COVID-19 and its impact on the global automation industry
Over the past decade, the global automation industry has made significant strides through increasing digital transformation of industrial processes. This change has been further accelerated due to a growing convergence of technologies including artificial intelligence, cloud computing, Industrial Internet of Things (IIoT) and advanced analytics.
Clear trends were evident in the global automation space right up to the emergence of COVID-19.
- A growing shift to software and software-as-a-service (SaaS) models: The operating model of global automation suppliers is increasingly resembling a software business. Software, which lies at the heart of all emerging technologies, has pushed automation suppliers to adopt the managed services and SaaS models, where industrial firms subscribe to digital services while paying an annual subscription. Users pay based on the automation provider’s promise to generate a desired outcome such as cost savings through predictive maintenance of industrial components.
- New industrial systems and components: Digital transformation has given birth to a new family of industrial parts and components which are more dependent on virtualization (augmented reality/virtual reality) and edge technology (smart devices, IIoT), as well as advanced networking infrastructure.
- A key focus on cybersecurity: Increasing dependence on software, the Internet and the cloud is bringing into focus the need to develop a robust cybersecurity system for industrial players. This has opened up an area of specialization for automation suppliers, which revolves around cybersecurity and health, safety and environment (HSE).
COVID-19 and its impact on manufacturing
Much of the world remains under lockdown in the face of the COVID-19 pandemic. Many countries remain under varying degrees of lockdown in 2020 with schools, restaurants, cinemas and businesses shut down and air travel severely limited through much of the globe. With no proven therapeutic available and a vaccine that might take at least 12 months to develop, there is extreme uncertainty on the time it will take for global economies to come back on-line.
Specifically, manufacturing has been hit hard with closures and mothballing of capacity at production plants, warehouses and mines across the globe. Large industrial firms, which remain the largest consumers of automation technology, have slashed capital expenditures for 2020 to counter the collapse in consumer and material demand during the global lockdown.
March 2020 manufacturing data for major industrial hubs including the United States, Europe, United Kingdomand Japan is devastating. The Purchasing Managers Index (PMI), a survey-based index that provides the pulse of the manufacturing activity in any economy, has seen historic lows. For reference, an index number below 50 indicates a recession. The exception is a reading of 52 for China, which has seen a bounce from 35.7, its worst-ever reading in February 2020, when the country was under lockdown (Table 1).
The Purchasing Managers Index (PMI) for March 2020, a survey-based index that provides the pulse of the manufacturing activity in any economy, has seen historic lows.
March PMI |
Comment |
|
United States |
49.2 |
Lowest reading since 2009 |
Eurozone |
26.4 |
Worst reading in the history of the index |
United Kingdom |
47.8 |
Lowest reading since mid-2012 |
Japan |
44.8 |
Lowest reading since 2009 |
China |
52 |
Improvement from worst-ever reading of 35.7 in February 2020 |
(Source: IHS Markit)
April PMI numbers are expected to be worse than March for most of the regions and the global manufacturing landscape is not expected to reflect a semblance of normalcy before the end of 2020.
The progress of automation and the performance of global automation suppliers are dependent on the health and smooth functioning of the global manufacturing sector. With several factories and production units having to shut down, mothball capacity or lay off workers to control fixed costs and losses, the drive to automate inevitably takes a back seat in the short-term. Only when economic and manufacturing activities return to normal can companies look to increase their capital expenditures and resume their automation journeys.
Cancellation of automation and manufacturing conferences
More than 100 annual manufacturing and automation conferences are held globally. These conferences serve as key sources of information sharing and marketing for manufacturing and automation technologies. Moreover, it helps automation professionals stay up to date with industry best practices and brainstorm on technical issues with fellow professionals from across the globe.
Due to the lockdowns due to COVID-19, nearly all conferences slated to happen in the last three quarters of 2020 have either been cancelled or postponed to 2021. Besides the devastating slowdown in manufacturing, cancellation of these conferences again points to the fact that the pace of automation might slow down in 2020, with hopes of a pickup in 2021.
Automation industry focus
Siemens has made available its Additive Manufacturing (AM) Network in conjunction with its 3D printers to help global health professionals to speed design and produce medical components. Use of this technology will enable faster and less complicated production of spare parts for machines such as ventilators. Additionally, Siemens UK and Siemens Healthineers AG have joined the coalition formed in response to the UK government’s Ventilator Challenge to meet the demand for thousands of ventilators required by the National Health Service (NHS). Specifically, Siemens is providing expert assistance to the consortium on areas of increasing manufacturing automation and productivity, simulating and testing scaled up manufacturing operations and modifying existing ventilator manufacturing machinery for higher throughput.
As several industrial firms temporarily switch over to the production of ventilators and protective equipment, Rockwell Automation, through its Independent Cart Technology (ICT), is helping customers to switch over and ramp up production of critical medical components and equipment. On the pharmaceutical front, the company is also working with customers to help in coming up with solutions to increase plant productivity for existing and under-trial medicines.
Emerson has decided to focus on key technologies used in the production of ventilators, respirators, hospital beds and testing equipment used during the spread of the virus. Erik VanLaningham, vice president of global marketing for industrial automation, highlighted how the company is responding to the current environment while ramping up production on key technologies such as miniature fluidic control valves for medical devices that help customers treat COVID-19. Also, Emerson’s ultrasonic equipment can slit, bond, seal or quilt nonwoven synthetic materials to make surgical face masks, face shields, disposable hygiene products, gowns and filter media. The company is helping its customers that use its ultrasonic technology to expedite the manufacture of nonwoven garments.
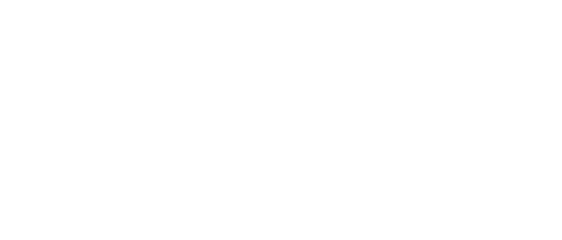
Leaders relevant to this article: