Out of sight no longer need be out of mind. That’s good news for remote support, a technology that allows machine builders to troubleshoot and fix systems at a distance.
“It allows us to be an in-house asset to a customer without actually being physically present,” says Michael Joyce, Jr., vice president of Integrated Industrial Technologies. The Pittsburgh, Pennsylvania-based automation integrator provides design programming services, equipment assembly and installation and final system commissioning works to its customers in the automotive and other industries, creating robotic material handlers, computer-controlled tooling and other solutions as needed.
The benefits of being able to reach out and touch a system are faster and less-expensive diagnostics and repairs, saving time and money. Beyond that, though, remote support could be the gateway to other services and revenue streams. For example, machine builders could monitor processes, improve machine performance or possibly even use the data to implement a performance contract.
Remote support and these other services are possible because of the widespread availability of broadband connections, even on plant floors. Technologies are also in place that make those connections secure, an issue that some customers still have concerns about. Finally, there are solutions that make such connections easier, taking care of the details that in the past proved to be stumbling blocks to engineers with expertise in controls and not networking.
Faster and less expensive
For an example of remote support and what it can do, consider Eagle Technologies Group, where remote support saves money and time. That directly benefits the company and its customers. Headquartered in Bridgman, Michigan, Eagle Technologies is a factory automation supplier serving the automotive and healthcare industries, among others. The company’s systems engage in dispensing, material handling and other manufacturing operations for customers scattered across North America and around the world.
“We have to support and service that equipment not just from a warranty standpoint but from a production standpoint, an improvement standpoint,” says Brandon Fuller, vice president of sales.
On the last point, Fuller says that a customer may contact Eagle Technologies with the information that a particular station is not working as well as others. In that case, the customer may want the automation supplier to investigate and make some adjustment to bring the output of the problem station more into line with that of other stations.
Also read: U.S. government resources for cybersecurity
In making these and service repair requests, customers expect to get a quick, almost instant, response. That presents a problem, since it may take a day or more to reach the customer site.
The solution is remote support, with staff from Eagle Technologies logging into the system, examining it at a distance and then making any needed changes. By going the remote route, it’s possible to be working on the problem within minutes, and the fix might be found and applied within an hour.
This is much faster than the alternative, and it’s much cheaper. The cost of flying engineers to a customer’s site and paying for their time can run into the thousands of dollars per trip. Remote support substantially reduces that expense.
“A customer that routinely requires support would save tens of thousands of dollars a year, easily,” says Jason Cleveland, vice president of engineering.
Most issues can be resolved remotely; Fuller estimates the success rate to be about 90%. Even for those one in 10 cases where a trip on-site is necessary, remote support can prove useful. Thanks to diagnostics, the engineer or technician will know before traveling what the problem likely is. With that knowledge, it’s possible to arrive on-site with the right parts, which minimizes downtime.
Customers are growing more accepting of remote access and support. That’s particularly true due to such options as VPN connections, which ensure the security of the link. In the case of Eagle Technologies, remote access can be turned on or off by the customer, leading to greater peace of mind.
As for the future, the latest twist is the use of video, with a camera relaying live images of a system in operation. This has the advantage of supplying extra information that together with sensor data can make remote monitoring, diagnostics, support and even process improvement and training more effective. Live video will be an increasing part of the remote support mix in the future, Fuller believes.
Eagle Technologies uses Rockwell Automation products for its remote support offerings, with one being directly connect to the machine using Allen Bradley remote access modules. Rockwell Automation has been supplying and engaged in remote monitoring and support for years. Changes in the plant floor infrastructure are increasing the need to do so due to the resulting impact on the skills needed, says Bhavnesh Patel, product manager for remote support services for Rockwell Automation.
“You have a lot of this IT infrastructure that’s coming down into the plant floor, so customers want expertise not only to support the automation assets but also the IT assets,” he says.
Such skills are in short supply, Patel adds. Remote support allows a company to multiply its talent pool by, for instance, allowing easier collaboration between widely dispersed centers of excellence. Another potential outcome of this access is predictive maintenance, which would be based upon the data collected remotely.
Looking toward the future, Patel points out that the same data could be used, for example, to monitor cardboard levels in a packaging machine and keep it restocked with inventory. Thus, remote access and support could lead to value-added services that a machine builder could offer to customers.
With video, support and more
Figure 1: Groninger’s lite-F features remote support with a video option.
Source: Groninger and Beckhoff Automation
An example of video in remote support and its use in other applications comes from packaging machine maker Groninger USA, which is a subsidiary of its German parent. The company recently introduced its American-made filling machine series, the lite-F (Figure 1). Its entire lite series features a remote support option that is based on a router and firewall, enabling remote access and therefore support to everything connected to the LAN side of the router (Figure 2). The list typically includes the PLC, HMI and servo drive system.
The remote access is secure. For one thing, it’s through a VPN tunnel. For another, the customer has complete management over when a connection is made or allowed.
“The customer can decide with a key switch or a password-protected button when this router initiates a VPN tunnel to a server at Groninger USA in Charlotte, North Carolina,” says Stefan Winzinger, electrical and automation engineer.
There is another element of the package: a webcam that can be remotely controlled. This serves two functions. One is on the support side, with the video offering Groninger support staff additional information about problems. By looking at pictures, for example, technicians may identify defective components that are causing production downtime. The second use is in training, such as when a customer is going to a new packaging solution and needs help getting it up and running.
Figure 2: A PC-based control system integrated into the lite-F provides for easy remote support access via a VPN tunnel.
Source: Groninger and Beckhoff Automation
The savings from this second use can total several thousand dollars. As for the first, having a line go down is expensive, with the cost depending upon how much production is lost for how long. The expense can easily run in the tens of thousands and potentially hundreds of thousands of dollars.
The company made the decision to package remote access with video capabilities based upon years of experience supporting customers over the phone. “We thought it would be really great to see the actual problem on the machine, instead of getting it just described,” Winzinger says.
For this and other products, Groninger uses TwinCAT automation control software and TwinSAFE EtherCAT I/O solutions from Beckhoff Automation. The fact that this is PC-based machine control is a plus when it comes to remote support, says Daymon Thompson, TwinCAT product specialist at Beckhoff.
“That’s an advantage for OEMs because they can get directly onto the machine control through traditional remote support, things like WebEx or TeamViewer or the really traditional VPN connections,” he says.
These are the same technologies and options used in the corporate IT world for a secure, remote connection. Thus, they are familiar solutions to IT staff and so likely to be more easily accepted by the gatekeepers to corporate networks.
For Beckhoff, then, the future of remote support on the plant floor looks like the future of remote support in corporate IT. There will be more cloud-based services with notification and remote configuration, Thompson says.
Bypassing pipes of all kinds
Sometimes, remote support shows up in some really remote areas, such as new oil and gas wells. The recent boom in oil and gas drilling in the United States brings with it infrastructure challenges. Traditionally, getting the gas produced to a processing plant has been done via a pipeline, but those are expensive to build and take many months to construct. Hence, the typical solution has involved flaring—burning off excess gas. That’s why remote and relatively unpopulated parts of North Dakota currently glow as brightly as major cities. However, emission regulations are in place to curtail this.
Enter Pioneer Energy in Lakewood, Colorado. The company designs, manufactures, deploys and services proprietary miniaturized gas plants that sit at the well head. This eliminates the need for a pipeline but multiplies the gas processing complexity by substituting many gas plants for one.
“In order to manage that complexity, we need some type of high-fidelity remote access,” says Andy Young, process control manager at Pioneer.
Small enough to fit on a single 40-ft trailer skid, Pioneer Energy’s plants can process a third of a million cubic feet of gas a day, transforming it into valuable liquid and natural gas products that can increase revenue per well by as much as 30%. Each system has about 150 analog and digital I/O points. At any given time, 30 or 40 of these are sampled per system and transmitted once a second, Young says (Figure 3).
Figure 3: Pioneer Energy supports mobile gas processing plants placed near wellheads remotely over cellular connections.
Source: Pioneer Energy
Because these mobile gas plants have to be set up quickly in remote areas, Pioneer Energy uses a two-way cellular connection to gather this data and to allow on-the-fly operational adjustments. The operation information helps to optimize the design of future systems while high-level data is available through a Web server interface (Figure 4).
Figure 4: Data collected for remote support helps field technicians servicing a mobile gas processing plant.
Source: Pioneer Energy
“It has really improved the service quality for our local field technicians, who don’t have access to the full picture, but they’re getting some of the highlights and that helps to make real-time decisions about what to do,” Young says of the data presented through the server.
He adds that the networking is in a hub-and-spoke model, with the central operations point being the hub and the various mobile gas plants being the spokes. That arrangement makes bringing individual gas plants online or taking them off relatively simple. That helps to make it possible for Pioneer Energy to get a mobile gas plant up and running within 24 hours, a key requirement.
Pioneer Energy has been engaged in field operations since 2014. Young says its approach became feasible when the company learned of mGuard technology from Phoenix Contact.
“An mGuard is a security appliance. It provides you VPN technology. It provides you firewall technology. It provides you the same technology over cellular networks, if you need to do that,” says Andres Suazo Wildt, product marketing specialist for process and serial bus systems, Phoenix Contact.
In 2014, Phoenix Contact extended this concept to a new product called mGuard Secure Cloud. An online portal, this service makes configuration and connection much simpler, says Suazo Wildt. All the end user needs is an account, along with the IP address of the device that is being connected. There is no fee for using the service, but it does only work with Phoenix Contact mGuard products.
Keeping things cool, remotely
A final remote support example comes from Stellar, a Jacksonville, Florida-based integrated design, engineering, construction and mechanical services firm. It acts as a distributor and system integrator of, among other things, industrial refrigeration systems. Stellar offers its clients what it calls Star Support, which enables real-time access to data from anywhere. The service allows Stellar to provide remote support and monitoring.
Vice President Steven Hawkins says that the data collected remotely improves support because it allows the company to respond faster to a problem. Remote support even improves those calls that have to be made by rolling a truck to a site.
“We can actually now send our work tickets to our field service crew,” Hawkins says. The company is implementing a system where critical parts will be carried on the truck. Thus, there may be no need for a truck to first visit a warehouse before going on a service call, thereby speeding up the repair and support process and cutting downtime. The latter is particularly critical with food and beverage, as too great a temperature rise will spoil product.
For its remote support, Stellar uses private-label gear based upon GE’s Equipment Insight solutions. Used within GE itself for years, Equipment Insight employs an edge device, called the Field Agent. This can be configured to communicate with nearly any industrial asset, says Steve Pavlosky, Equipment Insight leader at GE.
“The Field Agent buffers data to overcome any network unreliability, encrypts the data and transmits the data securely. Making data collection simple and secure is a key to the deployment of this technology.” Pavlosky says.
Remote support options
As these examples illustrate, remote support can be an effective tool, saving time and money while potentially enabling new products and services. When considering remote support implementations, it’s best to have several options, says Integrated Industrial Technologies’ Joyce. The systems his company creates are usually PC-based, which means that Integrated Industrial Technologies’ staff can use popular collaboration products like WebEx or LogMeIn to get remote access to a machine having problems. The issue may be resolved in under an hour by looking at log files, system utilities and occasionally remote debugging, Joyce says.
That is much less than the day of downtime that would be the case if travel had to be on-site. And the remote support approach also pays other dividends for Integrated Industrial Technologies. “It also allows us to handle these support requests with minimal disruption to ongoing development projects as the responsible engineer does not lose development time to the travel requirements,” Joyce says.
A downside of the current approach is that it does require the systems being accessed to sit on the client company’s business network. So, Integrated Industrial Technologies is looking into using an appliance to enable remote support access for production equipment. One option under evaluation will provide access to non-PC systems and also will provide hardware level security, thanks to an additional hardware component in the panel.
Some companies are sending out a fully loaded PC with systems, with the idea being that this enables virtual machine control and makes remote support easier. The idea has merit, if cybersecurity concerns are adequately addressed, says Joseph Kernich, integration expert of Machine Tools Analytics for Siemens Plant Data Services.
In the case of the Siemens products, there’s no need to ship an extra PC because the functionality is built-in, says Kernich. It is part of a cloud-based solution that provides more than just remote support to handle existing problems. It also enables spotting trends that can lead to issues in the future.
“Wear-and-tear trends are identified and allow corrective actions to be taken before faults will occur,” Kernich says.
He predicts that in the future every device on a plant network will connect to the cloud. The data thus collected will make it possible to improve support, remote or otherwise.
The future
Beyond any technical challenges, remote support does have some drawbacks. One is that traditional support involves face-to-face interactions. Those strengthen the bonds between machine builders and end customers, improving the partnership between the two, says Integrated Industrial Technologies’ Joyce. “Like much of today’s technology, it does remove some of the human factor when interacting with our customers,” he says of remote support.
Nonetheless, he predicts remote support will become increasingly common, driven by the fact that it enables quicker and less expensive troubleshooting and problem solving. “The conflicting requirements of access and security will need to strike a balance to give everyone what they want while minimizing the unintended consequences,” he says.
Sometimes the balancing act between security and access is complicated by a customer’s previous bad experiences, says Stellar’s Hawkins. Stellar handles this by putting systems in place to reassure its customers. For example, Hawkins says customers are made aware that there is “one-way access off the facility but no access to the facility without their involvement.”
As for the future, the Industrial Internet of Things and mobile terminals are widely seen as being increasingly important. One result will be that mobile devices will be used more and more often for remote support. It may even turn out, as in the Pioneer Energy case, that the data collected for remote support will be used for local troubleshooting and repair, with this made easier thanks to mobile terminals.
Another future trend may be the use of the data being collected as a basis for other service options, such as performance-based contracts. In these, customers would not buy systems or machines, but instead would buy a set amount of cooling capacity or a fixed number of widgets, paying a flat fee for each unit.
That transition to some sort of added service, and potentially more revenue, may be already underway. For instance, Eagle Technologies’ Fuller reports that most of the time customer requests involve remote support, instances where something is down. But, about 20% of the time the request is to make things work better. This is more likely to happen if the customer has a data metrics package that allows the operations staff to see how each production station is performing.
Fuller relates what happens next, saying, “They have a screen that says, ‘Station 5 is your slowest station.’ Then they can all Eagle up and say, ‘Can you remote in to Station 5? We want to speed that up a bit. We want you to make it faster.’”
Remote support may only be the beginning of the services that can be offered. If so, being out of sight might be something machine builders won’t mind.
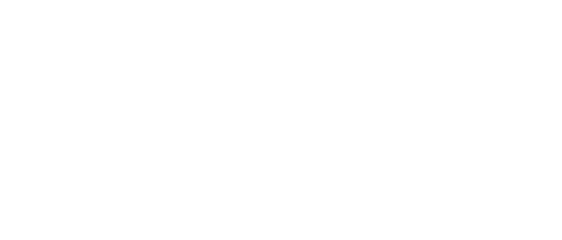
Leaders relevant to this article: