Manufacturers are under pressure to be more flexible, reduce downtime, increase efficiency and, above all, keep personnel safe. These efforts are complicated by yet another requirement: the successful management of external influences. These factors are difficult to predict, and, when their true effects become known, effective adaptation can be a challenge. Fortunately, the right machine-safety technology can help companies to reduce the impact of unforeseen events and keep productivity levels high.
How external factors impact OEE
To better understand how unexpected local and global phenomena can impact manufacturing, let’s use the COVID-19 pandemic as an example. Due to the many changes to local regulations that are taking place worldwide, most manufacturers must limit the number of people allowed in their facilities during a single shift. This helps to ensure employee wellbeing, but it also has an unexpected impact on factory operations. A company’s machine-safety expert might not be on-site when a functional safety problem arises, and this in turn will affect the production line, increase downtime and, depending on the type of failure, even require overtime to identify and solve the underlying cause.
How does a manufacturer overcome this difficult situation? One response may be to implement a functional safety program, but if there’s no in-house engineer trained to handle machine-safety challenges, it may be necessary to rely on a third party. This gives rise to other factors, such as availability, response times and unplanned costs, which again can impact equipment availability. It’s critical to provide on-site personnel with sufficient tools for troubleshooting in an intuitive way without the need for additional interfaces or complex technologies. Intelligent safety devices, flexible configurations and visualization can simultaneously improve safety and streamline productivity strategies.
The importance of visualization
Safety devices with clear status indicators are a great ally when it comes to protecting employees and keeping machines up and running. For example, input safety devices such as safety light curtains (SLCs) or safety scanners that have clear status indicators help operators to identify obstructions, faults or special configurations without a dedicated interface. This reduces downtime by making it easier to identify and fix conditions that would otherwise require a higher level of maintenance skills and additional tools.
Furthermore, adding a human-machine interface (HMI) to a safety system provides a level of visibility into the safety controller that was unimaginable just a few years ago. New developments offer safety monitor functions on the HMI by default, which means that no additional time is required for development (Figure 1). Besides providing status information, this safety monitor function can retrieve and display safety hardware configuration data without requiring anyone to open the control panel. This means that companies can keep people away from dangerous electrical equipment and lower the probability of anyone getting hurt while still providing access to clear information necessary to complete operational tasks.
A common challenge on the factory floor is troubleshooting intermittent stops in a system. These can be tough to sort out if there’s no access to additional data like event logs or error codes. As a result, maintenance teams face the challenge of monitoring the system until the failure happens again, with the hope of somehow being able to identify what went wrong. Such situations can quickly become overwhelming since they consume large amounts of time and lead to unexpected costs.
Interactive safety solutions
Functionality that simplifies maintenance, speeds up safety restoration and enables easy access to diagnostic information without complex or dedicated interfaces should be part of any safety system. With these features as part of a machine, the operational and maintenance teams can take the necessary steps to maintain a safety system.
From the safety-controller perspective, the latest generation on the market makes it possible to store programs and settings on an SD card inserted into the communication control unit. When the safety CPU unit needs to be replaced, the stored programs and settings can be easily copied to a new unit using the SD card. This eliminates the need for advanced training or dedicated tools for the same task and will ultimately save costs and contribute to higher productivity. Another benefit of an interactive solution is the option to have settings data automatically downloaded when replacing a safety I/O unit. In contrast, replacing a safety I/O unit with previous generations implies a reconfiguration of the safety system, which at the very least involves support from the manufacturer and sometimes assistance from a safety expert.
Another common challenge faced by maintenance teams is the troubleshooting a safety light curtains, particularly when they are installed in press and welding applications. It can be puzzling to identify the real root cause of any SLC that’s activating without a noticeable cause. Operators can use basic product information; like an incident light indicator to identify the SLC’s ambient light levels; status information to see how the safety and non-safety signals are switching; and maintenance information logs to track errors and warnings and suggest possible actions to take.
Prevent unauthorized modifications
Based on ISO 13849, in any safety system using a programmable safety relay or a safety PLC, the entire system needs to go through a verification and validation process before going into RUN mode to ensure that all safety functions work according to design. Once this process is completed, the system will create a unique safety signature or ID that will never change unless the configuration changes. If someone were to add a safety door switch to the machine, for example, this will require changes to the hardware configuration as well as to the program. Before starting the machine again, the validation process needs to be applied and the system can create a new safety signature.
In the past, only system integrators used safety signatures as part of their guarantee at the end of project commissioning. It soon became clear, however, that it was in everyone’s interest to be aware of any unforeseen safety-program modifications that could call into question the system’s actual safety level, such as the addition or removal of a new safety device without a risk assessment process to justify it.
In order to avoid exposing operators to this scenario, manufacturers should check the system’s safety signature at the beginning of each shift to make sure the system remains the same. Based on our previous comments, visualization is the key, and showing the safety signature in a human-machine interface helps operators to access this information and the safety managers during their machine safety audits.
Online functional test
According to IEC 62061 and ISO 13849-2:2015, the purpose of the validation process is to confirm that the safety design supports the overall safety specifications for the machine. Testing must be carried out to complete the validation, since it’s always complementary to analysis, and often necessary. The validation process through testing also requires personnel to define a plan, record results and perform the tests as close as possible to its final operating configuration.
Normally, running a functional test as part of the validation process for a commissioning project can be tedious, even for its designer. The personal who has better understanding of the safety-system must be on site, usually, is the system designer. Additional people may be required depending on system size. The entire process could take hours or possibly days; for example, an application with around 30 safety devices will require at least 16 hours.
Increase equipment availability with intelligent safety devices
Functional safety in combination with digitalization initiatives helps to reduce downtime and the need for people to be exposed to hazardous machine motion during operational or maintenance activities. This can be achieved when safety devices are monitored remotely so that there’s little reason to step inside hazardous areas simply to check the alarm of a safety device.
Common challenges faced by maintenance teams are simplified by providing the right technology and access to personnel on the factory floor. The ability to access safety data in real time and organize it into meaningful information creates enormous possibilities for manufacturers. Furthermore, working with intelligent safety devices helps to reinforce preventive-maintenance efforts by accessing safety data in real time and organizing it into meaningful information.
Questions to keep in mind
When designing a safety solution, manufacturers should ask themselves the following questions to ensure that they’re taking full advantage of technology for future applications.
- Are you making maintenance tasks easier to accomplish? How many dedicated tools will your team need for monitoring and troubleshooting tasks?
- How many training hours will be necessary to familiarize your team with the platforms and tools involved in the application?
- Does your validation plan cover functional testing? How many resources, time and people will you need to accomplish this plan?
- Are you tracking the safety signature for your machines? How do people access this information?
- How much safety-related data can you collect? Where are you planning to store the information?
- Do you need to offer access to safety-related data on the factory floor?
Summary
Machine guarding in combination with flexible manufacturing and intelligent devices is driving a new approach to project commissioning, not only to fulfill functional requirements, but also to take into consideration the complete lifecycle of a machine (Figure 2). This helps to reduce the impact of external influences, since the strategy of making machines more intelligent and improving their networking in turn improves efficiency, reduces costs and opens the door to the factory of the future. Manufacturers can combine digitalization and functional safety to empower their personnel to design and implement safety solutions that will protect them and keep machines running.
Figure 2: A new approach to project commissioning allows a combination of machine guarding and intelligent safety devices to enable flexible manufacturing and fulfill functional and safety requirements.
ALSO READ: Intrinsic safety comes with requirements
Latest from Machine Guarding
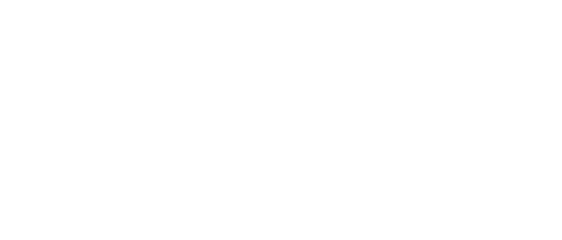
Leaders relevant to this article: