Automation technology will play a key role in allowing complex processes to operate more safely and efficiently with fewer personnel on site. Process control solutions will also enable monitoring and control from remote locations.
Evolution of control technology
In industries from refining and petrochemicals to mining and pharmaceuticals, processing plants have kept pace with the evolution of automation technology (Figure 1). This journey started in the 1950s with the introduction of PID controllers, which produce a control signal by reacting to the error already produced in a proportional (P), integral (I) and derivative (D) manner.
Expert control was introduced in the 1970s to fill the gap in process control. Expert systems tried to imitate the behavior of human operators using rules. Unfortunately, too many rules were usually required, and the performance of these systems could not go beyond that of human operator performance.
The industry saw the move from panel controls to digital control systems in the 1980s, whereby plant operators were able to safely expand an operatorās scope of responsibility by as much as three times. This development not only improved operational performance but also provided a better view and control of the process.
Figure 2: The current generation of automation technology continues to enhance systems through centralization of data collection and monitoring, allowing industrial operating companies to focus on control system optimization.
Once manufacturers started shifting paradigms to become more data-led in their production systems, it enabled them to draw on that data to inform the expert analysis of the process. This resulted in improved control limits and a reduction in the variance and the number of quality defects. It did, however, make operatorsā jobs more difficult, as they needed to manually maintain the process within finite control bounds. The next level of improvement was to make adaptive changes as quickly as possible, with an understanding of the system from start to finish, to improve production.
The current generation of automation technology and software solutions is continuing to enhance process systems through centralization of data collection and monitoring, allowing industrial operating companies to focus on control system optimization (Figure 2).
By using software, including advanced control and alarm management, plant operators have achieved improvements in process safety (Figure 3). They have also gained greater visibility into process risk. More importantly, advanced control defined optimal limits and rigorously executed controls to maintain those limits.
The ongoing enhancement of control technology has allowed industrial facilities to be operated with better throughput and quality, as well as greater reliability and efficiency. Most notably, with facilities running closer to optimal limits for longer periods of time, data suggests a dramatic improvement in overall safety. However, the shift to more efficient use of materials and labor in this next age of industrial discovery requires that the underlying technology continue to evolve at a rapid pace.
Journey to industrial autonomy
As evidenced around the world, industrial organizations can overcome competitive pressures and uncertain market conditions to achieve game-changing business outcomes by embracing the lifecycle journey to industrial autonomy. In fact, some organizations are just accelerating the journey theyāve already been on.
Figure 3: As industry continues to drive improved operational efficiencies, productivity and enhanced safety, control room consolidation, in support of centralized operations, becomes a key requirement.
According to a recent study by LNS Research, approximately 50% of industrial transformation leaders have an autonomous plant initiative formalized and an estimated 41% of these leaders are speeding up their autonomous plant efforts.
Increasingly, plant owners/operators are looking for solutions that go beyond basic automation. They require flexible systems that can self-optimize performance across a broader network, learn from new conditions in real or near-real time and autonomously run entire production processes. These systems can operate within the four walls of the plant, but they can also connect to a global network of similar assets and even to the digital supply network more broadly.
It is now clear that the transition from industrial automation to industrial autonomy will affect multiple roles within industrial organizations, including process control, engineering, field operations and maintenance.
The world of industrial autonomy is a crucial part of what ultimately comprises the Fourth Industrial Revolutionāalso known as Industry 4.0āwhich will enable assets and operations with robust adaptive capabilities. Autonomous control systems will respond without operator interaction to situations within a secure, bounded domain that was not pre-programmed or anticipated in the system design.
Industrial autonomy enables plant operating companies to harness the power of new digital technologies to create a truly seismic transformation of operational benefits. Since digital transformation is not a one-step process, understanding a facilityās capabilities, digital maturity and state of operations is crucial in identifying its next steps in the industrial evolution.
The trend toward industrial autonomy can be related to autonomous cars. It has been forecasted that autonomous cars are likely to become the primary method of personal and business transportation in the next 25 years. Some suggest that, in 2040, approximately 75% of the vehicles on the road will be fully autonomous.
Itās important to understand that the purpose of autonomous vehicles is not just about eliminating the driver. Rather, itās about eliminating the more than 30,000 road fatalities each year. Itās a matter of reducing the several million people with auto-related injuries every year. And itās also about saving approximately $190 billion per year in medical costs and property damage.
Also read: Top 4 reasons industrial tech is red hot
It is expected that autonomous vehicles will drive better than humans. Driving is challenging for humansāthereās a tremendous amount of input to sort through. With all that data, humans make mistakes, lose focus, respond to the wrong stimulus or even panic. Autonomous cars donāt panicāthey will methodically make optimal decisions based upon the available data.
Autonomous vehicles will usher in a new generation of transportation safety, reliability and efficiency; and they will do so at a lower cost. This is where there is an intersection with industrial facilities. Can industrial process plants move toward industrial autonomy and make a similar step-change improvement in benefits by harnessing the power of new technology?
How autonomous operations work
In a typical manufacturing facility, industrial autonomy means leveraging the latest technology to achieve better situational awareness. It means allowing a system to take an optimal action that achieves the desired outcome in the best way possible. Those desired outcomes can include better production, improved quality, more reliable operation and a much more efficient workforce.
Industrial autonomy helps to automate production tasks and to ensure those tasks are performed flawlessly and consistently. However, it doesnāt imply the absence of humansāpersonnel just move to higher-order tasks associated with continuous business improvement.
To move toward autonomy in industrial processes, one must dissect and look at what can be fully automated, what elements will require human supervision and which areas will remain manual. Once this clarity is established, it is possible to set a path to autonomy following six progressive levels:
- manual or semi-manual operations
- controlled and optimized operations
- intelligent operations
- remote operations
- resilient operations
- autonomous operations.
While the industrial autonomy maturity model does have a natural sequence and evolution, many facilities will have a varying degree of capability on each level. A plant might employ manual procedures for some operations while having pieces of equipment that operate largely autonomously. Companies need to assess their existing capabilities at each level.
The goal of industrial autonomy is to eliminate manual steps by automating them. As the user starts this journey, itās important to take the time to understand what processes are still manual or semi-manual and to assess which of those are dependent on the knowledge and skill of an individual to carry them out effectively. These manual operations can range from field personnel taking manual gauge readings to control staff performing a product transition based on their experience and a written procedure.
Industrial autonomy can help companies to achieve their goals to centrally monitor assets and, in some instances, conduct unmanned remote operations. This is particularly attractive for complex, remote or hazardous environments.
Autonomous systems will also transcend traditional predictive maintenance. Devices such as control valves with embedded sensors for temperature, pressure and sound will be able to operate autonomously, determine their maintenance needs and coordinate service requirements to minimize production disruptions.
Conclusion
The process industries have benefitted from industrial automation and will benefit even more with industrial autonomy. The pace of this transition is increasing with the advancement of enabling technologies such as artificial intelligence (AI), machine and deep learning, cloud and edge computing, wireless sensors and improved communications and networking.
Industrial autonomy is not defined solely by fewer people. Rather, itās about how control, sensing and knowledge are utilized to create an inflection point in operational benefits. Each step along this journey will yield sizeable benefits.
Ultimately, the arrival at industrial autonomy in the manufacturing sector will enable every day to be the best day of production and every employee becoming a knowledgeable expert.
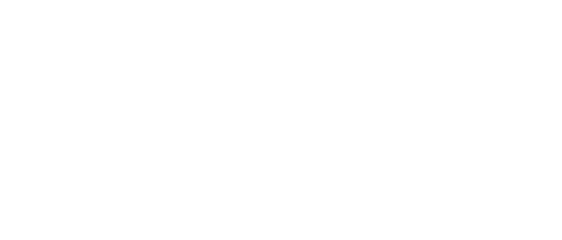
Leaders relevant to this article: