," says Jude Lague, Jet Edge's president. "Accuracies of cuts often must be within 0.005 inch or less. Waterjet manufacturers such as Jet Edge meet these requirements by powering their equipment with fast, accurate, reliable and consistent motion control products and sophisticated software. Our gantries feature a closed-loop drive system on X and Y axes; ac digital brushless servomotors, absolute encoders and SERCOS communications. They include preloaded anti-backlash recirculating ball screws and linear bearings with hardened precision ground ways."
The need for a flexible system is also important, Lague states. "We needed an open system that could easily integrate the full array of sensors that Jet Edge uses, while providing intricate motion control."
Jet Edge motion controls started with traditional industrial PC-based analog controls supplied by major vendors and more specialized custom manufacturers.
Ten years ago, Jet Edge decided to change to a digital motion control platform. "With the progression of our technology and our previous controls vendor not advancing its code, we needed a new platform that could help our technology grow," Lague says. "After an extensive search, we chose to work with Beckhoff Automation for a complete control solution. With Beckhoff industrial PCs (IPCs) and TwinCAT CNC software, Jet Edge was able to seamlessly and incrementally migrate to new technology. We chose Beckhoff for its flexibility and because the company is conveniently located here in Minnesota."
The TwinCAT system has become an integral component in Jet Edge's high-rail and mid-rail gantry machines. Jet Edge partnered with the Beckhoff to rewrite the Jet Edge HMI, and created an innovative CNC waterjet motion system by harnessing the power of the CNC capabilities in TwinCAT. The high-rail and mid-rail gantry systems are designed to be exceptionally stable with a rigid platform that minimizes machine vibration. The system is capable of advanced three-dimensional waterjet movement over the work area and ultra-high precision cutting.
Since making the shift to TwinCAT software, Jet Edge has seen an overall improvement in cutting tolerance and cut edge quality. "This is difficult to define as a numeric value, but we can operate with higher machine resolution with the new control system," says Jeff Schibley, Jet Edge regional manager. "This is partially associated with the speed and response time of the system in conjunction with SERCOS and a higher resolution motor and drive package. The cutting system now is less forgiving of programming errors. In the Aquavision 1, the operator could execute a program with sloppy geometry and overlapping kerfs in the cutting path. The new control gives the operators an error code and tells them they should not do that because they are going to produce an inaccurate part."
Running TwinCAT CNC software on IPCs enables Jet Edge to implement complete machine control and HMI with tightly coupled PLC functionality and multi-axis motion control processes. "TwinCAT and the IPCs work together on positioning tolerance, speeds and positioning," Schibley explains. "The IPC controls on/off functions of valves, block retrace, height sensors, laser mapping, servo communications and a portion of everything the cutting table does. The IPC can control the peripheral equipment without affecting the data execution of TwinCAT controlling the program path."
For the machine display, Jet Edge uses "economy" control panels with DVI/USB extension technology, which permits installation up to 50 meters away from the IPC. The 15-in. display has an aluminum front with sheet-steel rear cover, front-side IP65-rated and rear side, IP20.
Figure 1: Bus couplers connect the SERCOS bus system to the I/O terminals and provide the connection back to the central IPC.
The system integrates with SERCOS II. The IPC-specified features include a SERCOS mini-PCI fieldbus card that connects via fiber-optic cables for the SERCOS networking used in the machine for I/O and drive networking. The compact IPC is designed for control cabinet installation and all connections, including fieldbus and standard PC interfaces, are conveniently located at the front of the IPC housing. Cooling is managed by internal cooling fins and an exchangeable fan cartridge at the bottom of the IPC housing.
"Bus terminal I/O is used to implement a variety of Jet Edge machine functions," Lague adds. "Analog bus terminals assist with height sensors and plate mapping, while digital I/O terminals are leveraged for control relays and solenoid valves. Bus couplers (Figure 1) connect the SERCOS bus system to the I/O terminals and provide the connection back to the central IPC."
With regard to integrated safety, Schibley says the light curtains, safety mats, shuttle tables, conveyors and peripheral equipment are controlled by the IPC, which communicates the status of these to the Beckhoff system, adding that Jet Edge doesn't have to purchase a separate stand-alone PLC to control the peripherals.
Gives Us the Edge
Figure 2: Jet Edge’s Edge X-5 is a five-axis waterjet system that cuts complex, taper-free and 3D parts from virtually any material. It features an IPC controller running CNC software programmed specifically for five-axis waterjet cutting.
The new technology resulted in the design and build of Edge X-5 (Figure 2), a five-axis waterjet system that cuts complex, taper-free and 3D parts from virtually any material (Figure 3, page 36). It features a Beckhoff IPC controller running CNC software programmed specifically for 5-axis waterjet cutting. The Jet Edge AquaVision Di controller offers an open architecture design that enables users to choose from many CAD/CAM/nesting software providers or to use standard G & M code.
The controller operates on Microsoft Windows 7, and it's customary for Jet Edge to supply nesting and cut optimization software by Swedish company IGEMS. This software also produces the post processor file.
"While it's usually not the case, we don't always supply the operating software," Lague says. "However, it demonstrates the flexibility in the Jet Edge platform, so it does happen. Many or most of the large waterjet manufacturers will design and assemble their own proprietary hardware platforms and use their own CNC and cutting path trajectory software, as well as their own HMI software. This can limit the flexibility of their systems by restricting the customer's software selection. For example, if a Jet Edge customer wants to cut advanced aerospace components using proprietary software and cutting techniques, that customer often can integrate its software to the AquaVision Di control's operations without modifying the manufacturer's proprietary software. Our system's Intelligent Work Envelope automatically adjusts cutting processes depending on the angle of the cut to protect the operator, material and system components. Using this feature-rich solution, the machine operator can adjust the cutting parameters with ease. Even for the more technically advanced CNC users, engineers can still ‘get into the software' and modify parameters to their specifications."
Michael Waltrip Racing Selects Jet Edge
To create high-performance mechanical parts, Michael Waltrip Racing (MWR) selected the Edge X-5 to complement an existing three-axis system from Jet Edge. MWR uses its waterjet machinery to cut more than 1,000 parts for each of its NASCAR Sprint Cup cars. The team assembles about 56 cars per year, including the #55 Aaron's Dream Machine Toyota Camry and the #15 5-Hour Energy/Peak Toyota Camry driven by Clint Bowyer.
"To win high-profile business such as this, Jet Edge delivers high-pressure water solutions that operate at 36,000 psi to 90,000 psi with direct-drive electric or diesel-powered pumps ranging in size from 30 to 280 hp that can successfully run at 55,000 psi and produce UHP flow rates from 0.6 to 7.2 gpm to UHP cutting heads with advanced motion control systems," Lague explains. "These cutting heads can cut three-dimensional patterns in most materials when placed on a flat surface. The heads are connected to an overhead gantry system that moves over the cutting surface to make intricate and flawless parts." The powerful cutting force of the waterjet stream is kept under control using a 36-in. deep water tank that harmlessly dissipates the cutting stream and prevents it from cutting through the factory floor.
Waterjet cut parts can range in size from that of a gear in a Swiss wristwatch to 100 feet long or more. However, parts are most often cut from plates or sheets that are 4 x 8, 6 x 10, or 6 x 12 ft in size. Waterjet cutting envelopes most often are designed to capitalize on these sheet sizes, although larger Jet Edge systems that accommodate 20 x 12-ft sheets are not uncommon.
Further pushing the limits of waterjet cutting, Jet Edge established its 90,000-psi X-Stream pressure pump technology, which enables customers to cut parts faster and reduce operating costs by using less abrasive material, water and electricity. "X-Stream pressure pump technology led to the development of a revolutionary metal-on-metal seal technology that eliminates 50% of the required seals on our pumps," Schibley says. "This is hugely important in terms of service and maintenance, considering that conventional seals eventually need to be replaced."
Bus Transfer
Figure 3: The CNC waterjet motion system is capable of advanced three-dimensional waterjet movement over the work area and ultra-high precision cutting.
"The control system in our waterjet machines is no longer a limiting factor for volume, speed, accuracy or quality. Jet Edge is much farther down the road in reducing our production costs than we would have been with PLC controls," Schibley says.
In the initial selection of a new motion control platform 10 years ago, Jet Edge avoided any solution that didn't have an open architecture, Schibley notes.
"We would not accept buying an endless array of control-related equipment from the most expensive vendors out there," he adds. "This was another principal reason why Jet Edge chose Beckhoff Automation. Jet Edge replaced its controls and still retained the motor/drive components that formed a large part of its product platform. Some suppliers require that when you buy their control, you also must buy their motors and drives. Beckhoff didn't do that."
The analog controls previously used by Jet Edge in the 1990s generally had five-to-10 year operating lives, limited by computer component availability, operating software code changes and technical obsolescence. "The control products are extremely durable," Lague explains. "We have eliminated the warranty expenses and controller failures characterized by non-industrial PC platforms of the 1990s. In 10 years of operating Beckhoff controls in harsh waterjet cutting environments, Jet Edge never has had to replace a controller."
Next-Gen?
In continuing the company's evolution of automation and controls, Jet Edge is evaluating a change from SERCOS to EtherCAT industrial Ethernet for its motion and I/O bus. We think EtherCAT will help Jet Edge to extend its limits of machine performance into the foreseeable future.
What are the likely new short-term requirements our customers will ask for moving forward? How will the next-gen machine automation scheme be changing? "We know that customers need to cut volumetric shapes in 3D space," Lague notes. "When other waterjet manufacturers build that type of machine, I believe they switch to a higher-priced and higher-featured control rather than their proprietary control. Jet Edge will be able to simply integrate the 3D software into the existing AquaVision Di. We already use the higher-featured control system."
Nancy Lauseng is the marketing manager at Jet Edge. Learn more about the company at www.jetedge.com.
All photo credits are Jet Edge
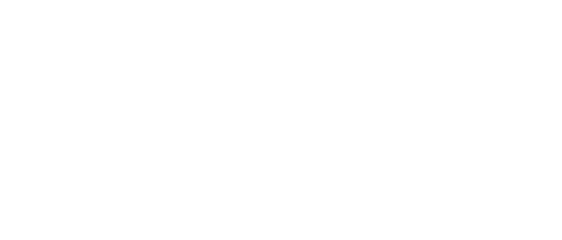
Leaders relevant to this article: