AMRs communicate with factory of the future using private 5G network
Ericsson made a single brand of AMRs the centerpiece of its new Industry 4.0 Smart Factory in Lewisville, Texas. A World Economic Forum (WEF) Global Lighthouse and Gold LEED-certified by the U.S. Green Building Council (USGBC), the smart factory boasts about 30 AMRs that move and handle electronic materials down the assembly line. The AMRs have different configurations to handle different types of tasks, such as the shopping-cart configuration or a conveyor-belt configuration (Figure 1).
The AMRs provide material—electric components on reels—to the assembly line, and they move boards from assembly to testing, as well as to shipping. In between there are multiple stations depending on the current situation (Figure 2).
Ericsson’s big bet on AMRs was partly based on the greater flexibility they provide over automated guided vehicles (AGVs) and on the factory’s ability to provide ubiquitous wireless connectivity across the entire factory. In order to enable Industry 4.0 powered by AMRs, the company needed to build and manage a highly reliable, low-latency network that would be able to handle the flow of large amounts of data between the AMR fleet and 5G access points. A failure to do so would create disruptive bottlenecks on the assembly line and require redundant human intervention. If successful, the company would gain significant benefits of Industry 4.0 deployments around productivity, agility and sustainability while giving it a showcase facility that could serve as a template for transforming manufacturing for the better around the world.
Why 5G?
Recent improvements in performance, capacity and speed have made Wi-Fi 6 a more viable option for enterprise deployments, but the AMR deployment in Texas required a level of scale and reliability that only 5G could provide. However, the ability to manage its own network, rather than piggyback on a public 5G network, was intriguing. Eventually, Ericsson got the best of both options, deciding to build and manage its own private 5G cellular network right there in the factory. This decision gives it the speed, coverage and reliability of 5G with the control of Wi-Fi networking.
In the factory, there are actually two separate private networks, with one of them serving the building management system. The Ericsson factory network is its own separate network with no outside connectivity, so cybersecurity is of limited concern.
The 5G coverage is provided by state-of-the-art radio products which cover the area through two Ericsson street macros.
Here are four reasons why it settled on a private 5G cellular network to provide ubiquitous connectivity for its AMR deployment.
1. Flexibility and agility: Network architects need to design connectivity around specific deployment needs, and just-in-time manufacturing powered by AMRs required a degree of reliability, security and coverage that private 5G cellular networks could provide. Just-in-time manufacturing also requires agility. As we saw during the pandemic, factory floors that can be transformed quickly allow manufacturers to pivot on demand and take advantage of emerging opportunities, such as manufacturing masks, goggles and other personal protective equipment (PPE). The private 5G cellular network that Ericsson built in Texas gives it the flexibility to meet any challenge or market demand that gets thrown its way.
2. Visibility and Control: Private 5G cellular networks give network administrators greater visibility and control into connectivity. Piggybacking on public 5G rather than building and managing its own network would hamstring the ability to identify performance, connectivity or security issues in real time and optimize the network for its own purposes. Relying on a private cellular network also reduces latency and shrinks the threat surface, making it easier to provide better security and protect systems from malicious threats. This was especially critical in the Lewisville factory where Ericsson manufactures some of its most important products for the crucial North America market.
3. Mobility: Coverage is really where private 5G cellular networks shine. Cellular access points cover 10 times more area than Wi-Fi and allow the company to improve route mapping for the AMR fleet, reducing the number of required access points from 20 to two across the 300,000-sq-ft facility. This greater mobility means that operators don’t have to worry about handovers between access points or dead spots on the factory floor. Nothing is more frustrating than walking out on the floor to see a conga line of robots stuck en-route from one station to the next, which requires a person to go out and physically move the AMRs along, causing a disruptive bottleneck in the manufacturing process. Not only is Ericsson able to save on fewer access points, the expanded coverage also makes it easier to scale and plan for future growth.
4. Sustainability: This is all moot, of course, if the factory of the future isn’t sustainable. Ericsson’s sustainability features include a solar-panel network, rainwater collection tanks, chilling tanks that use naturally forming ice for air conditioning and hundreds of temperature, air-quality and humidity sensors stationed around the facility that help maintain optimal climate conditions. As a result, Ericsson is able to save energy costs by 24% over comparable buildings, in large part due to the ubiquitous connectivity provided by the private 5G cellular network.
Synchronization and orchestration of AMR fleets
Ubiquitous connectivity is the enabling factor for Industry 4.0 AMR deployments, and Ericsson knew that it needed a highly reliable, low-latency network to ensure the flow of high volumes of data across the factory floor. While Wi-Fi 6 and public 5G networks are viable options for enterprise environments, relying on a private 5G cellular network for ubiquitous connectivity would provide the right combination of performance, speed, latency, visibility and control that operators needed to empower the autonomous manufacturing center in Texas.
Register for the conference at Automate Registration.
Latest from Robotics
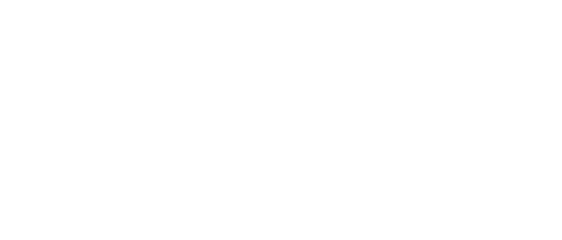
Leaders relevant to this article: